
9 minute read
Where the Wind Blows
Fifth-generation Landwehr Construction tackled two ISO certifications to meet the requirements of its biggest wind-energy customer.
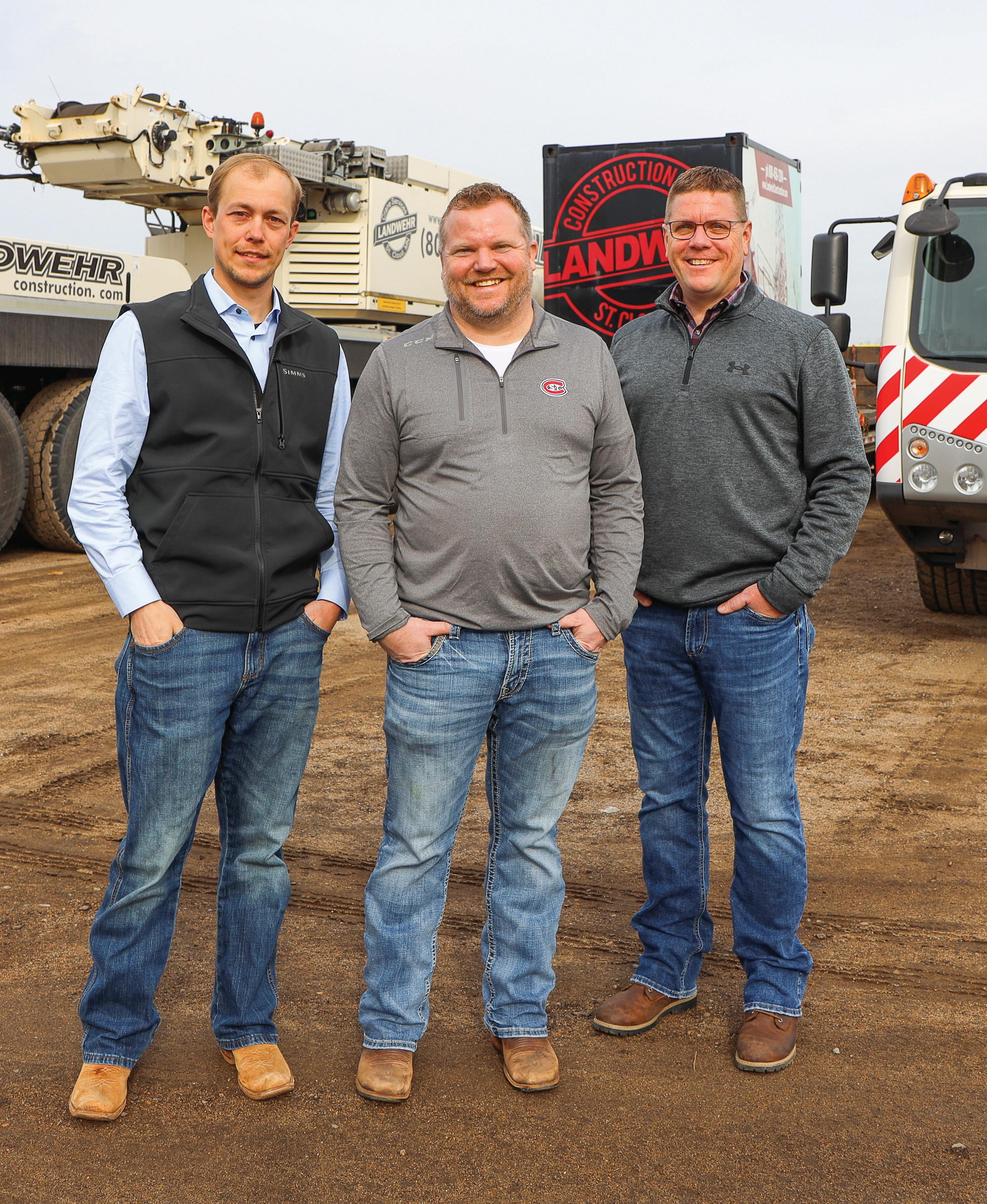
Advertisement
By Suzy Frisch
Wind energy has been soaring in the United States as a power source, and it is on track to become an even bigger player in the domestic energy grid. Driving across the wide-open spaces of the U.S., it’s common to see fields of giant wind turbines in action. These massive pieces of machinery had to find their way from the manufacturer to often rural areas for installation — no easy feat.
Metal and fiberglass components, including 262-foot blades and tower sections that weigh 75 tons each, must be moved from barge and train, to dock and rail yard, to truck, and then onto their eventual landing place. It’s a logistical challenge that takes a team of highly trained employees working in tandem to safely transport these heavy and huge elements.
St. Cloud-based Landwehr Construction has been engaged in this work since 2017, building on a long history of serving customers with its cranes and doing heavy civil construction projects. Wind energy is a fast-growing part of this fifthgeneration business, especially as it began working for Vestas, a Danish company that designs, manufactures, installs, and services wind turbines. From its North American headquarters in Portland, Ore., Vestas has become a big player in wind in the United States, installing nearly 24,000 turbines as of 2022.
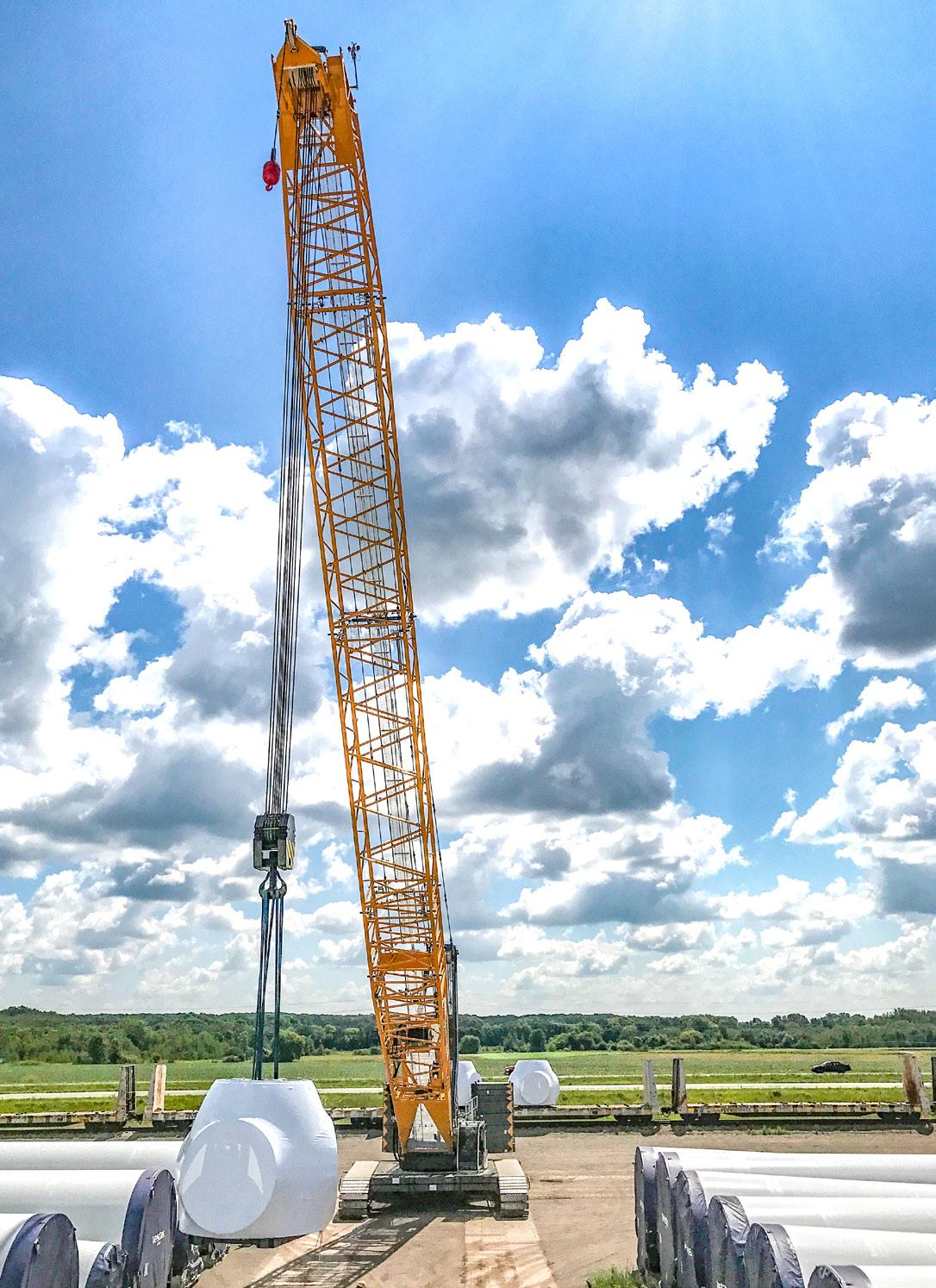
So when this growing company requested that its vendors earn two ISO certifications, the leaders at Landwehr Construction really didn’t have to think hard about it. They wanted to ensure that Landwehr continued to be a supplier of choice for Vestas’ turbine logistics and that it could continue thriving alongside the company.
“When one of your biggest clients tells you this is a requirement, it doesn’t give you a lot of wiggle room,” says Matt Fourre, vice president of cranes at Landwehr. “I’m not sure that if the requirement wasn’t there from Vestas that we would have gone through this process. But now that we are through it, it has brought a fair amount of benefit to our operations.”
Tackling two ISO certifications at the same time is not a small undertaking. And as a company that’s not a traditional manufacturer, Landwehr needed some help. Its leaders called in Enterprise Minnesota to guide Landwehr through the process of obtaining the ISO 9001:2015 certification for quality management systems and the ISO 45001:2018 certification for occupational health and safety. Vestas announced its new requirements in 2020 and wanted them completed by yearend 2022, a job made more complicated by the COVID-19 pandemic.
Landwehr received its certifications in early January 2023. They are already having a positive impact on how Landwehr runs its safety program while priming the company for an even brighter future, says Nate Landwehr, company president. Now Landwehr can retain a sizeable amount of business from an important client, and it’s primed to capitalize on even more work in the growing green energy sector.

“Even with our customers asking us to do this, we see the value of having processes that we can easily implement and train people on,” Landwehr says. “Having the certifications shows that we’re willing to put in the time and effort to institute plans and processes that are safety-driven, and it shows that we are making sure we’re keeping our people safe.”
Safety first
Safety has long been a primary driver at Landwehr, which got its start in 1895 in the dray line business with founder William Henry Landwehr at the helm. In a full-circle moment for the now construction-focused business, Landwehr’s dray line operators would transport goods from the railroads and distribute them to businesses in town. During Landwehr’s first decades of operation, it became known as the St. Cloud company that could move anything, including pianos and houses.
In the 1920s, Landwehr split into two businesses. The company that continues today focused on building and moving bridges and other large structures. Upon returning from World War II service and rejoining the family business, Ronald Landwehr (Nate’s grandfather) steered the company’s work to demolition, civil construction, and other crane-heavy work. Landwehr developed a specialty in installing box culverts, or precast bridges, that it continues doing today. It also moved into excavation, road construction, and civil earthwork, which carried it through the 1960s and ’70s.
When the 1981 recession hit, Landwehr dove deep into construction, working on a major paper mill expansion in Sartell that kept the company busy for years, Landwehr says. Under the leadership of current CEO Dan Landwehr, the company continued expanding its services in the highway heavy construction sector — including grading, demolition, and installing underground utilities — as well as deeper into civil construction projects like installing sewer and water systems and building roads.
All the while, Landwehr expanded outside of central Minnesota to tackle projects across the state. In the 21st century, Landwehr significantly expanded its 50-year-old crane business, Nate Landwehr says. It evolved into an indemand subcontractor that does a range of work, from setting rooftop HVAC units to erecting precast concrete walls for building projects to transporting materials to customers’ work sites.

Today, Landwehr has offices in St. Cloud and Chaska. Both handle crane and rigging-based projects for diverse customers working in varied settings, such as preparing sites for construction or hanging signs on U.S. Bank Stadium in Minneapolis. Landwehr’s crane work then opened doors for it to enter the renewable energy space. A trucking company hired Landwehr to build a rail site for offloading and transporting wind turbine components, and a new line of business for the company was born.
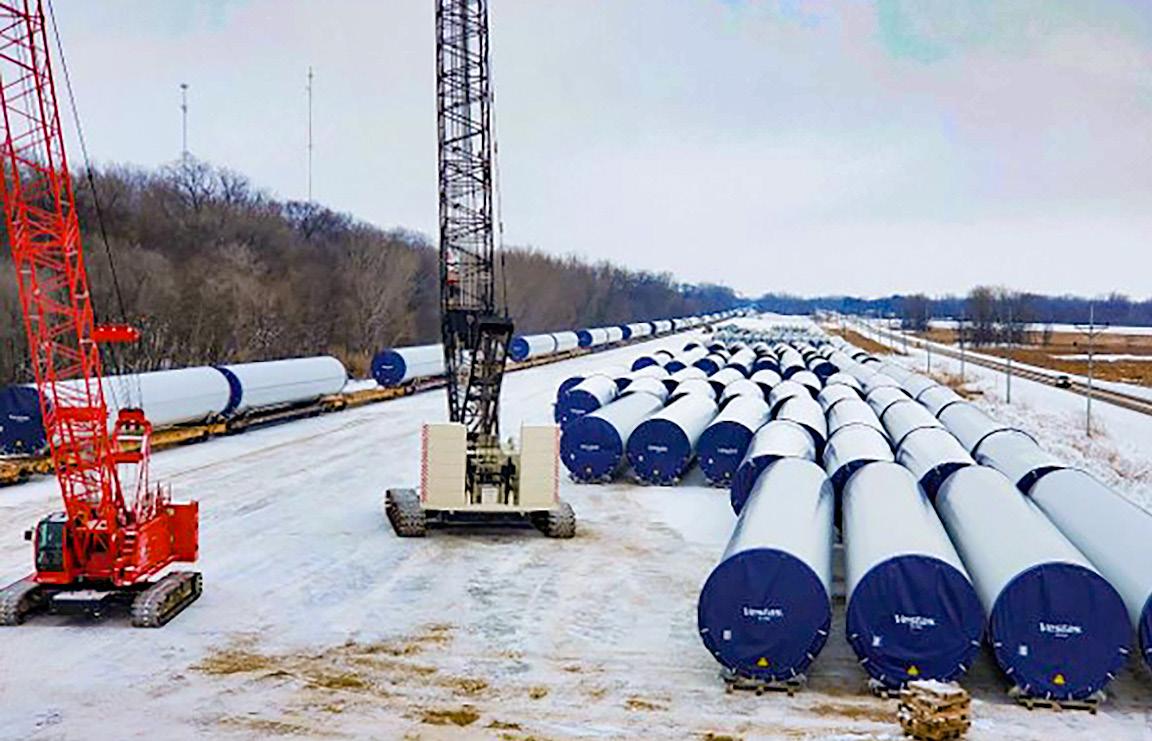
Such transitions have been a key component of Landwehr’s success over its 128year history, says Nate Landwehr, who has been leading the company since 2018. The company nimbly evolves or expands its operations to meet customers’ needs while offering a deep menu of services that help it withstand changing economic conditions, he says. Today, about 200 employees work at the company, with just shy of $100 million annually in revenue.
“What makes us unique is we do a lot of different things that keep us busy in down times,” Nate Landwehr says. “We’re seeing higher inflation rates, so our commercial work is slowing. Then we’ll pivot to more public bid work. When interest rates come down, we’ll pivot to doing more private work. And then the whole time we’re doing utility sector work and energy, our cranes are doing both. We do a lot of different things that keep us vertically integrated and give us options to pivot to when the times change.”
Another important element has been Landwehr’s long commitment to employee safety. Throughout its history, Landwehr leaders have emphasized that “we want all of our employees to go home as good or better than when they came to work,” Nate Landwehr says. Taking time to focus on the company’s processes and improving its systems for keeping workers safe seemed like a natural fit.
Two big jobs
It’s also timely. Many international wind energy companies have started requiring ISO certifications, especially related to safety, says Dawn Loberg, an Enterprise Minnesota business development consultant. Landwehr now has the necessary credentials to serve them. “All the big players in wind are requiring ISO safety,” she says. “ISO 45001:2018 is more prevalent in Europe, but as the world gets smaller, we’re going to see more and more companies needing it.”
Still, completing two ISO certifications simultaneously in a short amount of time initially made the undertaking seem daunting, says Tyler Adamsheck, Landwehr project manager and estimator who led the company’s ISO team. Add in the good complication that Landwehr was having a busy, record-breaking revenue year in 2022 and everything became a bit more challenging.
The Enterprise Minnesota team, including operations consultants Keith Gadacz and Greg Hunsaker, approached the dual certifications as one big continuous improvement initiative with safety at the core. Despite the difficulties, it was important work for Landwehr to complete that now gives it operational and competitive advantages, Hunsaker says.
Going through dual ISO certifications often bears fruit through cutting costs, avoiding other costs, streamlining operations, retaining and boosting sales, and showing employees that safety is an integral part of the company’s DNA. “The impact of integrating these two ISO pieces together to run and grow a business is just exponential,” Loberg says.
Much of Landwehr’s ISO initiative involved formalizing processes the company already used to prevent safety incidents, and train, document, and communicate about safety, Gadacz says. Landwehr needed to build up its management systems for quality and safety, implement changes, and then use and audit the new systems.
“These are management systems for safety and quality management that help them think about internal and external risks to the business,” Gadacz says. “We talk about the plan, what we are going to work on, what could go wrong, and how we can multiply opportunities and mitigate risks.”
Though the work can be difficult, there is value in putting in the time and coming out the other side with the ISO certifications. “It improves their operations. It encourages them to use data to make decisions,” Gadacz says. Company leaders can say, “Now that we know, we can think about how we replicate our performance and customer satisfaction or change it for the better.”
Landwehr can deploy its new systems to address all manner of concerns, such as preventing injuries, managing change, addressing turnover, or handling growth. “Their customer asked them to do this to be a strong supplier,” Gadacz says, “but the business got better with each of the improvements as well.”
Real, continuous improvement
Then there are other advantages that come from improving safety programs, Hunsaker says, including empowering employees to get more deeply involved in the company’s safety work. “They’re looking for people in the field to be problem-solvers and improvers of the safety process. They aren’t just looking to corporate when there’s a problem,” he adds. If employees see areas of improvement from their day-to-day experiences at job sites, they can scan a QR code that allows them to make suggestions or report issues to Landwehr.
Adamsheck confirms that Landwehr operates more efficiently since the company completed its ISO work. He typically oversees seven to nine windenergy sites that Landwehr is building and running concurrently for Vestas. The new processes have allowed each site to operate under one uniform plan, instead of having site supervisors run things their own ways.
“This has aligned everybody under the same program and allows us to switch supervisors between job sites with less disruption if we need to do schedule changes,” Adamsheck says. “Anybody can step into a job now and take it over because everything is being documented and monitored and recorded in the same way. It’s helped our onboarding process for new employees and made it more robust. That’s been a nice change.”
Improved consistency in Landwehr’s safety programs has been another positive. “We know where things are filed, and we know when an incident happens. We need to follow it all the way through and come up with a plan to eliminate it for the future,” Adamsheck says. “From our safety department to the field to our project managers, everyone understands the process, and everyone understands the extent that we have to follow through on everything.”
Landwehr has realized other operational efficiencies. For instance, field supervisors previously would reach out individually safety performance over time, identify patterns that might have gone previously unnoticed, and create metrics and goals for improving performance. “Safety has always been our number one priority day after day, job after job,” he says. “Over production, customer requests, anything. The ISO process has helped us set up better ways of doing things.”
Having a big picture view is important because if there’s an issue at one job site, it most likely is occurring at the other sites, too, Adamsheck says. There is better communication between site supervisors, and that makes it easier to keep the whole team informed about safety procedures, improvement ideas, and ways to lessen risk and prevent problems from happening again.
Injury prevention is key, Fourre says, especially at wind-energy job sites because the stakes are so high. That’s a key reason why Landwehr made improving its safety processes through ISO certification a top priority — both to retain a key customer and to improve the company’s systems and operations, he says.
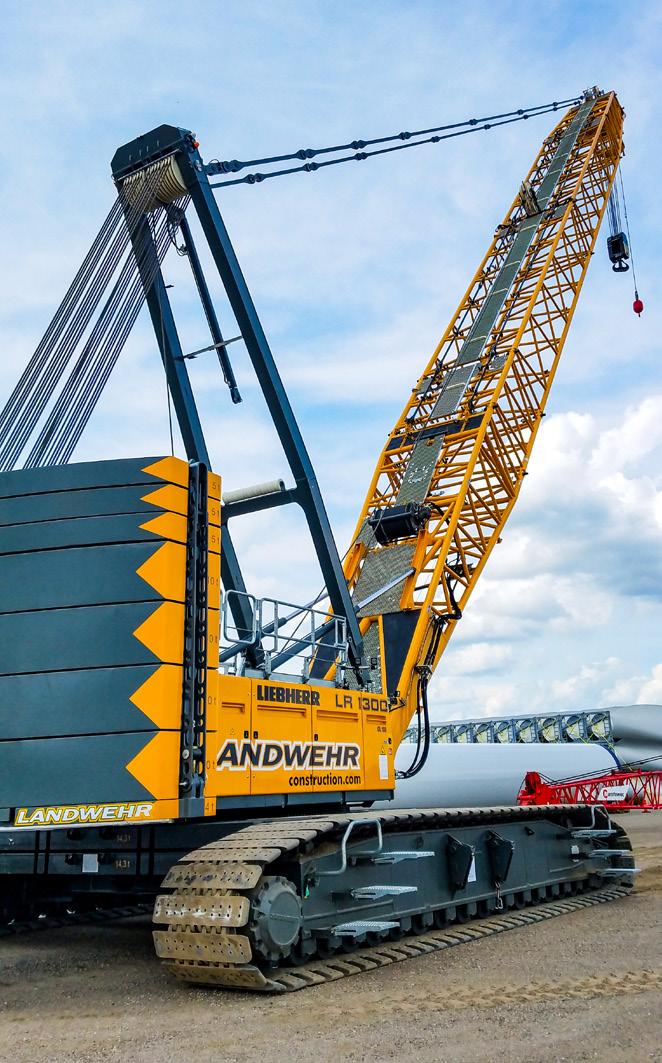
“We are handling components that are thousands of pounds and a football field in length. Everybody needs to be aligned on the same page to do that work safely,” Fourre says. “People are at risk of death or serious injury, and there are risks of huge amounts of damage or property loss. You make one wrong move, and you can put your best buddy in a really bad spot. We always say to employees, ‘Nothing that happens today is more important than your safety, your life, your livelihood, and being able to go home to your family as good or better than you came to work.’” to Adamsheck for information. Since Landwehr built up its management systems, supervisors now have remote access to the company’s hard drives and can get all the information they need. “It cut back on a lot of the back-and-forth conversations and emails about how we do things,” he says. “They can access most things on their own and can be much more self-sufficient.”
On top of the efficiencies, Adamsheck appreciates that the new processes allow Landwehr to better track the company’s
Though it’s still early, Landwehr already is noticing benefits from implementing ISO improvements in its wind-energy division, Nate Landwehr says. Having processes that are easy to implement and improve training will only make the company more efficient — benefits he would like capture in other divisions by implementing ISO principles there. Running the company well, including treating employees like family by keeping them safe, has been a thread that carries through Landwehr’s decades of operations.
“The main thing about being a fifthgeneration company is that our people have really helped us build it and keep us changing with the times and being innovative,” Nate Landwehr says. “We feel the future looks bright with all the different things we’re able to do and accomplish with our people.”