
27 minute read
The Warren Report
Andrew Warren is chairman of the British Energy Efficiency Federation
11/12.20
Advertisement
Snapshot reveals the state of UK housing
The recently completed analysis of EPC data reveals little or no progress in improving energy efficiency in housing stock in recent years A pproaching half the energy the UK consumes each year is used in buildings. Twothirds of that consumption happens in our homes. But Unsurprisingly, new homes tend to be far more efficient than older homes, producing less than half the carbon dioxide emissions and half the energy costs. Those built over the last 40 years the latest official statistics underscore the have, theoretically, all been built to scale of draughty, inefficient homes and minimum building regulation standards buildings which urgently need attention for the conservation of fuel and power. to drive down greenhouse gas emissions. Gradually these standards have been
Back in 2008 the law changed so that, tightened, each time to make any new whenever the occupancy of any building homes that little bit more energy efficient. alters, an Energy Performance Certificate The most recent change took place (EPC) must be provided. The formal eight years ago. Hence the sad revelation conveyancing process now ensures that, that the ONS median energy efficiency whenever a building is newly constructed rating bands for both types of homes - new or sold, this certificate is made available. and second-hand - have not improved at The purpose is to show prospective all in recent years. No strengthening is due occupiers the relative theoretical energy before 2025. efficiency of the property.
An EPC grades homes from ‘A’ as the Median score di erence best and cheapest to run, right down to ‘G’ The ONS survey reveals some surprising as the worst and most expensive - or least facts. Amazingly, no less than 14 local energy efficient. Within these categories, authorities seem to have managed the too, are more precise numerical markings, unlikely feat of having lower median going all the way up to 100. An EPC energy efficiency scores for new flats, doesn’t necessarily provide the most up to than they do for the existing ones in their date information, because they still only locality. have to be reassessed every ten years. Harlow in Essex had the biggest energy
When the government’s Clean Growth efficiency median score difference Strategy was launched almost exactly between new flats (a derisory 61, EPC band three years ago, the then-Energy and ‘D’), and existing flats (71, band ‘C’). Clean Growth Minister, Claire O’Neill -née During 2019 there were also big Perry - announced on BBC Radio 4’s Today differences between the standards programme that “all housing stock should required for new flats. Cambridge had the be up to at least Band C by 2035.” Last highest median energy efficiency score year, the average EPC rating issued for an for new flats, with 89 (EPC band ‘B’). But existing house was - only just - band D. North Lincolnshire the lowest, with an
Now that half of all homes in England astonishingly low average of 59.5 (band ‘D’). and Wales have acquired an EPC, the It is genuinely difficult to see how a Office for National Statistics (ONS) has new flat which can score so poorly on an published its first ever detailed analysis of EPC rating is actually complying with the EPC data. This provides what is probably relevant Parts of the Building Regulations the largest in-depth snapshot of the (L and F). And of course, if this is the energy efficient state of our housing stock. average score, then inevitably there will
have been some new flats sold in North Lincolnshire or Harlow which scored even lower.
There is no restriction upon sales of even the worst gas-guzzling homes. Earlier this year, the main professional organisation for estate agents and surveyors formally demanded that the Government ensure that practically every home sold – new or old- should achieve a minimum Energy Performance Certificate (EPC) rating of C. Traditionally the least outspoken of construction professionals, the Royal Institution of Chartered Surveyors (RICS) is now demanding radical initiatives to modernise the UK existing housing stock.
The Scottish Government is responding by proposing that from 2024 all owneroccupied properties will have to reach a C rating when they hit certain “trigger points”, such as sale or renovation. The former building regulations minister Lord (Don) Foster has introduced a Domestic Premises (Energy Performance) Bill to press for similar requirements in England.
On average, in both England and Wales, socially rented flats and houses with an EPC are rated more energy efficient than privately rented flats and houses respectively. But since April 2018 it has been illegal to let out any home with an ‘F’ or ‘G’ rating, and government is now consulting on tightening that requirement. Even so, just 6 per cent of councils have taken any enforcement action against landlords letting out substandard homes.
There remain major concerns regarding the large numbers of buildings still being rented out without any EPC, estimated to be approaching half of those in the private rented sector. Anecdotally, it is thought that such law-breaking accommodation is likely to be fairly sub-standard.
Some 43 per cent of privately rented homes are overseen by a professional letting agent. Fortunately, agents are mandated by law to ensure that EPCs are available. Have they been doing so? A recent Parliamentary Question from Lib Dem Sarah Olney elicited the admission that the Housing Ministry hasn’t the faintest idea, and has no intention of finding out.
EPCs for buildings remain a great concept. But only if they are accurately assessed. And if any and all transgressors are actively pursued.

Boilers & Burners
For further information on Crowley Carbon visitwww.eibi.co.uk/enquiriesand enter ENQUIRY No. 125
Ben Churchill is chief revenue officer at Crowley Carbon
Ten steps to a more efficient boiler
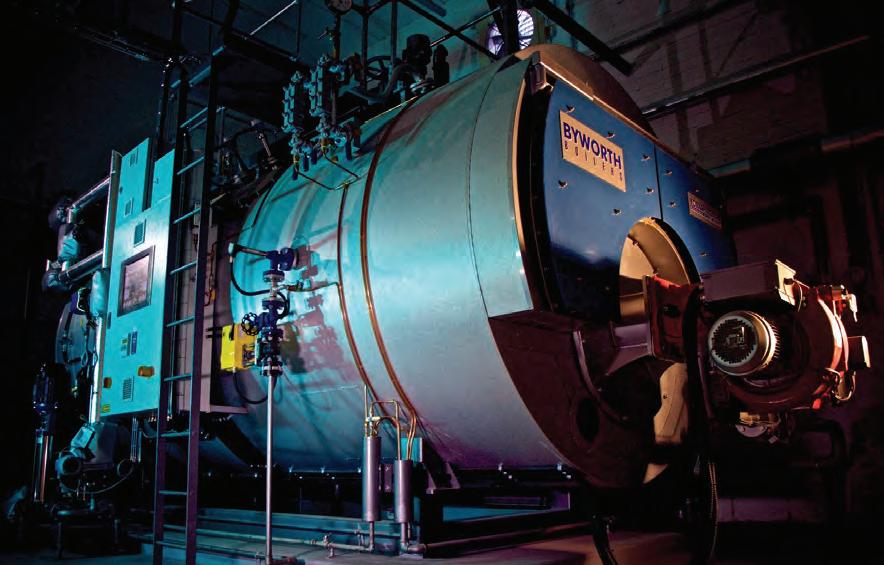
Are your boilers not working at optimum performance? Ben Churchill outlines ten ways to reduce maintenance and make your boiler more efficient
Boilers are an easy place your boiler and your steam reduces efficiency. In some cases, for businesses to save distribution systems. If boiler this may require sensors to be fitted money. Why? Because they water is too hard or treated and burner replacement. However, are often overlooked in improperly, or the boiler isn’t the investment may generate terms of maintenance and being blown down regularly, scale significant payback and savings, all performance. Furthermore, many will accumulate on heat transfer which can be sustained well into the businesses run old and inefficient surfaces. This scale will impede the future. boiler systems. heat transfer, reducing your boiler • Use VSD controls. If your boiler
There are two main areas where efficiency. The scale will also keep fans, boiler pumps and burners a boiler can lose efficiency: expelled the water from cooling heat transfer are not controlled by VSDs, the flue gases and boiler water. If you surfaces. If left untreated, scale can likelihood is that you are wasting ensure that your boiler expels the cause the boiler to overheat, leading energy. Quite simply, significant least amount of energy to your flue to costly boiler repairs and leaks. savings can be made by using and you are maximising the use Regular manual testing or online VSDs instead of dampers or valve of your boiler water, you will save water and efficiency testing can controls. Modern control systems money. detect problems before they escalate can optimise these savings while • Cleaning - clean the fireside of and restore the efficiency of the ensuring your system can meet all your boiler. This will ensure that boiler. its load requirements. soot or ash build up is not reducing • Control air settings - optimise • Fully utilise flue gas heat your heat exchange capacity. Soot oxygen for differing conditions. - use a specifically designed effectively insulates the boiler Low air generates soot, smoke and economiser. If you are sending tubes and reduces efficiency. Boiler carbon monoxide, all of which are excess heat up your flue, your boiler efficiency is also impacted when the very dangerous and cause reduced is not running to its optimum boiler isn’t getting the right amount heat transfer. Too much air also efficiency. Modern controls can help of air. reduces efficiency as the extra air is reduce heat loss. However, the best • Water treatment - poorly cold when acquired and has to be solution is a specifically designed treated water will destroy heated, which increases fuel use and economiser for your flue gas system. This can be used to preheat your feedwater or to displace some other hot water load in your process. A well-designed and professionally installed economiser can reduce fuel costs by 5-10 per cent. • Maximise your condensate return - there are a few ways to maximise your condensate return. Advantages include reduced water treatment costs, reduced energy consumption, reduced waste water and reduced fresh water usage. You can do this by: 1) ensuring your steam trapping is working optimally; 2) replacing direct steam heating with indirect steam heating; and 3) considering a pressurised condensate system. • Insulate - ensure proper insulation. Insulation on your boiler, on your valves and on your pipework deteriorate over time or are removed and not replaced properly after maintenance. Poor or improperly fitted insulation can significantly impact energy efficiency and maintenance costs and effect the overall operability of the system. • Blowdowns - fit a controlled blowdown system. Blowdowns are fundamental to good boiler operation as the process removes impurities from your steam boiler and minimises scale buildup. However, blowdowns are often not properly controlled and are frequently implemented unnecessarily. Fitting a controlled blowdown system which monitors the conductivity of your boiler water will stop you pouring valuable steam down the drain and ensure that you are controlling the conductivity of your steam effectively. • Control your steam load - peaky steam loads can hurt your boiler. Sudden changes to the steam load can cause carryover which occurs when the steam system pulls water from the boiler along with steam. This can damage pipes, valves and instrumentation. Peaky loads can often cause boilers to quench on high and low water levels and affect your production. • Air preheating - it is recommended to pre-heat your combustion air. A boiler takes cold air and heats it. A 5oC lift in input air temperature can increase the efficiency of a boiler by 1 per cent.
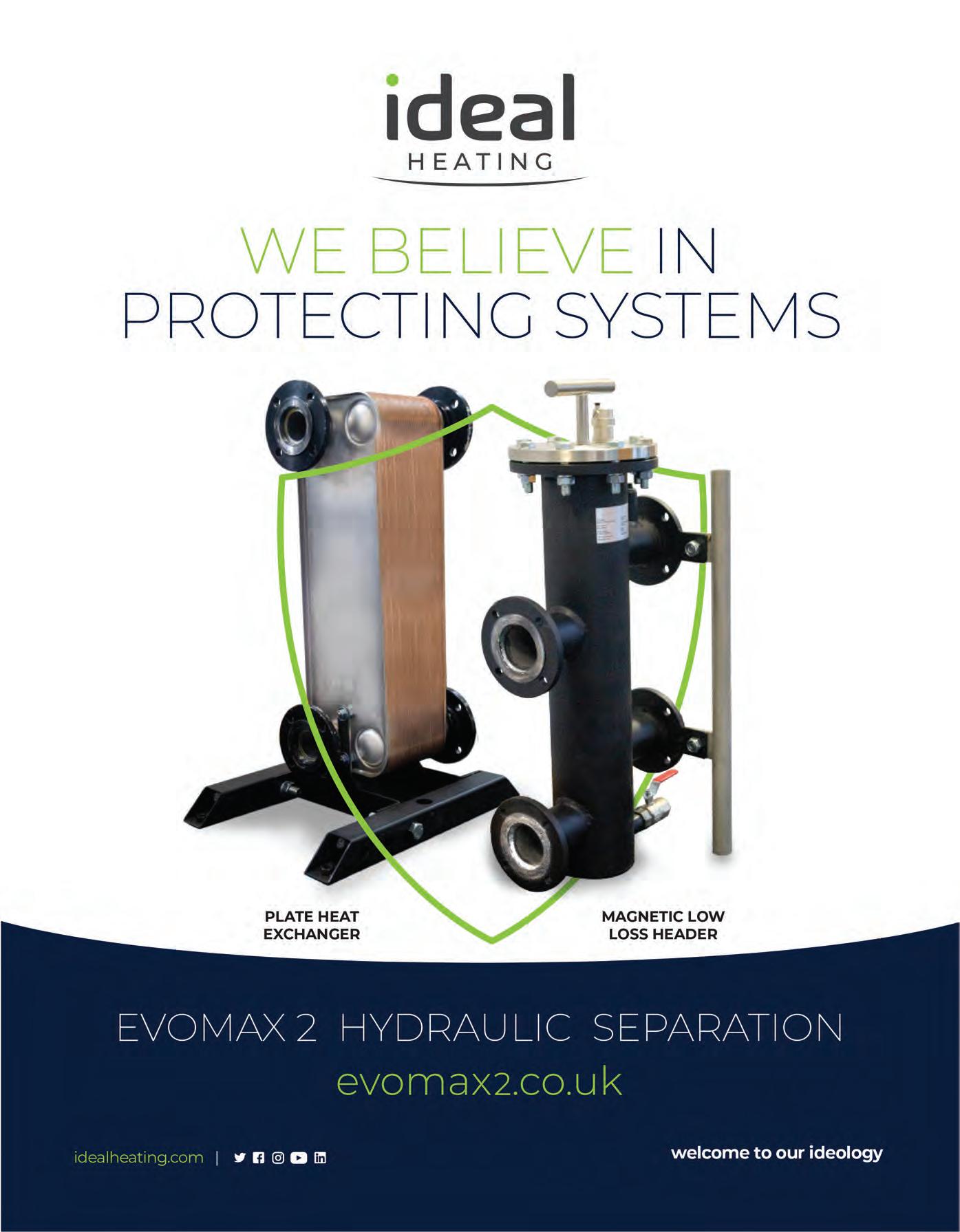
Boilers & Burners
For further information on Bosch Commercial & Industrial visitwww.eibi.co.uk/enquiriesand enter ENQUIRY No. 126
Pete Mills, is technical operations manager for Bosch Commercial & Industrial
Improving the here and now
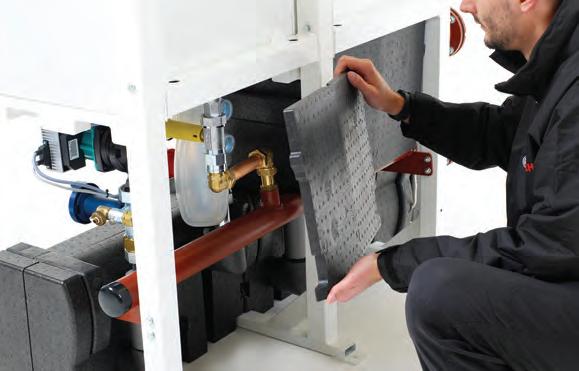
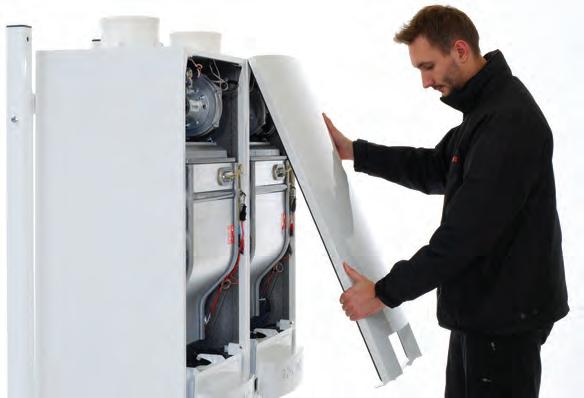
A conversion to hydrogen may be a likely long-term solution to decarbonisation of heating. But what can be done to improve the efficiency of existing boilers, asks Pete Mills We are all aware these days of the need for our heating systems to use less energy and if possible to proposal for widening of the wobbe band, which helps future proofing. Full 100 per cent hydrogen will require a new generation of appliances, of course, with the use energy from a renewable source. most likely route being that of a How we get to this stage and what hydrogen-ready gas appliance. This the implications of this transition will largely depend on the outcomes are will very much depend on the of Government-funded programmes circumstances of the building we such as Hy4Heat and HyDeploy. are heating, its age and thermal There is certainly some genuine performance. interest for large industrial boilers,
Government has for some time which have very long service laid out a broad policy objective lifetimes, to see how these could that highlights the potential routes be made ready for a hydrogen of the electrification of heat, conversion. Having a 10 per cent connection to district heating or oversized boiler shell at the outset eventual decarbonisation of the gas makes this a possibility and is well network. As guidance and regulation worth considering if you have develops further, the choices we face Modern condensing boilers can handle any blends of hydrogen up to the proposed 20 per cent appliances running with package when having to replace our heating the only option at this time decarbonisation for many buildings, burners into the MW size. boilers may be affected by tighter may be to remain with their gas as demonstrated in the recent report Condensing boilers need lower regulation and increased aspirations supply, optimise the control from Delta EE. return temperatures to get the to meet our social obligations. operation and reduce energy use greatest energy savings and sadly,
We should perhaps start this with improvements to building Genuine improvements this is still often over looked, process with a review of the options insulation. In the medium to long Many of our buildings may still particularly when a new boiler is that are available for the specific term, it may be that a decarbonised have inefficient non-condensing installed in a distress situation. building we need to heat and its gas supply has to come to the rescue boilers, which could see genuine Rebalancing systems from 82/71 to location. Many older buildings with if we are to tackle these hard to improvements through installing 80/60 is generally achievable for all poor thermal insulation and high treat buildings. The developments condensing boilers and reviewing but the oldest of heating systems. temperature heating systems will being made in exploring the use of the system operating temperatures. Coupling this with upgraded control require significant investment if hydrogen in our gas supplies look Modern condensing boilers, like systems that can offer weather the electrification route of using very encouraging. It is now highly the Bosch Condens 7000 F, are compensated control means that heat pumps is to be realised, while likely that we will see blends of particularly well adapted to the system temperatures can be lowered buildings that are more modern hydrogen being added to natural changes we may begin to see to for a significant number of days each may be adapted easier. This can gas, as the gas grid starts to go our current gas supply. They will year, when the demand will be less present a significant barrier if green. In the longer term, 100 certainly handle any blends of due to mild winter temperatures. businesses simply do not have the per cent hydrogen looks to hold hydrogen up to the proposed 20 per Selecting boilers that will offer a good money to invest right now. You the most cost-effective route to cent as well as the more complicated modulation range will help to ensure might be fortunate to be near to a that loads are matched better by the developing district heating scheme, boiler capacity and boiler cycling is where connection to the scheme reduced. This is not limited to the may be welcomed. This can certainly individual boiler turn down, but be an attractive option, but will should be considered across multiple typically require some upgrades to boilers within a cascade. This the system to ensure the low return arrangement can give very wide turn temperatures required by heat down ratios and has a much better networks can be achieved. In the load matching capacity. years to come, it is highly likely that Making these suggested regulations will tighten, meaning incremental improvements to hard choices about how we improve energy efficiency is certainly not and decarbonise our heating needs the ultimate goal for decarbonising will have to be made. heat, but in these strange times when
So what to do if your choices are businesses may be forced to make limited, your budget is cut or your hard choices, steps like this should be boiler is falling over? seen as a minimum step in the right
For many building operators, direction.

Boilers & Burners
For further information on Babcock Wanson visitwww.eibi.co.uk/enquiriesand enter ENQUIRY No. 127
Chris Horsley is process engineering director at Babcock Wanson
Live long and prosper
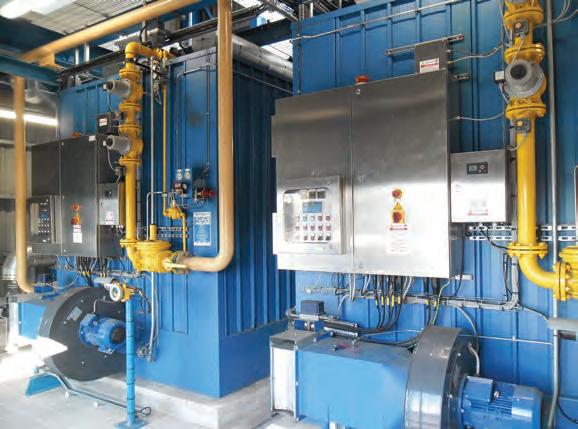
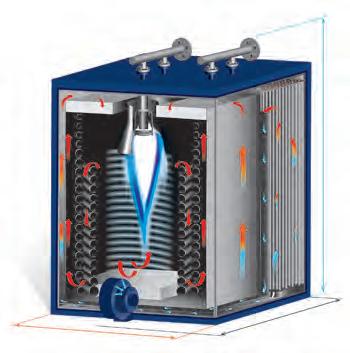
Thermal fluid heating has grown in popularity in recent years. Chris Horsley examines how this technology can bring energy saving and maintenance benefits
For a process heating equipment manufacturer, you might just say thermal fluid heaters are bad for business. They just go on and on - frequently for 20 years and often longer - and maintenance and service requirements are low, in fact a fraction of the cost of maintaining an equivalent heat output steam plant.
Even when the heaters themselves might be at the end of their working life, the pipe work system and other plant is often as good as new, so upgrades are simple and cost effective to implement at any time.
Thermal fluid heating is based on a similar principle to a simple hot water system. It consists of a heater connected to carbon steel Thermal fluid heaters, such as this one at Eastham Refinery, Ellesmere Port, have grown in popularity flow and return pipework which phase by pressure, so statutory reduction in productivity as it ages. can provide heat to one or more inspections are eliminated. A Babcock Wanson thermal fluid users or systems. Instead of water When it comes to flexibility in heater will usually run for more running through the pipework, a use, thermal fluid heaters often than 100,000 hours, although thermal fluid – typically a specialist work at high temperatures in a we are still servicing heaters that mineral oil or synthetic based simple closed loop. Compared are more than 40 years old and fluid – is used as the heat transfer to a steam system this means no working away every day quite medium. Different fluids can change of state of the fluid, so no happily! It would be difficult to be used to meet specific process condensate and therefore no flash find any equipment, process or heating requirements including steam losses, no blow down losses otherwise, that can match this high temperature operations and or make up water required, no level of service. processes requiring heating and effluent discharge and completely cooling thereby making it a very corrosion free operation without Exceptional longevity flexible system. the need for expensive chemical There’s no secret elixir for long
Thermal fluid heaters typically treatment. The savings thermal life when it comes to thermal operate at up to 350°C at fluid heaters bring are very fluid heaters. Their exceptional atmospheric pressure and remain significant, often up to 50 per cent pumpable down to -20°C and lower of the overall cost of running a with special fluids, which makes it process heating system. Thermal fluid heaters are unaffected by corrosion, contributing to a long service life a solution suitable for a multitude But one aspect that frequently of applications. gets overlooked is the longevity
Thermal fluid heaters have thermal fluid heaters enjoy, which rapidly grown in popularity across should be a major point when all industry sectors over the years. deciding how to heat a process,
This is mainly due to their far- especially in these uncertain times ranging benefits which include when many businesses are having to their ease of use, compact size, buckle belts that much tighter. With safer operation when compared sustainability a key issue, plant to steam generators, precise heat longevity is not only about reducing control, low exhaust emissions capex, but also reducing wastage and their energy efficiency. They and equipment redundancy. also operate outside the Pressure As mentioned, a thermal fluid
Systems Safety Regulations as the system should easily serve you fluid is not maintained in the liquid 20 or more years without any longevity is a direct result from their passive nature (there are very few moving parts) and the swapping out of water for a thermal fluid as the heat transfer medium. Unlike water- and steam-based systems, thermal fluid heaters are unaffected by corrosion caused by water over time, or by ambient temperature where water freezing within pipes leads to costly failures. In fact, most thermal fluids are mineral oil based so are effectively lubricants that help keep the system components protected in use.
However, not all thermal fluid heaters are equal, so it pays to do your homework. Heaters that will best stand the test of time are mostly designed for a downward fired configuration which ensures stress free and unrestricted expansion of the heater coils during normal operation. Also look for a heater that has been designed with a barrier between the hot combustion gases and the outer structure, as this will help provide long heater life as the higher pressure and cooler outer air helps prevent any escape of combustion gases as the plant ages over time.
Another key factor is overall emissions. With higher process operating efficiency comes lower total emissions which provides savings in operating costs while being much better for the environment.
It’s also vital that the thermal fluid heater you decide upon is correctly installed, commissioned and maintained. ‘Thermal Fluid Systems - A Practical Guide for Safe Design, Operation and Maintenance’ from the Combustion Engineering Association (CEA) proffers excellent advice for designers, owners, managers and operators of new and existing thermal fluid heating systems to operate safe and efficient installations.
With careful system design and careful choice of heater design a thermal fluid system will provide many years of trouble-free ownership, allowing the operator to concentrate on their process needs in the sure knowledge they are getting the best from their process heating investment.

eibi.co.uk/enquiries Enter 6
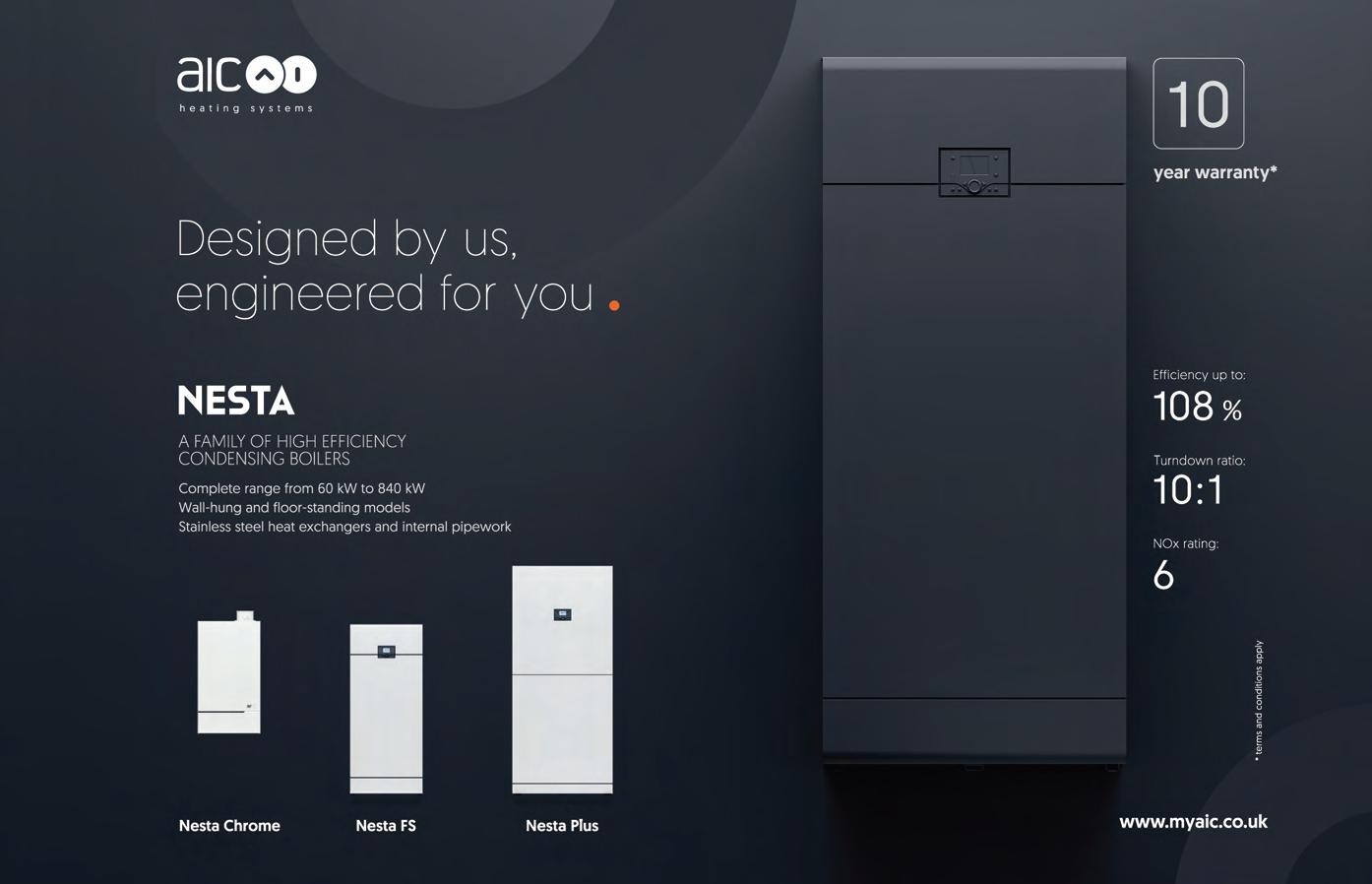
Boilers & Burners
For further information on products and services visit www.eibi.co.uk/enquiries and enter the appropriate online enquiry number
Hydrogenbased heating comes to the UK
UK-based green hydrogen project developer, Protium, together with its sister company Deuterium, is bringing a hydrogen-based heating solution to the UK.
Deuterium was launched this year to develop and commercialise new hydrogen technologies and has signed an exclusive IP licensing agreement with US-based Hydrogen Technologies Inc (HTI). The agreement aims to commercialise the company’s Hydrogen Dynamic Combustion Chamber (DCC), being the first project of its kind in the UK.
The DCC burns hydrogen and oxygen in a partial vacuum to create heat and steam. These can then be used for a wide variety of commercial and industrial applications, or to generate emission-free electricity, with the only by-product of the process being clean water. Deuterium acquired the licensing rights for this technology from the California-based Hydrogen Technologies Inc. in May 2020.
Deuterium will initially focus on identifying market participants to manufacture and assemble the system, with partner Protium identifying and working to develop the first commercialscale pilot site in UK.
Once deployed and operational, the solution will significantly support the decarbonisation of heating for properties in the UK, by providing a zero emission, low water usage heating system capable of displacing the use of fossil fuels for end-users.
Protium is in discussions with several UK industrial manufacturers to investigate viability of blending hydrogen and natural gas solutions to move towards net zero.
New boilers with weather compensation cut energy use
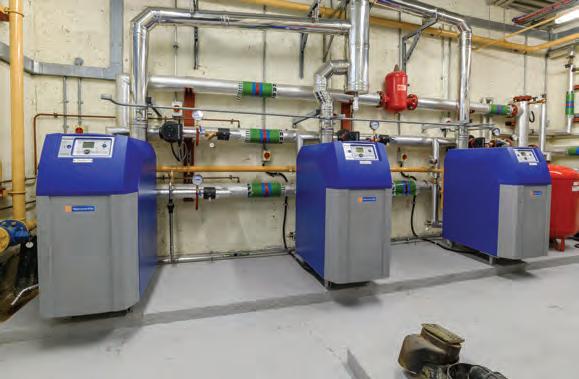
Allenbourn Middle School in Wimborne, Dorset, was suffering from an unreliable heating system. The three condensing boilers were getting old and unreliable.
Having worked on several other capital projects with the Wimborne Academy Trust which looks after the school, Coomber Associates were appointed to undertake the design, tendering, health and safety and contract administration of a replacement boiler plant.
The project was completed over the winter months. To maintain heat in the school during this period, a temporary mobile boiler plant was required.
A trailer with two of Hamworthy’s Stratton mk2 S2-150 wall hung boilers was provided. The mobile plant room provided heat for three weeks during which the replacement took place.
Other than the temporary plant, the difficulty of the project was to find boilers that would suit an old system and be compatible with the existing pipework. Fortunately, the Hamworthy Purewell Variheat mk2 cast iron condensing boilers fitted the bill with a similar footprint as the old boilers to sit on the same plinths. The cast iron heat exchanger with 10-year warranty and large waterways deals well with existing debris in older heating systems. The three boilers deliver an output of up to 285kW (50°/30°C) and can match the heat demand with a turndown ratio of 9:1.
Stuart Giles, engineering technician at Giles Heating and director at The Temporary Boiler Company, stated: “We have reduced the boiler outputs from 120kW to 95kW per boiler as part of the design. "Additionally, we have installed weather compensation, so the heating system only turns on when needed according to outside temperatures. The lower output boilers in combination with this and closer load matching thanks to the high turndown ratio means we’re effectively reducing energy wastage.”
ONLINE ENQUIRY 145
New burner for smaller output boilers
Following the launch of the Optimo 2 burner for medium size firetube steam boilers, Babcock Wanson has introduced the Optimo 1 which incorporates all the technological innovations of Optimo 2 but in a burner designed for smaller output boilers with a capacity of 1 to 2 t/h.
Optimo 1 ensures compliance with all applicable regulations, including the Medium Combustion Plant (MCP) Directive.
In addition to good environmental performance, Optimo 1 has been designed for energy efficiency, achieved through precise digital control of low excess air levels throughout the turndown range resulting in an excellent combustion efficiency regardless of the process load. Furthermore, Optimo 1 performs with a very high turndown ratio, enabling the burner to adjust its output to meet the needs of the process. This avoids the costly energy losses incurred by continual stop/start cycles, making Optimo 1 highly cost-effective and further adding to its overall operational efficiency.
Electricity consumption has also been reduced in this latest Babcock Wanson burner through the introduction of three interchangeable combustion air fans, covering the power range 1t/h, 1.5t/h and 2t/h. This enables Optimo 1 to match the boiler requirement and allows greater burner turndown as well as reduced electric consumption when operating at lower power levels.
The wider fan range available with the Optimo 1 has a
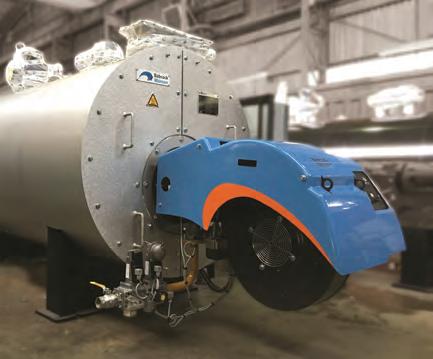
further benefit in that noise emission levels are reduced when using lower fan powers. With a new burner casing design, Babcock Wanson is also able to offer sound insulation where required.
The new casing of this latest Babcock Wanson burner has all the electronics of the combustion equipment integrated directly into it, facilitating its interface with a customer’s plant. ONLINE ENQUIRY 146
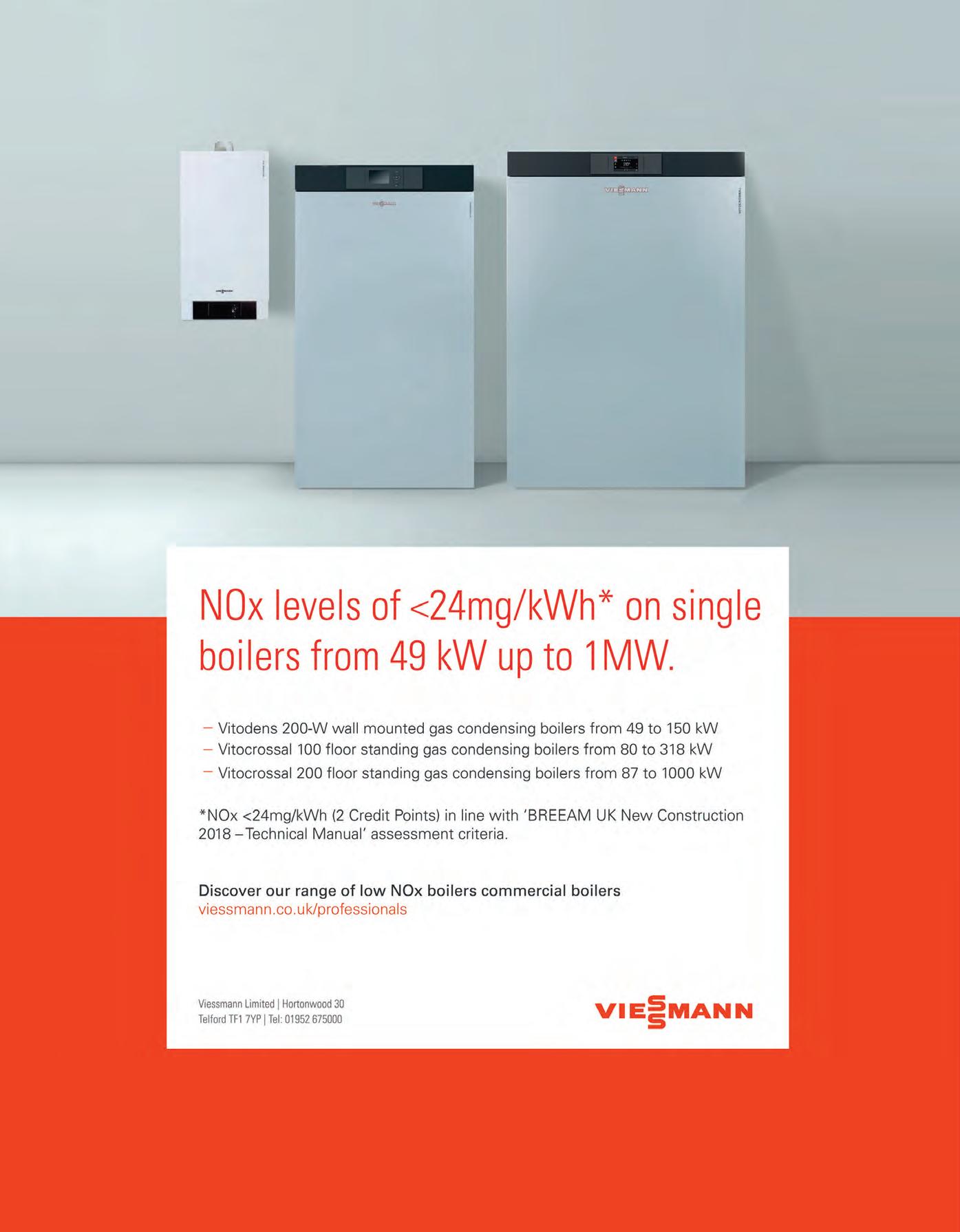
Boilers & Burners
For further information on products and services visit www.eibi.co.uk/enquiries and enter the appropriate online enquiry number
Boilers for Nottingham hospital

When, as part of a routine maintenance programme, Nottingham City Hospital’s Children’s Centre identified that the old boiler plant needed replacing, they engaged D H Squire Consulting Engineers LLP to advise on the most appropriate solution. Energy efficiency and reliability were the key considerations, along with the need to avoid any disruption to the hot water service throughout the changeover.
Patrick McBennett at D H Squire Consulting Engineers LLP specified two Remeha Gas 220 Ace 300 floorstanding boilers to meet the demand for space heating and domestic hot water.
A temporary boiler was already in place at the Children’s Centre, feeding two plate heat exchangers and meeting the requirement for an uninterrupted hot water supply. This enabled Palms Facilities, the principle contractor on the project, to begin work immediately on stripping out the two old floor-standing boilers.
The Palms Facilities team installed the two new Remeha boilers using the manufacturer’s cascade system and a low loss header. The latter will help optimise the performance and efficiency of the heating system while protecting the new boilers and increasing their lifespan through hydraulic separation of the primary and secondary circuits.
New flues and pump sets were also fitted as part of the project and the plant room and floors painted once the installation was complete.
ONLINE ENQUIRY 143
Burners help brewery upgrade
The largest brewery in the southern hemisphere has recently embarked on a programme to cut its carbon footprint and reduce its emissions.
South African Breweries has installed two natural-gas -fired boilers at its Rosslyn factory, near Pretoria. In addition, two of the existing coal-fired boilers have been converted to gas. A key part of the installation were four burners from Kent-based Limpsfield Combustion Engineering. The result has been a reduction in fuel consumption of almost a third while boiler efficiency has been boosted by 13 per cent.
The brewer reports that the new plant provides quick reaction to plant load and allows easy maintenance. In addition, the boiler house is considerably quieter thanks to an air inlet silencer. A further benefit is that CO levels are kept to below 10ppm.
The burners chosen for the brewery are the LC200, LC88 and two LC44 units. The LC range is available in a number of models with outputs ranging from 0.9 to 62MW. ONLINE ENQUIRY 142
Condensing boiler range extended
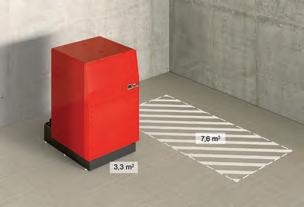
The Hoval UltraGas (1550) extends the upper output capacity of the popular UltraGas family of condensing boilers to 1,550kW, with the benefits of a substantially smaller footprint compared to similar sized condensing boilers on the market. With outputs ranging from 15kW to 1,550kW, with the same design and operation throughout, UltraGas boilers now offer low NOx, optimum efficiency solutions for the majority of applications, including heat networks and other large energy centres. The UltraGas (1550) measures just 1,550mm width, 2,152mm depth and 2,547mm height with a footprint of only 3.3m2. This has been achieved through further refinements to the aluFer heat exchangers and modulating premix burners.
This, combined with flexible connections, makes the UltraGas (1550) ideal for installation in tight spaces, freeing up plant room space for other items.
In keeping with the rest of the UltraGas family, UltraGas (1550) combines high efficiency with low emissions at all outputs. NOx emissions, for instance are just 31mg/kWh (relative to gross calorific value, according to EN 15502). As with other UltraGas boilers, control is via Hoval’s intelligent TopTronic system, which can also act as an interface with building management systems.
The premix burner generates an homogenous, optimum fuel/air mixture which can be adjusted across a wide range to meet varying heat loads by modulating the fan speed. As a result, UltraGas (1550) delivers a modulation range from 328kW to 1,550kW. ONLINE ENQUIRY 140
Added control with latest burner
SAACKE has added a new version to its TEMINOX range of burners.
The new unit has a more advanced burner head and its mixing system, variability in the nozzle geometry and the adjustable stabilisation plate ensure a high control range of up to 1:10 (gas operation).
The standard design is equipped with an electronic fuel-air compound control. A SAACKE UV flame sensor is provided for flame detection which monitors a wider frequency spectrum resulting in higher operational reliability.
The compact TEMINOX burner is delivered ready for connection to shell and water tube boilers, thermal oil heaters and thermal processing plants. It can be flexibly configured for the use of special fuels. Integrated SAACKE SCanView controls including variable speed drive and O2 control can be included. Because of its simple installation, commissioning and maintenance, the TEMINOX reduces the plant downtime and is suitable for new construction and retrofitting as additional combustion air duct systems are not required. The monoblock version has an integrated highperformance fan designed specifically for the burner which, together with the energy efficient motors, achieves high efficiency and can overcome large flue gasside draft losses where necessary. The duoblock version provides the additional option of use with preheated combustion air. The optional double gas ring also enables the simultaneous firing of two different gases.
With gas emissions less than 30 mg/m3, SAACKE’s ultra-low NOx TEMINOX burners have a capacity range from 3-28MW. The company says they meet the strictest regulations with low CO and residual oxygen content in the exhaust gas. ONLINE ENQUIRY 141