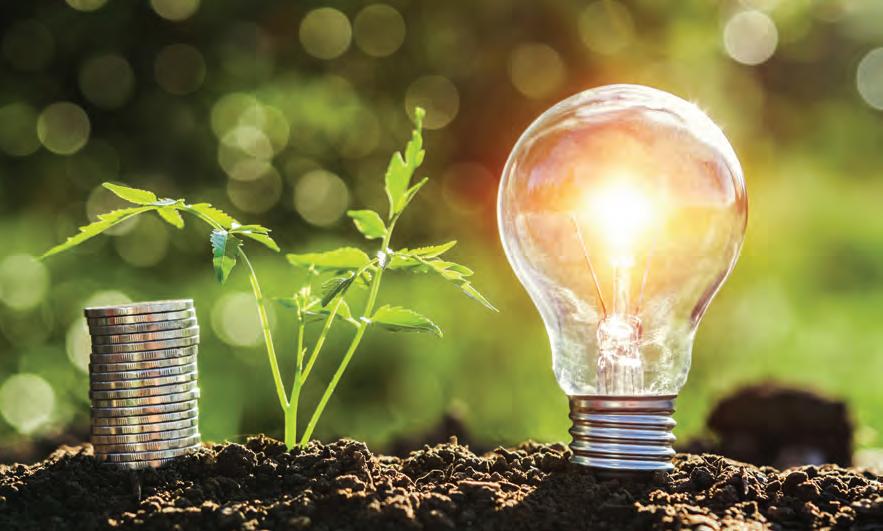
4 minute read
Compressed Air
Alexander Pavlov is UK general manager for Atlas Copco’s Compressors UK
Ten steps to greener production
Advertisement
Energy reduction is the only way to a carbon-neutral economy – and it can start in the compressor room, says Alexander Pavlov
The 10 steps to greener production in this guide can be taken right away and cost little. They are part of a continuous process to maintain peak production efficiency.
Step 1: Matching equipment to applications
Companies waste up to 50 per cent of the power needed to generate compressed air through inappropriate use or inefficient systems design. In many cases, they may be able to invest in smaller, cheaper equipment, as long as they have eliminated inefficiencies. 1) Isolate equipment when it is not in use. Use a simple manual isolation valve or an electronic valve to reduce equipment leakage. 2) Keep cool. Compressed air equipment should be installed in the coolest location in the facility, and heat generated should be removed from the compressor room. Every 5°C rise in air temperature results in a 2 per cent loss in efficiency. 3) Keep clean. Dust in the air will block filters. Every 3 millibar pressure drop in the intake filter increases power consumption by 1 per cent. 4) Keep working pressure as low as possible. A higher working pressure means a higher power requirement, higher energy costs and a larger carbon footprint. Step 2: Storage and distribution
Air receivers reduce the cycling time of air compressors, which increases their reliability and longevity. A larger air receiver can reduce power consumption. Consider separate compressed air systems if the majority of the production requires a lower pressure than the highest pressure requirement.
Companies often simply extend their pipework to meet the needs of new equipment, but this can cause pressure drops. There are three inexpensive ways to address this: 1. Increase the main distribution pipework diameter. This will enlarge the stored volume and also reduce air velocity and pressure drop. 2. Convert a dead-end or single pipework system into a ring-main pipework system. This increases volume and lowers the pressure drop. 3. Plug the leaks. The average production facility loses up to 20 per cent of the compressed air it generates to leaks.
Step 3: Know air purity requirements
Treating compressed air costs energy and money, so it is important to know the level of air purity required.
Atmospheric air contains water vapour and dust. When that air is compressed, the concentration of these contaminants also increases, and they must be filtered out to protect equipment and maintain the required level of air purity.
Step 4: Understanding air demand
It is important to be aware of peak production periods and times of lower air demand. With a good understanding of actual demand, it may be possible to save money when investing in a new compressor.
Step 5: Compressor types and their benefits
There are many types of air compressors, with different advantages based on operating pressure and flow requirements.
Piston compressor: Highly efficient on-load and off-load, but may not be suitable for all duty cycles.
Scroll compressor: Mainly used in applications requiring small and clean oil-free airflows. Best used in intermittent air demand applications. Simple and easy to maintain.
Tooth compressor: Oil-free, rotary tooth compressors are suitable for small to medium-sized applications. Good for intermittent and continuous duty applications.
Rotary screw compressor: The most common type, used in many applications. Screw compressors can maintain peak efficiency over a wide variety of flows.
Centrifugal compressor: Centrifugal compressors are most efficient when running continuously and are best for large volumes of compressed air.
Step 6: Equipment control
More pressure means more energy consumption. Control methods differ, and the flow pattern will determine which is best for a given installation. Generally, compressors are set to run within a pressure band; the wider the pressure band, the more energy is consumed. One method to narrow the pressure band is to use variablespeed drives.
Step 7: Optimising system control
A smart central controller that accommodates different compressor technologies and control types will lower the overall pressure bands to deliver the required air output in the most efficient way.
Step 8: Energy recovery
Up to 90 per cent of the electrical energy a compressor uses is converted into heat. That is why energy recovery is the best option to reduce energy consumption. Hot air can be captured and routed to a place where it is useful – for example, to warm a factory during the winter. Or heat can be removed from the cooling system via plate heat exchangers to heat water for boilers or showers.
Step 9: System maintenance
Maintenance is an essential component of an energy optimisation system. A well-maintained compressed air system will more than pay for its maintenance costs through energy savings.
Step 10: Remote monitoring
Smart remote monitoring technologies make it possible to connect industrial equipment over a secure network to mobile devices, to stay informed, optimise equipment performance from any location and receive messages that highlight potential issues.
Through adopting the ten steps strategy, not only do compressor owners derive environmental, financial and productivity benefits, but they can make progress towards achieving ISO50001 standard certification. Certification demonstrates an organisation’s commitment to reducing energy use and greenhouse gas emissions.