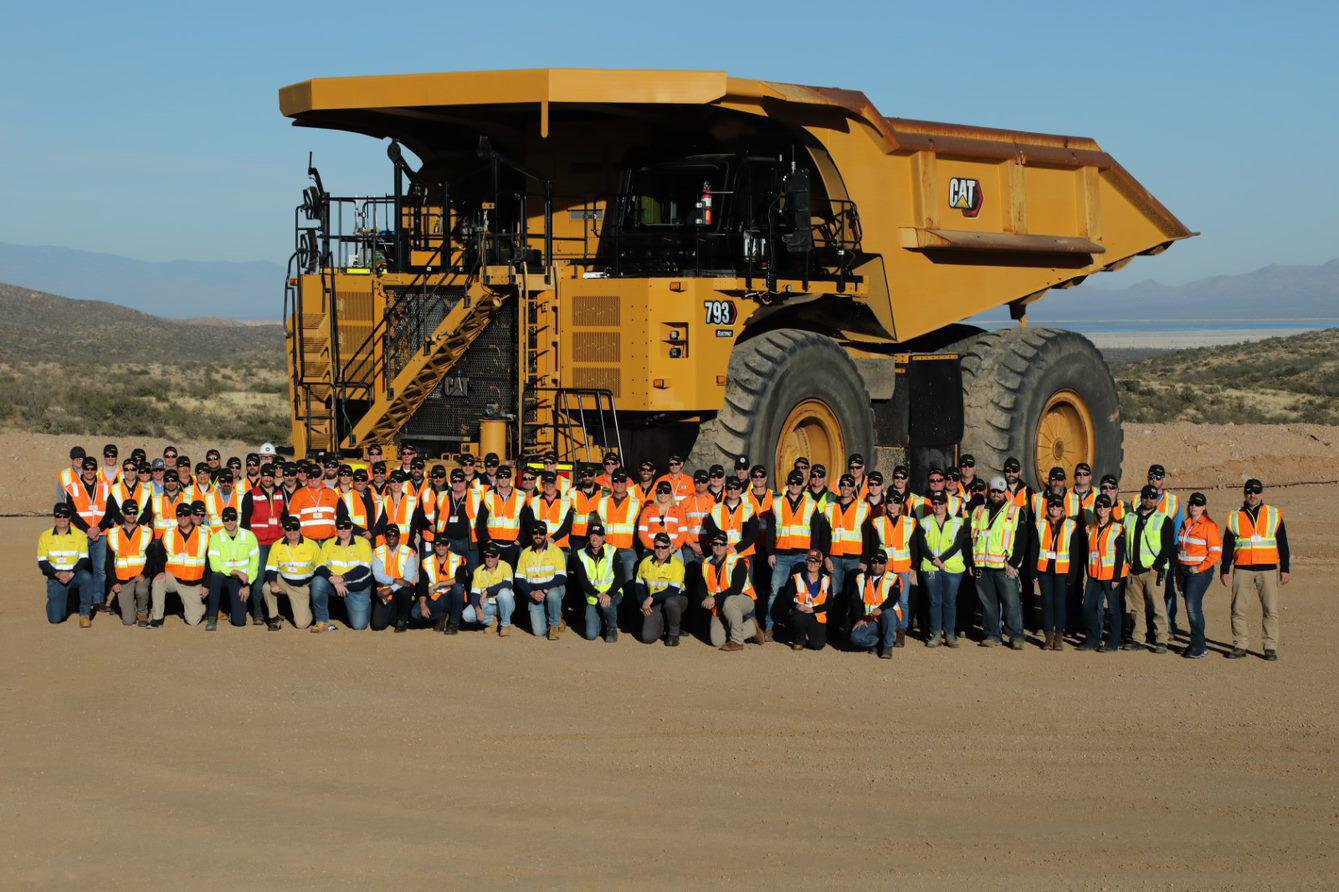
7 minute read
Powering the transition to electric mobility
As miners move towards fully decarbonised mine sites, Caterpillar’s Asia Pacific Hybrid Energy Solutions Manager, Adrian Constable, tells Energy and Mines how to best prepare for renewables-run electric fleets.
Energy and Mines: What are some of the main elements miners need to consider when working towards decarbonised power and mobility?
Advertisement
Adrian Constable: To decarbonise a mine, a good first step is to analyse the current carbon emissions from all processes and categorise these into Scope 1, 2 & 3 emissions. Pay careful attention to analyse each electrical load and mobility process in detail. Then, prioritise the areas where the biggest impact can be achieved.
Some of the main elements miners may need to consider when working towards decarbonised power and mobility are:
• Feasibility and affordability of using renewable energy sources and energy storage systems to reliably power operations and mobility on site, considering the space and solar/wind resource available.
• Current price of storage and potential for load shifting
• Technological innovation and adoption of electric vehicles and machinery that can lead to reduced fuel consumption, maintenance costs, and emissions
• Automation of vehicles and intelligent management of their charging to enable efficiency and electrical load stability
• Scalability of the solutions and optimal size for financial and environmental benefits with ease of expansion as factors allow
• “In-the-pit” charging electrical infrastructure and its potential mobility requirements
• Efficiency optimisation, such as optimising load processes to enhance productivity or spinning reserve that can be replaced with virtual spinning reserve from energy storage systems like the CAT Power Grid Stabiliser while also providing transient assist for grid stabilisation
• Exposure to fossil fuel price fluctuations and the motivation to reduce it
• Market demand and price fluctuations for critical minerals that are essential for the energy transition, such as copper, lithium, cobalt, and nickel
• Regulatory and policy frameworks that support or hinder the decarbonisation efforts of the mining sector, such as carbon pricing, subsidies, standards, and reporting requirements.
• Training – for example, updated and expanded electrical skills.
E&M: Mines are now incorporating an increasing percentage of renewables into their hybrid plants: how could this impact their electrification ambitions?
AC: On the positive side, incorporating more renewables into hybrid power plants could help mines reduce their dependence on fossil fuels, lower their operating costs and emissions, improve their energy security and reliability.
Incorporating a high percentage of renewables could also pose some challenges for mines, such as the intermittency of renewables, the integration and management of complex energy systems to balance both this intermittent renewable power and potentially newer mobile fleet variable charging loads, the higher upfront capital costs and payback periods, and the potential trade-offs between land use for mining and increased renewable energy production.
One example of a solution that can address some of these challenges is leveraging fast response and flexible Energy Storage Systems to provide power stabilisation to smooth both the intermittent renewable power and variable electrification charging loads. Caterpillar designed the BDP1000 inverter with an ultra-fast automatic response and patented transient assist non-linear droop algorithms with this type of application in mind. One then can combine this with intelligent load controllers and charging infrastructure. Caterpillar’s advanced hybrid energy controls and distributed power generation expertise combined with learnings from our zero-emissions battery electric mobile equipment, allows us to enable mines to integrate more renewables into their hybrid power plants and electrify their mobile mining equipment. Having a single vendor providing both mobility electrification and hybrid energy solutions with integrated control systems can be a positive advantage for mines.
E&M: How can mines prepare their power systems and operations for a move toward fleet electrification?
AC: Mines can prepare their power systems and operations for a move towards fleet electrification by:
• Conducting a comprehensive assessment of their current and future energy needs, demand profiles, load factors, and emission levels.
• Developing a clear electrification strategy and roadmap that aligns with their business objectives, environmental targets, stakeholder expectations, and regulatory requirements.
• Identifying and evaluating the most suitable renewable energy sources and storage options for their site-specific conditions, such as solar PV, wind turbines, batteries, hydrogen fuel cells, etc.
• Investing in upgrading or building new infrastructure and equipment that can support the electrification of their mining fleet, such as electric trolley lines, charging stations, electric vehicles and machinery, smart meters and controllers, etc.
• Engaging early with relevant stakeholders and partners to facilitate knowledge sharing, collaboration, innovation, financing, and policy support for their electrification initiatives.
Mine sites are complex, and each operation is unique. So, in our relationships with customers, we focus on a specific and collaborative approach to address customers’ unique challenges. In some cases, a customer’s goal requires a product that does not yet exist, so we focus on frontline customer input as Caterpillar designs and develops nextgeneration solutions to meet their needs. For example,
Caterpillar signed a series of transformative agreements with key mining customers in 2021. Through these collaborative agreements, we are developing and deploying customised, site-specific solutions to achieve our customers’ bold sustainability objectives to reduce or eliminate greenhouse gas emissions at their sites.
Caterpillar’s engineers are reimagining our machines at mine sites, enhancing them with alternative power sources and ensuring compatibility with renewable fuels. These solutions help customers run more fuel-efficient sites—reducing greenhouse gas emissions while supporting their total cost of ownership objectives.
What customers really want are sites that are safe, predictable and productive. That’s where Caterpillar stands apart from competitors, delivering key autonomy, alternative fuels, connectivity and digital, and electrification (AACE) technologies. Our MineStar technology suite enhances safety, productivity and profitability. It also allows for optimised energy management, as the site functions as a connected system.
E&M: What is the best way to integrate all infrastructure requirements to become all-electric?
AC: There is no single best way to integrate all infrastructure requirements to become all-electric, as different mines may have different needs, constraints, and opportunities. However, some possible ways to integrate all infrastructure requirements are:
• Adopting a modular, scalable, and flexible approach that allows for incremental expansion, adaptation, and optimisation of the infrastructure over time
• Recognising mobile “in-the-pit” distribution, power and load infrastructure may be required
• Having an intelligent re-deployable grid forming, high inertia battery energy storage system and mobile equipment charger package
• Leveraging digital technologies to monitor, control, and optimise the performance, efficiency and reliability of the infrastructure
• Collaborating with other mines or local communities to share or co-locate infrastructure assets, such as renewable energy plants, storage facilities, transmission lines, etc., to reduce capital expenditures and operational risks
• Engaging the mobile equipment and power OEMs early. Those that understand renewable energy, energy storage, electric energy distribution, local industry standard and ambient condition, electric mining machine capability and charging, operating, maintenance.
E&M: What are the inputs that can help mines determine electrical loads and sizing for renewable energy and storage systems to move to electrified sites?
AC: To determine electrical loads and sizing for renewable energy and storage systems to move to electrified sites, mines can consider the amount of energy required by the mine site (which may be a combination of today’s electrical load and fuel consumption for traditionally powered mobile fleets), as well as electrical and haul load profiles, productivity targets, details of mobile fleet, power quality targets, renewable energy resource and available space, the type and size of bi-directional power inverter to support high intermittency of both load and power sources, and combined renewable energy and load modelling with financial parameters.
Some examples of technologies that can help decarbonise power and mobility are electric mining trucks such as the battery electric Cat® 793 zero-exhaust emissions autonomous haul truck; Cat® R1700XE underground battery electric loaders, Cat® MEC500 mobile equipment chargers, automated energy controls and power management, moveable distributed power and energy storage systems, eg. Cat® PGS1260HD. Caterpillar’s MineStar technology suite for staffed and automated mines converges to create and maximise value and safety for our customers at the site level.