
5 minute read
Mine Electrification: The future is already here
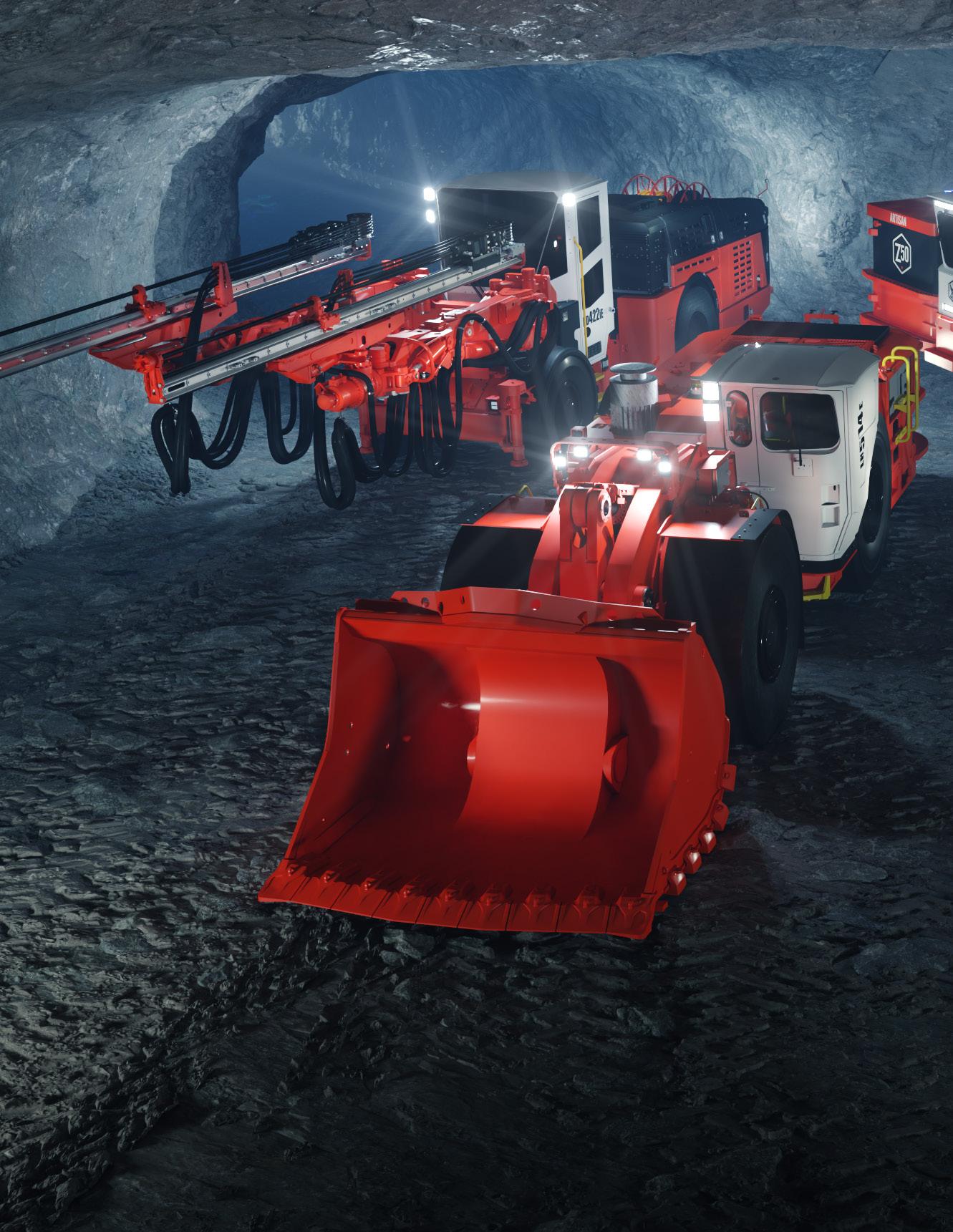
MINE ELECTRIFICATION: The future is already here. A discussion with Mats Eriksson President, Load and Haul Division at Sandvik Mining and Rock Technology
Advertisement
Many miners think of electrification as a valid option for the future; some like Newmont Goldcorp and Nouveau Monde Graphite are banking on it, developing fully-electric mines as we speak. But for Mats Eriksson, President, Load and Haul Division at Sandvik Mining and Rock Technology, electrification is not the future — it is the present.
Sandvik has already delivered 600 electric trucks and loaders for the mining sector. The company is working with Newmont Goldcorp on the all-electric Borden Mine, having already delivered electric loaders for the development phase and scheduled to provide electric trucks once the mine is ready to start operations. And through its recent acquisition of Artisan Vehicle Systems, Sandvik is now also supplying Kirkland Lake Gold’s Macassa Mine with electrified equipment.
Energy and Mines speaks to Eriksson about the pathway to electrification for the mining sector and the mindset change that is required to switch to battery-electric fleets.
Energy and Mines: What are the key drivers for mining operators to switch from diesel to electric equipment?
Mats Eriksson: If I look at it from the point of view of what this means for the mining industry, this is a very rare opportunity to combine health, sustainability and cost improvements. By improving your cost structure you also get benefits like better health environment and you’re also more sustainable. The cost reduction comes mainly from lower ventilation requirements for battery electric equipment. And another issue electrification helps to solve is around cooling: diesel engines generate a lot of heat, but moving to electric you can reduce that as well and cut cooling costs. There are a lot of positives with moving to electric.
This is not new to us at Sandvik: we have been supporting the mining industry to go into electrification for years. We have also been a frontrunner in automation and fully-automated mines.
E&M: Some miners have told us there is not enough on offer for electric trucks on the market, and this is what is slowing down electrification efforts. Why is it such a challenge for conventional OEMs to start manufacturing electric equipment?
ME: If you hear any miner complaining about not getting electric trucks, ask them to get in touch with Sandvik! I’m being bold here, but it’s true: there’s a very limited offering on the market at the moment. The main reason is that it’s really difficult to move outside of the conventional world of diesel loaders and trucks. When you start moving outside of that world, it gives you completely different opportunities with different technologies. But it’s difficult for companies that have been developing diesel trucks and loaders for decades to start thinking about the application in a different way. If you look at the car industry, Tesla came out of nowhere and they were thinking about how to make electric cars from scratch, not converting existing cars. That’s what most OEMs have a problem with: rethinking the whole application.
At Sandvik, we have a separate organization for the battery-electric vehicles specifically for that purpose: you cannot use what you have been using in conventional loaders and trucks, you have to rethink everything and work with a whole new world of suppliers and systems. Getting your head around that might be an issue for conventional OEMs.
And of course, when you have all your knowledge, investment and core competences all around a certain technology area, you don’t want to lose that. Changing the paradigm means putting aside what you have been investing in for years, so it can of course be a little counterintuitive. That’s why the mining industry today is still heavily diesel-reliant. But it will change, so it is better to get on it now instead of waiting for the competition to get better.
E&M: What are some considerations that operators should keep in mind when they look into electrifying a mine site?
ME: Putting it simply, you don’t need to change anything — you can move to electrification today.
You should think about optimizing your infrastructure and mining method, for example take advantage of gravity: recharge while you go downhill. For this, you should be fully loaded when you go downhill and empty when you go uphill, which is the opposite of what most miners are doing, but it can be arranged in an underground mine.
Then, know that you will reduce ventilation requirements and cut costs, but you still need air to circulate, so you have to think about how to circulate the air with less ventilation. There are just some things to think about, but what I suggest is to contact and work with the OEM you’ve chosen and go through the possibilities and restrictions with them. The knowledge and experience is already there in the market, it’s nothing you need to reinvent.
People tend to think that by going fully electric, the electricity consumption will go up. From the calculation we have done, that’s not true: the extra electricity needed to charge the equipment is more than offset by the reduction in ventilation and cooling brought by the use of such equipment. And because of battery swapping, charging the battery for some time when it’s not being used, you get a more steady flow of electricity consumption, reducing peak consumption.
E&M: What are some of the best options for mines looking for flexible solutions to drive down their emissions but not go fully electric?
mine, they could think about going electric in the expansion. In the transition, you could have mixed mines. We are also working very closely with engine manufacturers to provide as clean diesel engines as possible, with particle filters and other elements. That helps, but you still have the issue of heat. Really, my question is: why not go fully electric? Like I said before, this is a rare opportunity to save costs while being more sustainable and providing a healthier environment.
E&M: What role can automation play in the transition towards 100% electric mines?
ME: There are two things we would like to do with automation: increase productivity thanks to continuous operations, even in a blast situation; and remove people from dangerous environments. But really, it does not make a huge difference whether you automate a diesel fleet or an electric fleet. Automation is something that’s growing very fast in the market at the moment.
E&M: Finally, what do you see as the main goals or concerns for future mining?
ME: It depends from which angle you start looking at this. There are a lot of technologies that can be applied to the mining industry today to provide a better environment. Automation is a growing area, electrification is the next big step in the mining industry. In fact, the electrification of the mine is not the future, it’s here today if you’re ready to take the step. There already are mining companies investing in it so it’s clear that’s going to happen. But looking a bit further on, what I see is that you have a lot of unexplored areas in the world. Mining is going to go deeper underground, to unfriendly environments full of heat and moisture, and it’s only by using electrification that miners will be able to explore these areas cost-effectively. There’s also mining under the sea: a lot of ore sits below the seabed, and it’s not a simple thing to get it out, but there will probably be some exploration, helped by new technologies.