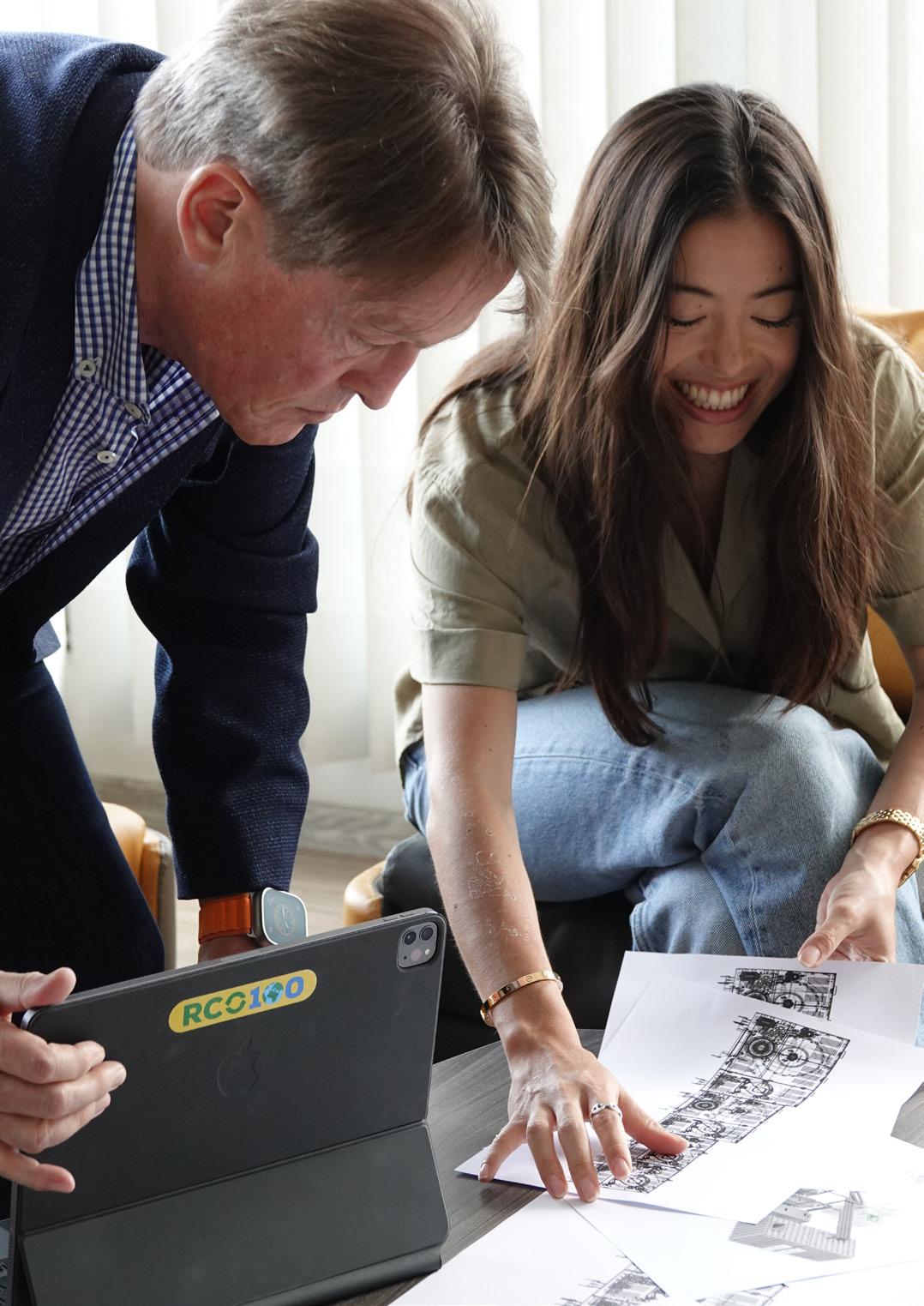
4 minute read
TIMELINE
1980s
Stefan embarks on his textile journey.
Advertisement
2005
We are a Swiss, family-owned and run textile sourcing and supply company headquartered in Singapore.
We have specialised in material, fibre, yarn, fabric and technology development and sourcing for the global market in garment and technical textiles.
2016
RCO100, our 100% recycled cotton technology, was launched in 2016, we have been developing a mechanical recycling system for cotton. Our first partner in this project was PVH Corp.
2018
By the end of 2018, we successfully spun open-end yarns up to Ne20 using 100% preconsumer industrial waste.
2019
PVH Corp introduced 100% recycled denim at their Paris fashion show in early 2019. In addition, we established a partnership at Kipas in Kahramanmaras, Türkiye, where we installed our custombuilt recycling line.
2023
Säntis Textiles is proud to bring to market the latest innovation in textile recycling RCO100.
Säntis Textiles, a multi-generational textile company, is proud to bring to market our latest innovation in textile recycling.
Our decades of knowledge have led us to develop a system that uses a mechanical fibre opening technology which treats the fibre gently and does not stress the material.
The aim was to develop a mechanical recycling system for 100% recycled cotton yarns and fabrics to maintain the best fibre length and strength possible.
Since 2016, we have been developing a mechanical recycling system for cotton. Our first partner in this project was PVH Corp.
By the end of 2018, we successfully spun open-end yarns up to Ne20 using 100% pre-consumer industrial waste.
These yarns have since been used to make the following yarns and fabrics: Denim, Chino, Canvas, Panama, Single Jersey, Pique and French-terry.
PVH Corp introduced 100% recycled denim at their Paris fashion show in early 2019. In addition, we established a partnership at Kipas in Kahramanmaras, Türkiye, where we installed our custom-built recycling line. Since then, we have continuously worked with leading global brands such as Lacoste, Patagonia and Mara Hoffmann on development to further their circular initiatives.
This line produces approximately 300-350 tons of mainly preconsumer and post-consumer cotton bales per month.
With the help of our partners, Säntis Textiles launches our new RCO100 recycling system:
• Components engineered by Swiss engineering company Swinsol
• Machine built by Turkish textile air conditioning equipment supplier Temsan.
Santis Textiles is proud to give the license for the production, sales and service to Temsan, the global leading supplier in textile air conditioning equipment.
Additionally, together with Swinsol, we developed a mechanical compact ring spinning system, specially designed for RCO100 carded compact ring yarns. This system, which includes a unique compacting system for the roving frame is the most suitable for recycled cotton fibres.
Unique features of the RCO100 recycling system:
• Most gentle fibre treatment of all mechanical recycling systems in the market. Our task is protect the fibers and to maintain maximum fiber lengths and strength.
• The standard line includes two conveyors and two strong built guillotine knives positioned in a 90º angle to achieve best possible cutting results.
• The initial buffer unit is also a mixing chamber for the cut material. It controls the feeding to the following pre-opener cylinders. The initial buffer unit also contains spark and metal detection.
• From the buffer, a feed table transports the material to the preopening cylinders. These are four modules which are configured with pin cylinders and / or saw tooth cylinders in order to optimize the pre-opening process.
• The feeding to these cylinders is through controlled feed rollers but without clamping points or counterrotating cylinders. Transport from one cylinder to the next is by perforated drums, which not only dedust the fiber fleece, but also forward it without stressing the material.
• The four pre-opener cylinders are equipped with covers on the bottom, which can be adjusted and equipped with carding elements, according to the in-feed materials.
• From the pre-openers, the material is sent to three parallel fine-opener lines, each equipped with 12 opening cylinder modules.
• The material is fed into chutes and then transported to the first opening cylinder which can be equipped again with pins or sawtooth / carding wires. The fibre fleece is again transported via perforated drums and no fibre clamping / squeezing is involved.
• Unopened yarn / fabric material drops below the cylinders to a suction and is returned to go around and start at the beginning of the opening process again. This feature allows the yarn/fabric cuttings to run through the system as many times needed or until the yarns are opened and the fibres flow free through the fine-opener arrangement. It is the most gentle way to treat the fibres and a crucial feature in our system to achieve best possible fibre lengths.
• Once the fibres are opened and de-dusted, they are sent to another buffer unit and then pressed to standard bales in a strong and efficient bale press.
• The dust is collected in a modern filter system.
• Future systems will include patented mechanical elastane extraction, patented direct can coiling and patented traceability technology.
• What is input and output of the machine? What kind of materials the machine can run?
The current machine is running at approx. 450 tons / month, i.e. this is approx. 10-12 tons / Day.
We can run any staple fibre fabrics. 100% cotton, polyester / cotton, polyester staple, viscose, cotton / nylon staple, linen, hemp (as long as it is cotton staple length).
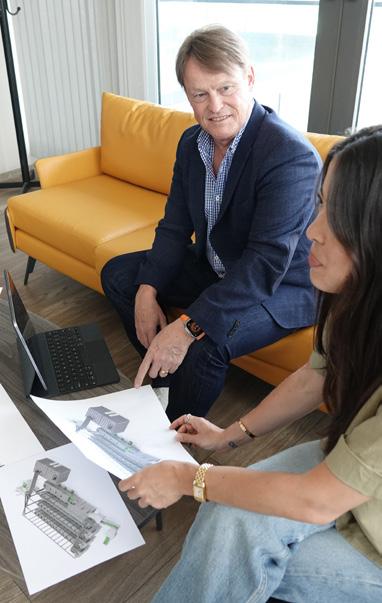
What is the output fibre length?
Turkish cotton has a 80% staple length of approx. 31-32mm. When we recycle this we come out with a 80% staple length of approx. 2526mm.
In general the output depends on the input fiber length of course, but we can say that we have approx. 1520% loss. We can keep longer fibres also by reducing the production rate.
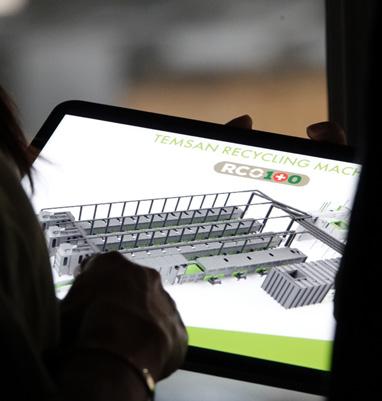
What kind of yarn can be produced with the output fibre?
We can spin Open End yarns from Ne5.9 - Ne20 and carded ring compact yarns from Ne8 – Ne30.
Additionally, we can spin carded ring compact core yarns up to Ne20 with 40 den and 70 den recycled elastane.
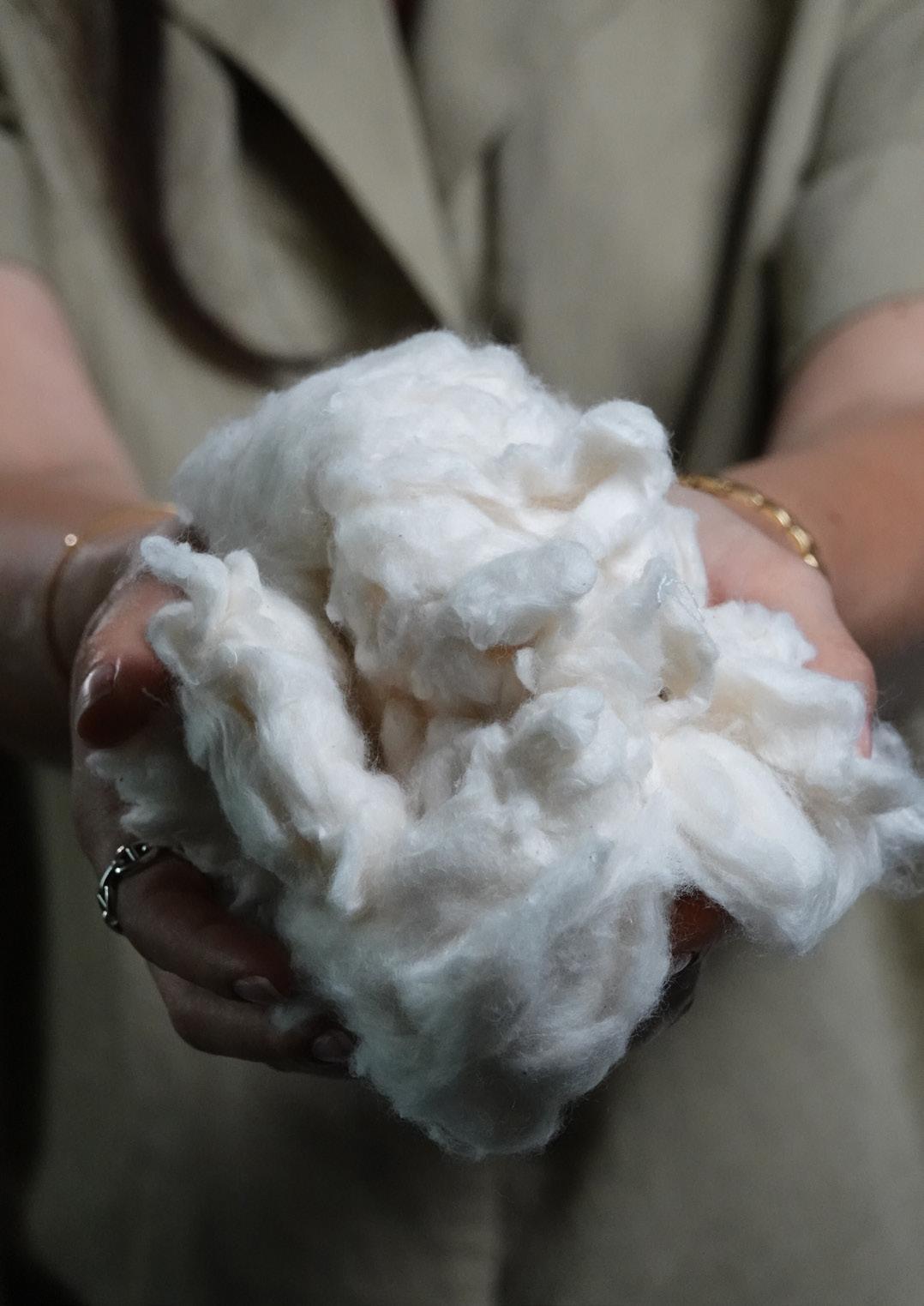
Buffer
Mixer Feeding Machine
3 X 12 Fine Cleaners
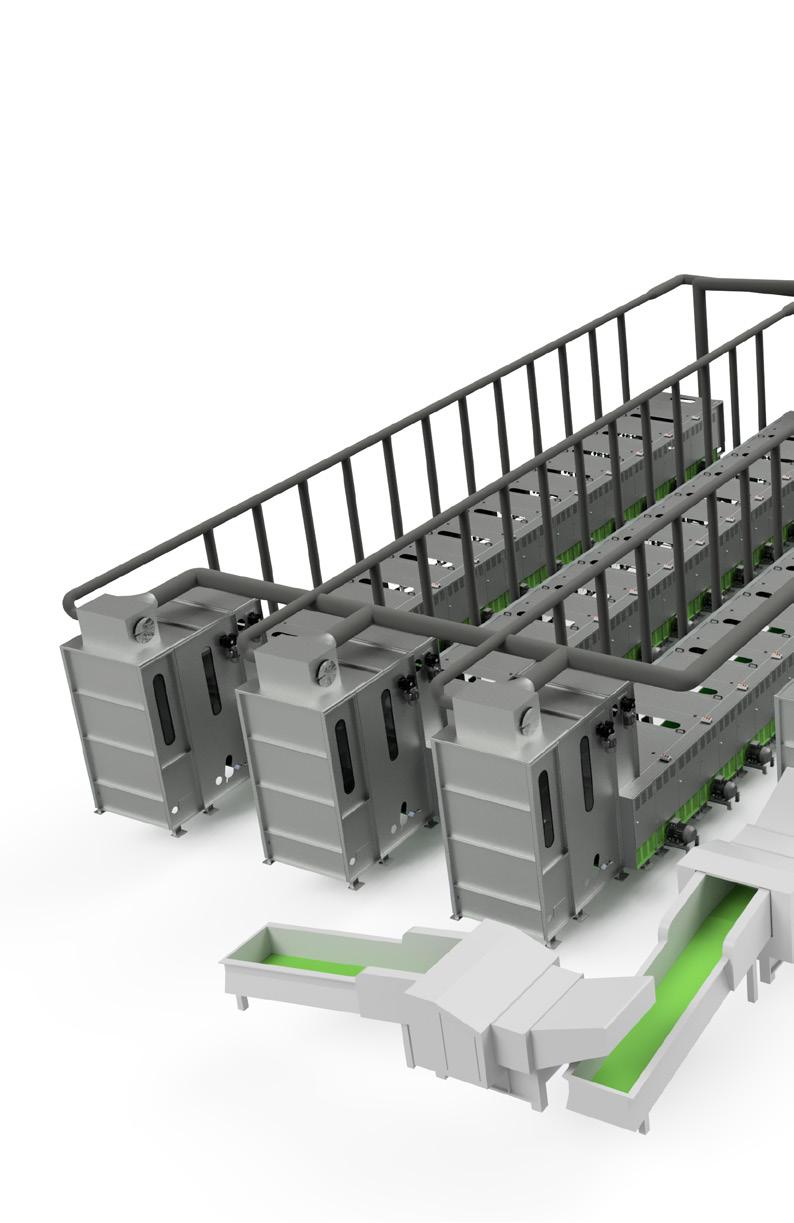
Balepress
Filter System
FOUR PRE - OPENERS
Buffer
Mixer Feeding Machine
Two Cutters
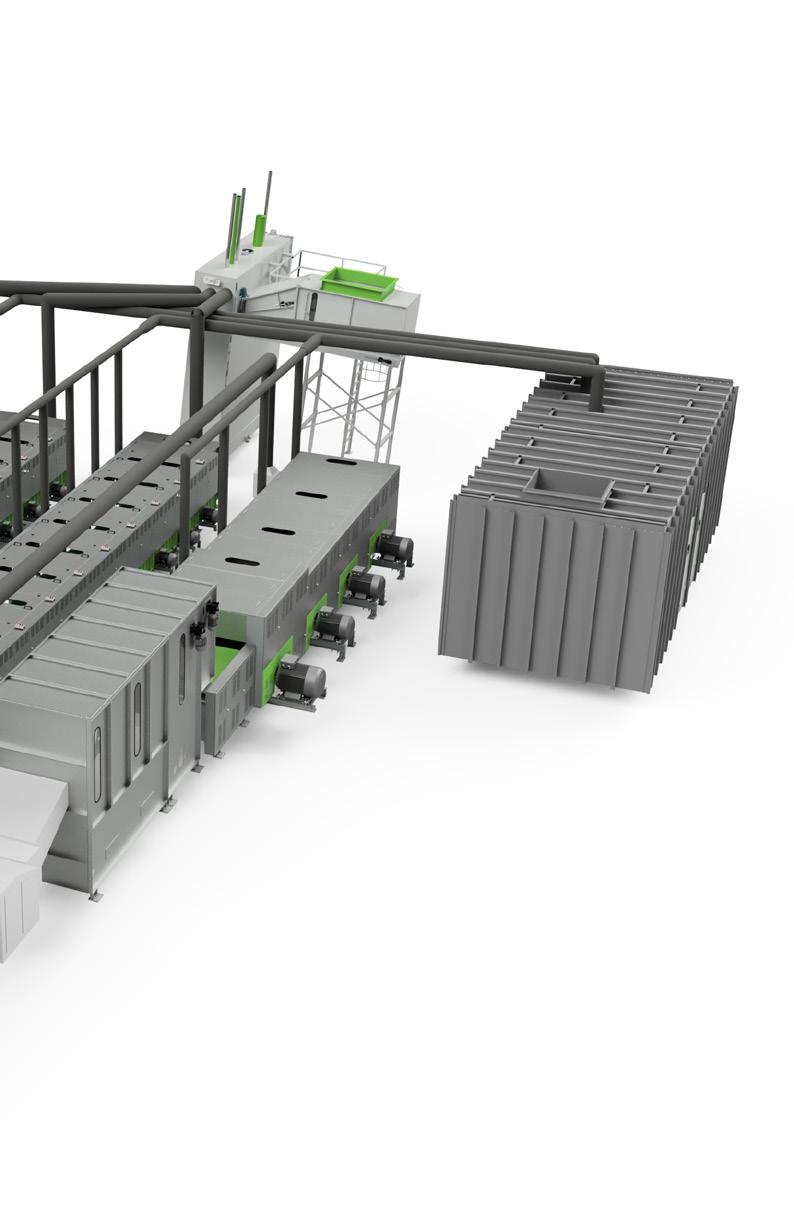
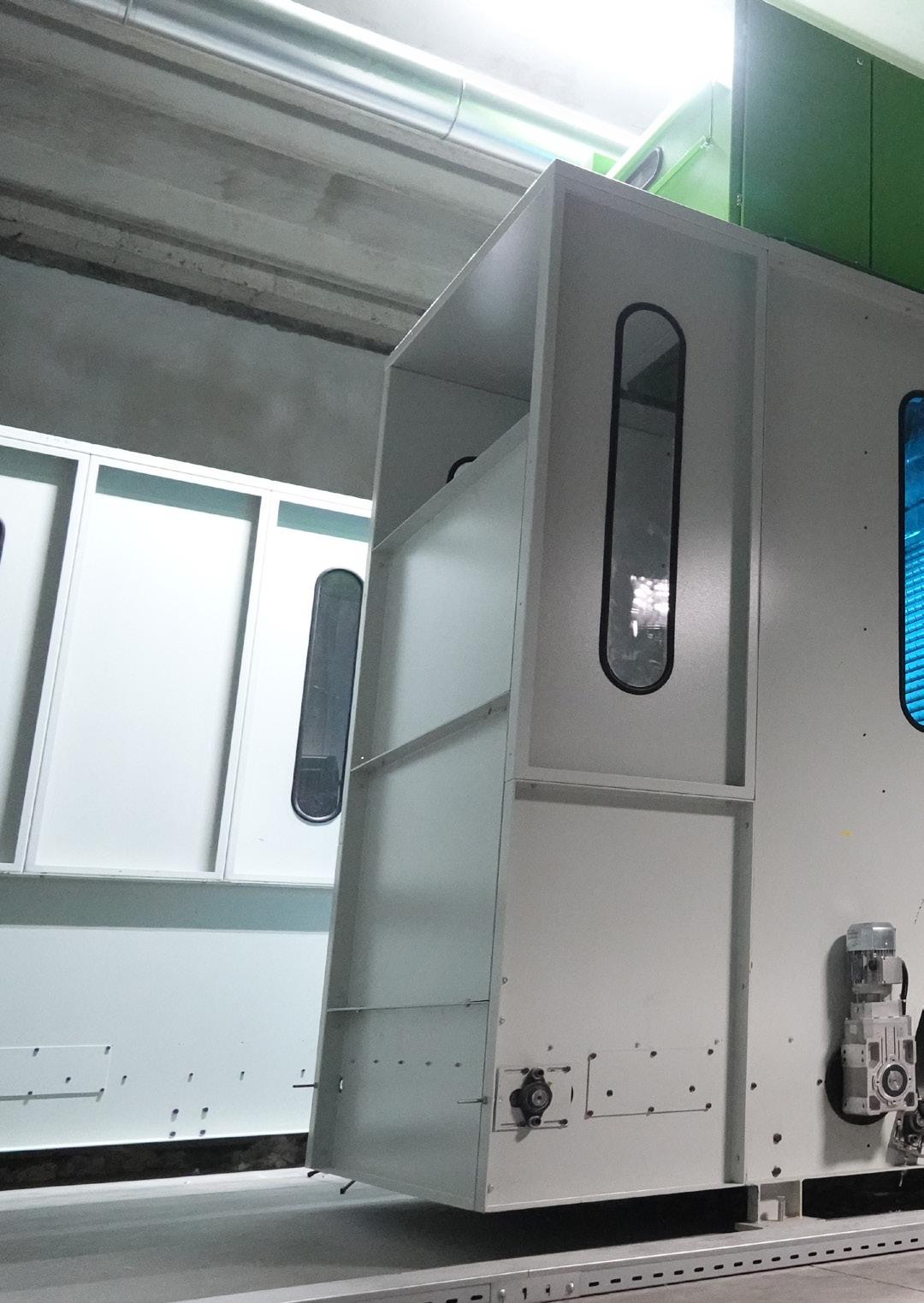
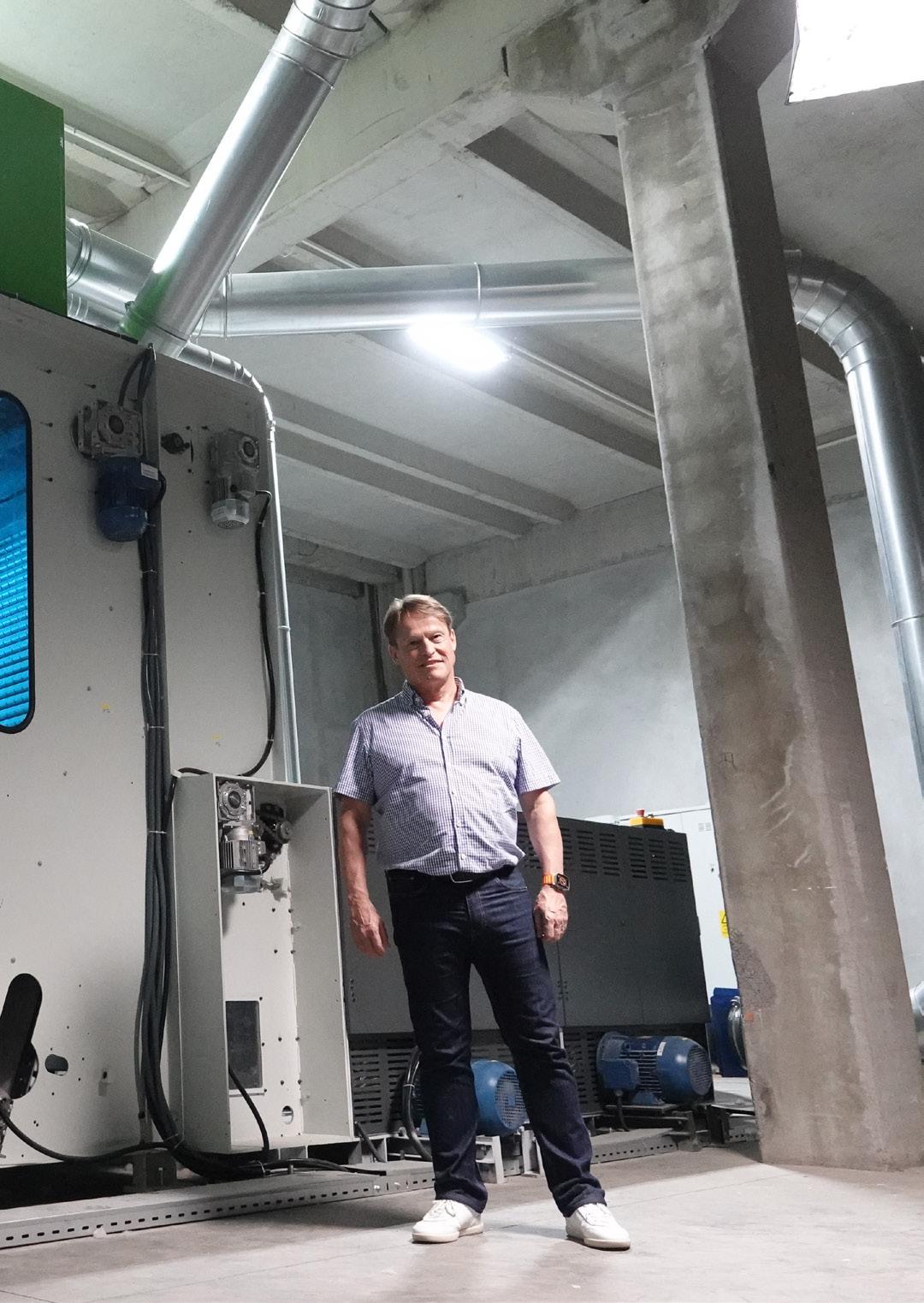
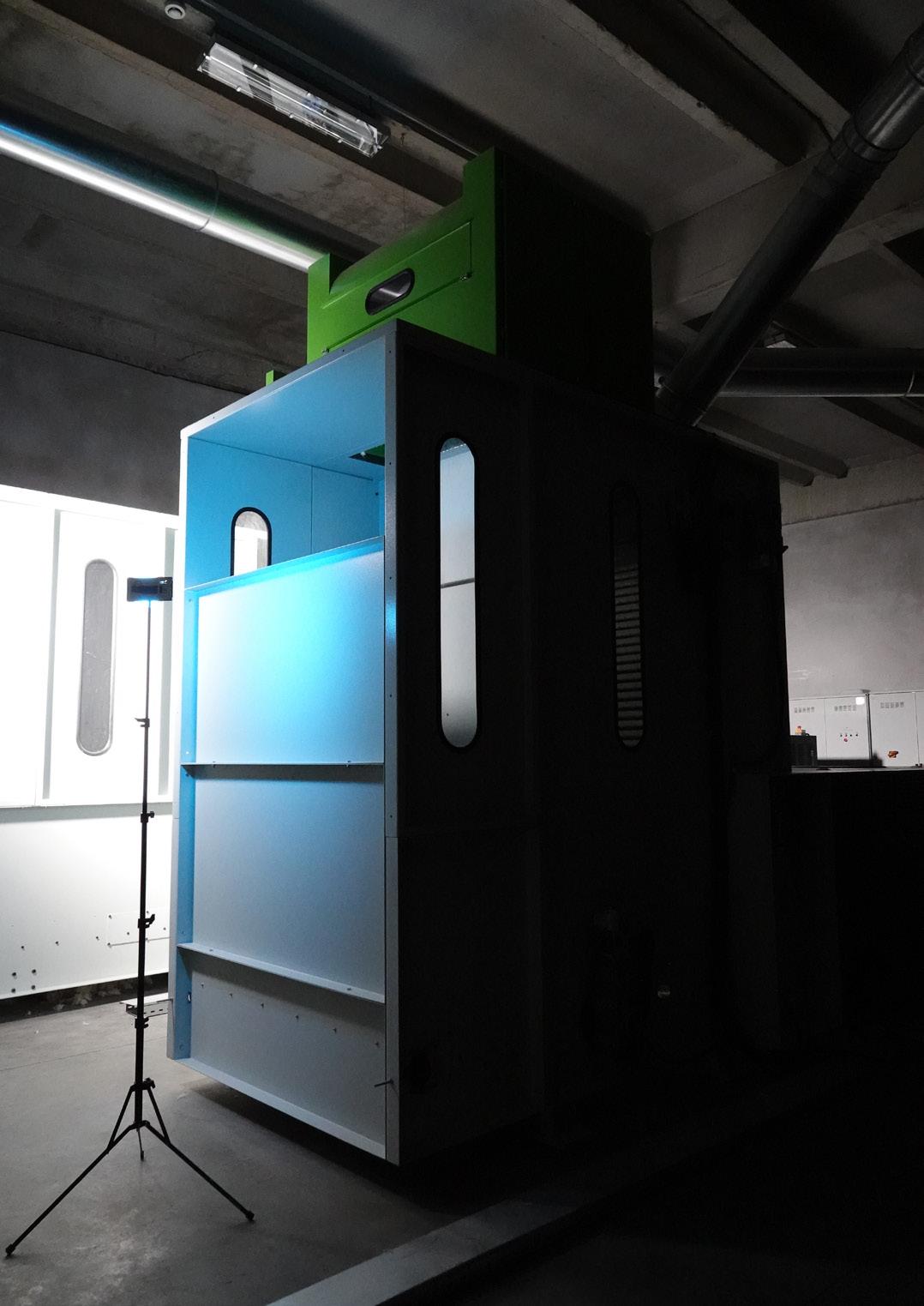