
25 minute read
Outdoor Living
heating & ventilation Rinnai To Create Hydrogen Information Hub For Consultants, Specifiers, End-Users
Rinnai, manufacturers of hot water heating units and delivery systems for all commercial sites, is to create a comprehensive information hub dedicated to the subject of Hydrogen as a low-carbon energy for the future.
Advertisement
T
he Rinnai Hydrogen Information Hub will be aimed at building services consultants, engineers, specifiers and endusers. It will be online and include webinars plus all requested digital or onsite meetings. ‘Rinnai welcomes the UK government’s recent ‘Ten Point Plan’, in particular the drive to decarbonisation through the use of Hydrogen. Heating emissions are a huge issue and Hydrogen is one answer to the Energy Trilemma, as we have stated several times,’ says Rinnai’s Chris Goggin who is also a board member of the ICOM Energy Association. ‘Hydrogen in the domestic setting is seeing up to £500 million government funding on trials for homes using hydrogen, starting with a Hydrogen Neighbourhood in 2023, moving to a Hydrogen Village by 2025, with an aim for a Hydrogen Town – equivalent to tens of thousands of homes – before the end of the decade. Of this funding, £240 million will be for hydrogen production facilities. Rinnai has made data and information contributions and

had close consultations with the lead research agency primed with advising the UK Government. The UK, along with many other countries, faces an Energy Trilemma - the pressing need for de-carbonisation, which means a shift in energy pathways; security and longevity of supply; long term affordability to the industrial and end-consumer.
This country’s housing stock is over 24 million units and the UK had a total energy consumption increase by 1.1 per cent in 2018 to reach 143 million tonnes of oil equivalent (mtoe), the highest level since 2013.
Says Chris Goggin for Rinnai, “All questions and queries on the growing consensus on the suitability of Hydrogen as the replacement for all fossil-fuels will be answered by the Hub. Zero Carbon cannot be achieved via Zero Information on the strategies needed to achieve the goal”. “Hydrogen can make a major contribution to decarbonising the UK energy grid, whilst also providing a sustainable answer to the political and societal questions of the Energy Trilemma,” says Chris Goggin. The distribution of Hydrogen creates a resolution to the Trilemma questions and the very necessary decarbonisation of the UK energy grid. Hydrogen can be potentially combusted through existing ‘in situ’ appliances, complete with smart controls and cost-effective hardware & software upgrades as demonstrated by proprietary technology in hot water heating units. Many countries in Europe and Asia are using the post-pandemic economic regeneration plans to instigate plans to switch to hydrogen as the main fuel source for housing, industry and transport. France has recently announced a €7 billion package to build a carbon-free hydrogen industry and Germany has allocated €9 billion.
In the summer the European Commission stated it wanted to increase its production capacity of electrolysers from 250MW today to 40GW in 2030. Similar strategies have been released by the UK, Australia, and Asian countries. These moves are clear trends to massive public investments in the sector.
Hydrogen is already ‘cost competitive’ in niche applications, according to recent research, with the forecast that it is likely to at least price-match industrial-scale alternatives in less than a decade.
Rinnai is a true global player in the manufacture of domestic and commercial appliances and operates in almost 50 countries. Rinnai is the world’s leading manufacturer of continuous flow hot water systems - it makes and sells 2 million units each year. The range of units can be manifolded to supply, limitless hot water to any site of any size. This means fast, efficient, temperature-controlled water on demand at the point of delivery – kitchens, showers, accommodation blocks, bathrooms, washrooms - and less space spent on plant rooms with no or little maintenance as all units are proven to be robust with a long, long working life.
Call 01928 531 870 or email engineer@rinnaiuk.com or sales@rinnaiuk.com alternatively use the smart online contact points “Help Me Choose” or “Ask Us a Question”, all held on the website homepage at www.rinnaiuk.com
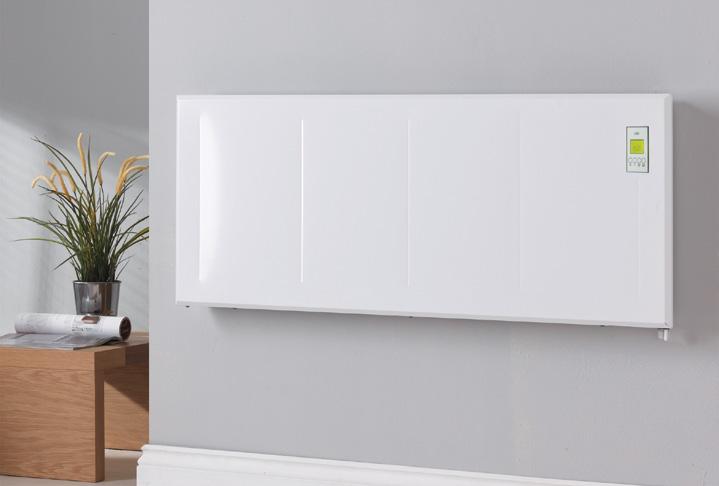
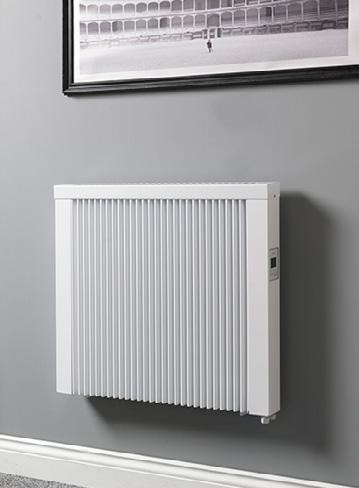
Hybrid Heating for the modern home – the choice is yours
EHC offer a comprehensive Range of Electric Products that are all controlled by the well-established DSR Technology Control System. It enables you to select a Hybrid Heating Solution from the range for the various rooms within your property to suit your design style and budget – the choice is yours.
All DSR Controlled Heaters are manually operated using the “easy to use” Controller located on the Heater. They also have Wi-Fi capability that can be activated when you purchase the optional DSR Smart Gateway which will allow you to control your Heaters Anytime, Anywhere 24/7 up to a maximum of 30 Heaters using our free bespoke APP.
When used with the EHC Smart Gateway you can take advantage of the in-built Wi-Fi ready capability and are able to program your heaters individually or in groups. The DSR Control APP has many features designed to enhance your comfort levels and provide essential information regarding your heating system. There is also an optional Power Meter Clamp available for Load Shedding Control.
Popular features within the APP
• Setting Times to suit lifestyle • Adjust each room temperature to suit using the manual boost • Limit electricity consumption to avoid exceeding maximum power available • Monitor your electricity consumption history • View the Temperature history by room • Alexa and Google Home commands The DSR Range of Heaters all offer partial heat retention via the internal storage tiles. They are designed to provide an even heat across the surface area of the Heaters and in turn provide a combination of Convected and Radiant Heat. The comprehensive range of Heaters which are available in various Outputs are:
• EHC Combination Heaters
• Edge
• Solaris
• Visage
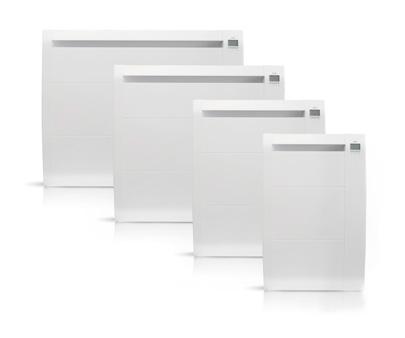
For further information or a free Brochure contact 01698 820533 or visit www.electric-heatingcompany.co.uk

heating & Ventilation A useful app for homeowners and installers to visualise a free-standing stove installation
Have you ever wondered what a modern, log burning stove would look like in your house, especially as you don’t already have a natural chimney breast for a fireplace?

T
his App allows the user to see what it looks like, as well as calculating the components required. Stoves can easily be installed into existing homes, be it a newly built house on an estate or an existing, older house or even a self-build project. A stove can be installed going through the ceilings of each room and out of the roof, or along the outside and up the building.
The App gives you a choice of four basic stove designs, to give an impression of what a typical design would look like in your home. This amazing App then be used to assist the installer in selecting the parts required following a full site survey, which can then be ordered directly from their chosen distributor of the Schiedel product range.
Please note that as conditions on site may vary, the final price for the system may change following the full site survey and may vary between distributors.
Please note that the installer may advise on additional components or advise which components are not needed (for example extra wall bands based on exact measurements and site surveys). The quote provided is Schiedel’s list pricing and these prices are different with their distributors, who can also provide some amazing discounts.
FAQs
What sort of phone can be used?
A modern phone from the last few years should be okay to run the augmented reality part of the Builder. However, the recommended spec is for a device running Android 7.0 and iOS 11. The relevant app stores will advise if this can be installed.
How accurate is this?
The accuracy will depend on the information and dimensions fed into the app but should always be followed up by a full site survey carried out by an experienced installer. Schiedel recommends HETAS accredited installers for solid fuel installations. Don’t worry. Enter the approximate values and we can calculate the components. Your installer or Schiedel’s technical support team can verify if the set of components are accurate for the installation.
The pipe lengths are different.
This is because it is not recommended to have a joint within a ceiling or a wall. However, this can be assessed when on site or can be discussed with our technical team.
Some of the options are missing if I choose internal or external.
That’s correct, some measurements aren’t needed, plus some options are not available when choosing one of the other options. If you have an installation which is different to the standard ones, then fill in the details for the closest installation type and put information in the notes section for our technical team to look at.
www.schiedel.com/uk/ augmented-reality-chimneybuilder-for-stoves/
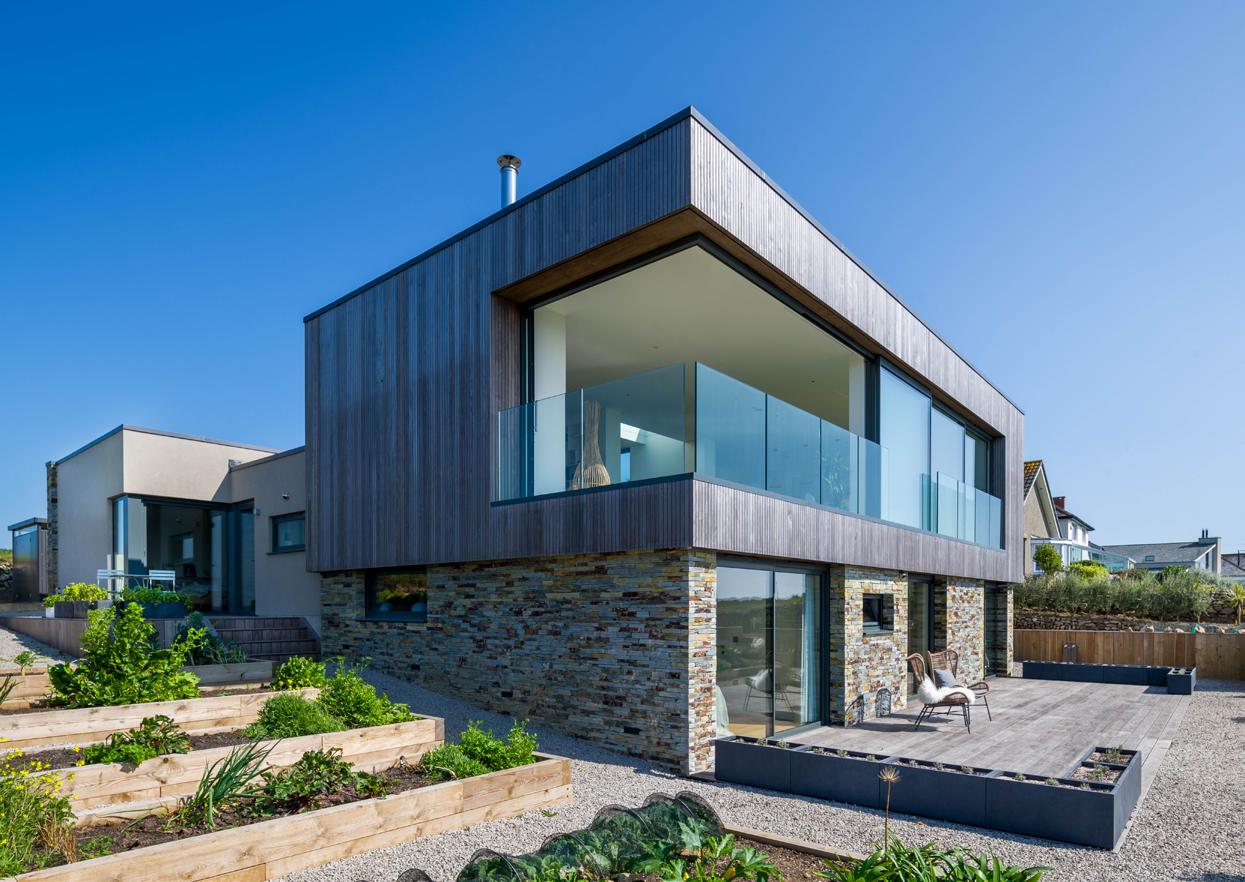
Situated on the picturesque coast of Cornwall in South West England, the recently completed family home, dubbed the Stone House offers unparalleled sea views and a unique view of historic castle, St Michael’s Mount. Designed and brought to life by the combined efforts of Suzanne Brewer Architects and Lilly Lewarne Architects, Kebony, a global leader in the production of sustainable modified wood, was used to clad the exterior of this contemporary building, creating a beautiful natural mix of both wood and stone.
The homeowner’s dream was brought to life earlier this year; Suzanne Brewer Architects, guided the project through a successful planning permission, whilst Lilly Lewarne Architects was the practice appointed to carry out the technical design and construction stages of this contemporary project by the sea. Stone and Kebony wood were the materials selected inside and out for their authenticity and the way in which they ‘wear in’ instead of ‘wearing out’, creating a rustic feel for the property which elegantly blends into the natural landscape of the Cornish hillside. Kebony’s enhanced durability, sustainable qualities and unique aesthetic made it the perfect choice of wood for this unique project. Developed in Norway, Kebony’s revolutionary technology is an environmentally friendly process which modifies sustainably sourced softwoods by heating
the wood with furfuryl alcohol - an agricultural by-product. By polymerising the wood’s cell wall, the softwoods permanently take on the attributes of tropical hardwood including high durability, hardness, and dimensional stability. Kebony’s uniquely natural aesthetic and sustainable credentials were perfectly suited to realise the ambition of the modern seaside family home. One of Stone House’s key selling points is its spectacular view of both the Atlantic Ocean and St Michael’s Mount, famed for its picturesque landscape and uniquely peaceful community feel, with only 30 islanders calling the village their home. Each morning the village springs to life with school children and workers gathering to travel to the mainland, goods being loaded onto the quayside and islanders preparing for the jobs the day will bring.

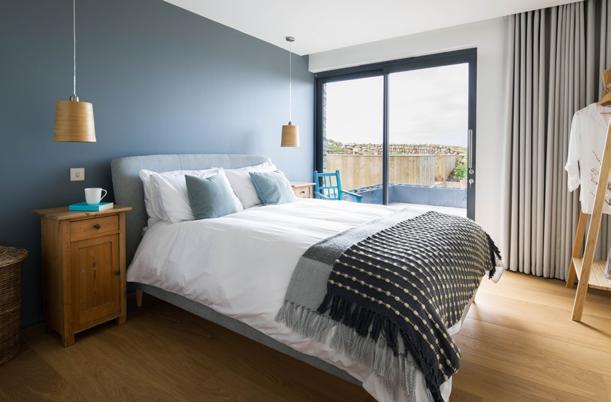
Rob Simmonds, Project Architect at Lilly Lewarne Architects commented: “We are very proud to have worked on the design and construction of this beautiful home on the south coast, which looks stunning within its natural surroundings. Working with Kebony wood was not only cost-effective but proved to be completely suited to the homeowner’s vision, and we certainly look forward to using the material again in future projects.” Nina Landbø, International Sales Manager Norway at Kebony added: “We are delighted that Kebony has played an important role in the development of this beautiful, rustic home in Cornwall. It is great to have made a longlasting mark on the unique British seaside town and we hope it inspires the development of many more natural, sustainable homes in the area, and across the globe.”
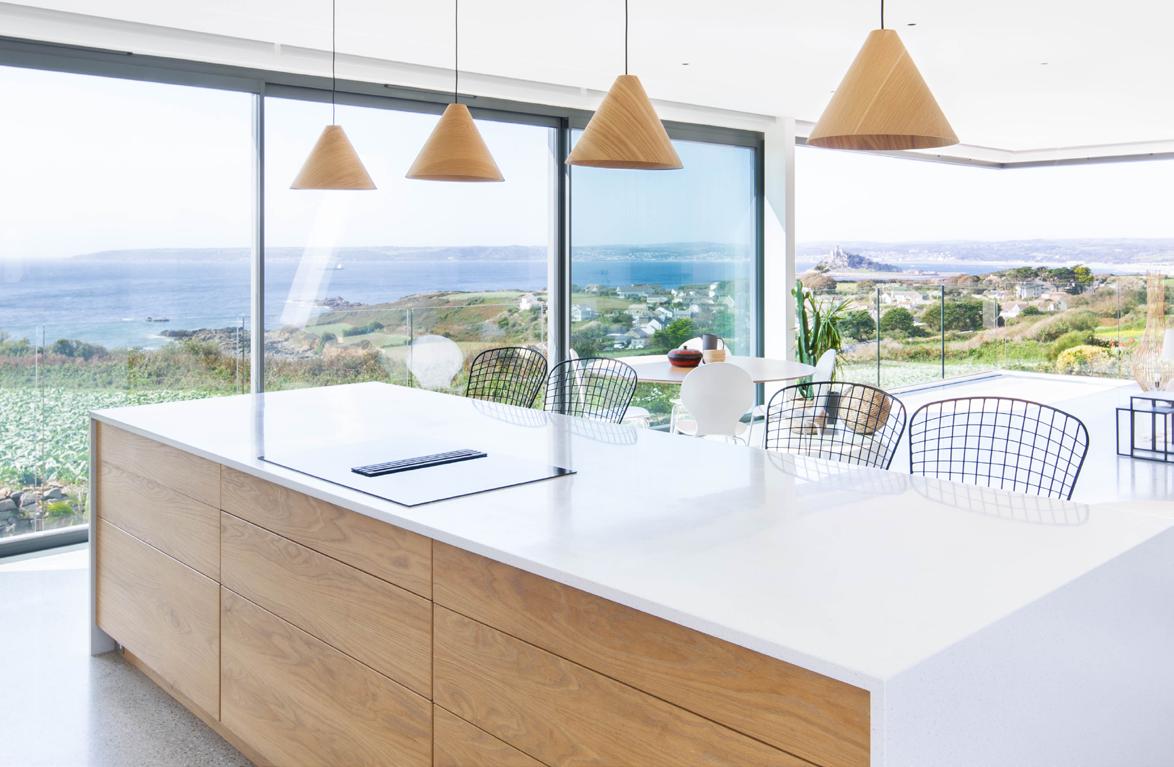
sustainability 2020 is SureCav’s most successful year to date
SureCav, an innovative brand of 100% recycled polypropylene backing membrane for masonry construction, announces 2020 as a record year for sales and enquiries.

T
he average growth in sales over the last 5 years is 15%. This has accelerated to an 18% average for Autumn/ Winter 2020. The forecast y/e figures for 31st January show EBITDA growth over 50% on the previous year.
These positive figures indicate an increasing appetite for the company’s two flagship products SureCav 25 and SureCav 50 as a focus on green construction in the specification and housebuilding sectors increases.
Forecasts for 2021/2022 are positive, indicating this upward trajectory will continue with a predicted increase of 20-30% and further potential of achieving a 100% increase in sales within two years.
Planning for Success Since its foundation, SureCav had previously seen steady growth and consistent interest in its product portfolio from traditional housebuilder and specifiers working within this sector.
However, last year saw the brand make considerable, sweeping investments to strengthen its position and extend its reach. This began with the launch of a new, more intuitive, and targeted website which gives a more incisive picture of the product. SureCav also signed-up to NBS’ powerful new construction product platform, NBS Source, which will position them front and centre with the whole of the British, Canadian, and Australian specifier audience. So unique are the brand’s products, a new, dedicated Uniclass code had to be developed when the portfolio was brought onto the system.
This was further followed by a renewed commitment to BBA (British Board of Agrément) with continual engagement to ensure accreditation.
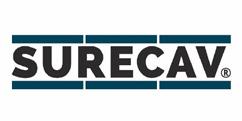
A New Broom
In the latter half of the year, SureCav signed a contract with a new manufacturer, the world-famous Hillbrush, one of the world’s leading producers of brushware and cleaning tools as well as experts in recycled plastics.
Based in Mere, Wiltshire, close to SureCav’s headquarters in Wincanton, Somerset, the new partnership will open up a host of new audiences for the brand, including a greater presence in emerging markets like the USA.
Brand new machinery and plant equipment will also improve efficiencies and ensure both SureCav 25 and SueCav 50 are made with as little environmental impact as possible. Little Black Book
In line with these new developments, SureCav has also grown its client base with new orders placed from across the housebuilding industry.
Commenting on the figures, and looking forward, founder and managing director, Charlie Ayers, says, “When you consider these results against the backdrop of an extremely challenging year, full of uncertainty, one cannot help but be positive. It seems that, with far more time available to consider alternative materials to meet the increasing number of sustainability briefs, fast becoming the norm across all construction projects, built environment professionals are discovering the benefits of SureCav.
“Significantly, once a specifier uses our product, they never go back to the original product it has replaced in the build. We expect this trend to continue and will, accordingly be ramping up sales and marketing activity alongside our new manufacturing partners, Hillbrush, to raise awareness of how SureCav not only improves your bottom line it also helps you do your bit for the environment.”
To find out more about SureCav and its portfolio of products click here.
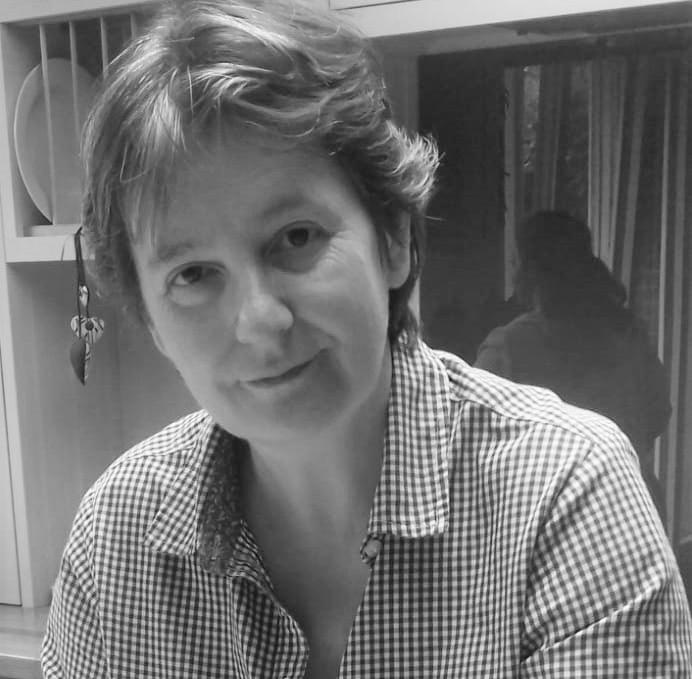
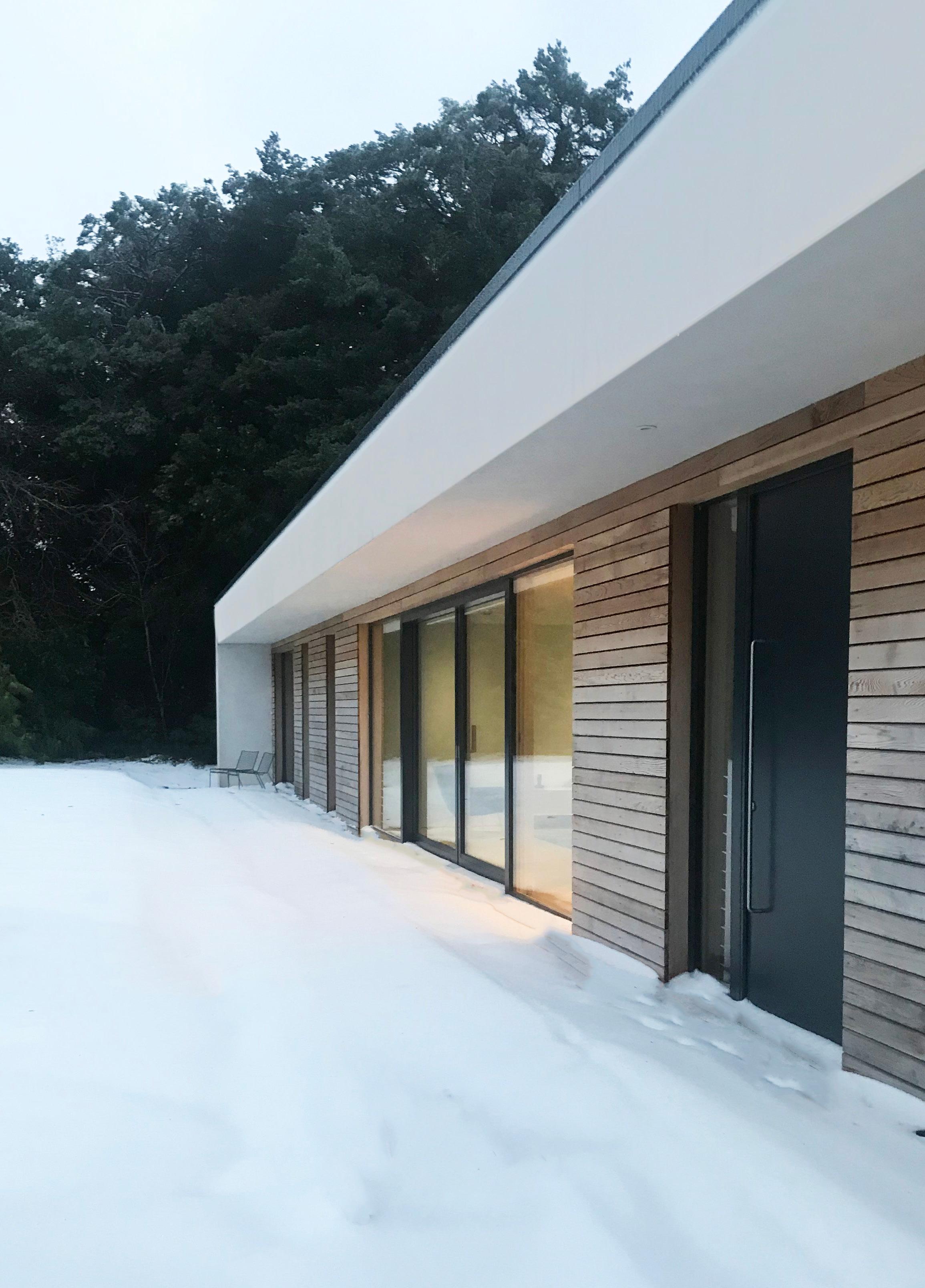


We asked eco-materials supplier Ecomerchant to pick some of the standout products from 2020 and asked if their popularity could be linked to current and proposed regulations.
Liquid applied airtight membranes first arrived in the UK around 5 years ago. The idea that an airtight membrane could be spray or brush applied was groundbreaking despite the use of similar means of application for protective coatings and waterproofing. Blowerproof was first introduced to the UK by Ecomerchant in early 2016. The product became BBA certified (the first to do so) in 2017 and was quickly picked up by the Passive House sector.
Over the past two years, liquid applied membranes have seen exceptional growth as the demand for airtight buildings increased. The ultimate application came in spring 2019 when the Imperial War Museum archive used Blowerproof to create the most airtight building in the UK (ACH 0.03) for storing its priceless archive of documents.
For the refurb sector, the use of liquid applied membranes is a game-changer. The water-based VOC free liquid can be applied to almost any surface even in the trickiest and most demanding applications it creates a permanent flexible layer which allows airtightness to be delivered where previously achieving high levels were nigh on impossible.
Wood fibre flexible batts and rigid carrier boards. Insulation is a key component of most retrofit projects and the increase in wood fibre use over the past few years has been steady - but the take up this year has been exceptional. Wood fibre is a versatile product, which offers desirable performance characteristics for new build and renovations. Being vapour permeable it helps buffer moisture, its density (up to 250Kg/m3) protects against overheating and its natural makeup alleviates concerns over synthetic ingredients, off gassing and poor indoor air quality. The flexible batts are popular for installation between studs and the dense rigid boards for carrying render or plaster either internally or externally on timber frames or direct to masonry or brick. Calcium silicate boards; the elimination of mould and subsequent reduction in health issues has driven sales of SkamoWall Board. The calcium silicate board is part of a system which includes adhesive, primer and plaster that combine to create a buffer to manage moisture, improve insulation and eliminate mould.
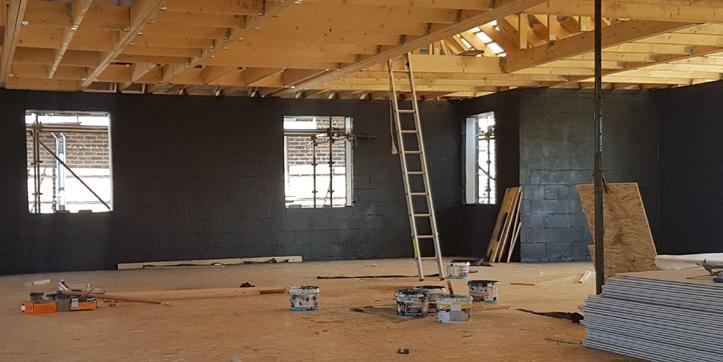
Blowerproof BBA certified liquid applied airtight membrane applied direct to blockwork prior to application of dot & dab plasterboard. An effective, simple and secure way to achieve passive levels of airtightness.
Steico Special Dry used as a roof sarking board on a Sussex Passive standard build. Building by Kithurst Builders using naturally insulated passive panels and Steico I joist roof. Airtightness materials Blowerproof and Pro Clima.
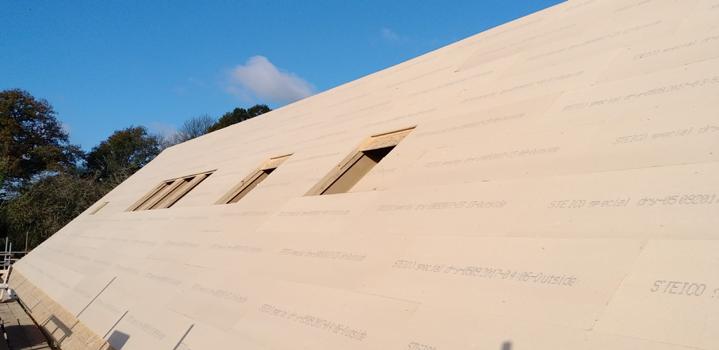
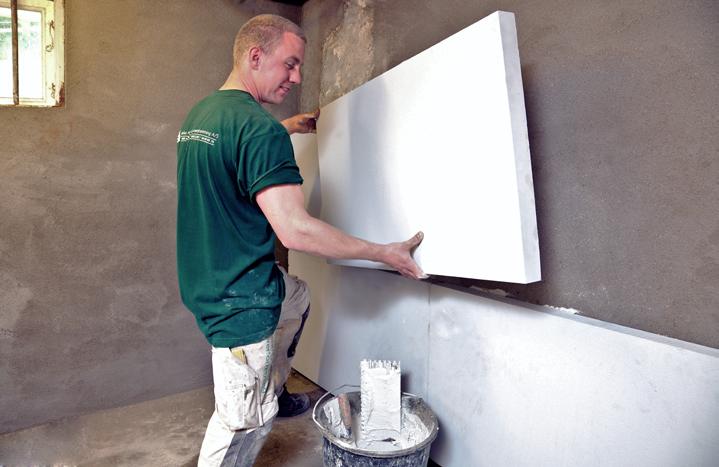
Skamowall Board calcium silicate board used to line a basement retrofit, Skamowlall board insulates and buffers moisture and prevents mould growth. System comprises Skamol fungicide (optional), adhesive and finishing plaster. The whole system is vapour open.
The board’s inert chemical structure renders it incapable of supporting mould growth. The improved insulation and breathability of the system allow ventilation to harmlessly remove moisture from the building. The plastered board acts as a vapour control layer whilst remaining breathable. The SkamoWall Board has been a favourite of landlords and owners of older buildings with solid walls where persistent problems often cause unwelcome maintenance costs and tenant complaints.
Education is a key specification tool
The use of these products is exclusively a matter of personal choice so why are they so popular? There are several answers but largely this is to do with how educated the buyer is about building features that are desired but not mandatory within building regulations. For non-developer new build this demand is clear and growing, driven by a client who include improved building performance and occupant health within the brief. For retrofit one reason may be the limits on design imposed where a significant uplift in performance can be achieved through upgrading the building fabric where options such as orientation, outward changes to shape or ‘look’ and modifying the footprint are not possible so forcing a more open approach to problem-solving. carbon, energy, moisture, ventilation and health in our housing stock. But they persist in partial and piecemeal solutions, apparently oblivious to the interactions between these problems and the need for a holistic approach. A change of attitude and major upskilling of the workforce, especially in refurbishment projects, is required to deliver effective solutions to the enormous backlog of remedial works required to deliver the healthy, comfortable and affordable homes that are essential if the UK is to meet its carbon targets.
Health matters
Since lockdown in March increased awareness of the way our buildings actually perform has been consequence of many of us spending more time at home, we have experienced how our buildings perform at times we would usually be absent i.e. during the day when we would otherwise have been at work. Increased focus on our health has broadened the interest and understanding of how building design and fabric can have a direct effect on our wellbeing, at the least this is shown as a precautionary approach to avoid known producers of toxins such as VOC’s or formaldehyde (prompted by the lockdown boom in home decorating and refurbishment) or on insufficient insulation or ventilation; at best our focus has shifted to including building health and indoor air quality (not mandated through building regulations) as part of what we need to demand from our homes and workplaces. On the subject of what is mandated and what is not 2020 is ending with a familiar scenario of promised changes and little real regulatory progress. The government has finally published plans for a new version of Approved Document L (for energy efficiency), a new F (for ventilation), and confirmed a new regulatory standard for managing summer overheating is on the cards. This consultation phase is still in progress.
These documents currently apply to new-build homes in England, but we can expect further publications to pick up on Welsh standards, non-domestic development and existing buildings. Notice that retrofit is still not a priority despite estimates that around 80% of the homes we will be occupying in 2050 already exist.
The UK GBBC report ‘Net Zero Carbon Buildings: A Framework Definition’ which was launched at the Houses of Parliament in April 2019 provides a framework on how to achieve net-zero carbon buildings in both construction and operation (in-use energy consumption), whilst beginning to provide direction for addressing whole life carbon in the industry. Again this projects well into the future with targets set for 2030 for new build but not until 2050 for existing buildings.
The much-vaunted PAS2035 (linked to the requirement to implement PAS2030) launched last summer is still not a mandatory requirement except for certain types of funded retrofit project, this excellent standard is advised rather than imposed so, therefore, is unable to deliver the intended improvements to existing homes at scale for the moment. Mandatory inclusion of PAS 2035 is currently scheduled from July 2021 for ECO (Energy Company Obligation) projects only.
We are yet to feel the full effects of the Hackitt review and to cap the year off nicely we still have an unresolved Brexit to muddy the waters and prolong inaction.
If we are to ‘build back better’ the connection between buildings that are low in embodied carbon, low energy users, that manage moisture through material choice and design, are healthy and nontoxic to the occupants and

PH15 System build Steico I joist construction, Vapourblock airtight racking board, Steico rigid woodfibre sheating, blown insulation cellulose or woodfibre.
durable, can be summed up by a requirement to simply build healthier buildings an ambition that is sadly lacking from almost all the current providers.
The housing crisis has not gone away
We still have a crisis within the housing sector to deal with and a lot of this is tied in with energy efficiency and energy use. The nature of the problem is neatly encapsulated by Richard Tibenham director of Greenlite Energy Assessors and associate lecturer of building physics at the University of Lincoln. Tibenham refers to The Committee on Climate Change report ‘UK Housing: Fit for the Future?’ which claims that emissions reductions from the UK’s 29m homes have stalled, while energy use in homes increased between 2016 and 2017. It further claims that we will not meet our legally binding targets for emissions reduction under the Paris Agreement without near-complete decarbonisation of the housing stock by 2050.
At present, there is no agreed solution to modify the built environment such that it can operate in a carbon-neutral fashion by 2050. The problem can be made substantially less dire, however, by not adding yet further energy demand at this critical time.
So whether it is carbon reduction in building operation, energy generation, design or materials choice we are facing the absolute need to decarbonise the sector, and this will need to be backed by mandatory regulations.
New build can rapidly become a retrofit problem.
Lord Deben Chair of the UK CCC sums this all up rather neatly saying “there are other influences on housing emissions. For example, there is the fact that the Government still have not raised the standards for new buildings. At the moment, we are building more trouble every year1” in essence poor standards for existing buildings just increases the size of the retrofit market. They condemn most of what we are building now to retrofitting in the future a frankly crazy notion when we are already faced with the challenge of upgrading the energy performance of the entire housing stock, it is nonsensical to be continuously making the problem worse by allowing new homes to be built that will also need to be
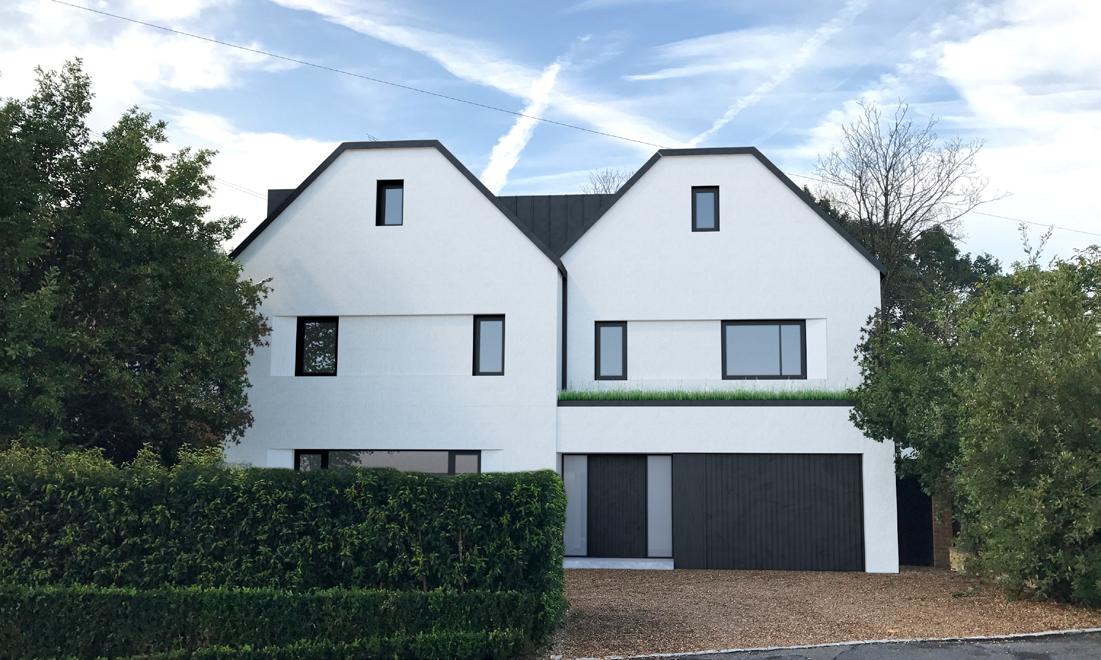
Beltane Drive Wimbledon: Architect Tim Gledstone Construction PH15 System from Passivhaus Homes Ltd. Energy/Carbon Target: Passivhaus PLUS or net zero operational carbon. PH15: Delivering best energy performance using low embodied, healthy, building materials. Materials Steico wood fibre insulation Steico I Joists, Unilin Vapourblock airtight racking board, Pro Clima airtight tapes.
retrofitted, which begs the question why not build better now especially if this is straightforward to achieve. This situation is made worse by the various ways in which the law allows buildings to be built to historic standards2 astoundingly Government data shows that 62 per cent of homes that Persimmon built in 2018 were to standards that pre-date the 2013 Building Regulations, as were 52 per cent of Taylor Wimpey’s and 47 per cent of Barratt’s. They are not alone as government data shows that 12 per cent of the new homes built in 2018 were rated EPC C, whilst 7 per cent were rated D or below3 .
So little remains in terms of positive regulatory drivers for the present. One option is to elect to use a voluntary standard such as The Passivhaus Institute developed ‘EnerPHit Certificate’ (a quality-approved energy retrofit with Passivhaus components). This certificate sets a slightly different standard requirement to the full Passivhaus standard. Each home and building is unique and poses specific problems and solutions to reduce carbon emissions, improve energy efficiency and ultimately achieve greater energy security. However, EnerPHit does not directly address the issues of moisture and occupant health although it could be argued that they are mitigated by improved fabric and performance. In retrofit, in particular, there does need to be sympathy between the existing structure and the intended use, ensuring that the building functions without the likelihood of creating unforeseen problems that may later degrade the fabric. This requires a holistic approach and the use of a range of materials and resolutions to create a long-lasting energy efficient healthy building.
The use of non-standard materials like the ones highlighted by Ecomerchant does indicate to us that this process is underway and that there are many who will not wait for legislation to catch up. In fact they may well reap extra benefits in the future when others are faced with costly upgrades simply to bring buildings into compliance.
For more information please contact Ecomerchant: Web: www.ecomerchant.co.uk email: info@ecomerchant.co.uk Tel: 01793 847 444.

1 Lord Deben, Chairman, Committee on Climate Change Business, Energy and Industrial Strategy Committee Oral evidence: Energy Efficiency, HC 1730 Tuesday 26 March 2019 2 See notes 131-4 Select Committee BEIS Energy efficiency and net zero 12th July 2019 https:// publications.parliament.uk/pa/cm201719/cmselect/cmbeis/1730/173009.htm#footnote-047 3 Ministry of Housing, Communities and Local Government, Live tables on Energy Performance of Buildings Certificates (2018)
Dove House Residential Care Home adds a platform lift
Dove House occupies an 17th Century, historic property in the centre of the Market Town of Ashbourne.


B
uilt as the Dower House for the Boothby Family who also owned the nearby, Ashbourne Hall, it has been extended over the years as a private residence, then private school until it was converted to a Care Home in the 1980’s. It provides care for up to 20 residents in 16 single and 2 shared rooms over three levels.
Director, Dr. Richard Shepherd, recently contacted Invalifts about the possibility of installing a platform lift to replace the 1980’s shaft lift, which had become unreliable.
After an initial site survey, Invalifts recommended and installed their compact platform lift, with a custom footprint of 1180mm x 1530mm optimising the available space.
The unit was installed in the existing shaft with fully glazed doors to maximise light into the area.
In order to comply with EN81-41, all enclosed lifting platforms require a means of two-way emergency communication, so an intercom was implemented, in case of emergency. The residents and staff were thrilled with the installation.
Dr. Shepherd said; “Thank you for the successful completion of the installation. The two guys who did the work were professional, courteous and worked closely with us to minimise the risks of having visitors to the Home. The lift is excellent, everything as we expected and we are impressed that it was delivered on time, installed in two days and we had a really good handover.”
If you would like to know more about the our platform lifts or other access solutions, please contact the Invalifts team on 0845 468 2543 or alternatively, email sales@invalifts.com