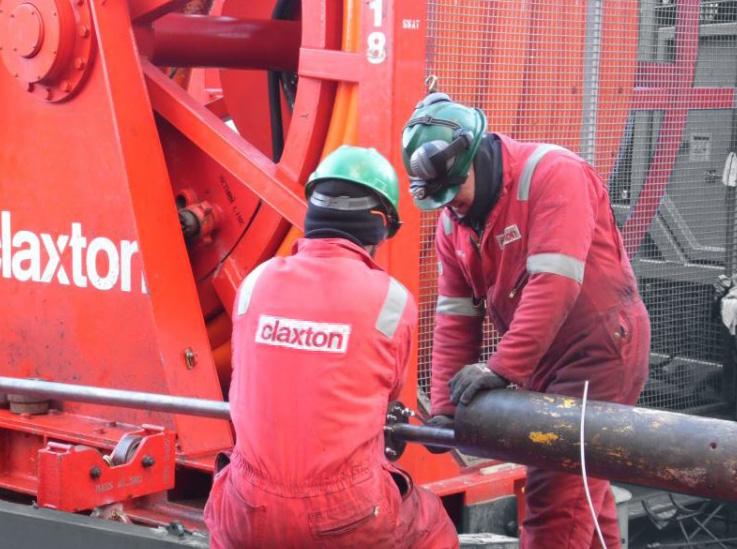
9 minute read
CLAXTON ENGINEERING
Innovation and Family Ethos Drives Claxton CLAXTON ENGINEERING
PRODUCTION: David Napier
Claxton Engineering has grown from a small company founded by Bob Claxton in 1985 to a major global player in the offshore oil and gas industry run by Bob’s daughter Laura Claxton. Now part of the Acteon Group, Claxton is looking to bolster its presence in the decommissioning industry, a sector set to grow significantly in the near future.
// Located on the far eastern coast of the UK, the town of Great Yarmouth has grown to become a hub for oil and gas industry expertise. Thanks to its location, suitable for easy access to the Southern North Sea and other hubs in Scandinavia and the Netherlands, Great Yarmouth is the ideal base for all types of service provider. Since the discovery of oil and gas in the North Sea in the 1960s, Yarmouth has become recognised as one of the most concentrated bases for oil and gas expertise anywhere in the country. Some of the world’s largest oil and gas names have set up shop in Yarmouth with vast reserves estimated to have life until 2035, and fields and facilities that are all crying out for modernisation and refurbishment. In particular, Great Yarmouth has become an industry leader in shallow water engineering, mature asset management and normally unmanned installations among many other areas. But one big area of growth that is helping to boost Great Yarmouth’s industry players in these times of uncertainty is decommissioning. Major investments received recently have provided a lift for the decommissioning sector and this is an area in which Yarmouth is keen to position itself as a centre of excellence.
One of the area’s leading organisations active in decommissioning and a range of other related activities is Claxton Engineering. Founded in 1985 by Bob Claxton, the business’s original focus was offshore engineering services for upstream clients from around the world, specifically wellhead installation and servicing. Over the past 32 years, the company has achieved a number of significant milestones, introducing new services and opening up new offices in far flung regions including Aberdeen, Dubai, Norway and Singapore. It has been the recipient of the Queen’s Award for International Trade and, in 1999, the business was acquired by what would later become the Acteon Group of Companies.
Major success was realised in 1996 when the company introduced its SWAT™ (suspended well abandonment tool) innovation. The SWAT™, delivered in conjunction with sister company InterMoor, is deployed through a moonpool, landed on the wellhead and then used to carry out casing perforation and placement of the required cement barriers in the well. This in turn opens up the option for the deployment of more Claxton services including wellhead severance using the SABRE™ cutting tool, and recovery using the subsea wellhead recovery tool.
The SWAT™ system has been used on more than 100 well abandonment projects worldwide and is widely regarded as an industry leading innovation.
Today, the company is run by Bob’s daughter, Managing Director, Laura Claxton who says: “Our promise
to you is that Claxton will make it happen for your project. From the rental of a simple adaptor, to a full riser system or well abandonment project, you’ll get the same level of service and dedication from our team. And in the event you have a problem on a project, just pick up the phone – there will be no ‘hard sell’ and the Claxton team will do everything we can to ensure your project is both successful and safe.”
NORTH SEA DEVELOPMENT In November, Claxton won a contract in the North Sea for the supply of an all-new 34” subsea overshot, which utilises hydraulic inflatable seal technology. This highly technical project will see Claxton enable tieback to the subsea well’s low-pressure (LP) housing without having to directly interface with the wellhead manufacturer’s proprietary connector. “The Claxton overshot swallows over the LP housing and utilises inflatable seals to provide pressure integrity around the housing’s outer body. With the overshot attached to the base of a 30” environmental riser, the solution allows a hydrostatic fluid column to be held within the riser. The riser analysis stipulated no requirement to mechanically lock the overshot to the LP housing,” the company says.
The company will also be supplying service personnel to ensure installation runs smoothly.
The innovative design of the overshot includes a quick-connector to the 30” riser, eliminating costly offshore handling time.
In October, Claxton was awarded two contracts to provide conductor guide centralisation on the Norwegian Continental Shelf (NCS). The operator allowed Claxton to be involved in the project from the early stages and this aided both parties as design was specific and the entire process simplified.
Both of these projects are highly technical and high-value but typical of the type of work that Claxton is used to in the North Sea and around the world, sticking to its mantra – Make It Happen.
In June, Claxton was awarded a significant contract for casing, cutting and recovery in the North Sea. Working across two different sites for the same operator, Claxton will ensure the removal of Christmas trees and other activities as part of a decommissioning programme.
“Our global experience allows us to provide the most comprehensive decommissioning package for all of our clients, but always having an eye on providing the most cost-effective solution for abrasive severance, cut verification and recovery,” said Laura Claxton.
“We will be using a 150te hydraulic proving jack package, Claxton Double Drilling Units (DDUs) for drilling and pinning and rapid cut band saws for cutting the combined multi strings. Marine growth stripping and removal using
our purpose designed tooling will also be delivered, along with multi-string severance using our proprietary abrasive water jet cutting system SABRETM,” she added.
“As part of the provided solution our equipment is unique and can again offer the operator real savings. Our bottom hole anchor and catch tool system for example, allows recovery of the conductor stump and conductor during the surface recovery stage reducing this to a single operation and removing the need for fishing tools.
“We have also provided an engineered and aligned solution to reduce the number of slewing operations required by the JULB crane with a revision to our existing tubing laydown frame by incorporating a travelling bogie system. The frame and bogie eliminates the need for the crane to slew from the well centre while still allowing tubing to be laid

out on deck. This saves valuable time on a project.”
SAFE & RELIABLE Earlier this year, in July, Claxton celebrated five injury free years, with no time lost to injuries since 2012. Claxton’s QHSSE Director, Peter Carrier said of the milestone: “For a fifth consecutive year Claxton’s global workforce has managed all activity risks to ensure they have maintained their record of no lost time injuries. A feat in its self, but combined with the varied industrial locations, the complex activities and universal interfaces that require to be mastered, a prodigious event. Our playing field, and client’s requirements are, ever changing, and such a record displays that, Claxton is ever adaptable, risk focused and determined to maintain the old oil and gas mantra ‘there is nothing so important’.
“An effective health and safety management system requires the contribution of every staff member and importantly, the support and recognition of your senior management team. This event has not just realised itself, it has taken time, effort, and masses of deliberation and sometimes a self-acknowledgement that perhaps we could have done it better, but that’s the learning and the companies attitude to QHSE continuous improvement.”
The company has also obtained an OHSAS 18001 certification, demonstrating safety excellence. Alongside this, Claxton is also the proud holder of ISO 14001 certification for environmental management and ISO 9001 – 2008 certification for quality management.
“Our dedicated in-house quality team has recently been expanded to help us continue to raise the quality bar as the business grows – they keep our equipment certified and ready to mobilise on a moment’s notice, and just as importantly, communicate quality
issues across the entire business,” the company says.
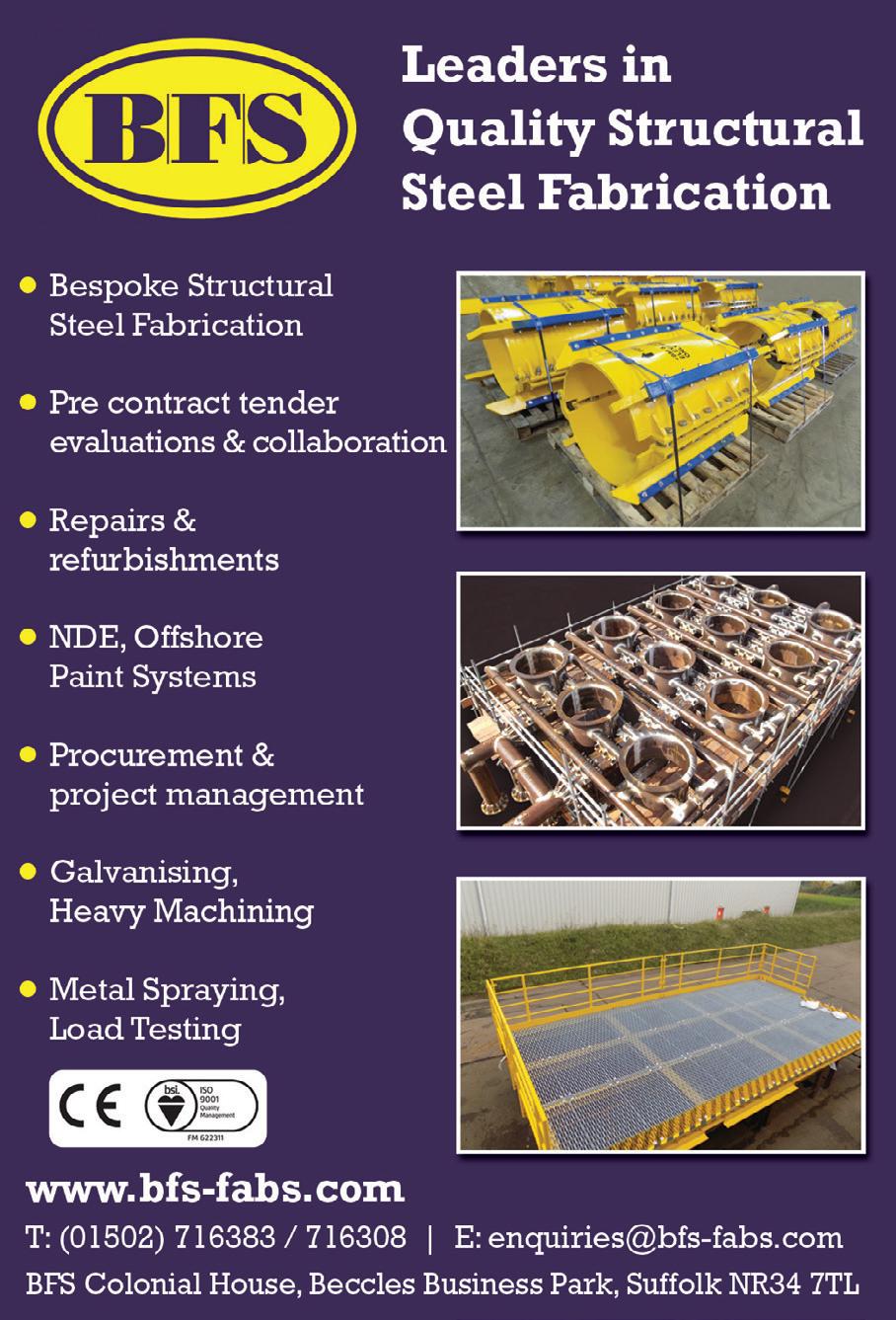
INNOVATION SPECIALIST In May, Claxton announced that it had deployed its WellRaizerTM modular conductor recovery system for the first time. This innovative system was used for well-recovery work on the NCS.
The WellRaizerTM allows for the collection of oil and gas conductor pipe without the need to deploy a jack-up rig or drilling platform.
“With the launch of WellRaizerTM Claxton is now able to bring severance and recovery all under one roof. We believe this capability is a first of its kind for the industry and means we can offer a full solution rather than just a one-off service to our customers,” said Claxton R&D Manager, Matt Marcantonio.
“The WellRaizerTM recovery system comprises of both a static and travelling elevator which grip the tubular sections via two powered slip packages. The unit also incorporates material handling cranes to remove reliance on the main crane for smaller operations and has been developed to meet design codes for this campaign and safety standards for work on the Norwegian Continental Shelf including: NORSOK Z-015, NORSOK R-002, API 4F, API 8C, DNV 2-7.1, and DNV 2-7.3,” he added.
“Through its maiden voyage, we looked at maximising time savings at every stage, whether prior to mobilisation onshore, achieving a safer operation whilst mitigating risks offshore, or providing the multi-skilled staff who now run more efficiently both WellRaizerTM and the subsea abrasive cutting system SABRETM,” he said. Just one of many strings to the Claxton bow, the WellRaizerTM system provides cost savings and project efficiencies the likes of which are not offered elsewhere in the industry. Importantly, the facts across the oil and gas industry show that the major oil fields around world are declining in their production numbers and this is expected to continue in the near-term and long-term future. According to Oil and Gas Authority Aberdeen, Scotland, a total of 1,832 wells are forecast to be plugged and abandoned in the North Sea and Norwegian Continental Shelves region between 2017 and 2023. Globally, the offshore decommissioning market is predicted to grow at approximately 6.93% by 2023, and Claxton, one of Great Yarmouth’s success stories, is set to be positioned at the forefront of the industry. Its ability to deliver first-class expertise and equipment on time, on budget, anywhere in the world while maintaining the family business ethos that has seen it grow tremendously is what will help Claxton continue in this ever-changing market sector.
CLAXTON ENGINEERING
+44 (0) 1493 744 500 @ClaxtonNews www.claxtonengineering.com
Leaders in Quality Structural Steel Fabrication
• Bespoke structural steel fabrication • CNC Precision & general machining • Repairs & refurbishments • NDE, load testing • Offshore paint systems, metal spraying & galvanising • Pre contract tender evaluations & collaboration • Press braking, CNC profiler & rolling
www.bfs-fabs.com T: (01502) 716383 / 716308 | E: enquiries@bfs-fabs.com BFS Colonial House, Beccles Business Park, Suffolk NR34 7TL