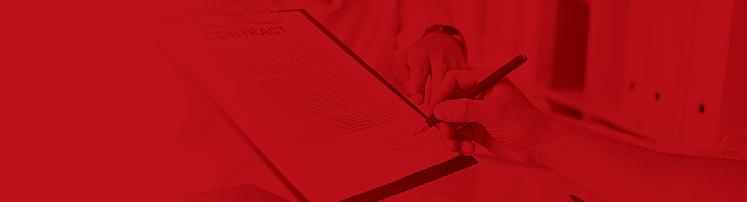
33 minute read
ESTA Viewpoint
A slow road towards a green recovery
Advertisement
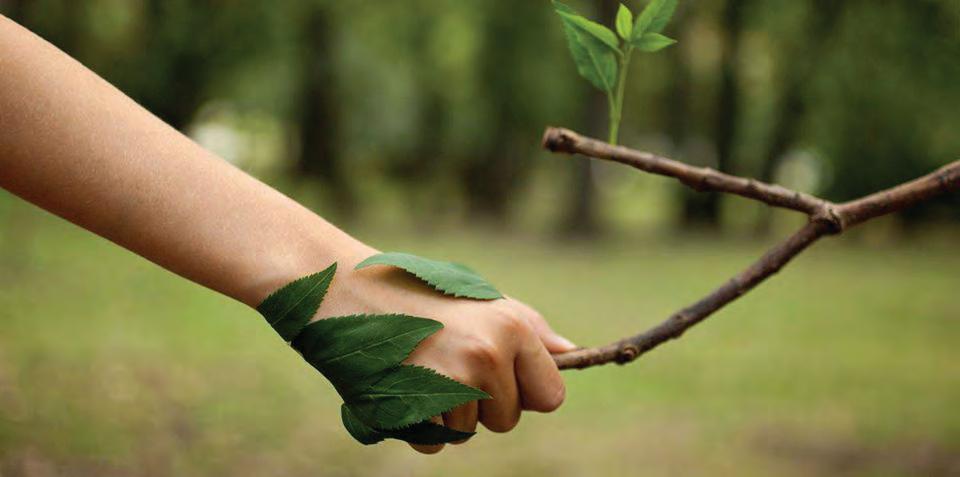
As hosts of the COP26 summit the UK should be leading the way to a green recovery. But current government policies are falling well short, says Mervyn Pilley
There is an overwhelming consensus from the UK population that any post pandemic response should be based around tackling the environmental crisis more urgently through a ‘green recovery.’
The Chancellor, Rishi Sunak, through his recent summer economic update, has been working hard again to try and deal with the immense challenges facing him. However, the general view of his announced plans is that it represents an encouraging but far too small start along the road. One must hope that an autumn statement will go far faster and further. It was always likely to be ultra-difficult for the chancellor to keep everybody happy due to the costs of dealing with the pandemic and the resulting knock-on effect of the economy. The road to economic recovery is littered with obstacles.
Despite that, it would seem to make sense for more joined-up policy thinking. In view of the likely huge increase in the UK unemployment figure it would surely be sensible to strive to invest in creating jobs in what should be a fastgrowing sector – green jobs involving carbon reduction. Unfortunately, the Government has failed to employ joinedup thinking at sufficient scale. While there are areas of hope, it is noticeable that the £9.2bn earmarked in the Conservative Party manifesto has not really begun to be spent. Yes, a manifesto is just that and not a policy but even that was not enough when compared with green recovery spends in other countries in Europe. There is a debate of just how much of the newly announced spending is new money and not just a rehash of previous announcements.
Talking about rehashed things, the green homes grant scheme is effectively a rehashed green deal policy and, as was shown then, it is very unlikely that homeowners will be sufficiently motivated by promises of part payment towards insulation of their homes.
One must ask why the Government does not use the tax system far more to change behaviours. It is ironic
Mervyn Pilley is executive director of ESTA (Energy Services and Technology Association)
that the Government withdrew the Enhanced Capital Allowances on the 1st April this year that has immediately taken away an incentive for UK plc to invest in equipment offering energy efficiency solutions. Unfortunately, this is another example of how energy efficiency is treated as the poor relation of carbon reduction whereas it should be an absolute cornerstone of a carbon reduction plan. The Government itself, albeit with a different Prime Minster, has enshrined net zero targets in law so it must do what is needed to avoid breaking its own law.
Installers are needed, both for that scheme and retrofit at scale. Interestingly, it is the creation of an army of installers that would potentially help solve a large part of the rise in unemployment. The installers required to carry out retrofit to residential and commercial property is going to be supplied in the most part by SMEs. Main consultants may be the organisers/ facilitators, but the SME supply chain will provide the labour. What does not help, therefore, are confusing policies for incentives to take on trainees and apprentices that never seem to last for long. Very small, one-off grants are not going to solve the big problems.
SMEs will have a lot of expensive barriers to jump through to get onto the Government’s chosen quality approval schemes for retrofit. A far greater incentive will be needed to persuade companies to take on a long-term and sustainable workforce. Why could this not be achieved through the tax system? This type of incentive would actually cost the Treasury less as the tax take would go up from PAYE on employees as well as more corporation tax on businesses’ increased profits.
The same issues apply to the construction sector in general. Brexit and an ageing workforce, coupled with the abject failure of schemes such as the apprenticeship levy, have meant that the skills shortage in all areas of construction and engineering is only going to get worse.
Time is short for all of us. As hosts of the rearranged COP26 we should be leading the world in green policies. Unfortunately, the ambition just is not there. There is going to have to be major increase in green policies in the forthcoming autumn budget.
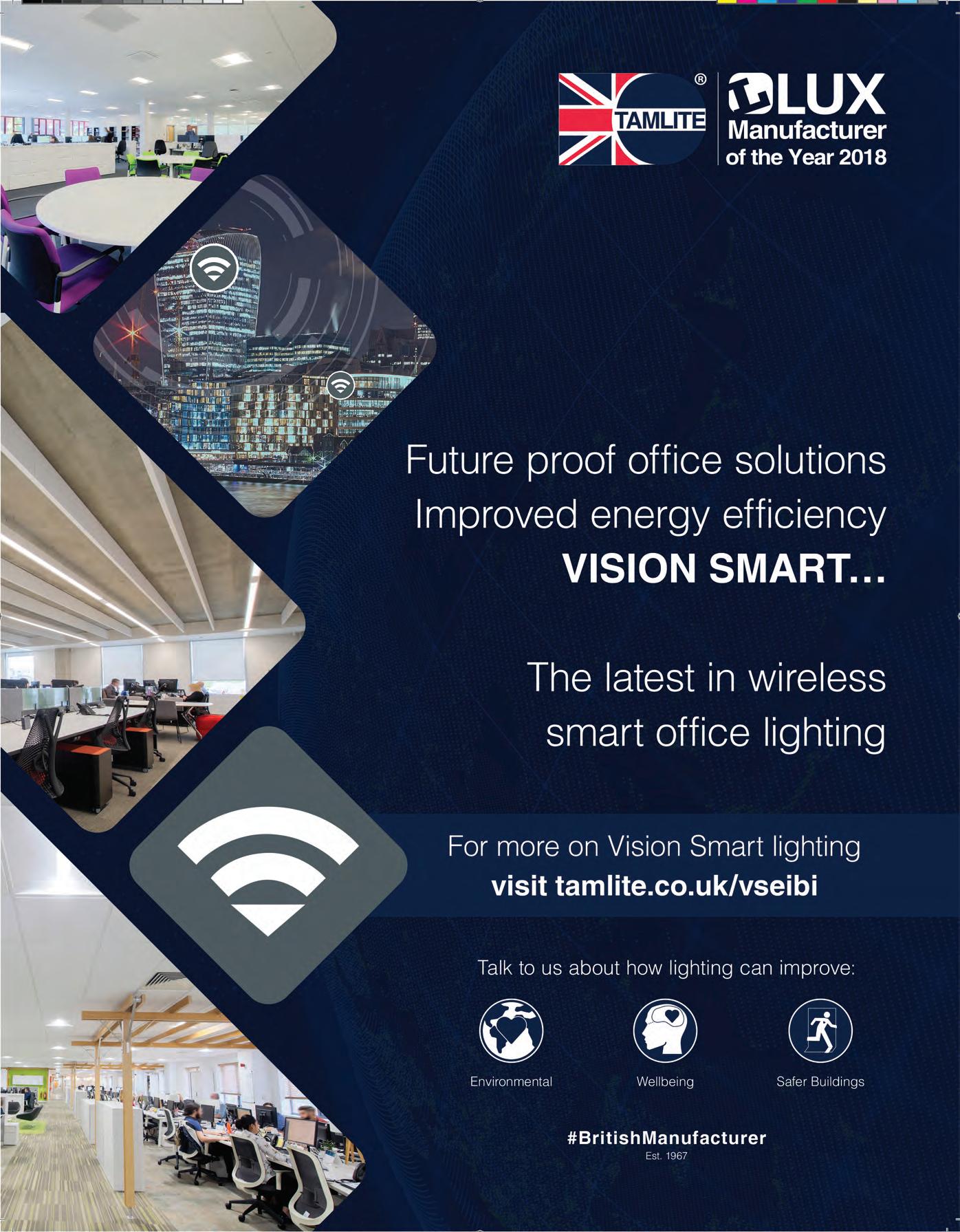
Smart Buildings
For further information onSchneider Electricvisitwww.eibi.co.uk/enquiriesand enter ENQUIRY No. 134
Kas Mohammed is vice president of digital energy, Schneider Electric
Welcome back to the office
Kas Mohammed explains how smart buildings will help us adjust to a new world where data automation and connected technology will play a fundamental role in workforce management
As lockdown restrictions ease, more workers are returning to the workplace. Over the past few months, the concept of an office has altered past the point of return – open-plan offices and hot-desking suddenly look more risky than revolutionary, busy is bad and airflow isn’t just positive, it’s necessary.
Facility managers have a raft of other key considerations before they can welcome back occupants. Fundamentally, they must take care of everyone’s wellbeing by putting all available safeguards in place. This includes developing specialised strategies that meet the individual demands, enabling social distancing, and effectively and consistently communicating any updates.
While safety is the current priority, ensuring buildings support wellbeing, productivity and development is also key. While facility managers have traditionally relied on verbal feedback, smart building technology, from sensors to software, will now play a vital role in creating safe and productive buildings. Modern technology can monitor and control occupancy, comfort, energy usage and improve communication. As a result, office spaces can be made safe and sustainable, while improving the health, happiness and productivity of occupants.
Man y people are concerned and anxious about being in or travelling to workplaces. A recent study of 2,000 adults commissioned by Bupa Health Clinics found as many as 65 per cent of people in the UK are anxious about returning to their office. Another report from the TUC, showed that 39 per cent of UK workers are concerned about their ability to socially distance from colleagues. Clearly, workplaces need to become smarter and more flexible to cater to the new realities.
However, one crucial piece of
Modern digital management systems ensure energy managers can understand the real-time and long-term uses of spaces
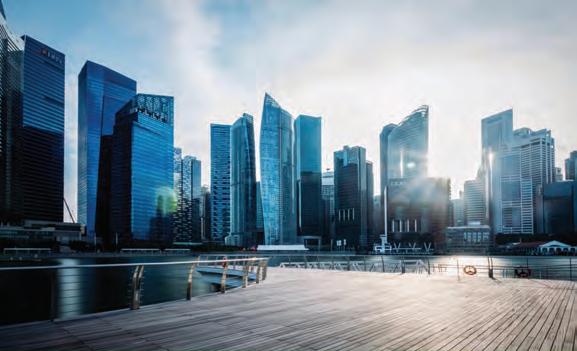
the puzzle is often ignored. All the health and safety strategies available can be implemented, but without effective communication they risk being ignored or misunderstood.
Workplace information To improve communication and provide instant access to workplace information, building managers are increasingly turning to fully customisable, centralised mobile applications. Such apps, linked to building technology, can send automatic and personal updates to occupants on everything from parking restrictions, desk changes, densely populated zones, meeting room bookings, comfort controls, transport issue and more, all on a single platform. Furthermore, administrators and HR departments can be granted the ability get instant feedback on strategies, usage and services, to greatly improve decision-making at a business level.
The return to work is likely to put greater stress on the office environment, with flexible shifts and hours becoming more common. This widely considered tactic aims to reduce the large numbers of people travelling at peak times and therefore the spread of infection.
Some high-profile businesses, including Facebook and Google, have already employed large-scale flexible work schemes. In light of the environmental impact, with lower levels of pollution and energy use from fewer commutes, some are touting an end of the traditional office.
However, there is research that suggests that remote working is not for everyone. According to a survey from the Society for Human Resources, 71 per cent of us are struggling to adjust to remote work, 65 per cent sa y maintaining employee morale has been a challenge, and more than a third are facing difficulties with company culture.
Clearly, there are positives and negatives on either side of the argument, with individual circumstances determining the best course of action. Fundamentally, an effective level of personal, instant and ongoing management requires a smart, connected building management system.
Modern digital office management systems provide facility managers with the ability to understand the real-time and long-term uses of spaces with the office to improve comfort, enhance productivity, and reduce facility service costs.
Creating safe zones, improving flow, flagging vacating desks and updating on numbers, is all automatically and instantly fed to office admin teams to ensure safety, comfort and efficiency. Without micro-managing or dictating rigid policies, these teams can effectively manage their workforce from afar, gaining unparalleled insight on activity.
Society, business and buildings have passed the point of no return. We are entering a new age, where data, automation and connected technology will play a fundamental role not just in manufacturing and IT, but in workforce management, engagement, safety and development.
Data, combined with the latest technology, holds the key. We must create a smarter workplace with joined-up systems allowing us to monitor and automate key processes, including staf f seating and of fice access based on capacity and occupancy levels.
Modern of fice management technology can ensure that social distancing is maintained by ensuring occupants are located appropriately in agreed zones (enabling lighting/heating, etc. to be switched off or reduced in areas that aren’t occupied). It can determine the best of fice flows to minimise unnecessary contact and ensure these are being followed. Empty desks can be f lagged and cleaned as soon as they are vacated, while fresh air is pumped during the hours required or when levels drop below a certain point in specific areas.
Smart of fice technology enables effective communication with, as well the management and understanding of the occupants of a building. We have to come to appreciate the role these abilities play in creating a healthy, comfortable work environment and a more enjoyable and productive workplace - now is the time to build our workplaces back better with smart, connected technology at its foundation.
Smart Buildings
For further information onEnOceanvisitwww.eibi.co.uk/enquiriesand enter ENQUIRY No. 135
Andreas Schneider is CEO of EnOcean
More than energy efficiency
Andreas Schneider takes a look at how building smart is the only way to cut CO2 emissions and make the best possible use of the space in the offices of the future
Our society is facing major challenges – caused by a global transformation. These include climate change and the need to drastically cut CO 2 emissions. However, global developments such as increasing urbanisation and ageing populations also demand answers. Business as usual is simply not working any more.
In exaggerated terms, this means that simply constructing higher buildings or adding more streets won’t solve the problem. Only smart, networked use of existing buildings and infrastructure will produce a sustainable concept. Although technology cannot be the sole answer, when combined with other factors, digitalisation, in particular, supports this change and makes it easier for people. After all, digitalisation supplies data for new workplaces and living environments and thereby makes for a livable future in a rapidly changing world.
Buildings are currently being put to the test, as they are some of the world’s biggest CO 2 producers. They account for one third of all CO 2 emissions in the EU. The energy savings potential is equally high – for example, with smart building control in residential and commercial structures.
The EU has set clear targets for its member states with the European Energy Performance of Buildings Directive (EPBD). Existing buildings are supposed to be CO 2 neutral by 2050, with a focus on networking and smart building control, among other things. For example, the digitalisation of heating and air-conditioning systems is intended to provide information about a building’s actual energy efficiency. The EU is serious about this: Member states were required to implement the directive into national law by March 2020.
To meet legal requirements,
Raw data collected by millions of sensors can be the solution for the huge demands that will be placed on the buildings of the future
the various disciplines must be intelligently interconnected and digitalised in keeping with a smart building or smart home. Standardised interfaces and open wireless standards like those specified by the EnOcean Alliance, Bluetooth SIG and Zigbee Alliance form the basis for this.
Certifying complete buildings The Smart Buildings Alliance (SBA) presented its Ready2Services concept on this basis in 2018. Complete buildings can be certified so that the sensors and gateways used are interoperable with the entire network infrastructure and the various IT applications.
Employee well-being and productivity can be increased in offices through different parameters such as human-centric lighting (HCL) and demand
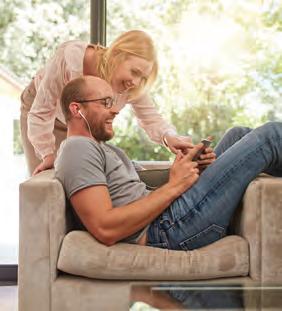
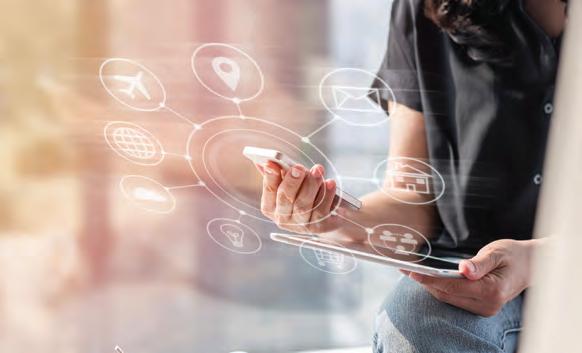
based use of space. The use of IoT solutions allows companies to adapt their planned use of space to actual and ever-changing requirements, thereby identifying and cutting hidden costs.
In the US, the LaSalle real estate consulting firm has come up with an interesting calculation. The 3-30-300 rule is an example of the average cost ratios incurred by a company. • $3 for energy; • $30 for space; • $300 for salaries.
All figures are per square foot (0.09m 2 ) per year.
Because of the legal requirements mentioned above (EPBD, Title 24), companies must take action and lower their energy consumption to reduce the CO 2 emissions of buildings. In many cases, a logical step is to invest in a smart, radio-based heating control system. At first glance, this pays off only where energy consumption is concerned, but in fact it is an initial step toward digitalised building spaces and thus offers additional savings potential.
If a certain basic infrastructure consisting of radio-based sensors, gateways and actuators is present, the system can be easily expanded. One common application is to optimise the use of rooms in commercial buildings. For example, if 30 to 40 percent of the desks remain unused on a regular basis, it is worthwhile to introduce a hot-desking concept, in which the employees flexibly share desks depending on occupancy. To do this, additional presence sensors are needed to record the presence of people in a room or at a desk and send this information to the cloud, where an algorithm controls occupancy. This approach can reduce the cost of space, especially in expensive urban locations.
Attractive work environments have been proven to increase employee productivity. According to LaSalle, optimisation has the greatest impact in this area. Concepts such as employee wellness take these findings into account and optimise work environments for employees. They include control of room temperature, air quality, humidity and lights, as well as including IoT solutions for demand-oriented cleaning service of restrooms and kitchens. Such applications create new tasks and business areas for facility management. The idea is no longer to simply manage a building but to offer new services.
However, smart buildings are the wave of the future and not only for environmental reasons. The ability to charge electric cars must be provided, while demographic change requires new approaches to looking after people in need of care, and crowded conditions in cities demand better use of space.
Raw data collected by millions of sensors can be the solution for all these scenarios. This data forms the basis for energy efficiency, CO 2 reduction and better use of resources. In light of the large number of sensors required, these devices must be standardised, radio-based, self-powered and easy to retrofit. The energy harvesting technology from EnOcean enables new and existing buildings to be sustainably digitalised and made smart – without any cables or battery waste.
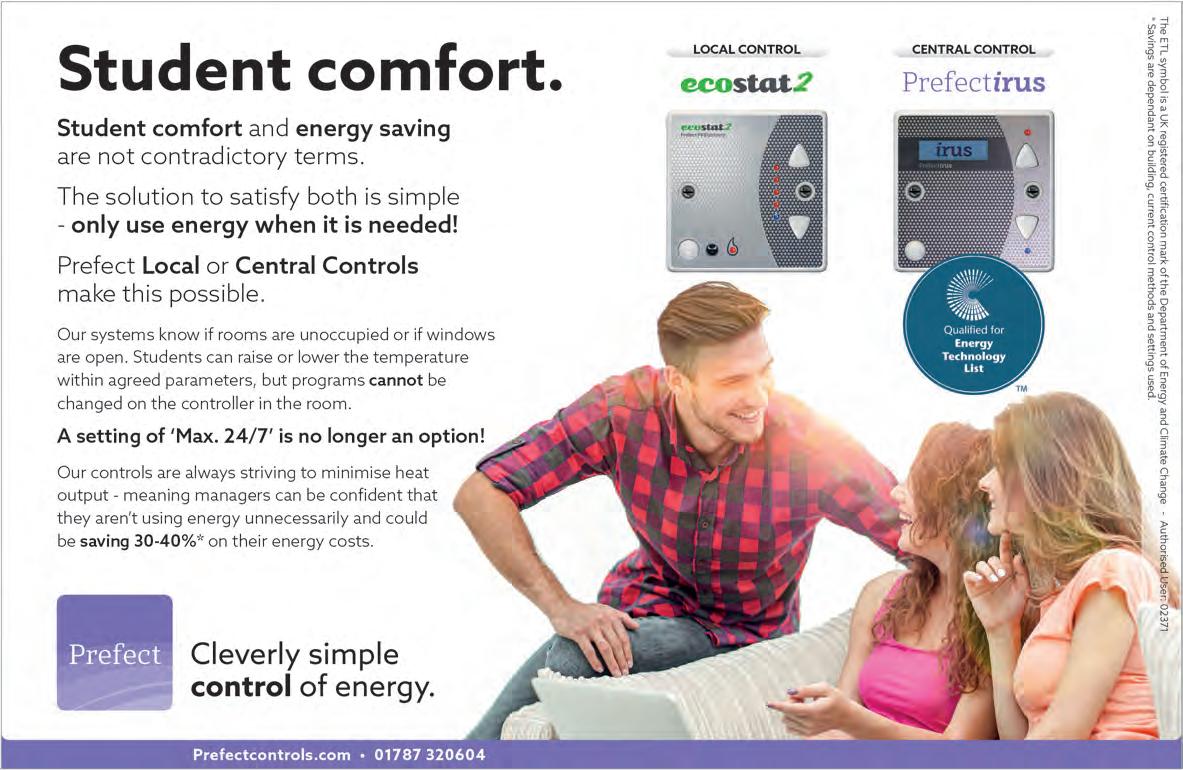
eibi.co.uk/enquiries Enter 11
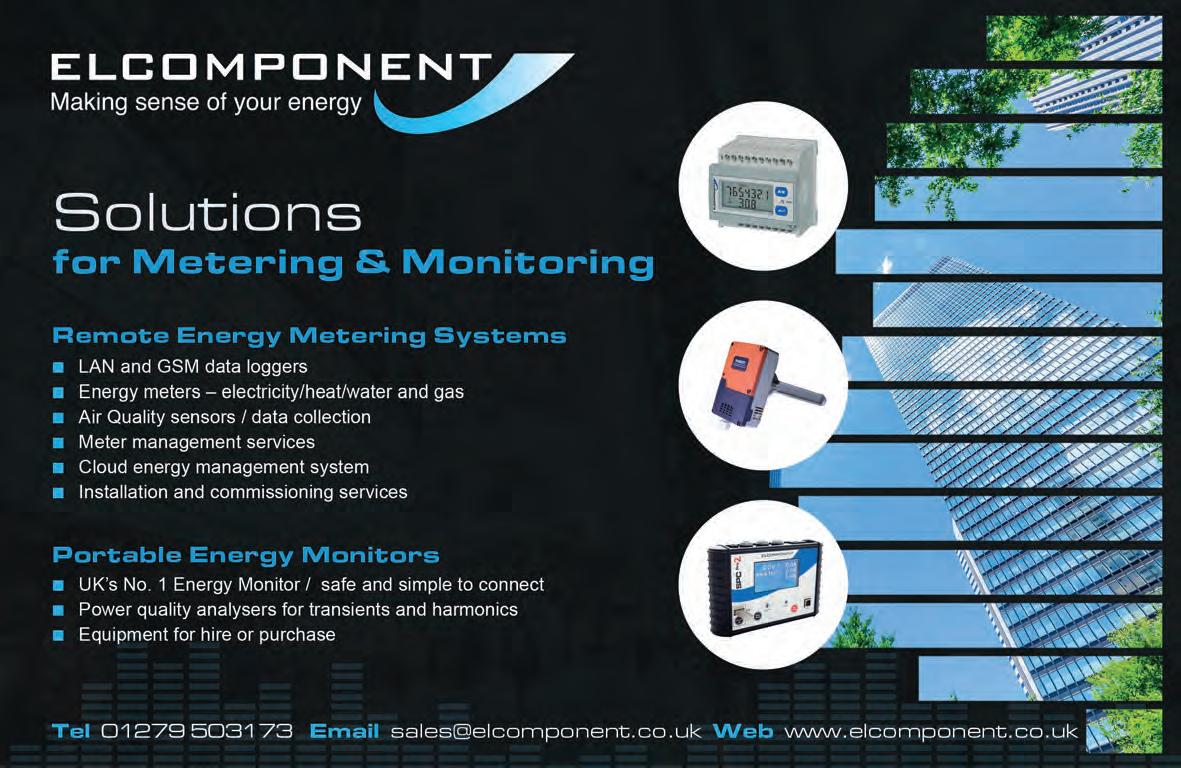
Smart Buildings
For further information on products and services visit www.eibi.co.uk/enquiries and enter the appropriate online enquiry number
Controllers ‘transform’ buildings
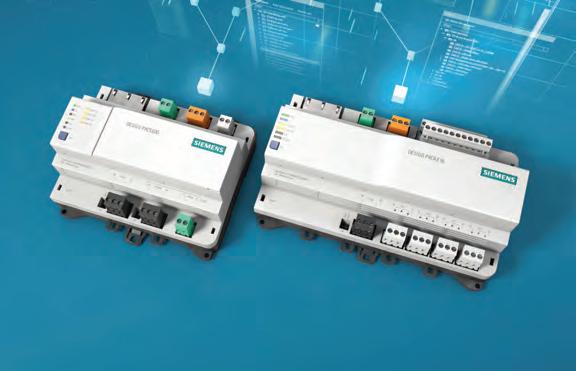
Siemens Smart Infrastructure says its new building automation controllers, Desigo PXC4 and PXC5, transform buildings into high-performing, energy efficient assets.
The controllers offer a wide range of benefits for automating small and medium-sized buildings to get the most flexible and scalable building automation.
With a licence-free Desigo Engineering Framework, devices can now be seamlessly integrated in the same framework for intuitive engineering. Features such as open by design for successful integration of different protocols and easy wireless access facilitate building automation. Both controllers were designed to expand and strengthen the Desigo portfolio and focus on one specific automation element - the Desigo PXC4 for HVAC plants and Desigo PXC5 for system functions and integration.
The new controllers were simultaneously released with the Desigo Engineering Framework, which consists of the HIT Portal, a web-based planning and selection tool; the engineering and commissioning tool ABT Site for PC users and the commissioning tool ‘ABT Go’ app for mobile use. The framework doesn’t require a license and can support the building throughout its entire lifecycle.
With a wide number of preconfigured functions as well as program blocks and various example sites, the engineering tool ABT Site offers simplified programming to highly reduce engineering complexity. Thanks to the open by design approach, multiple protocols can be integrated and mixed easily. With this setup, projects can now be processed easier, faster and more reliably – on- site or remotely.
ONLINE ENQUIRY 136
Radio network for testbed project
MMX Communications Services, a telecoms systems integrator, has developed in partnership with Siemens, an ultra-high frequency (UHF) radio network for the Smart Energy Network Demonstrator (SEND), based at Keele University, UK.
SEND is Europe’s largest testbed for the research and development (R&D) of renewable and smart energy technologies. Keele University, with Siemens, has created a centrally controlled, self-healing energy micro-grid across the campus. Integrating electricity, gas and heat, this smart energy network has helped Keele reduce carbon emissions by 4,000 tonnes and save £2m in energy costs per annum. The project involved the digitalisation of 24 substations, the installation of over 1,500 smart meters, 500 home controllers and a 5MW renewable integration package.
The UHF network is central to the activity at SEND, allowing the energy research and business community at the ‘at-scale living laboratory’ to collect, analyse and utilise energy data with the aim of developing technologies to reduce emissions and increase energy efficiency. ONLINE ENQUIRY 138
Managing student accommodation
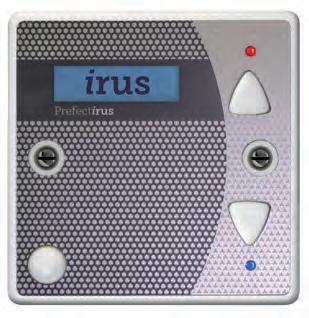
Automation can make a huge difference to the energy budget of student accommodation.
If all students were diligent and turned their heating off when they left their room, unnecessary use of energy would not be a problem. PIR sensors are used for this purpose but they are often set to activate when the occupant returns, rather than focussing on saving energy.
Prefect Controls’ Irus automated energy management system is designed for student accommodation using PIR. A node in each room monitors temperature, humidity, light, and decibels. Managers access data on the web-based portal and set maximum temperature and time profiles for boost, setback and frost modes in individual rooms.
The PIR sensor on the room node can be set to presence or absence detection. Presence detects an occupant entering the room and activates a programme to bring the room to a comfortable temperature. This is very convenient for the person in the room - but not so great for those paying the energy bill.
Switching the PIR to absence detection makes a lot more sense. This way, on entering the room the student needs to press the button to activate the boost mode, which will run for a pre-determined time period before reverting to the setback mode.
Should they leave their room shortly after pressing the button though, the control unit’s PIR will notice the room is empty and cut short the boost programme, thus not heating an empty room.
If we conservatively estimate that 30 minutes of unnecessary heating is avoided in this scenario, and then multiply that for a 1,000-bedroom facility, the numbers equate to almost 21 days of preventable heating. Consider that in terms of annual use and it becomes clear how automating a heating system with Irus can make savings of 40 per cent. ONLINE ENQUIRY 137
Gateway eases device integration
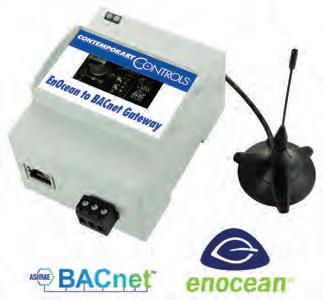
Contemporary Controls’ EnOcean to BACnet gateway makes it easy to integrate EnOcean devices into BACnet networks. The gateway allows users to discover and select EnOcean devices on their network. The gateway will then create new virtual BACnet devices for the BACnet network. These virtual devices will have the appropriate BACnet objects.
The process begins by selecting the appropriate EnOcean Equipment Profile (EEP) for the EnOcean device. This provides the gateway enough information to know which objects to create for this virtual BACnet device and how to map the received data to these objects. This virtual device will have the properties of the device contained in its BACnet objects and will update this data whenever the device transmits new data. As more devices are added to the gateway, more virtual BACnet devices will be created. All these exist on their own virtual network. This allows head-ends to easily discover these devices and receive the data via BACnet.
Will Darby is managing director of Carlo Gavazzi UK
Smart Buildings
For further information on Carlo Gavazzi UK visitwww.eibi.co.uk/enquiriesand enter ENQUIRY No. 128
Distance learning
Will Darby looks at how the Internet of Things is accelerating the use of new technology beyond the traditional building management and energy management systems
BMS and EMS systems have been used to control the day-to-day operations of a building, such as ventilation, lighting and comfort control for decades. But for every pound spent on energy, a business could be spending 10 times that amount on leasing office space and 100 times that on employees. Using space more efficiently and increasing employee productivity are likely to have a bigger impact on reducing a business’ energy use and increase its profitability.
Now, an ever-increasing number of Internet of Things (IoT) devices are making workplaces, homes, campuses and even towns smarter and more energy efficient by improving utilisation, reducing costs, predicting maintenance needs and increasing the reliability of energy assets. A building that in the past would have had a few strategically positioned BMS sensors, can now have hundreds of low-cost, network-connected sensors throughout, all of which will continuously collect data.
To be of use, however, this data must be meticulously collected and analysed. There is a variety of different ways in which data can be collected. Which is the best will depend on the number of devices connected and the area over which they are distributed.
Data collection is relatively easy if all meters and sensors are located relatively close together so that the wireless transmission of data can be achieved using Bluetooth,
ZigBee or WiFi, for example. All of these systems are economic to run and can transmit large amounts of data over short distances without the need for cabling. This means that there is minimal cost for cabling while installation is straightforward, particularly for retrofit applications.
If, however, the IoT devices are located remotely or are spread over a large area, such as a campus or
There is a variety of different ways data can be collected. Which is the best depends on the number of devices connected
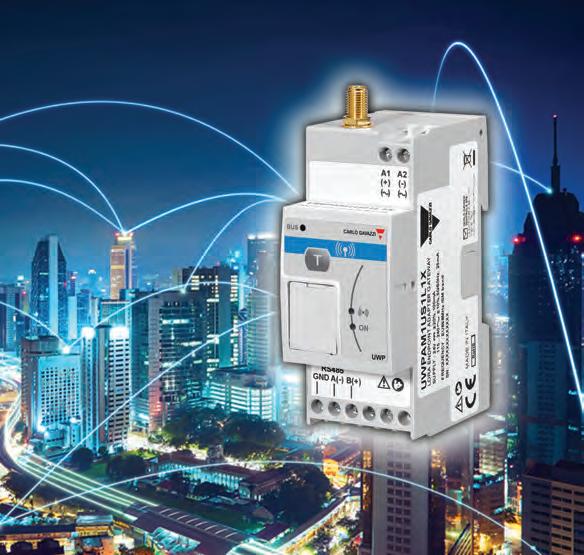
manufacturing site, then cellular technologies such as 3G, 4G and 5G could be used to transmit the data over the increased distance. They could even transmit the data internationally. Unfortunately, this solution is relatively costly to set up and maintain because it requires a mobile phone contract and SIM for each measurement point if they are to connect to the cellular network.
Cost-effective alternative A more cost-effective alternative to collect data from IoT devices located over a large area is to use a Low Power Wide Area network (LPWAN). These work by ensuring IoT devices send only small packets of data (up to 50kbit/s) periodically or infrequently over networks spanning many kilometres.
LoRa is the most common long range, low power technology. The LoRa Alliance is an open, non-profit association formed to promote the adoption of this technology. In Europe, LoRa uses the licence-free radio frequency band at 868 MHz to transmit data.
LoRaWAN is the network on which LoRa operates. The network architecture deployed is a star topology, in which gateways relay messages between end devices and a central network server. Communication between the IoT device and gateway is bidirectional.
If, say, an energy manager wants to connect numerous meter devices dispersed over a large campus, for example, with minimal wiring and installation costs. If the manager were to opt for a traditional wireless solution, such as WiFi, this would be unable to operate over the area of the campus without the deployment of numerous wireless repeater stations to take the signal and to re-broadcast it.
Carlo Gavazzi’s solution is to use its UWP-A Long Range Wireless Endpoint Adaptor to convert each meter into a long range wireless endpoint. The UWP-A’s ease of installation, without the need for repeaters even over a long range, and the plug-and-play connection to Carlo Gavazzi’s meters make set up easy for installers and system integrators.
The UWP-A can transmit measured data to the UWP-M gateway using LoRa technology. The UWP A and UWP M embed end-to-end data encryption to ensure data is secure. The UWP-M acts as a gateway for numerous UWP-A devices. It connects to the Carlo Gavazzi UWP 3.0 platform which acts as a data concentrator to provide the data to the system servers. The UWP 3.0’s Web-App allows users to check data and to generate reports.
By working in the license-free EU 868MHz band, the UWP-A allows installers to set-up a secure wireless network from scratch to cover an industrial facility, a shopping mall or a big building.
Where an existing LoRaWAN network already exists, in a smart city for example, connection is even easier: all a systems integrator has to do is to use a Carlo Gavazzi UWP-A end point adaptor to convert a Carlo Gavazzi meter into an LoRaWAN enabled unit. This simple solution allows system integrators to deploy a monitoring solution using standard LoRaWAN gateways via an existing LoRaWAN system and also to join public Smart-City networks for large-scale deployments of energy efficiency monitoring systems.
Whenever a project is focused on sub-metering and cost allocation in large buildings, industry, farms and cities, Carlo Gavazzi’s LoRaWAN systems offer a cost effective, secure and robust wireless network solution, without the expense of the SIM card, signal repeater devices and removing the need for cabling.
Humidification
For further information on CAREL visitwww.eibi.co.uk/enquiriesand enter ENQUIRY No. 130
Get in the healthy zone
What are the best conditions for people to work in? Pasquale DeMitrio looks at buildings, people, pathogens and minimising the spread of COVID-19
Sports announcers will commonly state that the athlete was really in a ‘zone’ during times of success. What does that mean when an athlete is in the ‘zone?’ The ‘zone’ is a place of optimal peak performance. Perfectly synchronized. Everything seems to come together and work out perfectly when in that zone.
With regards indoor air quality, what can it mean to be in that zone? How do we find that optimal performance? That perfect zone? Where everything just comes together and works perfectly for optimal performance. Well, with regards to healthy indoor conditions,
In the zone: our buildings have to match top performance to keep us all healthy
that perfect zone is when the indoor relative humidity is kept between 40-60 per cent! That is what getting in the zone means to us.
Get into the healthy zone that brings out optimal performance.
So let’s take a look at what that really means. What is the
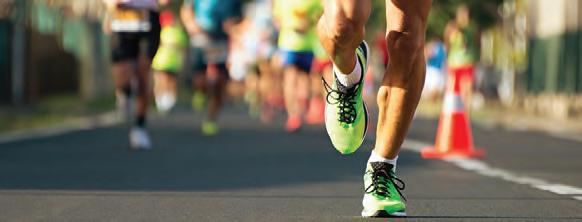
significance of this healthy zone?
There are three core reasons that 40-60 per cent indoor relative humidity is optimal.
Protection from pathogens One of the biggest reasons this is the optimal healthy zone is that the human immune system is optimised when the relative humidity is between 40-60 per cent. What occurs during this time in the human body is our nasal passages, throat and lungs are all properly protected from the attack of pathogens. The mucosa, or protective fluid that protects our interior tissue, is at an ideal viscosity. It allows the cleansing of particles to happen properly. When this part of the immune system is working, the bacteria cannot penetrate our tissue and wreak havoc on our bodies. As we breathe in, the pathogens are correctly processed and killed off before they can duplicate and spread.
Many of our buildings are kept way below this optimal zone, especially during the colder and winter months. It is common to find buildings at 20 per cent RH and lower during these months. Exactly the opposite of what is
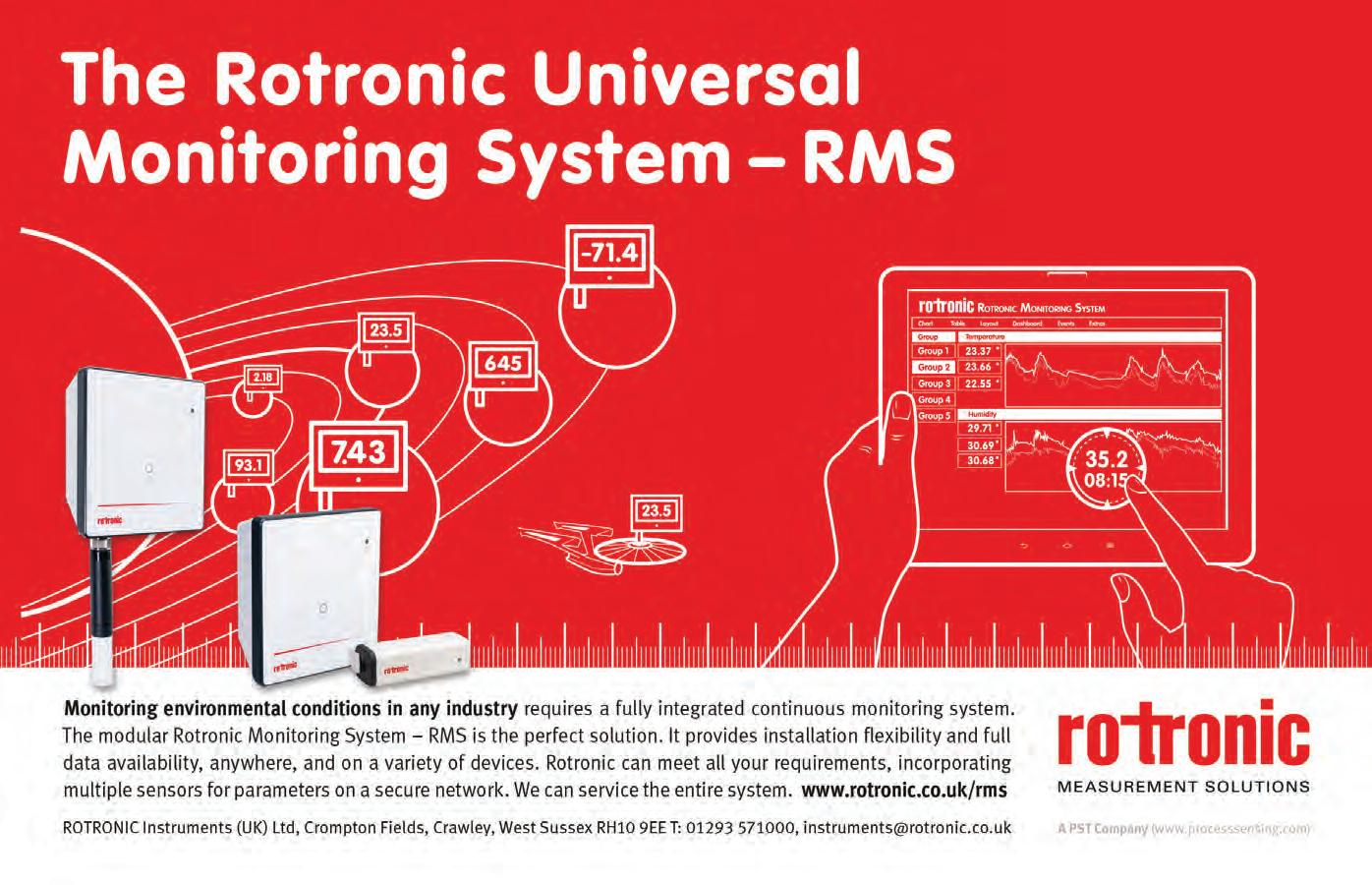
Pasquale DeMitrio is head of sales - North America, CAREL USA
mentioned above happens to our this healthy zone will help reduce respiratory immune system. Due to the ability of pathogens to travel the low humidity levels, we become further and longer distances. very vulnerable to infection. The Now think about when the RH mucosa becomes coarse and stiff, per cent is low and how that opens and allows pathogens to take hold up the door for further spread of and penetrate our body tissue. This infections. These particles become will lead to infections and illness. light, airy, and very buoyant. They Not exactly the healthy zone we are can float for hours, days, weeks, looking for. and even re-contaminate areas
The second key reason for this that were previously cleaned. The healthy zone is the route of travel recent example of COVID-19 has for pathogens is minimised. As the really brought this to light. The humidity level is kept between entire world is wearing masks 40-60 per cent RH, the particles over their faces to prevent the in the air become heavier and less Low humidity levels can lead us to become buoyant. They can dehydrated and pathogens can take hold travel only short distances and settle out quickly. Once they settle out on surfaces, it is much easier to clean up and prevent further spread. Staying in
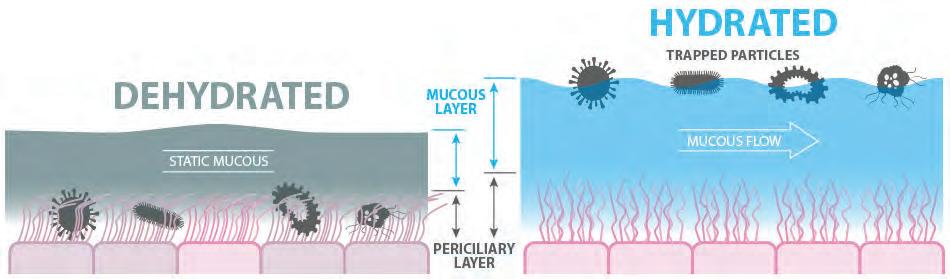
inhalation of aerosols containing the virus. Through the winter months, when indoor humidity is low, that is when we see an annual increase in flu and other viruses, including COVID-19.
Thirdly, we have to look at how viruses respond to different humidity levels. In 2014, the US-based National Institute for Occupational Safety and Health (NIOSH) published a study looking at the flu virus (Noti, et al). It found that the infectivity of the flu virus was reduced by 85 per cent once the RH level reached 40 per cent. The study also looked at lower levels of humidity and the virus thrived at 30 per cent and below. Once again, this healthy zone of 40-60 per cent RH is creating a difficult environment for viruses to thrive. Reducing the infectivity of the flu, and potentially other viruses, including COVID-19, would certainly qualify as optimal peak performance.
Considering what it means to be in the zone, there is a perfect area that protects our immune system. Which also happens to be the same zone that makes it very difficult for pathogens to travel around. And, it’s the same zone that reduces the actual infectivity of viruses. If we are looking for perfectly synchronised events to call the zone for indoor air quality, we found it. Monitor and control indoor RH per cent to between 40- 60 per cent and your building will be in the zone.

Humidification
For further information on Humidity Solutions visitwww.eibi.co.uk/enquiriesand enter ENQUIRY No. 140
John Barker is managing director at Humidity Solutions
Towards a stable environment
Close control of humidity is crucial in the manufacture and development of lithium-ion batteries. John Barker looks at the solutions available to make the process safe and reliable
Lithium battery technology is changing all the time, and in quite dramatic ways. New materials and chemical reactions are being tested every day, to reduce costs and meet ever-growing demand. But to be carried out efficiently and safely, it’s important that these tests are done in specially designed, ultra-low humidity dry rooms. This is primarily because of the chemical reactions that can happen if conditions are not met.
With batteries, you have chemical components like lithium-ion, lithium iron phosphate, graphene. These chemicals need a stable environment with less than 1 per cent humidity, as they are highly sensitive to moisture.
A reaction between lithium and water is exothermic, which means it generates heat, and produces a substance called lithium hydroxide, along with hydrogen. The heat from that reaction can, if left unchecked, potentially lead to burning or an explosion. To minimise this risk manufacturers need to keep the water content in the air to a minimum at all times.
As well as the safety concerns, keeping air moisture levels low is necessary to help achieve high levels of product yield, better quality control, energy efficiency, cycle life and even end storage capacity for every battery produced.
When we look at this kind of installation ‘known as a dry room’, the applications are actually much wider than just lithium batteries.
With the advent of consumer electronics, electric vehicles, solar power and grid storage applications, there is a huge variety of battery production processes, each using a unique chemical process and needing its own environmental controls.
This means that as well as the chemistry side of things, a lot of other things factor in to deciding what the dehumidification capacity needed for a dry room. The dehumidification system must be custom designed with enough drying capacity to maintain the dry room at the specified condition. Most battery manufacturers require a room’s humidity/average moisture level to be maintained as low as -40°C dew point (0.5 per cent relative humidity at 22°C) and sometimes even lower. Some of the factors that need to be taken into account include: • dry room size; • type of chemistry and process; • moisture infiltration; • personnel activity within the room; and • airlocks for material and personnel movement.
And that’s just the beginning. All of that means that it is very difficult to find a single solution that can address all of these issues, falls within budget and is reliable enough to stand up to the rigorous safety standards required by the industry. Specialist advice is clearly required to ensure you design and install the correct system for your facility.
Humidity Solutions is able to
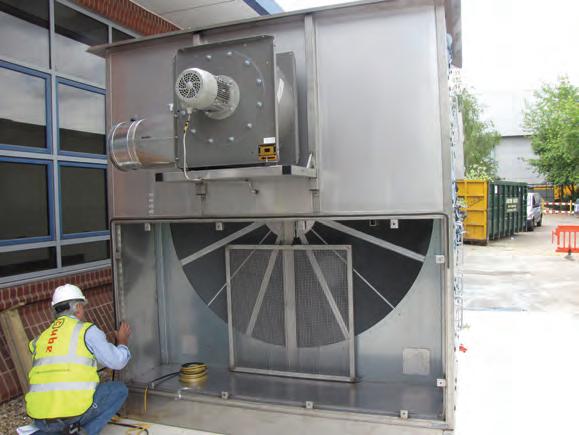
design and deliver bespoke humidity control systems due to strategic distribution partnerships with dehumidification specialists around the world who can address every unique project without having to buy multiple systems from multiple places. One such example is the solution provided by Cotes, the Danish dehumidification equipment manufacturer, to Nexeon in the UK.
A UK expert on silicon materials for batteries, Nexeon has been working to bring ground-breaking silicon anodes to market for the next generation of lithium-ion batteries. The company has patented a new way of structuring and etching silicon for use in such anodes, resulting in extended cycle life and a significant increase in battery capacity.
Commercial-scale facility The Nexeon pilot plant is configured to represent a commercialscale manufacturing facility. An advanced technology dry room is crucial for this capability because moisture dramatically reduces the performance of the electrolyte. It is essential that the levels of moisture in the air are kept as low as possible.
According to Nexeon, one of the biggest practical challenges
A large-capacity dehumidifier ensures that manufacturers of batteries keep water content in the air to a minimum
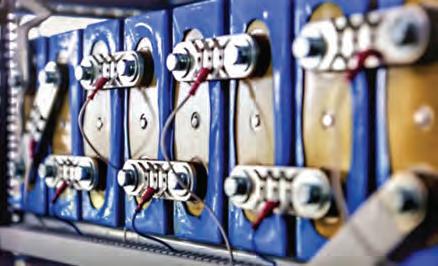
of the process lies in the moisture introduced by the unusually many visitors to this new facility. Moisture from their bodies has a relatively big effect on the very low humidity levels in the dry room.
Nexeon opened a fully automated pilot plant for silicon anode production in 2010. The site was set up based around a manufacturing dry room delivered by Scientific Climate Systems Ltd. The site was equipped with a Cotes CRP40000 adsorption dehumidification system, configured to remove unwanted moisture from 13,000m 3 of air per hour.
The dry room and the CRP40000 dehumidifier — installed outdoors in a corrosion-resistant AISI 304 stainless steel cabinet — were commissioned during torrential downpours in summer 2010. Nevertheless, the new installation met or exceeded all the required specifications, and achieved an exceptionally low -74.5°C dew point.
According to Nexeon’s engineering and operations director, Ian McDonald, the Cotes CRP40000 adsorption dehumidifier makes it possible to maintain the required dew point and to quickly return humidity to the desired -60°C level, minimising fluctuations after visitors have exited.
This large-capacity dehumidifier unit was specially configured to comply with Nexeon requirements, with a focus on minimising energy consumption.
The CRP40000 dehumidifier was therefore fitted with an indirect gasfired regeneration heater to dry the air, and an unusually large proportion of the dry air is recycled.
Also, a pre-cooling system was fitted to help avoid any extra energy consumption caused by temperature fluctuations and other variations in operating conditions.
Humidification
For further information on products and services visit www.eibi.co.uk/ enquiries and enter the appropriate online enquiry number
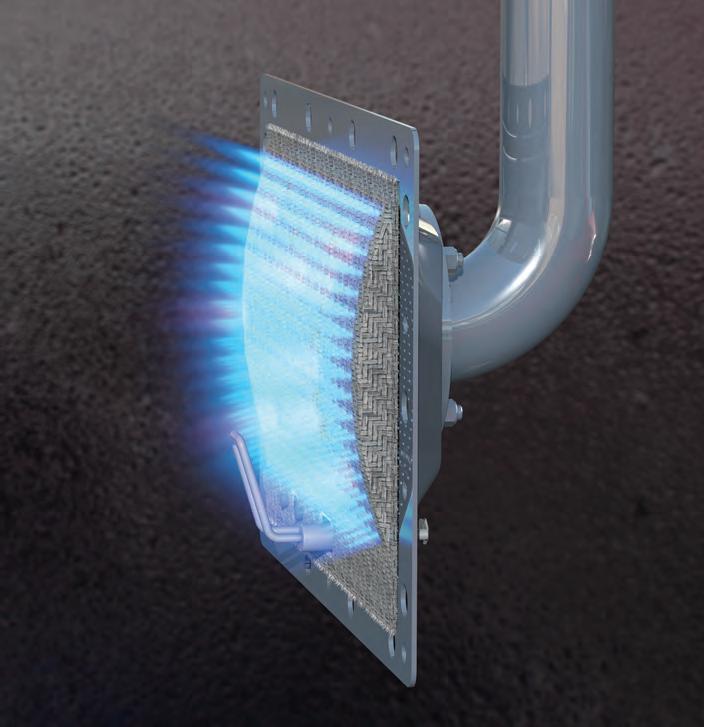
Healthcare website from humidity specialist
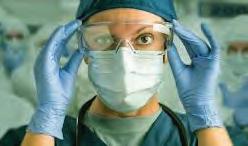
CAREL is highlighting its knowledge and experience in indoor air quality with the launch of a new website devoted entirely to healthcare.
“Our goal is help spread awareness on the positive relationship between relative humidity control and people’s health,” commented Stefano Ruzzon, group head of sales, HVAC projects and dealers. “Through this new website, we intend to disseminate knowledge that contributes to the creation of healthy environments, with the aim of preventing infections, increasing productivity and ensuring the comfort of patients and staff”.
With three different sections, the site highlights the close relationship between relative humidity control and air quality, and consequently personal well-being. The site features both technical diagrams and more descriptive contents, so as to provide a broad overview of the topic and make it more readily accessible to different readers. Specific documents are also available, such as white papers and success stories.
Indoor air quality, being a critical element in people’s health and well-being, has always been at the centre of CAREL’s attention. Indeed the company has acquired significant expertise in this area, the result of its extensive experience in air conditioning, air handling and humidification, as well as its participation at specialist conferences and seminars and synergies with international networks aimed at disseminating and advancing knowledge.
“The healthcare website is designed primarily for consultants who need a reliable educational tool before identifying solutions for healthcare facilities that are highly efficient and easy to install and maintain,” Ruzzon added. “At the same time, however, we hope that this site can also be a useful tool for end users, a source of valuable information regarding the impact of relative humidity on how healthy their work environment is”. • https://healthcare.carel.com ONLINE ENQUIRY 146
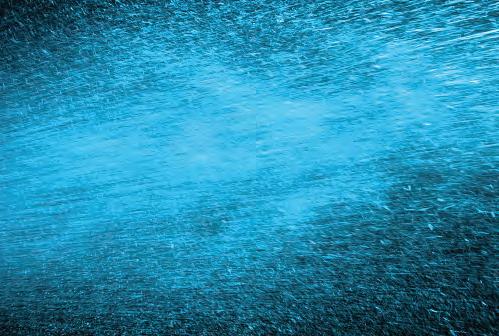
CONDAIR GS
New condensing gas-fired steam humidifier
The new Condair GS provides hygienic steam humidification at a third of the energy cost of electric steam humidifiers.
Its condensing technology uses heat from the exhaust gases to pre-heat the incoming water. This saves energy and reduces flue gas temperatures, allowing for economic plastic rather than stainless steel flues.
Discover more about the Condair GS
www.condair.co.uk/GS T: +44 (0)1903 850 200