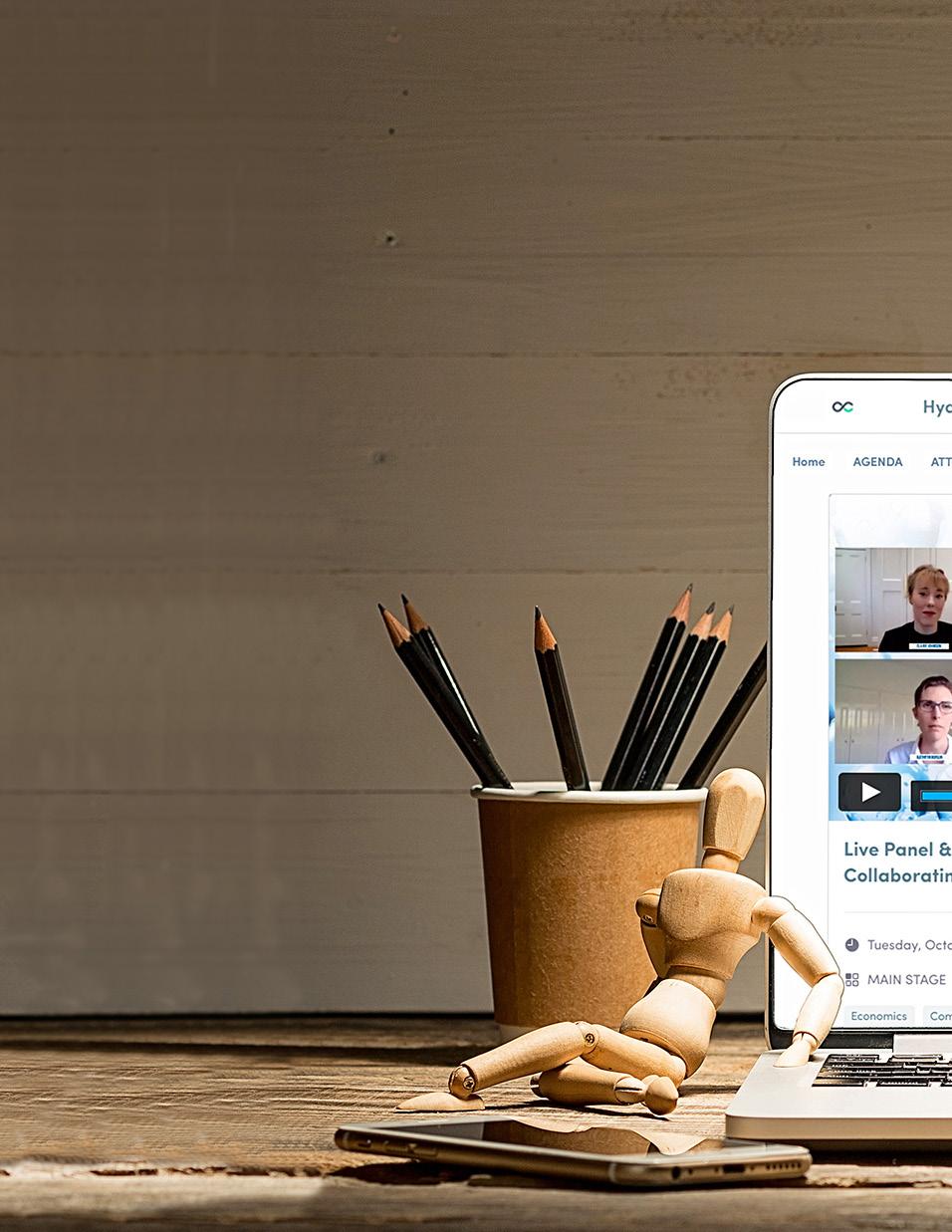
12 minute read
Achieving Scalability in Hydrogen Projects for Mines HYDROGEN AND MINES VIRTUAL SUMMIT REPORT
MELODIE MICHEL, Reporter, Energy and Mines
While still not commercially viable, hydrogen applications in mining are progressing quickly. With numerous pilots, industry collaboration and the development of the hydrogen industry at large picking up pace, it won’t be long before the coveted molecule achieves its broad decarbonization potential in the mining sector.
Advertisement
At the Hydrogen and Mines Virtual Summit held on October 6 and 7, 400 attendees including miners, regulators, OEMs and suppliers shared their individual initiatives, and discussed what is needed to take efforts further. “If you think about in a few decades, the opportunity that hydrogen offers for the mining sector is to become completely self-sufficient in energy: self-sufficiency in electricity and for fuelling vehicles, with no need to import gas or diesel,” said Geoffrey Drucker, Managing Director of Countrywide Renewable Energy, adding that decarbonizing could bring unquantifiable value for miners, both in terms fundraising and new commercial opportunities in green metals.
While this complete self-sufficiency may still be a few years away, miners seem to be aware of the hydrogen opportunity. Among the ones speaking at the summit, Anglo American presented the details of its fuel cell haul truck and high-speed refuelling system project in South Africa; and Fortescue Metals Group talked about its plans for a fuel cell coach fleet and hydrogen refuelling station at Christmas Creek in Australia. Other miners, like BHP or Codelco, are yet to reveal the details of their hydrogen initiatives, but the fact that over 100 mining representatives attended the conference shows that interest is not lacking.
So what are the obstacles on the path to hydrogen commercialization? According to speakers in the keynote panel, “Hydrogen in Mining, Understanding the Australian Landscape”, it’s all about cost. “We are in a pre-commercial environment, so hydrogen is not able to be cheaper than incumbent fossil fuel with incumbent infrastructure. That needs to change, and we see that with the focus on decarbonization, that creates a case for hydrogen and renewables. But we need to encourage that to happen faster, we need infrastructure and scale so we’re not dealing with just pilots and demonstrations,” said Fiona Simon, CEO of the Australia Hydrogen Council. “Funding, policy setting and relationships will help overcome the barriers,” she added.
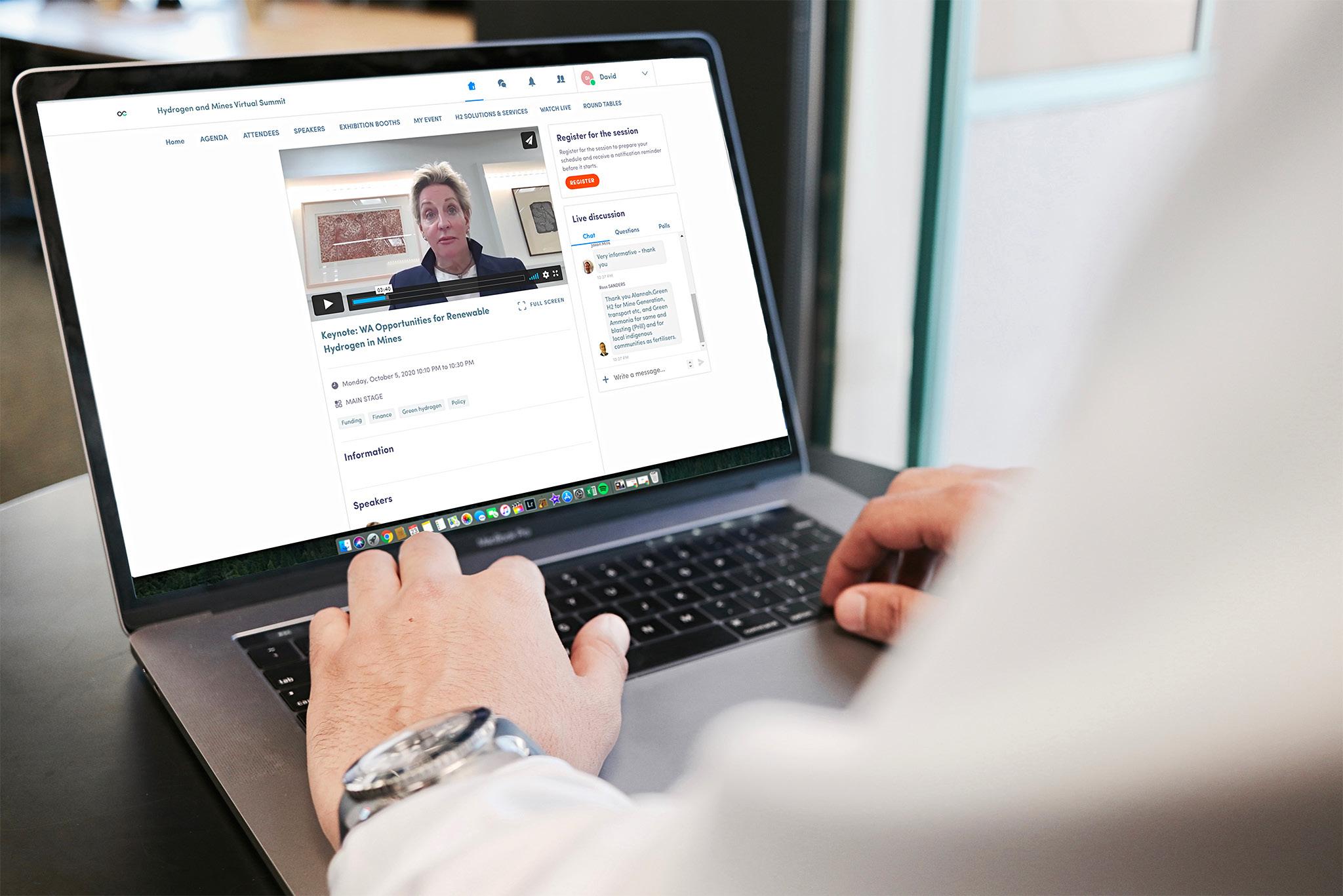
Filling the technology gaps
Other barriers mentioned by panellists include figuring out a site’s renewable generation capacity for hydrogen production, but also ensuring clean water availability, training the workforce and selecting the right equipment. New equipment is constantly being developed, particularly from mining and oil and gas services companies looking to pivot towards hydrogen: for instance, Baker Hughes is currently looking to redeploy its gas turbine, compression and pipeline technologies for the hydrogen space. “We have a number of gas turbines running today on blends with hydrogen; we had a gas turbine running on 100% hydrogen in Italy nearly 10 years ago, and since then we have been developing the technology to make it available to the mass market,” said Matthew Marinovich during his presentation for Baker Hughes.
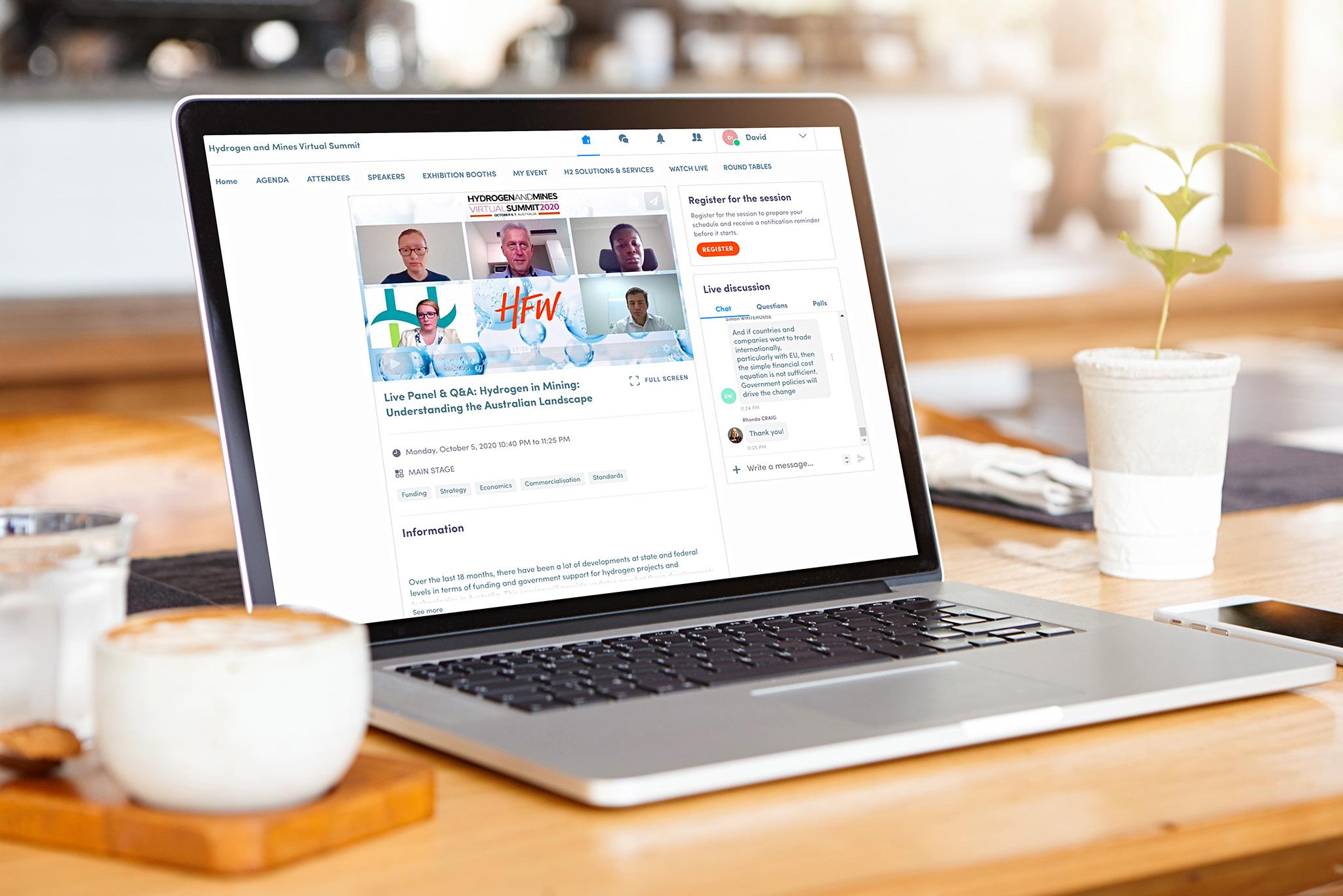
But for many, there is no readily available equipment to select from, particularly when it comes to mobile fleets. “The type of vehicles that we operate are not really viable commercially, so we had to work around identifying the right partners to develop our solution rather than buying one off the shelf,” said Michael Dolan, Hydrogen Manager at Fortescue. The company has contracted Hyzon to build 10 coaches fitted with fuel cell electric drive trains, and BOC to deliver the renewable refuelling station, intended not only to fuel the coaches, but also to test a number of other vehicles as they become available.
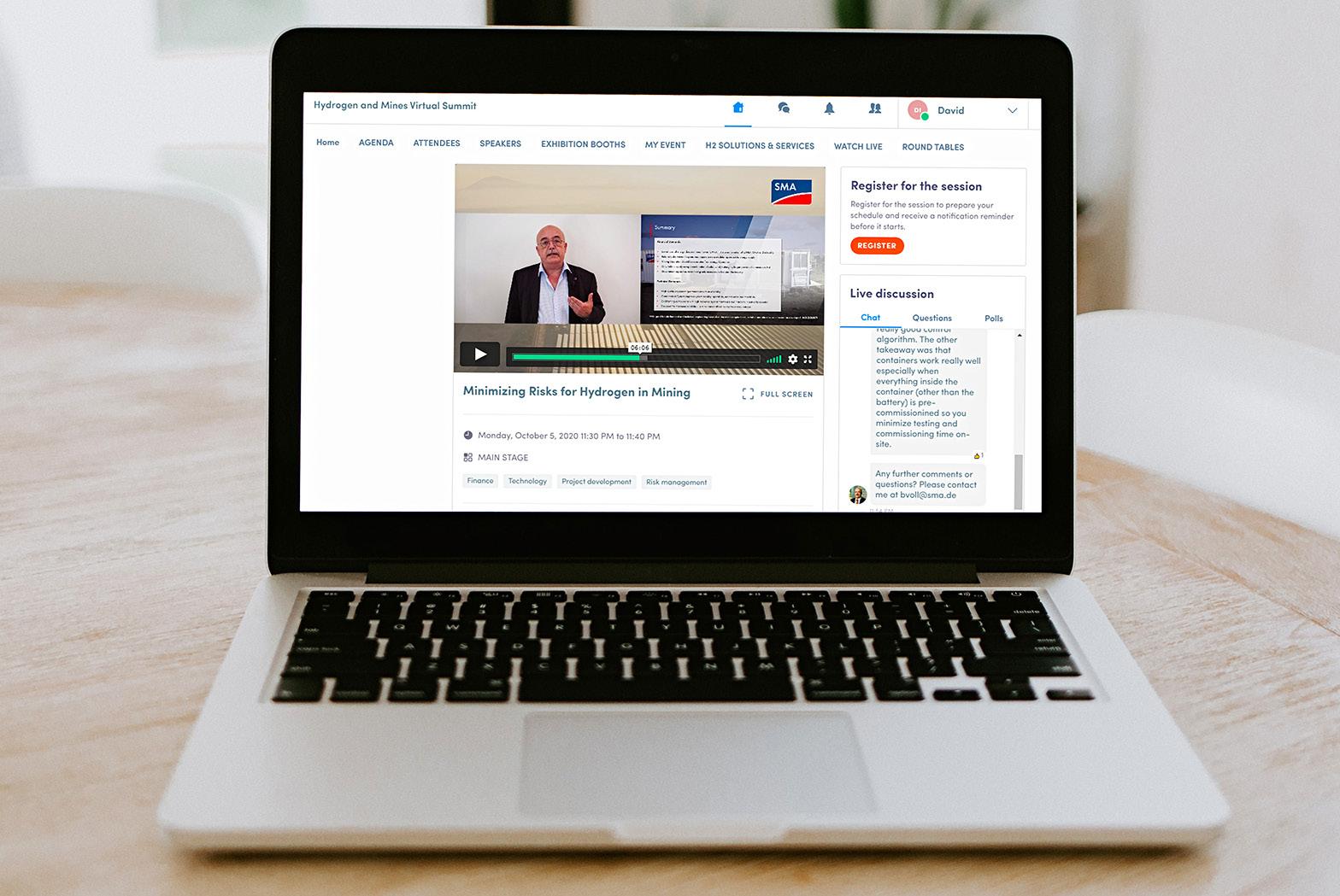
Meanwhile, faced with the lack of availability of hydrogen engines for mining haul trucks, Anglo American decided to build its own. In his presentation on the project, Julian Soles, the company’s Head of Technology Development, Mining and Sustainability, explained that while Anglo is in conversations with OEMs, there remain gaps in the technology available. “Platforms are already electrified, but what’s not developed is a replacement for the diesel engine, so we are building a hybrid hydrogen-battery engine that is going to replace that diesel engine on the platform,” he said. “We are very comfortable that fuel cells can perform in a mining environment today, so we are using off-the-shelf fuel cells and hydrogen tanks.”
According to data collected by Hitachi, it appears that loading and haulage accounts for over 50% of all fossil fuel use in the mining sector, making this segment sound like “a quick win”, but the wide variety of loading and haulage equipment in the sector makes it difficult for OEMs to build a one-size-fits-all solution. “Globally, haulage fleets are very diverse; there are many different haul profiles that are influenced by geography and environment. More than one solution will be required to meet the industry’s expectations,” said John Schellenberg, Mining Product Manager, Trucks, at Hitachi. The company is actively pursuing two development pathways: electrification and energy management, with hydrogen as a strong partner to the electrification pathway. “We see the development of the haulage unit as the easiest part of the equation: we already have a solid modern electrified platform to work from. Our development challenge consists of repowering the current product,” Schellenberg added.
Other players, including Engie, are also working on the development of a fuel cell and battery power train for mining trucks. But one of the issues with replacing diesel with hydrogen in a hybrid haul truck is that more frequent refuelling is needed: approximately six hours of operation is achievable based on a 35% load factor, according to Hitachi, but this is still much lower than what is achievable with diesel. This has to be taken into account when planning operations with a fuel cell haul truck. Still, this is considered a minor challenge by OEMs, with hydrogen supply and infrastructure seen as a much trickier obstacle to overcome.
Building up the supply chain
While there are still some gaps to fill in hydrogen fuel cell equipment, the biggest hurdle in the development of the industry is infrastructure. In current mobility projects, miners have to build the hydrogen supply on site, but not everyone in the industry wants to become a hydrogen producer. And even if they do, the manufacturing capacity for electrolyzers is currently very limited.
Speaking in a panel focused on the Green Hydrogen Consortium, Michel Carreau, Global Director of Hybrid Power at Hatch, pointed out: “Right now, suppliers are racking their brains on how they can deliver five, six or ten projects within two years: they have a manufacturing capability of making one electrolyzer in 18 months. You need to create a supply chain able to meet the challenge of developing more projects within the same year.”
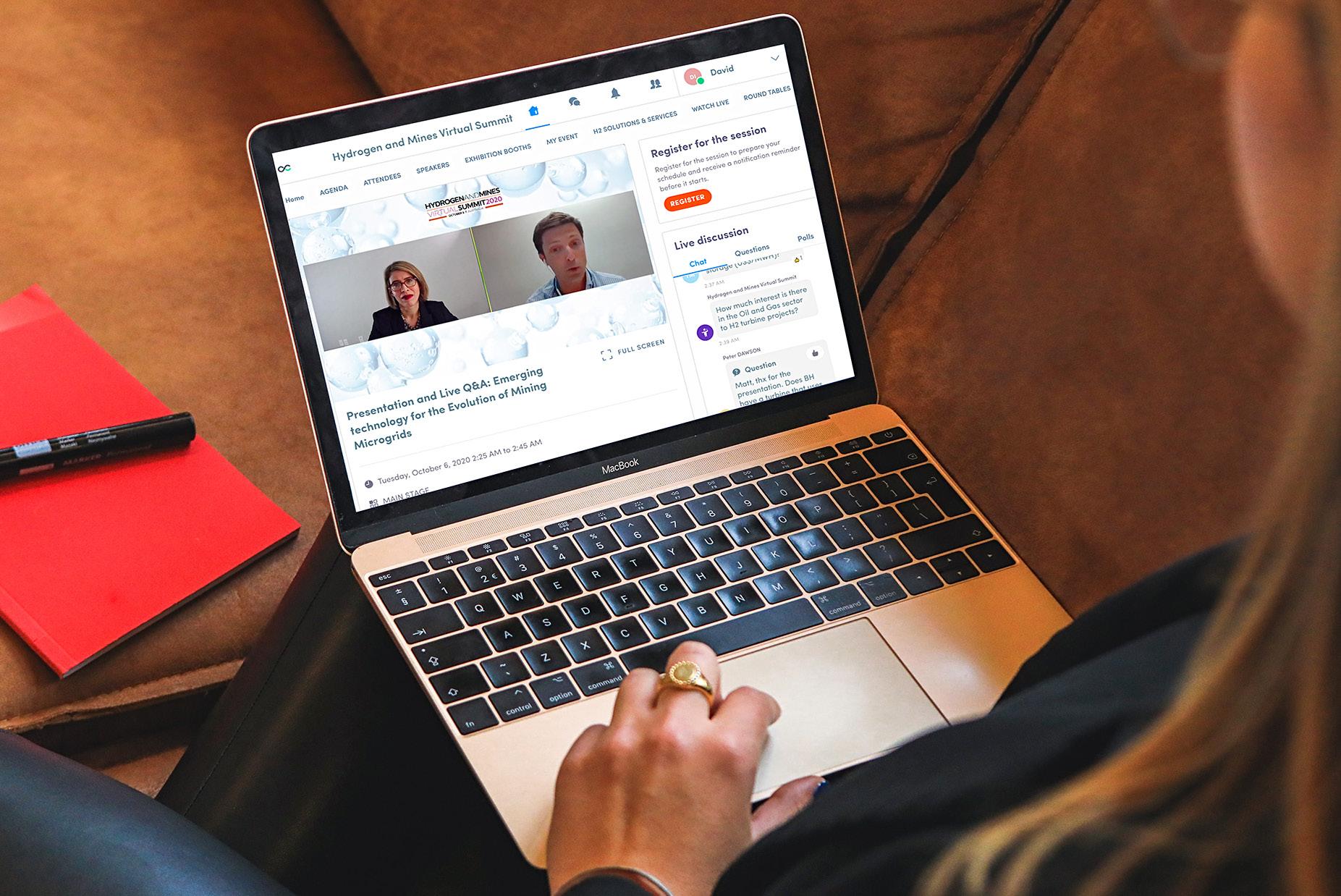
According to him, the real challenge is in going from 1 MW or 2 MW projects to 10 MW or 20 MW projects. “We really need to do bigger projects to learn and streamline so that it becomes very easy: now, to do a 100 MW wind project, it’s the same challenge as 20 MW. But the jump is from now to 20 MW, there are no projects yet,” he said. The industry is currently in its pilot phase, but there are many efforts to scale it up. Hatch, for instance, is currently working on two 20 MW projects, one in Quebec and the other in the US. ABB and Hydrogen Optimized also recently signed a memorandum of understanding to develop large-scale (100 MW) green hydrogen production systems.
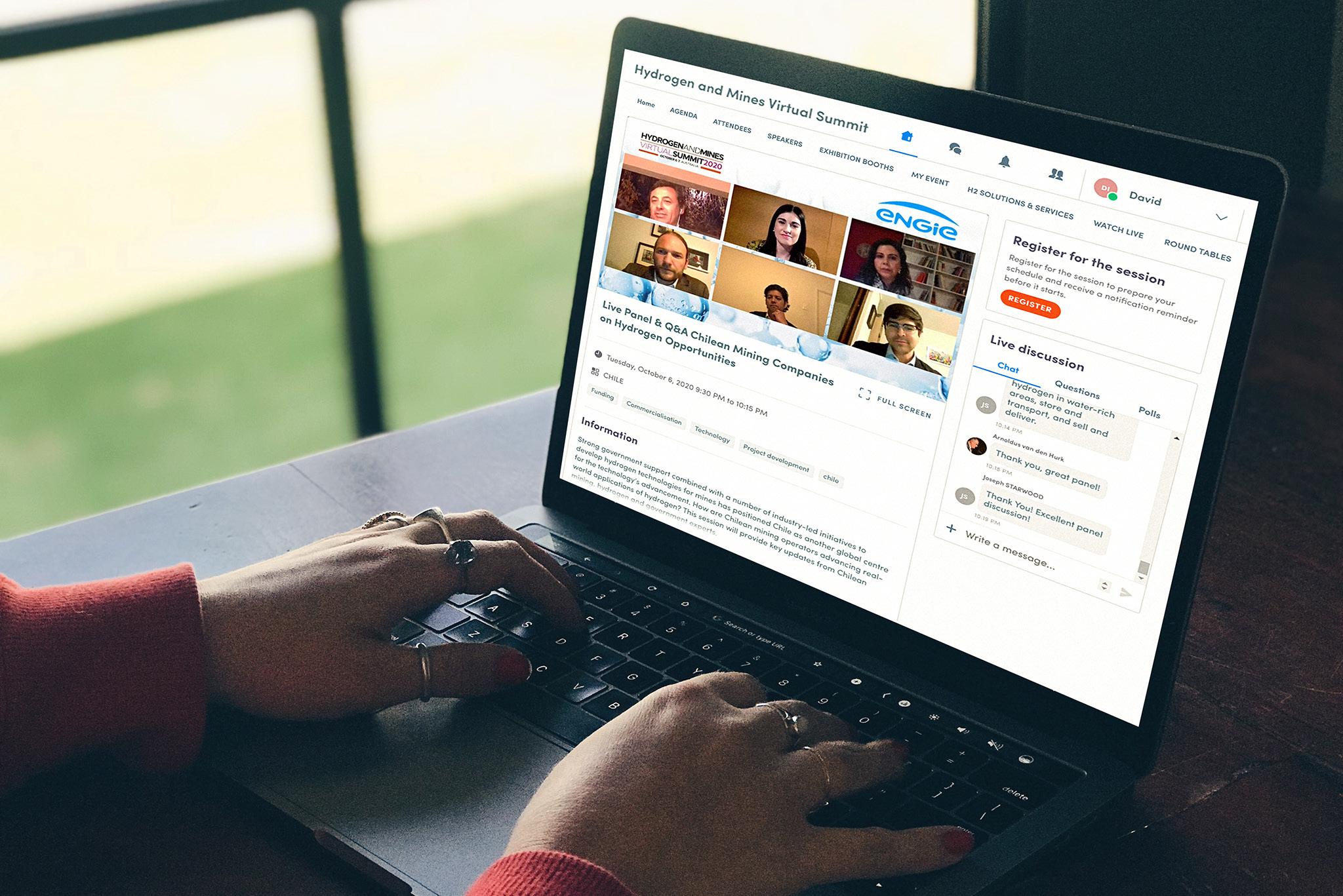
On the government side, the Australian Renewable Energy Agency (ARENA) is actively pushing to support larger-scale projects. The agency has so far invested around A$55mn in supporting pre-feasibility demonstrations and small-scale hydrogen projects, but its recently announced A$70mn Hydrogen Deployment Funding Round is clearly looking for initiatives that can pick up the pace: the seven projects shortlisted so far all have plans to deploy 10 MW or larger electrolyzers. “Through that process, we are aiming to provide grant funding to support at least two projects that demonstrate larger scale renewable hydrogen production activities,” said Zoe Von Batenburg, Manager of Business Development and Transactions at ARENA.

Developing the right standards
The development of larger-scale projects will not only help build capacity in the industry; it will also allow for the creation of the right regulatory environment for market growth. Standards Australia is working on the adoption of technical and safety standards for the domestic hydrogen sector, particularly in terms of production and refuelling stations, as well as storage of hydrogen, both in liquid and gas form. “Having people like ARENA to fund these projects is very important, from our perspective as the body looking to standardize the industry. People want to know what the benchmark is, and having the ability to run these projects, capture the learnings and standardize the processes is important for everyone,” noted Emelia Addo-Appiah, Stakeholder Engagement Manager at Standards Australia.
In Chile, the government has committed US$200mn to the development of its hydrogen market, within the framework of its commitment to carbon neutrality by 2050. Corfo, the government body in charge of innovation and new industries, started developing a green hydrogen strategy three years ago. Its first focus was to kickstart demand, by working on the development of fuel cell mining equipment. Now the Chilean Ministry of Energy has taken over the work achieved by Corfo to create a national hydrogen strategy by the end of 2020. “We are working on three fronts: market growth, safety regulations and permitting, and international outreach,” said Benjamín Maluenda Philippi, Unit Head for New Energy Carriers at Ministry of Energy, adding that it was time to create the capabilities in the public sector to permit hydrogen projects efficiently and correctly.
Consuelo Glaría López, Hydrogen Solution Developer at Engie BUH2 in Chile, identified regulation as one of the main challenges for hydrogen commercialization today. “There are plenty of international standards for hydrogen, but they were not developed for heavy duty applications like mining trucks. Until those standards are available it won’t be possible to massively introduce hydrogen in the mines. Chile, Australia and other mining countries have a responsibility to develop those standards,” she said.
At SmartEnergy, Managing Director Christian Pho Duc agreed: “Our main challenge is on the permitting legislation side: it’s lagging behind even in leading countries. In the process of judging whether an electrolyzer is an industrial thing or an energy thing, and which laws and rules apply, there’s a lot of thought ongoing but it’s not finalized. That’s one thing we need to think about: supporting a fast track of this permitting process.”
Small-scale applications
With the availability of specialized equipment, growing electrolyzer manufacturing capacity and development of international standards, the cost of hydrogen solutions for mining is set to come down dramatically. ARENA predicts that electrolyzers will follow the same cost curve as solar PV: a 25% reduction in cost for every doubling in capacity.
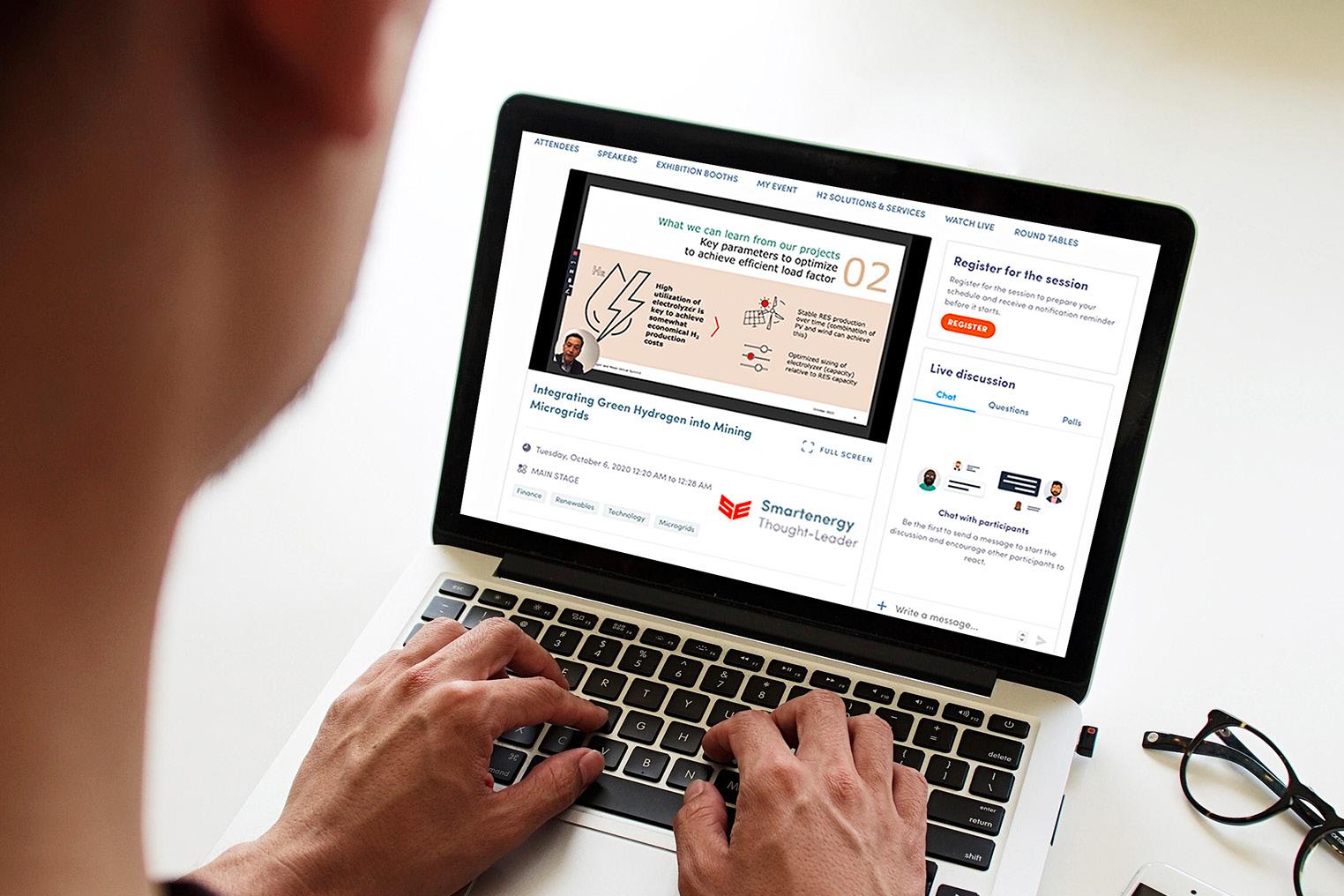
“From a commercial perspective obviously the cost of green hydrogen production and transportation are still a challenge. Electrolyzer cost and energy input are the main elements that companies should focus on to achieve cost reductions. The capital cost of large-scale solar PV and the cost of electrolyzers are both expected to fall, which should give encouragement to companies to start with hydrogen introduction into microgrids,” said Bernardene Smith, Associate Director at KPMG. She added that the collocation of hydrogen production facilities with the renewable production will further contribute to making hydrogen in microgrids viable, by reducing transportation costs.
In his presentation, Smartenergy’s Pho Duc pointed out that high utilization of the electrolyzer is key to reach economical production costs. “Electrolyzer sizing needs to be adapted to be the most efficient possible, as reducing the levelized cost of hydrogen to the minimum from the start is crucial,” he said.

In the meantime, some companies are working on interim solutions, to allow mining companies to get comfortable with hydrogen with limited investment. “You don’t necessarily need to go straight to fuel cells, there are other types of technologies that provide an interim for existing mining operations,” said Warner Priest, Head of Emerging Technologies at Siemens. He mentioned South Australian manufacturer Hydrogen Direct Injection (HYDI), which has built a hydrogen injection system they can fit to vehicles to reduce emissions from 25% to 30% and increase efficiency around 10% to 15%. “Those units could also potentially be put on stationery equipment.
So there’s a way to go from pure diesel to a diesel and hydrogen mix and then to hydrogen fuel cells,” added Priest.
For Julien Colas, Global Partnerships and Solutions Developer at Engie Hydrogen, it makes a lot of sense to explore hydrogen in smallscale applications at present. “We talk a lot about scaling up because it’s the challenge to decrease the cost, but before scaling up we need to start, and small applications are a good way to test the technology. Another important change in the rise of the hydrogen economy is the cultural and organizational change required. Starting with small projects and pilots is also a good way to test the cultural and organizational change for you,” he said.
NUGGETS OF WISDOM
Here are a few pearls of wisdom gained from short-form sponsor presentations at the Hydrogen and Mines Summit.
SMA
A holistic supply made of high-quality solar and wind generation, a fast-acting battery, a power plant manager and long-term hydrogen storage is needed to minimize risks related to load volatility, commodity prices and short mine lives. Ideally, all technology should be modular.
Transform Materials
Blue hydrogen production through methane conversion using microwave hardware can present key advantages compared to water electrolysis: it requires about 40% less energy and produces high-value co-products such as acetylene.
HFW
The miner in hydrogen projects is not just a customer receiving a supply or service. They are intimately involved in all of the project components, and as such, must consider potential contract issues both from a customer and from a supplier’s point of view, and keep in mind the collaboration aspects of contracting.
Hydrogen Optimized
Over the past 20 years, only 250 MW of new electrolyzers have been installed, most under 1 MW. Today, we are talking about one mining site that needs a system larger than the sum of every electrolyzer system built in the past 20 years. New, fundamentally different large-scale water electrolysis technology is required for the mining sector.