
9 minute read
The race for green milestones
projects
The race for green milestones
Advertisement
Over the past few years, the mining sector’s transition towards carbon-neutral power and fleet options has been ramping up. This is due to both a stronger focus on climate change in global politics and business, and the growth and maturity of the renewables sector, which has pushed down prices and increased efficiencies. Renewables are no longer considered “alternative energy” — they have become a viable option to consider on all mine sites, one that developers cannot afford to overlook in their economic feasibility studies.

PHOTO COURTESY NMG
In this article, we explore the ambitious milestones set by three different miners: the construction of the largest off-grid hybrid solar plant on B2Gold’s Fekola Mine in Mali; the development of the first 100% electric open-pit mine at Matawinie by Nouveau Monde Graphite; and the full electrification of the underground Borden Mine by Newmont Goldcorp. Through these examples, two trends are emerging that could determine the future of the global mining sector: in remote mines, solar and battery technology are shifting the power paradigm, while in grid-connected sites, the 100% electric mine is close to becoming a reality.
Leveraging solar efficiency at Fekola
In August 2019, B2Gold announced its intention to build a 30 MW solar plant at its Fekola mine site in Mali. Energy from the plant will be added to the 60 MW of heavy fuel oil (HFO) capacity already on site, and a 3.5MWh battery storage facility will be added for more efficiency. The US$38mn project is expected to be completed by the third quarter of 2020 and will save B2Gold over 13 million litres of fuel per year, with a four-year payback period.
Dennis Stansbury, Senior Vice President of Engineering and Project Evaluations at B2Gold, explains that the drop in solar panel and battery costs was what made this project so economically viable. «A plant like this three or four years ago would have had a 10-year payback.” With all fuel coming by road from the Port of Dakar over 1,000km away, logistics was an important factor in the decision to build the solar facility on site.
“We’ll save 2.5 to 3 cents per KWh on our power, which will create about a 7% decrease in our process operating costs, since power is a very high percentage of those. We’ll be producing over 63,000MWh of power per year, and the CO2 savings are close to 39,000 tonnes per year. So it’s a very good thing to do both environmentally and economically,” Stansbury adds.
This is the second solar plant that B2Gold has installed on its facilities, after the 7 MW plant built at the Otjikoto mine in Namibia. Though much smaller than the Fekola project, the Otjikoto plant already provides 13% of the energy consumed at the mine, and saved B2Gold 2.4 million litres of fuel in 2018.

FEKOLA MINE COURTESY B2GOLD
The company has opted to build both plants in-house, instead of using Engineering, Procurement, Construction and Maintenance (EPCM) contracts or power purchase agreements. According to Stansbury, this doesn’t necessarily save any money, but it does make projects more efficient. “When we build our own processing plants, they come up on time and within budget, and the ramp-up to full production is achieved in weeks, not months. We also control the manpower, and after building a plant we already have trained operators: the people who built it become the people operating and maintaining it, which is an enormous advantage,” he explains. Still, B2Gold will be upgrading its recruitment criteria and looking for people with electrical engineering degrees to work on the plant, in order to ensure maximum operating efficiency. Of course, building a solar plant as a mining operator also comes with its challenges, most notably in terms of procurement: while 30 MW of solar capacity is not small, it pales in comparison to the 500 MW mega solar projects being built in India or China. As a result, B2Gold has chosen to team up with Suntrace and its partner BayWa to ensure orders are delivered on time. “BayWa is involved in purchasing a lot of solar power each year, so we’re using a bit of their clout to make sure that our orders don’t get set aside for a much bigger solar plant somewhere else,” Stansbury says. This is the second solar plant that B2Gold has installed on its facilities. Though much smaller than the Fekola project, the Otjikoto plant already provides 13% of the energy consumed at the mine, and saved B2Gold 2.4 million litres of fuel in 2018.
For him, solar is becoming the obvious choice for mining operators looking for cheap off-grid power: pricing is already at a competitive level, and the technology is improving daily, with panels performing well even in West Africa’s infamous dust storms. The recent State of Play: Strategy survey of global miners seems to confirm that opinion: in it, 78% of Australian mining executives said they believe that renewable and solar energy will eventually become “the most widely used energy source in the industry”.
Stansbury adds: “Solar is going to keep booming. Solar power is close to free once it’s up and running: to give you an idea, the cost for our HFO power at Fekola right now is around 16 cents per kWh; once the solar plant is online [and capital costs have been amortised], the cost for that power will be less than one cent per kWh for operations and maintenance. There’s no comparison once you got it there.”

Borden Mine (courtesy Newmont Goldcorp)
Borden mine project: saving power costs by going electric
It sounds counterintuitive, but according to Maarten van Koppen, Energy and Sustainability Manager at Newmont Goldcorp, using an all-electric fleet in the underground operations of this new Ontario mine will save Newmont Goldcorp a lot of electricity. “In most jurisdictions, you have to ventilate for air quality to provide a healthy work environment. So, if you don’t have any diesel exhaust gases, your air quality drastically improves. On the main ventilation, we’ve reduced energy use by about half compared to a diesel fleet, and on the secondary ventilation, the savings are even larger. And of course, if you don’t ventilate as much, you also save on fans and ventilation tubes… it’s a bit of a ripple effect and there are a lot of savings,” he explains.
Newmont Goldcorp announced its intention to make Borden an all-electric mine back in 2016. Three years later, production has started and is being ramped up to reach commercial production levels later this year. The decision to go electric aligns with stakeholder expectations that the mine “remain invisible”, according to van Koppen. Since the mine is located very close to a lake enjoyed by the local community, the company wanted to remain as discreet as possible, and with low noise pollution, an electric fleet is as discreet as can be.

MAARTEN VAN KOPPEN Energy and Sustainability Manager at Newmont Goldcorp
But finding the business case was not as straightforward. “It seems so evident when we talk about it now, but we went through a bit of an evolution trying to find out what the business case was,” recalls van Koppen. “The first step was fuel savings on the vehicles themselves, then the next stage was to save on heating fuel, and ventilation is where we ended up seeing the biggest cost savings.” He adds that going electric had knock-on effects: a fully diesel mine would have required more power than the site’s existing and planned additional grid connections could provide. “We are limited in the amount of electricity that we can get from the grid there. So by going electric and setting up our mine as an energy-efficient place, we could avoid very costly and time-consuming permits, a transformer station and transmission lines. When we added all of these things up, it made the business case for going electric,” he says. Being a first-mover in the electrification of mine sites can be a challenge: when Newmont Goldcorp embarked on this adventure, there was no commercial electric mining equipment readily available. “We had to challenge the original equipment manufacturers (OEM) to supply electric equipment. Some of them had already started designing battery-electric equipment, and we found two good partners in McLean Engineering and Sandvik Mining that supply our equipment now, and it’s working very well. Of course, there are a lot of issues that come with introducing new equipment, but working together with the OEMs we’re able to overcome those,” adds van Koppen. Newmont Goldcorp announced its intention to make Borden an all electric mine back in 2016. Three years later, production has started and is being ramped up to reach commercial production levels later this year.
One of the issues the company encountered had to do with the harmonics generated by the variable frequency drives installed for fans, pumps and other equipment. “We suspected and allowed for harmonic filters, though we knew we had to field adjust once installation was completed” he says. Some of the chargers on the equipment didn’t respond very well to these harmonics, and Newmont Goldcorp had to go through a trial-and-error process to reprogram or swap these chargers. “This is the kind of hiccup you only find out once you are in operation,” he notes.
And while the company is also looking at integrating solar energy on some of its remote sites, van Koppen believes 100% electric mines will be the first milestone to be reached in the industry. “We are looking to go fully electric at Borden at least for the underground portion, and I know that other players are looking to do the same thing. It will be a bit of a race to see who can get there first,” he says.
Electrification as a win-win for Matawinie
Nouveau Monde Graphite is planning to build the world’s first 100% electric open-pit mine in Quebec — a somewhat natural decision, given that graphite is one of the main elements used in lithium-ion batteries for electric vehicles.
“We first looked at where would could sell this graphite, and then we asked our engineers to look at the option of using electric trucks on the project and realized it was possible to use the very technology we sell to. For us it’s a win-win on all levels, so we thought: ‘if we don’t do it, no one will’,” says Eric Desaulniers, the firm’s CEO.
Being hooked to the Hydro Quebec grid was a significant advantage: the company already has access to 12 MW through the existing line, and is building extra connections to bring the 200 MW needed for the project without disturbing the supply for surrounding communities.
But, as was the case for Newmont Goldcorp’s Borden Mine, the issue is in finding the right electric equipment for the site. Desaulniers explains: “The challenge is to convince the OEMs that this is the mine of the future and they need to move as quickly as possible. For them, this is hurting the business: they would much prefer to keep selling their existing products. We need to convince them that they need to move quicker than their competitors in order to secure market share.”
The firm is looking at different options, not just for electric vehicles, but also cable electric solutions readily available for drilling or digging. They will also need to find the appropriate software solutions
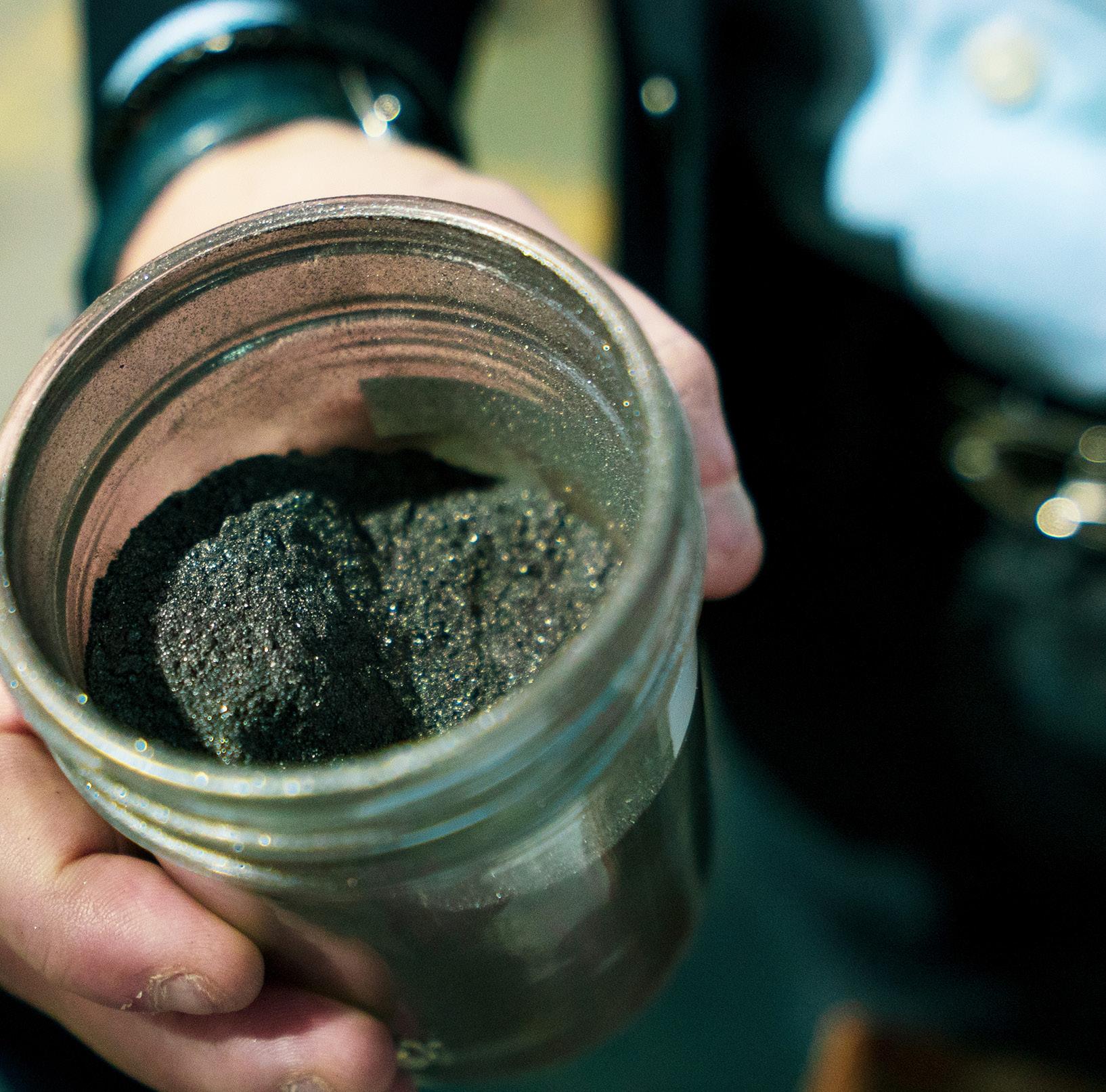
PHOTO COURTESY NMG
to handle the operations of an all-electric mine. “We need to design processes with charging times in mind. The challenges are different for a battery-powered mine, so we will be visiting different all-electric operations in the next few weeks to find out what they are using in terms of mine management,” adds Desaulniers.
Nouveau Monde Graphite is targeting commercial production by 2022, so it’s going to be a busy couple of years — but the company is confident it will eventually find all the equipment it needs to be fully electric. “We really want to be all-electric on Day 1, but there’s still a lot of work to be done,” says David Lyon, Director of Electrification and Automation. “So we’re looking at the bridging technologies that exist. We are confident that the hauling trucks and a lot of the equipment will be all electric, but there may be some parts that will be more difficult to start with. Still, by 2025 everything will be electric.”
The benefits will be tremendous: no fuel expenses, low maintenance costs, regenerative braking, and peak shaving on grid power prices through battery storage.
Once it’s all in place, the benefits will be tremendous: no fuel expenses, low maintenance costs, regenerative braking that will allow the trucks to charge more energy downhill than they use uphill, and peak shaving on grid power prices through battery storage. For the team at Nouveau Monde, every new mine should put all-electric operations on the table. “Sometimes it can be more difficult if the mine is remote, they may have to build their own electricity source (a solar power plant for example), but in the end it could still be cheaper for the mine. Everyone needs to make the effort to look at the technology out there and consider an all-electric mine,” urges Desaulniers.