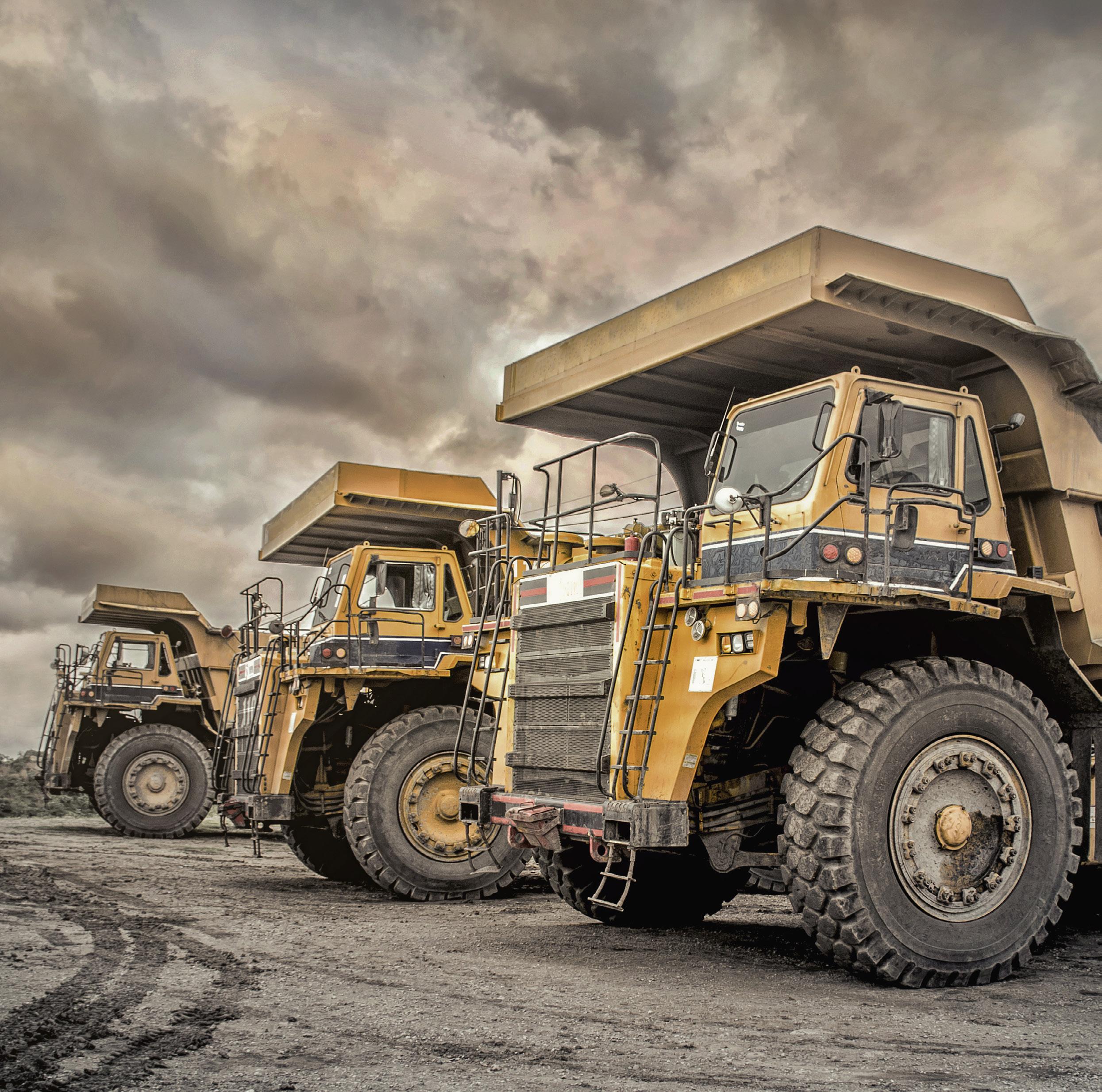
2 minute read
CONTENT POD 4: Decarbonizing Material Movement
DECARBONIZING MATERIAL MOVEMENT: TOWARDS ZEROEMISSIONS FLEETS
Now that mining’s energy transition is well underway, many miners are starting to tackle their other large emission culprit: material movement. The Energy and Mines Virtual World Congress fourth content pod focused on the solutions being explored to displace diesel in mobile equipment.
Advertisement
UNDERGROUND VS OPEN PIT
Within the theme of fleet decarbonization, a dichotomy has emerged between underground and open-pit operations. Many of the miners speaking at the conference pointed out that the transition to zerocarbon equipment underground is much more advanced than for openpit operations. “Codelco has made significant progress for decarbonizing underground. Two years ago we started with logistics and personnel equipment. Now we are moving to construction equipment, and next year we are starting to test production equipment,” said Gonzalo Ramirez, Project Manager, Electromobility and Energy Transition at Codelco, during a panel on zero-carbon fleets.
Brian Huff, VP of Technology, Artisan Vehicles at Sandvik, added that the electrified technology for underground equipment is already available. “What it took to tip the scale was the ability to swap batteries. Charging is limiting so when you scale up, that puts a choke point on the ability to recharge, but swapping the batteries means you can do that in less than five minutes, with very little downtime and impact on productivity,” Huff pointed out, though he did admit that surface mining is more of a challenge because of the size of the equipment.
Vale already has 25 batteryelectric vehicles (BEV) operating in underground base metal mines in Canada, and plans to more than double this number by the end of 2025. But electrifying underground may also require some operational changes: “Historically mining has been a batch process, but we may move to a more continuous process, which may offer benefits in energy efficiency,” mentioned Alex Mulloy, Mining Engineer at Vale.
MINER-OEM COLLABORATION
Various technologies are being developed to tackle the immense challenge of decarbonizing open-pit mining equipment, including hydrogen fuel cells and BEV, but so far it isn’t clear which will provide the most efficient solution. “We believe it won’t be a winner takes all: mine sites have such different ecosystems and inputs that the right solution will depend on regeneration capture, mine site design, etc,” said Robert Schaefer, Director, Mining Accounts, Growth and Innovation at Cummins. He added that these technologies should become commercially available within the next decade.
But one thing’s for sure: in order to tackle this challenge, miners and OEMs must continue to collaborate. One of the platforms they are using for this purpose is the Innovation for Cleaner Safer Vehicles (ICSV), an initiative by the International Council on Mining and Metals (ICMM). Presenting on the topic, ICMM’s Sarah Bell, Director of Health, Safety and Product Stewardship explained that the ICSV brings together 27 of the world’s leading miners and 19 OEMs to collaborate in a non-competitive space. “We need to create tools for change that make sure the commitment on both sides is real: maturity frameworks and practical tools for members to move at their own industry-informed pace,” she added.
SPONSORS’ CORNER
Intelline pointed out that more efficient combustion engines could already help displace CO2 emissions from vehicles, as well as enabling the transition to cleaner fuels when they become available.
Tembo 4x4 e-LV presented the benefits of switching heavy duty 4X4 vehicles’ drive trains to electric: zero emissions, low maintenance costs, less downtime and faster return on investment.