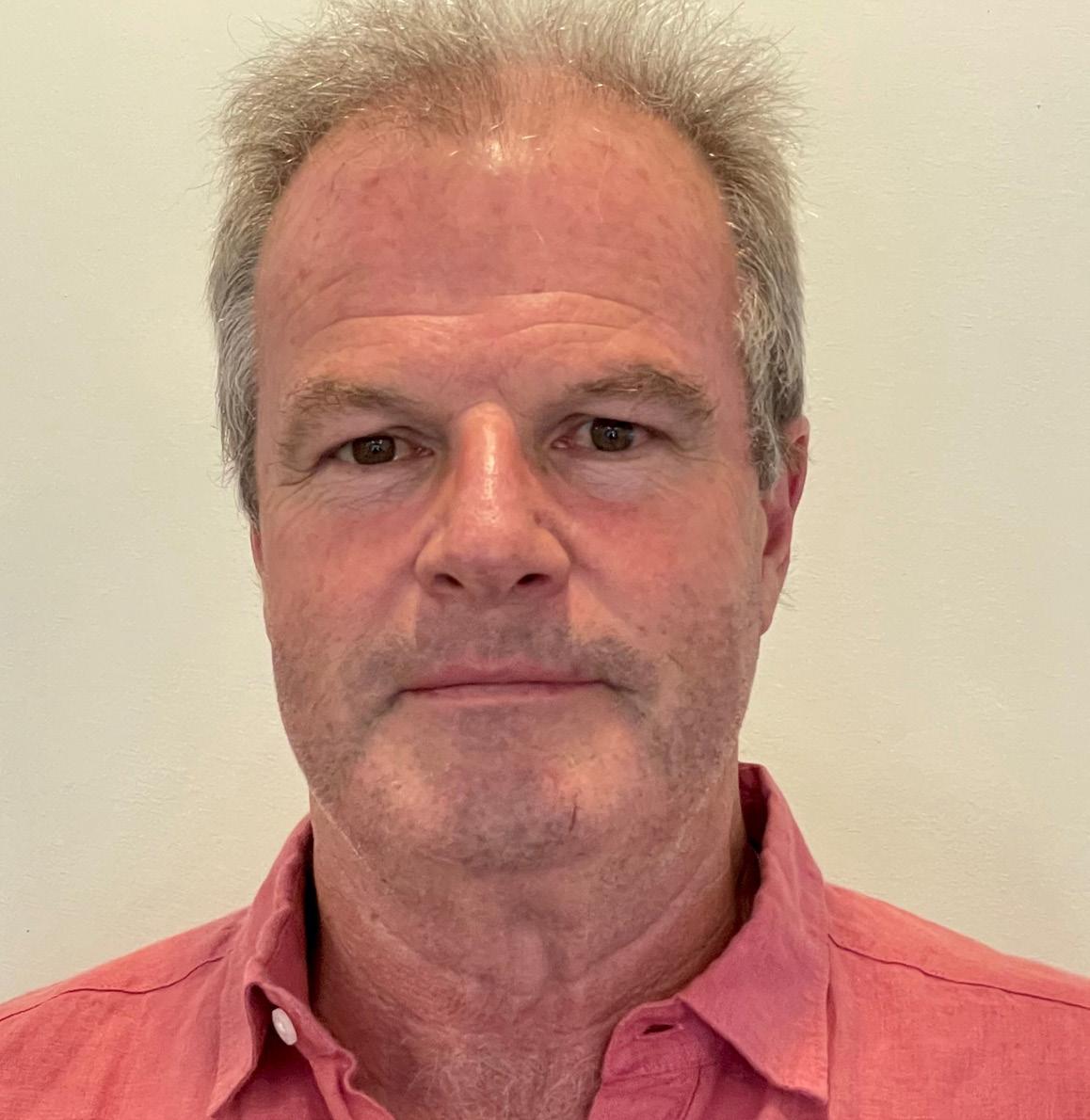
3 minute read
INDUSTRY FOCUS: MANUFACTURING
forging plant where we can forge anywhere up to 25kgs. We also have machine shops where we can do all of our own machining – milling, turning, CNC machines, thread roller, welding bays, welding robots, and the assembly side as well.
“We take raw material, usually an aluminium ingot or steel bar, and we take it right through the process. The only thing we outsource is galvanising and heat treatment. We can manufacture a product right from raw basic steel through forging, to drilling, to machining, to getting it galvanised and getting it assembled and utilised as a finished product, all our own design, our own IP, and our own testing.”
BUY LOCAL!
33% unemployment in South Africa is universally cited as unacceptable. Hindle believes buying local is the key to solving this problem. This means general public choosing local products and services, businesses partnering with other local companies to localise value chains, and government supporting local procurement policies.
//Last year, in the wake of the pandemic, as all industries struggled against the backdrop of a weak South African economy, insight from Pan-African Investment and Research Services suggested that just a 10% increase in manufacturing investment in South Africa could help to achieve a GDP contribution increase of 13%. A 9% increase in fiscal revenue and an 8% increase in employment creation could also be achieved.
Currently, manufacturing accounts for between 10-15% of GDP in South Africa. This critical sector is globally accepted as a driver and supporter of economic growth, and onshoring capability in SA has long been a government target.
But it’s not easy. Manufacturers in the East are cheap, fast, and quality. Setting up a manufacturing operation in SA is capital intensive, and a welldocumented skills shortage is growing.
Thankfully, there are some that realise the potential in Africa’s most advanced and industrialised economy. In an industry plagued with inefficiency and challenge, McWade Productions – leading manufacturer of electrical transmission components - remains optimistic. Approaching it’s sixth decade of operation, the privately-held Gauteng headquartered business has been manufacturing locally since the 60s and knows about the benefits.
“We pride ourselves on local manufacture and design. We are 100% locally owned company and made up of 100% IP,” says Director, Marc Hindle.
“We have our own aluminium foundry and we cast all of our own aluminium components. At the Nigel factory, we have a steel
“For me, the only way for this country to grow is if we employ people,” he says. “The best way to employ people is buying locally. That means we must have products that are competitive, at the right price, right quality, and made to world-class standards. That is why we have chosen the path we have. It has certainly been our focus – we don’t want to be briefcase salesmen, picking up agencies around the world. We try and make as much as we can and we are always searching for local suppliers wherever possible.”
This methodology goes back through the company’s history to it’s initial founding, when it started out as a small maker of electrical substation on claims, sold to Eskom. As the state power company grew, McWade grew. It’s reliability and quality were in-demand from the utility as it increased coverage across South Africa. Acquisition and diversification helped to fuel expansion, and the company now offers almost every product required to move electrical capacity from generating asset to regional substation.

“We work up to 765kV, right at the top end on substations and transmission lines, down to 11kV – but we don’t do household connections,” says Hindle, an industry veteran, with McWade for more than 30 years.
“We tick a lot of boxes for the country. We make everything. We are a Level 1 BEE company. we are ISO 9001 accredited and we believe we represent a lot of what this country needs,” he adds.
And buying local is now more attractive from a cost perspective. The global logistics crisis that came as a result of China’s close-down around the pandemic wreaked havoc across the business environment, and many that were reliant on the East for imports were choked.
“A lot of those have come back to the local market and we are starting to manufacture goods that use to be imported. We struggled to meet imported prices but our customers don’t have to carry as much stock. They can order smaller batches from us, and our quality is just as good or better,” says Hindle.
Shipping containers from China is no longer a straightforward exercise – especially when transporting critical infrastructure components like those produced in Gauteng by McWade. The costs and schedules have increased by more than 100%, and sometimes are triple that of 2019. Alongside the Rand being decimated in foreign currency markets, importing is less appealing. “Customers are starting to send more and more products our way, outside of electrical, and that is exciting,” says Hindle.
Diversification
Currently, the McWade Productions range includes high-voltage substation interconnecting clamps (up to 765kV),