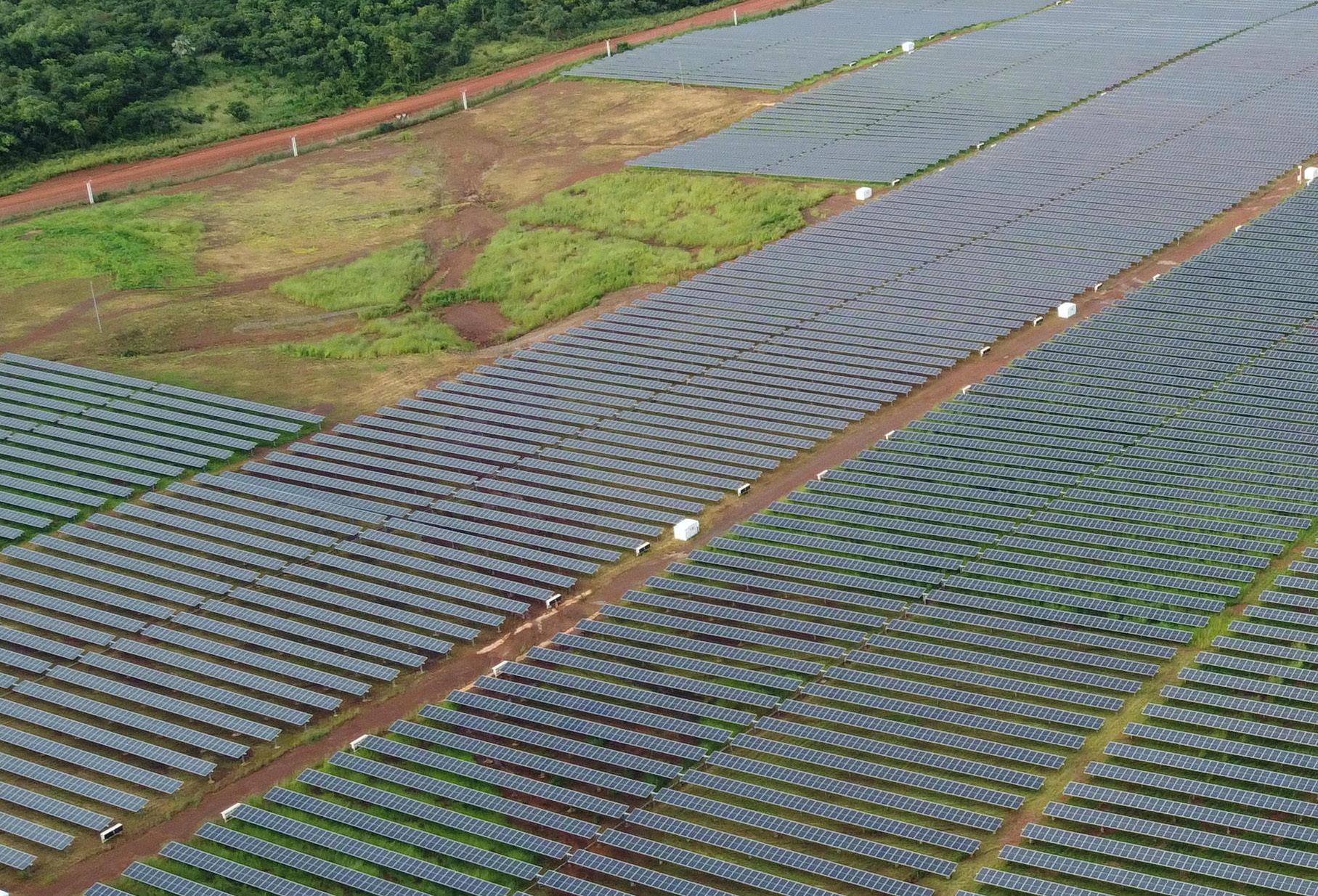
9 minute read
The time to act on 2030 targets is running out
Interim decarbonization targets are looming ever closer, but the path to a green energy supply is anything but straightforward for miners. Martin Schlecht, Director Engineering & Projects at Dornier Suntrace, shares his insights on the main remaining challenges.
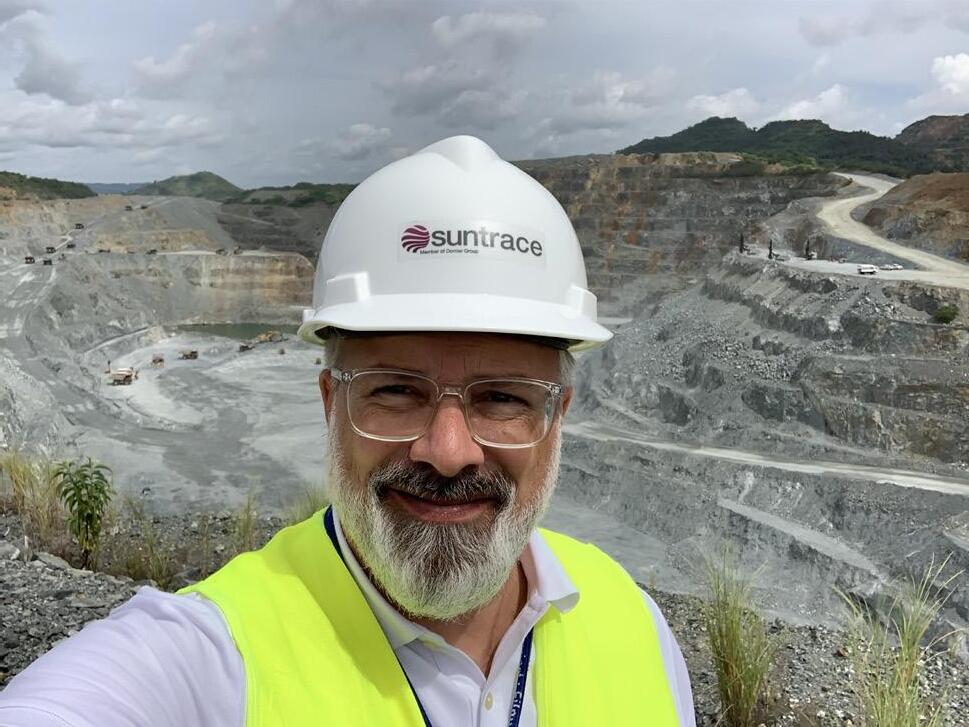
ENERGY AND MINES: What do you see as some of the essential steps required to facilitate the shutdown of HFO engines during daylight hours for an off-grid mining operation?
MARTIN SCHLECHT: Shutting off all engines means you don’t have any spinning reserve available from the engines. So you need to replace the spinning reserve with the battery itself, with all its operational requirements. Engines are the safety net for off-grid operations, that every miner is used to, and it can be an emotional step to switch them all off in the first place.
It’s important to track the weather forecast, as you should not switch off all engines if you don’t have enough sunshine. At Fekola, we have a sophisticated weather forecasting system that gives operators a lot of advanced warning to get engines up and running: the clouds should not take you by surprise. Specific to HFO engines is that they should not be started more than once a day, as more starts would increase the maintenance significantly. So that sequence also needs to be optimized for each day’s operations.
It’s also a matter of how big the solar plant is and how many days during the year it will provide enough energy to switch off all engines. That’s a commercial evaluation: you find the optimum size of the solar plant based on whatever cost of energy or payback period against fuel cost savings you want to see.
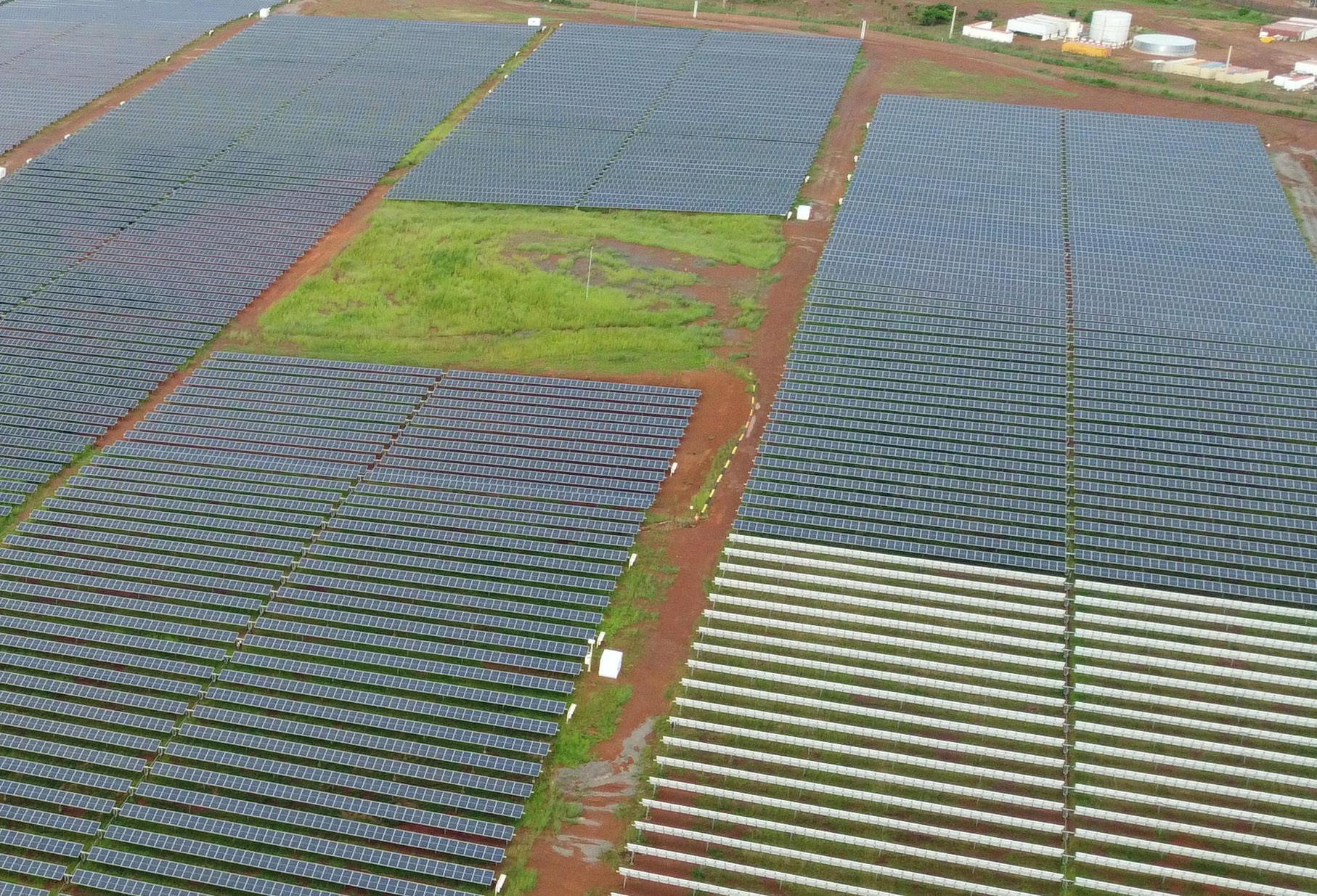
But I think it will be a mind-blowing experience to be around the mine when suddenly there is silence in the powerhouses and the mine is still operating at full load.
E&M: What are your key takeaways from your experience with the off-grid solar-battery hybrid system for B2Gold’s Fekola gold mine in Mali?
MS: We did an assessment of the performance of the powerplant after one year (which was last year in July), and it exceeded the calculated performance. It delivers the expected 20% fuel savings, and since fuel prices went up sky high when Russia attacked Ukraine, the cost savings were higher than anticipated. So it has proven to be a hedge against the volatility of the fuel cost in a positive way.
The operational experience at the Fekola gold mine has been positive so far, and they are able to operate and maintain it with their own power plant staff. We’re only involved on special occasions, so that works well. We’re already working on phase two, which involves growing the solar plant in order to be able to run on zero engines several days a year. That is definitely a sign of trust, both in the performance of the solar and battery plant but also in our work at Dornier Suntrace.
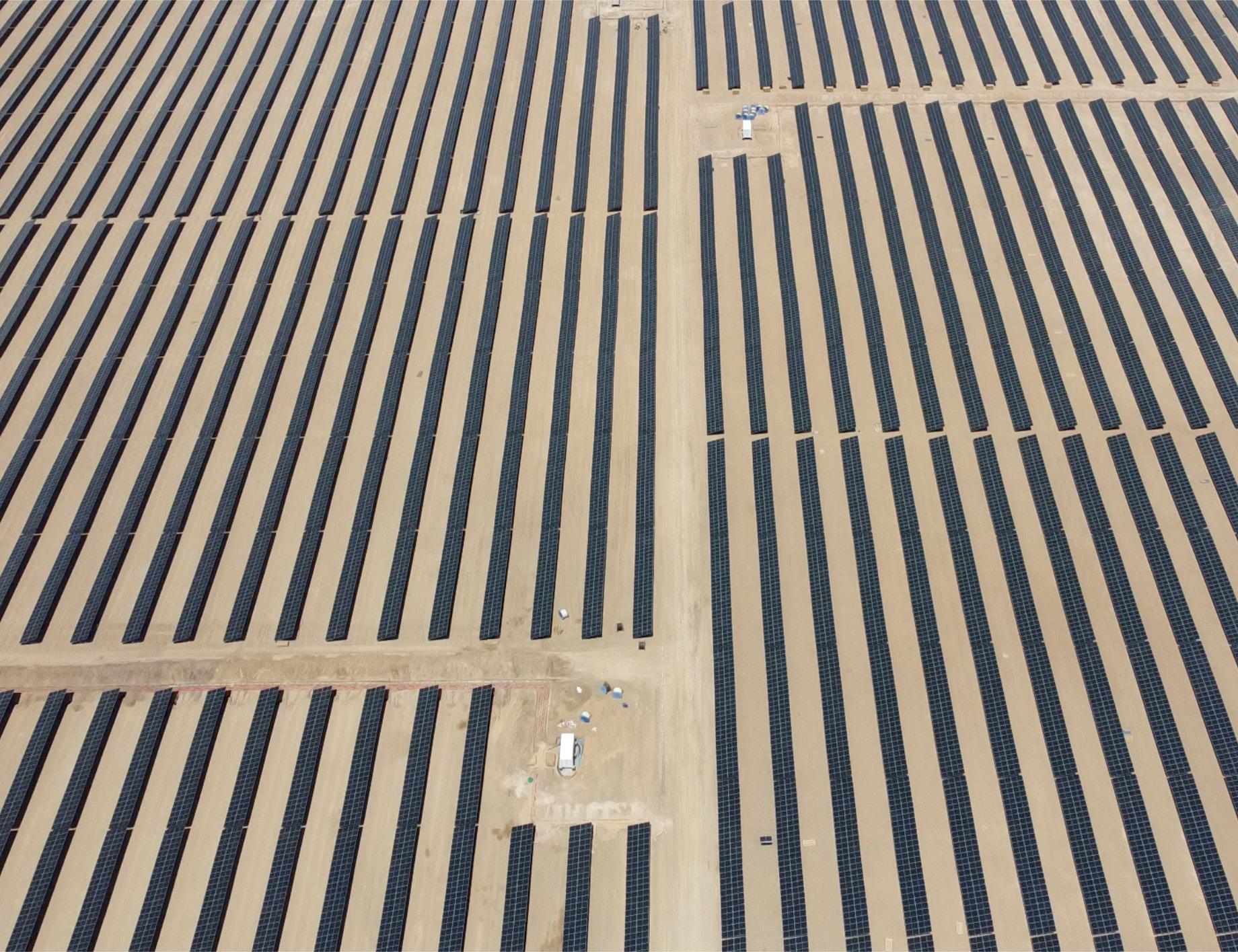
E&M: Where are hybrid solutions for mines heading in terms of new and innovative strategies to drive further energy decarbonization for remote mining operations?
MS: Last year at Energy & Mines, I presented a case study on integrating wind with solar and battery for an off-grid solution. And it showed that 85% renewables coverage can be reached at economic terms, when adding wind and solar at enough overcapacity to charge a battery. The case study showed that under used assumptions, a payback against heavy fuel cost would be possible within five to six years.
But it’s a huge Capex: the investment into such a big renewable plant can easily reach the lower three digit million range, so quite significant even when compared to the overall investment into a mine. But the annual fuel savings will be huge as well. Basically, it’s a trade-off of Capex versus Opex, and it’s also a question of whether the mine is willing to invest in renewable energy for an existing asset or explore new assets. That’s where it becomes tricky, on where to allocate the funds that the mines have, and where they generate the best revenue from their core business perspective.
And then of course, if you look at electrification of the mine fleet, there is potentially another load that needs to be supplied from renewable energy and that also will involve energy storage. You have batteries within the vehicles and at the charging locations, and that can also help you to leverage the fluctuations from the renewables. How these concepts work, how to organize the logistics for electrification and how much renewable energy you need at what time is something where we are reinforcing our team with our colleagues from our mobility section with their experience. Going forward, we will provide integrated engineering solutions that also cover the electrification of operations, including vehicle charging logistics, energy storage, conveyor systems, all integrated with the renewable energy generation on site.
In the area of mine water management, both water supply and drainage will require optimization for the usage of renewable energy. For instance, the idea of water storage as energy storage in mine water management is a whole new field, we are currently developing with our water section.
E&M: What are some of the challenges mining companies still face in trying to transition to renewable energy and address Scope 2 emissions?
MS: We work mostly with gold mines and most of them had good business during the last years since gold prices remain high. So for them, investing in renewables from their own funds is not so much of a concern, at least not in the sizes and dimensions that we’re supporting them currently. Still, some mines are moving, and some are still working on their options. However, when it comes to delivering on the 2030 decarbonization commitments that most mining companies have made, the time to act is running out. It is also relevant to note that electricity is only responsible for one large share of the emissions on a mining site, while operations produce the balance.
Efficient conversion of mine operations to renewable energy supply requires a reassessment of all processes. At Dornier, we are working within our group on integrating both e-mobility and water management into the renewable energy supply scheme.
Some of these commitments have to convert into physical renewable power generation within the next six years, and mines need to understand that a solar project, from conception to operation, will require at least two to three years. And with the renewables push everywhere, providers like us are very busy, so the work capacity is not idle. To find a competent supplier that has time when you need them, it’s good to plan ahead. I don’t see a bottleneck in terms of technology and equipment, but I do see it around the people that are actually supporting the implementation: engineers, workforce, and contractors doing the job.
E&M: What should miners be thinking about when integrating renewable energy while trying to electrify fleets?
MS: The discussion of hydrogen versus electrification is ongoing, however recently some aspects seem to turn towards electrification. For example, Australia’s three largest miners made an announcement that they decided against hydrogen and are going to electrify trucks instead. I do understand that truck manufacturers are developing and already selling options, but manufacturing is not yet rolled out in full scale.
And when it comes to the different options to electrify mining operations, it may be good to think outside the box. Options are swapping an engine for a battery and figuring out how you charge it most efficiently alongside the truck operations, but also conveyor belts could be a substitute for hauling: it’s easier to electrify than trucks, it doesn’t need a battery, and it can run continuously from renewable electricity. For open pits, the concepts for electric trucks and charging logistics are being developed and there is no common knowledge at this point. I think you can improve further than simply swapping a diesel engine for a battery: there may be a transition in the nature of the fleet itself.
E&M: What do you think needs to be considered during the hybrid design phase to account for the shift to decarbonized fleets - i.e. electric or hydrogen-powered mine trucks and equipment?
MS: The electricity consumed by operations is, of course, an additional load, regardless of whether you generate hydrogen on-site or charge electric vehicles’ batteries: both will require green electricity. Due to the efficiency of the electrolysis process, you usually need three to five times more green electricity to produce hydrogen compared to using the electricity in the first place. Batteries have 10 to 15% loss, which is very low compared to the losses that you have when using hydrogen. So going forward, hydrogen may not have too many benefits to outcompete the electric solution day to day.
One should approach decarbonization gradually, assessing what degree of decarbonization is economic, but provides a benefit to the operations or at least keeps operations at an equivalent cost level. I would not say that every renewable investment needs to have an investment-level internal rate of return, but that is usually the way these investments are looked at. And if it’s just break-even at the cost level, that’s not very attractive as an investment. If not, there is a push to decarbonize for not losing the market, as for example could happen with Carbon Border Adjustment Mechanism taxes and the like.
For now, we only implement projects that have such a strong cost-benefit that they pay back within four to six years and bring huge savings on fuel cost. When the renewable plant is being amortized, it’s almost free of charge electricity, and the more years you have remaining to continue, the more profitable it will be for operations. And that may help the business case for hydrogen: as seasonal fluctuations occur, you could use some of the excess power you get during abundant periods to produce hydrogen-based fuel, store it, and then use it in seasons when renewables are scarce. However, these economics are still to be determined.