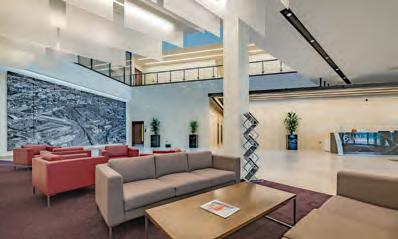
37 minute read
Products in Action
Flagship offices benefit from controls
The new Wellington Place development in Leeds is a flagship project for sustainable design both in terms of the way it was constructed and the comfort of occupants. Distech Controls has worked with local system integrator Linear Control Systems Ltd to create a sophisticated Building Energy Management System (BEMS) for two buildings at Wellington Place, that all place the comfort and wellbeing of occupants at the forefront of the design. Once the project is complete, Wellington Place will have 140,000m2 of commercial, retail, leisure and residential space. Developer MEPC says it will be one of the largest new city centre business quarters in Europe. So far, four buildings on the site have been completed and are now being managed by CBRE. Distech Controls has worked with Linear Control Systems Ltd on buildings six and seven.
Advertisement
Each building features a four-pipe fan coil air conditioning system that is controlled by the Distech Controls ECB-PTU Series. This is a range of microprocessor-based programmable controllers designed to control powered terminal units such as fan coil units, heat pump units, and chilled beams. Each controller uses the BACnet MS/TP LAN communication protocol and is BTL-Listed as BACnet Application Specific Controllers (BASC) and WSP Certified.
Clean air at Italian football stadium
Italian Serie A football club, Udinese Calcio, has installed the DEPURO PRO range of air purifiers and sanitisers by their main sponsor Vortice in its Stadio Friuli stadium in Udine, north east Italy. The air purifiers are used in the locker rooms, the entrance to the commercial area, as well as in the press room. This is part of the efforts to make playing at and visiting the club as safe and hygienic as possible. The DEPURO PRO EVO with photocatalysis module is claimed to kill up to 99.995 per cent of pathogens such as viruses and bacteria, thus ensuring people’s health and safety, constantly maintaining a good indoor air quality. Tested and certified by the University of Milan in co-operation with the Department of Biomedical and Clinical Sciences of the Luigi Sacco hospital in Milan, the DEPURO PRO EVO is being utilised in a number of health and sports facilities, places of worship, schools and commercial buildings as the world continues to tackle COVID-19.
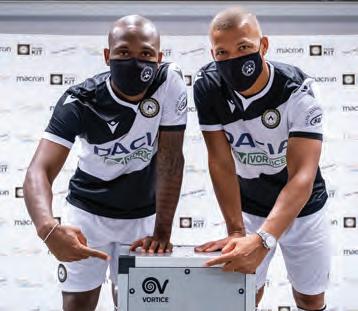
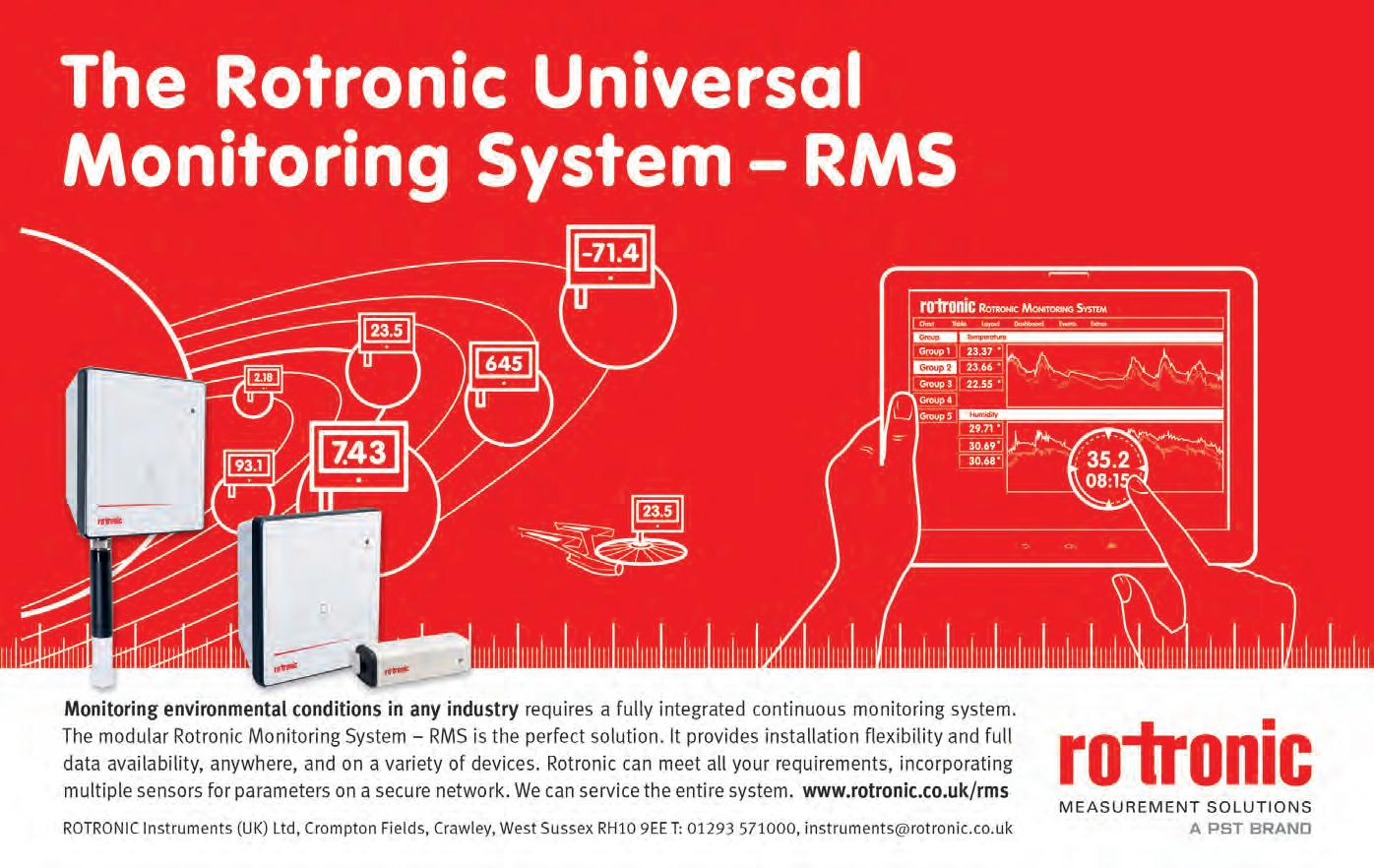
Energy in Universities
Adrian Barber is marketing manager at Prefect Controls
Student heating under control
Adrian Barber looks at how a university has overcome lockdown to forge ahead with updating the control of a heating system in its student village, resulting in annual savings of up to £75,000
The University of the West of England has updated the heating system at its Student Village accommodation with the help of a new control system.
The university has introduced its ‘Strategy 2030 - Transforming Futures’ programme that outlines their ambition to be carbon neutral with net-zero emissions of greenhouse gases by 2030 along with achieving ISO14001 to set clear targets to reduce water and energy use.
The Student Village built in 2006, on Frenchay Campus, is home to 2,000 students. The original heating system was becoming tired and inefficient to manage. Each room needed to be visited to programme the control with a handset, and the heater panels needed replacing. Kirsti Norris, energy manager, explained: “As panels failed, there was a risk of them getting replaced on an ad hoc basis with integrated control heaters, but we had always wanted a better way of controlling the heating and, having to enter students’ rooms, even before Covid, was not great. We had a hotch potch of settings in rooms all over the place and no way to re-set them all at once.”
Norris and Melissa Clarke, energy projects officer, attended the Association of University Engineers conference in 2019 and stepped onto the Prefect Controls stand. Clarke stated: “When we saw the Prefect offering we thought that this is what we need. It offered more control, shorter running times, reduced energy consumption.”
Access via internet portal
Irus is a centrally controlled system, accessed via an internet portal. It enables energy managers to set temperatures/times for the threestage student profile. Setback mode is the default setting (typically 18°C), but if the student requires more heat, they simply tap the ‘up’ button triggering boost mode (commonly 23°C). Boost runs for a pre-set time (45 minutes) before reverting to setback. If the student leaves the room during boost, the PIR detects their absence and reverts to Setback, likewise if windows are opened heat input is reduced by 50 per cent. If rooms are vacant for longer periods (typically 12 hours), Frost mode is activated, maintaining at least 5°C. Irus also monitors humidity, light and decibel levels. “The accommodation team are very keen on the decibel monitoring feature,” Clarke added. “When they receive antisocial noise complaints, they will be able to determine exactly when and where the noise occurred”.
Being a centrally controlled internet system, universal adjustments can be made from anywhere. Clarke explained: “We are really keen on a reset button for the end of the year so that when students return to site in September all rooms will be back to the standard profile and we won’t have various different settings throughout blocks. The main drivers for considering Irus were energy, carbon, and of course cost reduction.”
After a survey was commissioned, savings calculated, and quotations submitted. Norris had to convince colleagues that disruption during the installation would be minimal. “The biggest fear we had for this whole project was from the accommodation team,” she said “Considering we were planning the install around conference bookings they were really anxious about disruptions to residents. No matter how good the product is, it was the installation upset that could have blown the whole thing. To have the reassurances we received from Bangor and Bristol universities, who have worked with Prefect before, helped to get the accommodation team on board. That good reputation went beyond the product.”
Will Mills, project manager at Prefect, commented: “It all happened very quickly, and everything was slotting nicely into place. We were just about to embark on our biggest Irus project – then Covid struck!”
“The project stalled in February last year and, of course, budgets were frozen, added Clarke. “It was very frustrating because we saw all these buildings that were empty. Usually in the summer we have conferences and we felt this was a real missed opportunity to get on
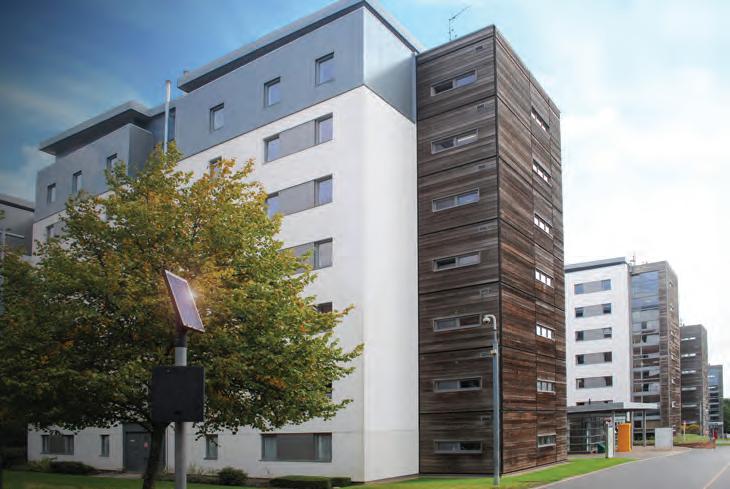
The University of the West of England is saving up to £75,000 a year on student accommodation heating thanks to greater room control
with the job – the quicker we make the projects happen, the quicker we make the financial savings. We are conservatively estimating saving 20-30 per cent - that’s over £75,000 per year!”
Mills added, “After lockdown and a return to the office, the university contacted us to say that they had the money, and want to try and do it this summer,” she said. “So, we rebooted the project and had six weeks to install as many rooms as possible. We managed 75 per cent, the rest will be completed during 2021.”
So, what was the Covid-effect? “Covid hasn’t really affected the installation process too much,” said Clarke. “We have been working in empty blocks, but had to make a lot of considerations for safe-working. Everything that is being done just requires an extra line of thought.”
One hidden benefit of the system that Norris has identified, was never even considered in her business case, “If we have students isolating and they have a problem with their heating we can deal with it without even entering the building, which is an added bonus in these Covid-times.”
Nigel Thomas is ABB’s national specification and projects sales manager
Energy in Universities
A new era for student accommodation
Nigel Thomas examines how a 17-storey student block in Swansea will be equipped with the latest monitoring to ensure energy efficiency is maintained
The latest addition to Swansea’s skyline is a £50m 17-storey purpose-built student accommodation block. Developer RDE Silex and partner Fusion Students are behind the project, which will house up to 780 students.
The main building will be Swansea’s second tallest at 60m. Its cladding design has been altered with aluminium panels backed with mineral wool insulation rather than PUR as first planned.
Scheduled to open in September 2021, the development will feature 780 bedrooms, shared social and leisure facilities, as well as retail ground floor space.
Property developer RDE Silex and operator Fusion Students wanted infrastructure to provide comfort for students and cost-effective energy efficiency performance for sustainable living. They also wanted a building that would last for a long time while working towards environmental standards that may grow more stringent in the future.
Unlike offices and commercial buildings, this is residential so the electrical system’s design needed to allow students to control individual heating and lighting in each room.
Since operational costs typically make up 80 percent of a building’s lifetime cost, Fusion Swansea deployed the technology to gain better control over its energy bills and carbon emissions.
This meant adopting a system that would meet BREEAM certification. To achieve this, the electrical system complies with Part L of the Building Regulations and meets the CIBSE TM39 guidance for energy metering in non-domestic buildings.
In addition, the system enables cloud-based remote monitoring capability and 24/7 alerts. This capability will support a shift to condition-based monitoring and avoid unplanned outages. Fusion’s building managers will also be able to use this to check alerts, such as when energy consumption exceeds a pre-defined level. Building managers can log in from any device to access data to view equipment status and review and compare historical operating data, allowing them to make decisions confidently.
The hardware comprises everything that Fusion needs to control, monitor, and manage electricity from the incoming utility supply to individual circuits. To provide this, we supplied smart switchgear, including the latest generation of air circuit breakers (ACBs) and moulded case circuit breakers (MCCBs) for the main low voltage switchgear panel, as well as automatic transfer switches (ATSs).
These all feature built-in communication modules to support energy metering, power quality, and analytics to monitor all the main circuits in the building.
In addition, we also supplied circuit monitoring systems, Internet of Things (IoT) gateways and energy meters to support the extensive monitoring that Fusion will need.
The devices are all linked to the cloud-based Ability Energy and Asset Manager platform for users to view and analyse data to optimise energy consumption in real-time.
The other benefit of the built-in digital metering and communication technology is that it saves time during engineering design, installation and commissioning. The built-in capability reduces the need to select, purchase, install and test multiple individual components.
Fusion wanted to minimise the space required for building services. Therefore, there was little space inside the riser cupboards that house the main panels that feed each floor.
A project like this would usually use energy meters, but they require a metering cubicle so to save space we provided energy sensors. These were compact enough to install inside the distribution panels and communicate directly with the digital platform so there is no need for a dedicated cubicle to house the meters or for a meter reading technician to access them. We also provided technical guidance on how to integrate the digital metering system.
The project shows how the latest technology can help developers create safe and sustainable student accommodation while keeping the lid on costs and complying with energy efficiency regulations.
However, with safety and energy efficiency requirements tightening, the real test is how well it will adapt in the future. For instance, we’re expecting to see the 18th Edition of the IET Wiring Regulations being changed with a new Part 8 covering energy efficiency.
Owners of large commercial and public properties are adopting low-energy building design. This is partly to reduce energy bills but also to meet UK targets for all new buildings to be net-zero by 2030 and for all buildings by 2050. Smart building technology will play a role in achieving this by using data to optimise energy consumption.
Scalability is another essential feature of future proofing. Over time, systems may need to meet tighter regulations, add new circuits or integrate extra sensors.
The digital twin concept is a big trend for Building Information Modelling (BIM). Digital twins are the online virtual versions of real-life buildings or other assets.
Ultimately, digital technology has a bright future ahead as it provides the data to measure, manage, and improve your buildings’ efficiency.
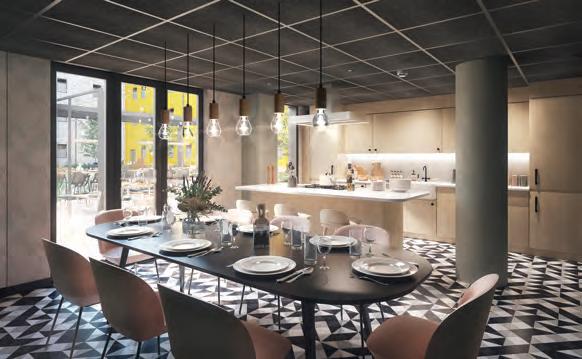
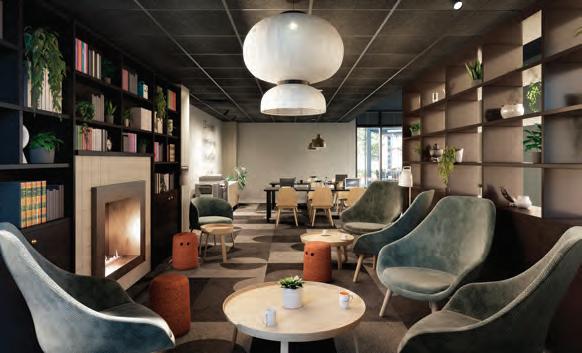
Energy in Universities
North London college benefits from heat recovery air conditioning
Students and staff at Barnet and Southgate College are benefitting from an outstanding indoor environment following installation of Toshiba’s heat recovery air conditioning system by Bry-Kol Building Services.
Barnet and Southgate College, a north London college with approximately 13,000 students across three campuses, recently completed a major upgrade of the main teaching block on its Southgate site. The project involved back-toconcrete refurbishment of facilities, including engineering, laboratory, administration and teaching spaces, and installation of new highperformance HVAC systems, headed by Bry-Kol Building Services as mechanical services contractor on the project.
The high-efficiency Toshiba air conditioning solution chosen comprises Super Heat Recovery Multi (SHRM-e) Variable Refrigerant Flow (VRF) systems linked to Toshiba VN-M heat recovery ventilation units, along with SmartTouch controllers. Indoor units include mostly four-way ceiling suspended cassettes, plus high wall units and concealed ducted systems.
The heat recovery ventilation system harvests energy that would otherwise be lost from the building when it is exhausted, and uses it to warm incoming fresh air to reduce the need for heating, saving energy and reducing the building’s carbon emissions.
The high performance Toshiba solution was selected by contractor Bry-Kol Building Services as it offered the outstanding energy efficiency, noise and comfort characteristics required for the project.
“We know Toshiba equipment well and it is excellent, and backed by superb technical support,” said BryKol project manager Jason Taylor, who led the installation. “They are very proactive and anything we need from them, we get when we need it. Toshiba produced all the schematics for the project, and inevitably there were some changes to the design along the way. However, Toshiba were able to quickly update the drawings and provide us with updates – often within a day.”
The installation on floors two to five of the building took place while the first floor remained occupied and operational, requiring careful planning and management on site.
Toshiba’s SHRM-e three-pipe heat recovery VRF air conditioning system sets an industry benchmark for energy efficiency performance and continuous heating, achieving a world-first European Seasonal Energy Efficiency Ratio (ESEER) of 8 in most capacities.
The system uses an advanced rotary compressor, developed and manufactured by Toshiba, based on a two-stage compression process for improved efficiency and performance. Wear surfaces on compression vanes are treated with a high-tech Diamond-Like Carbon (DLC) coating, giving outstanding hardness, wear resistance and reliability. This enables a significant increase in compressor rotation speed, resulting in a higher displacement volume – up to 50 per cent greater than for the previous generation of VRF.
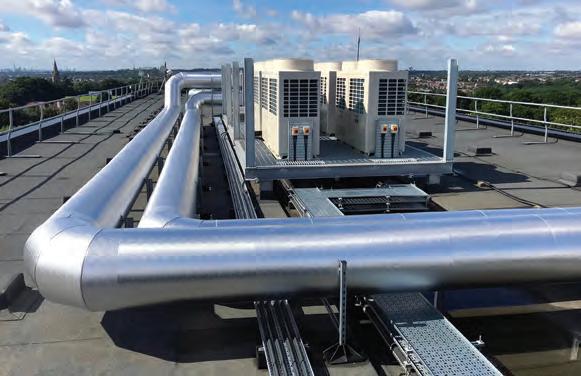
Modern UPS systems save university costs
Achieving optimum power efficiency is a phrase that’s often associated with data centre infrastructure as they look to implement the most efficient equipment and reduce the all-important PUE ratio. However, this is particularly applicable across educational establishments.
However, just as power consumption has increased, so has the amount of wastage, believes Power Control Ltd, specialist in uninterruptible supply. Any wasted electricity not only contributes to greenhouse gas emissions and places added stress on the grid, but it’s also a major financial cost.
Out of all educational establishments, universities tend to be the largest consumers of power and so have the most pertinent need for upgrading to new, more efficient technologies. Their need for power spans across a robust IT and networking infrastructure, research centres, emergency lighting, computers, and electronically controlled doors.
However, often hidden in server rooms and away from unauthorised persons, UPS systems are vital for protecting against disturbances and providing a consistent supply of power. While efficiency upgrades are being made to most other devices and equipment that requires power, UPS systems are typically at the bottom of the list.
Energy efficiency simply means using less energy to perform the same task. Today’s UPS systems can achieve efficiencies upwards of 98 per cent, a figure that is also important for minimising running costs and achieving optimum battery runtime in the event of a power failure. An efficient UPS consumes less energy throughout their service lives without sacrificing quality, meaning a significant reduction in spend on utility bills – a cost that is sky high for many universities.
Savings made on utility costs can also offset the initial price of investing in new UPS technology and therefore delivers a greater ROI in comparison to older, less efficient systems.
Given the range of critical applications a UPS must support, a balance needs to be met between availability, reliability and efficiency. Reducing a facilities carbon footprint is a consideration given by all facility managers, educational establishments included. Competitive pricing must compliment the savings made by installing an efficient UPS and above all flexibility and scalability is important so that UPS capacity can grow in line with the facilities developing requirements.
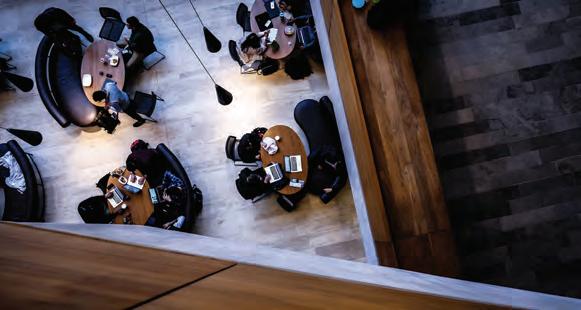
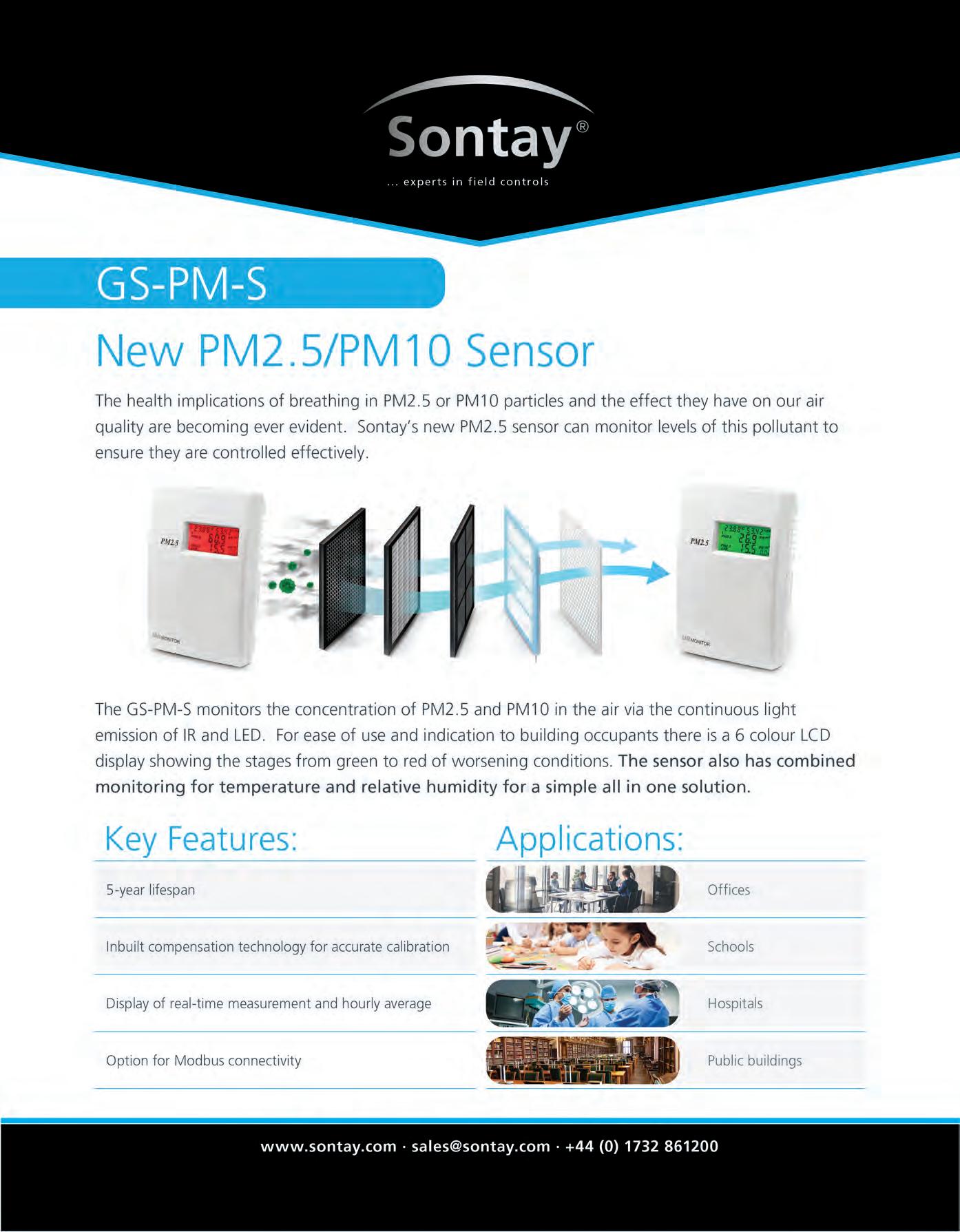
Energy in Universities
Advanced climate control solution for university battery dry room
Munters, a supplier of energyefficient climate control solutions, was approached by the University of Birmingham to build a bespoke turnkey battery dry room and HVAC plant for their vital battery research.
The Energy Materials Group at the University of Birmingham works with moisture sensitive materials such as lithium-ion, sodium-ion, and solid-state chemistries. All of these materials require very dry climate conditions to prevent damage, explosive reactions, and to ensure product integrity.
Munters agreed to be principle contractor for this project, and as the research team had worked in existing Munters low dew point facilities installed in other industry and academic settings in the past, expectations of a comparable facility here were extremely high.
One of the key challenges encountered during this project was working within a grade II listed building. “The added complexity of working within a listed building presented a number of challenges throughout the project, including working around pillars, matching existing building louvres that were over 20 years old, and complying with increased planning and building regulations” says Paul Richards, Munters project manager.
The 50m2 dry room consistently maintains conditions to around -40°C dew point at a temperature of 20°C, with capacity for approximately six people. These conditions are created and maintained by the Munters desiccant dehumidification solution installed in the adjacent plant room.
“Having the dry room has certainly opened up new opportunities for us,” says Scott Gorman, research fellow and the dry room manager. “Around half of the projects that are carried out each year will use the dry room regularly. It gives us a unique selling point, and allows us to bridge that gap between industry and academia.”
Munters and the university worked together to optimise the dry room design and ensure reliable climate control performance. The Munters system is high performing yet energyefficient, which results in a cost effective solution for the university. Low-leakage wall panels and ductwork and a positive pressure in the room are all also critical. Munters optimised the room and ductwork designs using CFD modelling to ensure it would meet target dew point in all areas of the room.
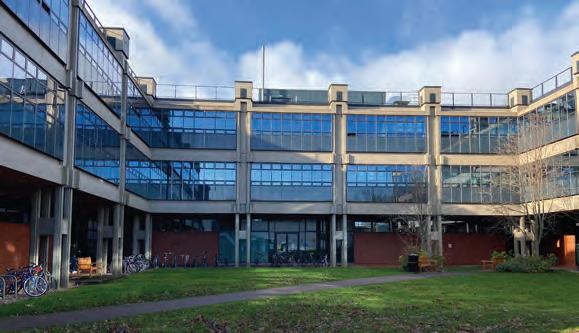
University forges ahead with net-zero targets
Energy solutions provider, SSE Enterprise, has signed a joint development agreement with Goldsmiths, University of London, to design and deliver a low-carbon campus infrastructure in pursuit of the university’s ambitious net zero targets.
The project will see SSE Enterprise’s distributed energy division look to consolidate all of Goldsmiths’ significant energy consuming buildings onto a centralised campuswide heat and power network. It is estimated that the first phase of the project will save the institution an average of 1,375 tonnes of CO2 per year – the equivalent annual energy use of 144 homes.
The project has a core focus to reduce the carbon emissions associated with heat, as the university pledges to become completely carbon neutral by 2025. The system will heat the buildings using a low-carbon heat pump, removing the majority of gas consumption on site and saving up to 7,850MWh of gas per year.
By integrating all power onto a single private network, the university will be able to use a much higher proportion of any onsite renewables, without the risk of exporting that electricity onto the grid. The new power system will expand on the university’s existing solar resources, installing a further 400kW of solar PV into the new private network, which will then be used to supply the heat pump, further reducing carbon emissions on site.
Giles Newton, head of public sector and regulated markets at SSE Enterprise, said: “By bringing the whole campus onto a centralised system, we are able to integrate more renewable generation into its buildings without having to upgrade each one individually. While previous projects of this kind have focused on single technology solutions, we have chosen to adopt a whole systems approach. Integrating the entire system enables Goldsmiths to closely manage its carbon emissions and future proof the campus for renewable efficiency.”
Everton Williams, deputy director estates at Goldsmiths, added: “We are excited to begin this journey with SSE Enterprise as they support us in our goals to deliver our PLAN25 strategy and achieve a completely carbon neutral campus by 2025. We have already made significant strides in this area with our investment in solar PV panels, but this new partnership will see us fully embracing a ‘whole systems’ approach by adopting and integrating other low-carbon technologies.”
SSE Enterprise have already designed a concept for the system and are currently supporting Goldsmiths with applications for grant funding to enable the construction of the network and potentially the long-term operation of the system over a 25-year period. The 1MWth heat pump set to be installed will supply 6,500MWh of low carbon heat to the site every year.
SSE has been confirmed as a major partner for this year’s COP26 climate change conference in Glasgow in November. SSE Group aims to deliver a £7.5bn low carbon investment programme, developing some of the assets and infrastructure required for the UK to reach its target of net zero emissions by 2050.
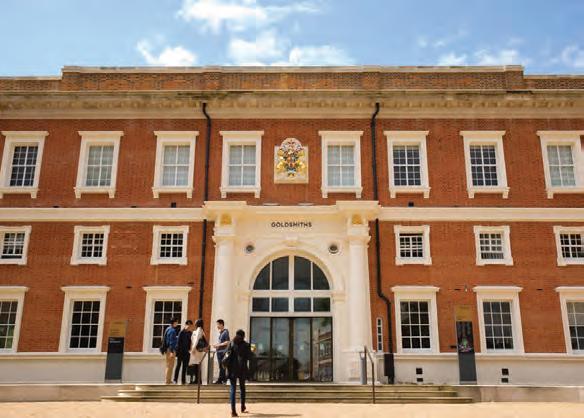
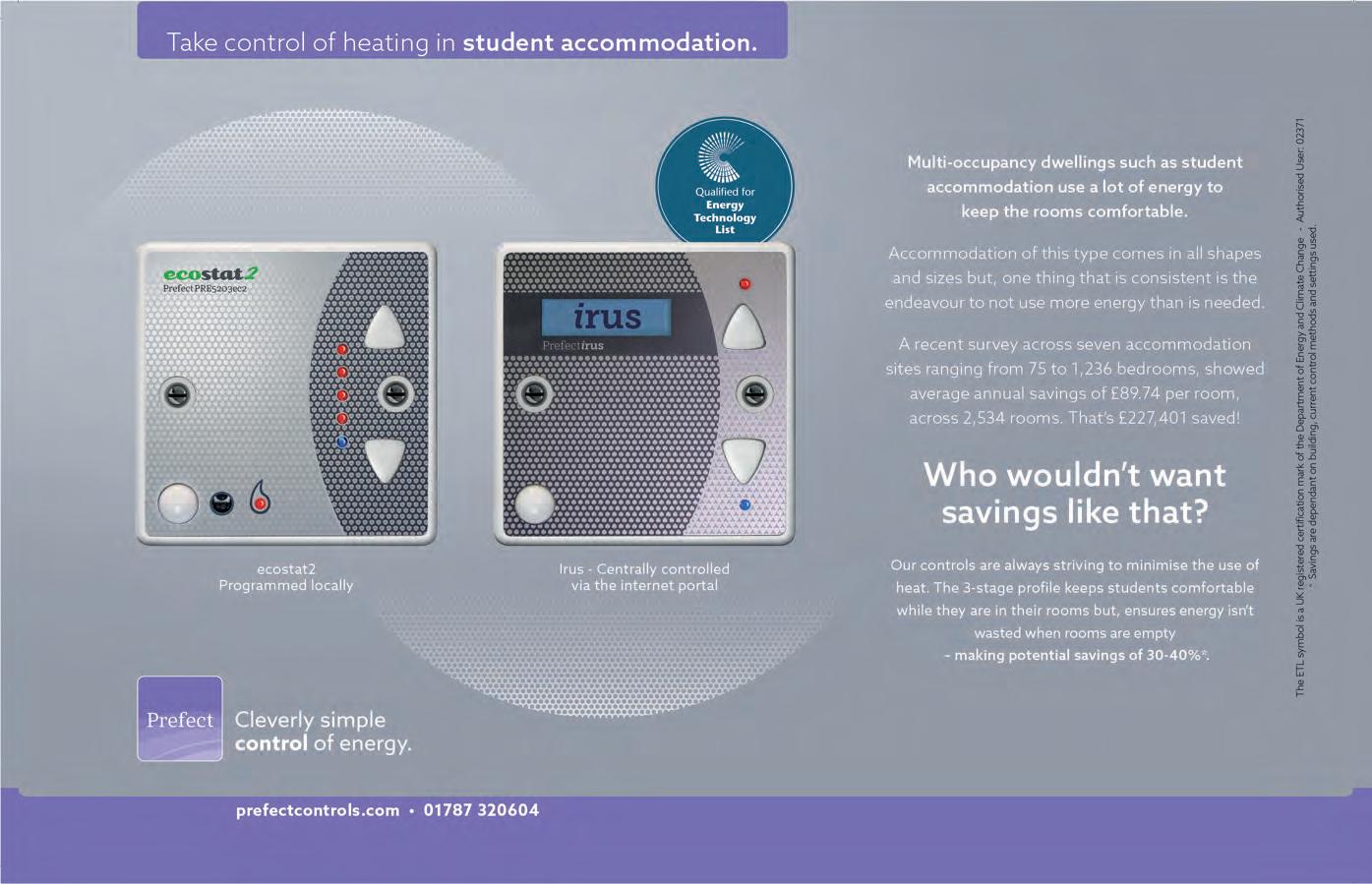
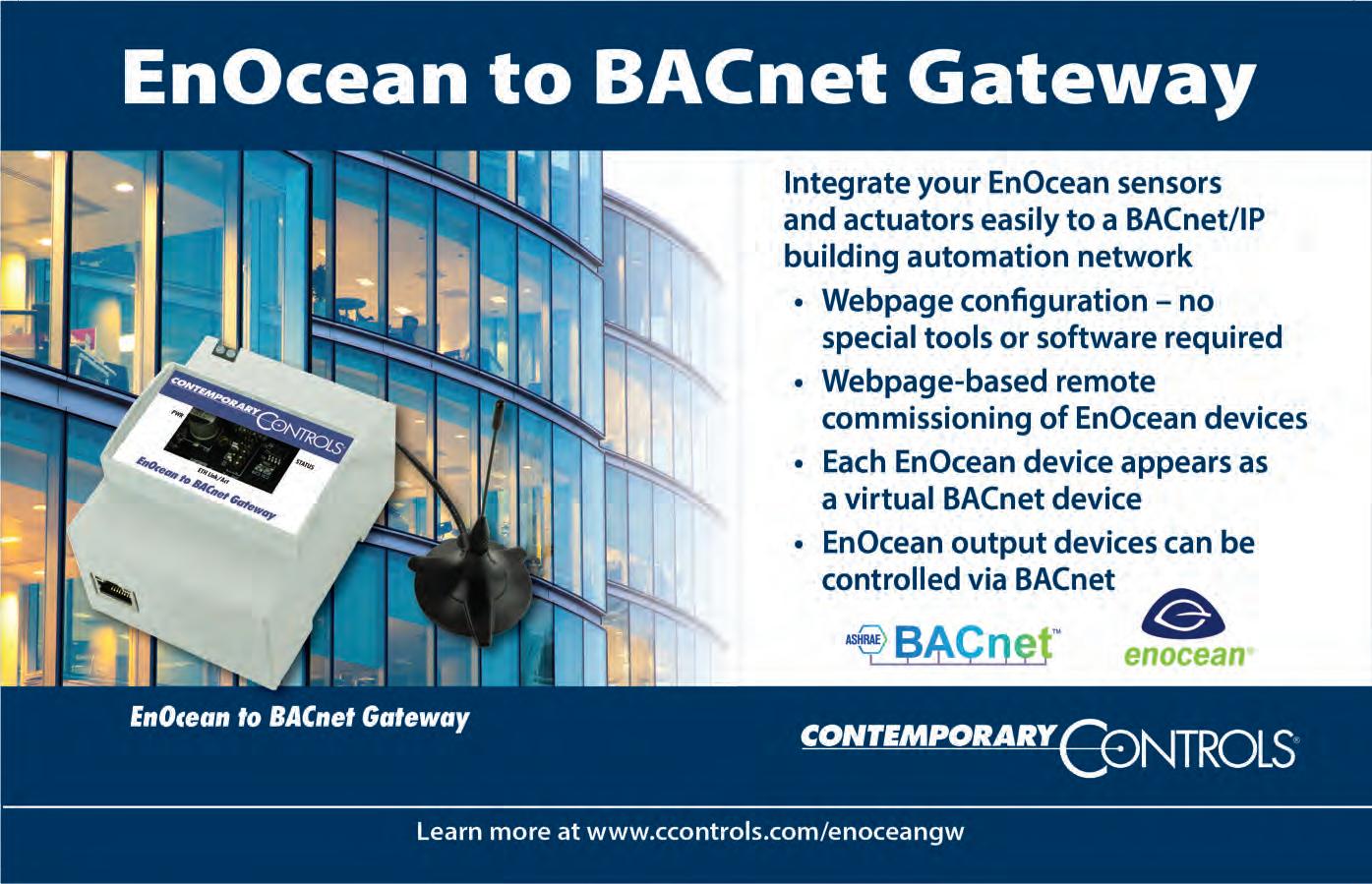
Corporate Power Purchase Agreements
Adam Clarke is senior manager of PPA and Sustainability Solutions, EDF
Corporate PPAs – a net zero opportunity
Placing Net Zero at the heart of business decisions is a necessity. It’s what investors are looking for. It’s what customers are demanding. And ultimately, it’ll pay dividends for your bottom line, says Adam Clarke
Energy powers every business activity. So for any business, it’s the ideal place to start on the journey to Net Zero.
Organisations across the world are already committing to Net Zero, knowing it is better for people, for the planet and for profit. The time to go Net Zero is now.
By taking control of your energy you can unlock bottom-line value for your business. Using energy more efficiently enables you to save both money and carbon. Investing in decentralised opportunities, like on-site generation or Corporate
Power Purchase Agreements (CPPAs) can unlock new revenue streams and increase resilience.
And showing your brand is committed to sustainability will enhance your reputation as consumers and investors become more environmentally aware.
Crucially, understanding your energy needs can help you significantly reduce your environmental impact. Harnessing quick wins and having a smart approach to buying, using and managing your energy, will accelerate your organisation’s journey to Net Zero.
The opportunity is huge, but it can seem overwhelming to work out where to begin. We’ve learnt from deep experience with businesses across sectors that becoming sustainable cannot happen overnight. Going Net Zero is best done one change at a time, and your electricity supply is a great place to start.
Choosing a zero carbon supply option will have a positive impact on your business’ sustainability credentials, allowing you to report zero carbon emissions for your electricity use.
Depending on your business’ objectives, ambitions and capabilities there are a number of zero carbon options available.
If you’re looking for an option that’s quick and simple to agree, enabling you to purchase the volume you require over the short term, zero carbon supply backed by nuclear or renewable electricity could work for you. Both of these options allow you to report zero carbon emissions.
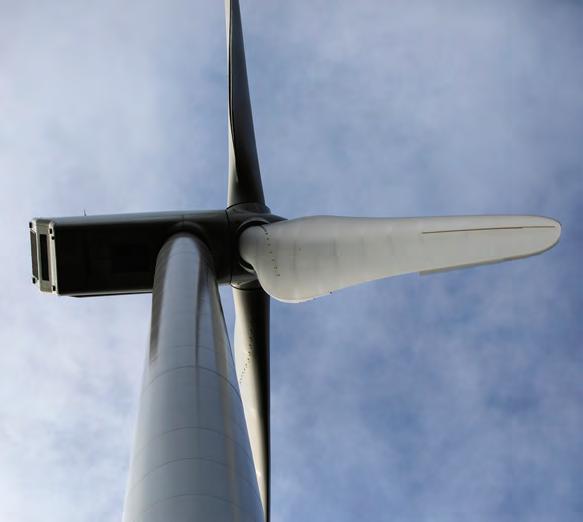
Rewarding complexity
If your business is in a position to make a longer-term commitment, CPPAs provide an excellent option for showcasing credibility and authenticity in your commitment to zero carbon.
A CPPA is a direct contractual agreement between your business and a renewable energy generator. Your power would still come via the grid (there’s no physical connection), but you are contracting with a named generator, enabling you to say that your energy is coming from a specific source.
CPPAs are more complex and long term than some businesses want for their energy supply. But, if you have long-term demand certainty, are comfortable managing a little price risk and sustainability is a top priority for your business, this could be the ideal solution for you.
These contracts can be complex and lengthy to agree and are usually between 10 and 15 years in duration. This longterm commitment and direct investment into the financing of renewable projects provides unique risks and opportunities.
Suppliers, like EDF, can help to minimise complexity in the
negotiation and contracting process and manage the contract throughout its duration. Their extensive energy trading experience means they will be able to support in managing your consumption profile against any intermittency or change in demand. You may choose to sign a CPPA for all, or a proportion, of your business’ consumption. Whichever option works best for your business, your supplier can either make up any shortfall with electricity from other zero carbon sources or sell excess output on your behalf as required, allowing for flexibility in consumption. And, this longer-term approach can be a real advantage for mitigating price risk within your business, allowing long-term certainty on the price you will pay for your electricity, regardless of market movement.
Above all, CPPAs ensure high authenticity of carbon credentials. They give your business real credibility in your reporting, ensuring you meet the carbon requirements for your portfolio. A CPPA would allow your business to point to exactly where your power is coming from, so you can prove the source of your electricity to your stakeholders. And if you contract with a new asset that isn’t built yet, you’ll be striking sustainability gold - additionality. You’ll be able to show that your business has been instrumental in bringing more renewable energy to the grid, having a real impact on emissions.
Every business is different. And it’s essential that you have a supply contract structure that suits you, so a CPPA doesn’t work for everyone. But, although CPPAs are often more complex to arrange and require a longer-term approach to purchasing electricity, by signing a CPPA your business is making a commitment to achieving Net Zero.
We can help your business understand whether a CPPA would work for you or explore alternative zero carbon supply opportunities.
There’s never been a more urgent time to take action and accelerate your journey to Net Zero. • Get in touch with us at letstalkpower@edfenergy.com
Richard Poate is senior manager at TÜV SÜD
Batteries & Energy Storage
The danger within the power
Lithium-ion batteries are such an important part of our home and workspaces. But proper storage and risk management are essential, believes Richard Poate
Lithium-ion batteries power our world. They are found in virtually all types of electrical and electronic devices, including consumer products, wearable medical devices, vehicles and advanced industrial equipment. They offer several advantages over conventional batteries, including greater energy density and cell voltage, and little charging capacity loss over time for rechargeable batteries. Without them, our ability to stay in touch and get things done would be very limited indeed.
However, the widespread use of lithium-ion batteries has also brought to the forefront concerns about their safety. While normally safe under most use conditions, lithium-ion batteries that are poorly designed or which consist of low-quality materials or have been assembled incorrectly or have been damaged can overheat and even explode, potentially resulting in catastrophic consequences involving life and property.
While lithium-ion battery technology development has advanced over the last few decades, it has also presented new fire and explosion risks. For commercial and industrial environments, the proper storage and risk management of lithium-ion batteries is therefore critical.
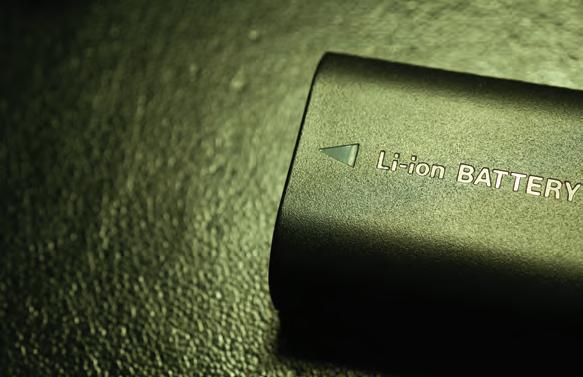
Lithium-ion configurations
There are three major configurations for lithium-ion batteries: • the small format - batteries we are used to seeing in electronic devices and hand tools; • larger batteries - used in mobile equipment such as lift trucks and vehicles; and • very large-scale energy storage systems - typically used for uninterruptible power supplies or for electric power grid storage, often in conjunction with renewable power generation equipment.
As well as many benefits, there are potential safety risks related to thermal stability and internal short circuits, which can cause overheating and even explosion. Safety problems arise due to poor design, the use of low-quality materials, incorrect assembly, or damage. Even for lithium-ion batteries with integrated safety features, an unanticipated breach in the battery separator material can result in a high current that overheats the battery’s electrolyte.
While battery manufacturers and developers are continually improving lithium-ion battery design and performance, this can make them more vulnerable to small manufacturing defects or internal damage from the physical impact with another object. Variations in battery design, and the quality of materials and manufacture can also cause potential safety risks.
Of course, this problem will be magnified if large quantities of batteries are stored on-site or transported between industrial facilities. Fortunately, there are important steps that operators of industrial facilities can take to reduce the risks. This includes ensuring that the facility is equipped with suitable sprinklers.
Idle batteries in storage are not typically subject to internal ignition. However, large-scale testing has shown that lithiumion batteries behave similarly to unexpanded plastic commodities in a fire. Therefore, sprinkler protection should be provided.
Risk of generating heat
Fully charged lithium-ion batteries have a higher energy density and are therefore at greater risk of generating significant heat from short circuiting caused by internal defects. It is therefore important to ensure that lithium-ion batteries stored in the longer-term are charged at levels below 50 per cent charge capacity and kept at temperatures between 4-27°C. This will help to minimise the risk of thermal runaway from manufacturing defects or internal failures.
While usually safe, as lithiumion battery charging can cause safety problems, stations designated for charging large format batteries should be separated from other combustible materials by at least one metre. For larger format batteries, such as those used in mobile equipment, battery chargers and batteries being charged should be separated from other combustible contents by at least one metre. Stations used for charging small format batteries should be set on a firm, non-combustible surface and be separated from other combustible materials by at least 30cm.
Bins holding damaged or discarded batteries should be separated by at least three metres from all other storage areas, as well as bins holding other potentially combustible materials. This separation will help to reduce the risk of spreading a fire that might originate amongst discarded or waste batteries. In addition, these bins should be metal and have metal lids whenever practical.
Internal components and mechanisms in lithium-ion batteries are highly susceptible to physical or mechanical damage when the battery is subject to a severe external force or when it is dropped on a hard surface. Any external evidence of damage should therefore trigger concerns about a battery’s internal integrity, and it should be safely disposed of in bins intended solely for damaged batteries.
For larger format batteries, such as mobile equipment batteries, ensure that battery chargers and batteries being charged are separated from other combustible contents by at least 3m.
As lithium-ion batteries bring so many positive benefits to product innovation, they will continue to evolve as manufacturers seek new ways to increase battery density and reduce size. Therefore, the safety of lithium-ion battery technology will continue to be investigated to address unexpected hazards that emerge. As we learn more about the risks associated with the use, bulk storage and recycling of lithium-ion batteries, changes in standards and best practices can be expected to change as well. It is therefore vital that the safety of lithium-ion battery technology and its storage remains under scrutiny so that these evolving hazards can be addressed.
Batteries & Energy Storage
Alexander Baal is director sales operations, Jungheinrich UK
Moving towards electricity
Alexander Baal explains how deploying Lithium-ion-powered material handling equipment is one method that can support businesses’ CSR initiatives
Environmental credentials are a fundamental component of corporate CSR initiatives. In 2019, the UK became the first major economy to legislate an end to its contribution to global warming by 2050, requiring the UK to bring all greenhouse gas emissions to net zero by this date.
After rising steadily for decades, global carbon dioxide emissions fell by 6.4 per cent, or 2.3bn tonnes, in 2020, as the COVID-19 pandemic drastically restricted economic and social activities worldwide. A great reduction, but as the world reopens, will we see these numbers rise once more? Businesses bear the responsibility both to deliver the infrastructure and change that helps shape a modern, post-pandemic economy, while doing it in a way that effectively measures, evaluates and reduces carbon impact.
The market trend for businesses to move away from transportation and industrial equipment powered by fossil fuels has been gaining momentum for many years and this includes warehouse equipment such as forklift trucks.
When considering the area of materials handling equipment, great strides in innovation have been made in recent years to deliver an alternative to gas and diesel power that not only support the move to more sustainable energy sources, but also provide invaluable efficiency gains. The numbers speak for themselves that electric forklifts offer a significant positive effect when compared against their diesel or gas counterparts. For example, if a comparison is taken for a standard 2,000kg electric counterbalanced truck working 2,000 hours per year with its diesel and gas counterparts, we see that the electric truck would produce circa 4,600 kg of CO2 in that year compared to circa 13,980 kg for the diesel and circa 17,640kg of CO2 for the LPG. This means electric trucks provide a CO2 saving of 67 per cent per year against the LPG equivalent
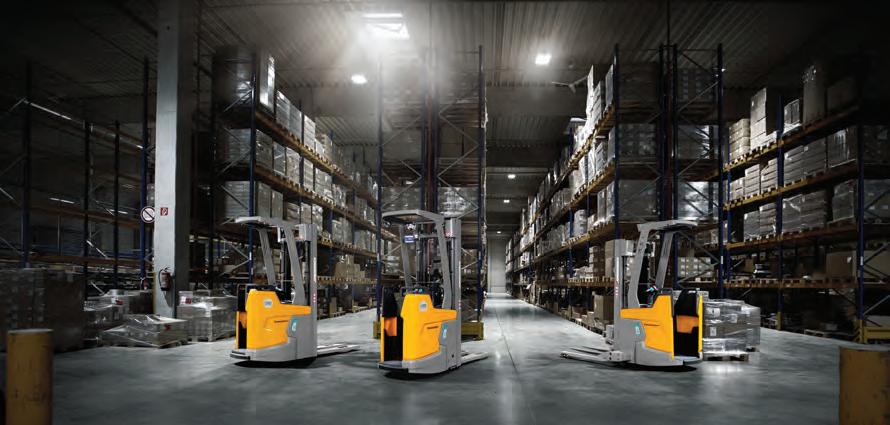
There may be a higher outlay for electric forklifts but running and maintenance costs are much lower
and 74 per cent saving over the diesel truck counterpart.
It is true that an electric forklift embraces a higher initial outlay than its diesel or gas counterparts. However, it also benefits from lower maintenance costs as there are fewer moving parts and hence fewer service items involved. While short-term savings can be made by the acquisition of the I/C engine trucks, the longer-term total cost of ownership of Lithium-ion-powered trucks can offer distinct value. There will always be differences in the amount consumers pay for diesel, LPG and electricity. However, the pricing for electricity typically remains far more stable than the long-term pricing for any by-product of crude oil, which is an important factor when considering decisions for the business. Depending on how many forklifts are being serviced at any one time, the outlay for electricity comes up trumps in the fight against fossil fuels.
Support for business logistics
The benefits for materials handling fleet operators to consider Lithiumion are considerable for both efficiency and reliability. Lithium-ion supports 24x7 logistics operations without the need for regular battery changes due to its short charging times, high power and energy density, meaning there is no dropoff in power over the life cycle of the battery. Moreover, operators don’t need to factor machinery downtime into their operation, resulting in higher productivity throughput. Business savings are made as no maintenance is required and no period of battery resting is needed after each charge. During the recharge process, less energy is wasted as heat thus cost saving to further the business contributing to renewable energy, resulting in lower energy costs.
In order to become more sustainable, businesses will inevitably need to adapt to using cleaner sources of energy. Many will therefore need to overhaul their diesel equipment and consider more energy efficient power alternatives, such as Lithium-ion. EV Batteries will require less lithium by over half over the next decade. In addition, the amount of cobalt required will drop by more than three-quarters and nickel by around a fifth according to analysis by Belgium-based research body, Transport and Environment. Compared to diesel or gas equivalents, electric machinery will consume far fewer raw materials, making it the clear choice for a sustainable future. Therefore, by deploying a Lithium-ion powered alternative to warehouse equipment, businesses can increase efficiency and sustainability in the longterm, providing a key competitive advantage and advancing CSR goals.
The fall of carbon dioxide emissions as a result of the pandemic has provided a global opportunity for change and identified initiatives that can contribute to the continued reduction of CO2. Businesses have a crucial role to play to promote clean energy and deploy or scaleup new sustainable technologies to make equipment more energy efficient. Striving to deploy Lithium-ion powered handling equipment in future operations is one of the many proactive measures companies can take to ensure that their carbon footprint is reduced and sustainability is increased – especially with the significant rise of e-commerce which is set to continue, and from which many businesses have already benefited.
Crucially, businesses must capitalise on this opportunity for change for the better. Not just to support global sustainability efforts to save the planet, but realise the additional benefits that come alongside – including cost savings, productivity gains and no downtime.
Batteries & Energy Storage
Dr Shanmugam Kumar is reader in composites and additive manufacturing, University of Glasgow
The age of the recyclable battery
Researchers at the University of Glasgow have designed a recyclable ‘veggie’ battery that could power future devices more efficiently
Ateam of engineers led by the University of Glasgow has developed a new type of 3D-printed battery that uses electrodes made from vegetable starch and carbon nanotubes could provide devices with a more environmentallyfriendly, higher-capacity source of power. It is hoped that more sustainable lithium-ion batteries capable of storing and delivering power more efficiently can be produced.
Lithium-ion batteries provide a useful combination of lightweight, compact form factors and the ability to withstand many cycles of charging and discharging. That has made them ideally suited for use in a wide array of devices, including laptops, and electric vehicles.
Like many batteries, lithiumion batteries comprise a positive electrode, often made from lithium cobalt/manganese oxide or lithium iron phosphate, and a negative electrode, often made from lithium metal. During charging, lithium ions flow through an electrolyte from the positive electrode to the negative electrode where they are stored. During use, the ions flow in the opposite direction, generating energy to power devices through an electrochemical reaction.
One of the physical limitations on the amount of energy current designs of lithium-ion batteries can store and release is the thickness of their electrodes. Thicker electrodes restrict diffusion of lithium ions across the electrode, thereby limiting the specific energy of lithium-ion batteries. Increasing electrodes’ thickness also decreases their strain-tolerance, making them more prone to cracking. Once an electrode breaks, the battery is rendered useless.
Increased surface area
The Glasgow-led team’s battery aims to strike a better balance between the size and the surface area of electrodes by introducing tiny nanoscale and microscale holes, or pores, into their design. By riddling the surface and interior of the electrodes with pores, they can greatly increase the surface area compared to a solid electrode of the same external dimensions.
To do so, the scientists used an additive manufacturing technique, also known as 3D printing, to tightly control the size and placement of each and every pore in their electrodes. They loaded a 3D printer with a material they developed which combines polylactic acid, lithium-iron phosphate and carbon nanotubes. The polylactic acid is a biodegradable material processed from the starch of corn, sugar cane, and sugar beet, increasing the battery’s recyclability.
They experimented with making circular electrodes at three different thicknesses of 100, 200 and 300 microns. Each electrode was tested with different combinations of materials, varying the amount of carbon nanotubes in the material mixture from 3 to 10 percent by weight, and the porosity from 10 to 70 percent by introducing tightlycontrolled grids of holes throughout the electrode.
The team’s 300-micron electrode battery with 70 per cent porosity performed the best during testing, with a specific capacity of 151 milliampere-hour per gram, or mAh/g – the standard measurement of how much charge a battery can hold. That is around two to three times the performance of
The 3D printing process gives control over the electrodes’ porosity Microscale pores were introduced into the design of the surface area a traditional lithium-ion battery with a solid electrode of the same thickness.
The increased porosity, and thus the larger surface area, of the thickest 300-micron electrode also influenced the battery’s areal capacity. The thicker electrode was capable of storing 4.4 milliamperehour per square centimetre (or mAh cm−2) compared to 1.7 mAh cm−2 achieved in the 100-micron electrode, a gain of 158 percent.
The research was led by Dr Shanmugam Kumar from the University of Glasgow’s James Watt School of Engineering, alongside colleagues from Khalifa University of Science and Technology in Abu Dhabi, and Texas A&M University and Arizona State University in the USA.
Lithium-ion batteries are increasingly common in everyday life and are likely to continue to increase in ubiquity as we move towards more electrification of transport and a more sustainable world. However, lithium-ion batteries have their own sustainability issues, so it’s important that we look to find new ways to make them better and more environmentally-friendly.
The 3D printing process used in this research gives a huge amount of control over the electrodes’ porosity, allowing the team to engineer very precisely a new metamaterial capable of addressing some of the shortcomings of the current generation of lithium-ion batteries. They believe they have created a battery with a high specific capacity and areal capacity with excellent cyclability.
The team says that these are promising initial results, and they are now keen to continue to explore the possibilities that this kind of microarchitected materials offer to create better, more recyclable batteries for future consumers.”
The team’s full paper, titled ‘Additive manufacturing enabled, microarchitected, hierarchically porous polylactic- acid/Lithium iron phosphate/carbon nanotube nanocomposite electrodes for high performance Li-Ion batteries’, is published in the Journal of Power Sources. The research was supported by funding from the Abu Dhabi National Oil Company.
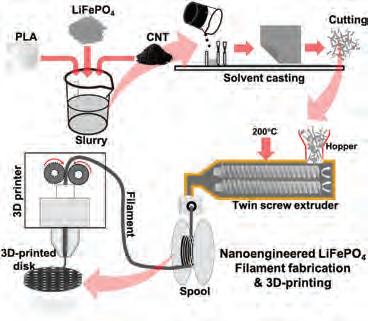
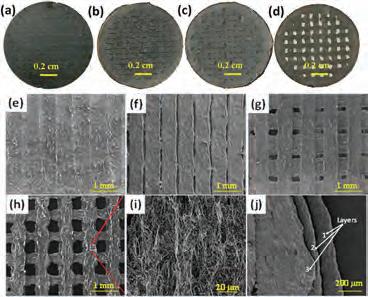