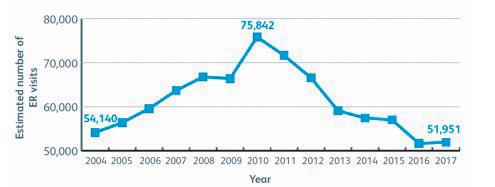
11 minute read
PACKAGING
from EPM May/Jun 2021
by EPM Magazine
EPM speaks to GARETH BAKEWELL, joint managing director at Reelvision about the evolution of packaging technologies in pharma and what this means for the safety of medicines.
LEADING THE PACK
Packaging in life sciences is constantly evolving with new safety features (anti-tampering, tracking technologies etc). Despite this, do you think these technologies are being implemented in enough of a widespread manner throughout the industry?
Without question there are many pharma companies that have a good strategy when it comes to protecting their products from targeted counterfeiters. These businesses have adopted a number of both physical and digital techniques. At Reelvision we have a constant fl ow of new designs and often received artwork that contains various counterfeiting features ranging from micro dots that appear randomly to micro text with hidden copy errors and pattern gloss varnishes with intentional imperfections.
However there are many missed opportunities for brand owners to implement counterfeit features into their products and this could be due to a misconception that their inclusion will aff ect the cost of the packaging, which is not always the case. But with any advancement, the uptake of technology can be gradual and this is not always a bad thing as a slow uptake can often make the advancement more robust leading to long term positivity.
Reelvision’s lead time is particularly fast in this industry. How do you achieve this?
To achieve this service and quality performance, we developed an inline print and die-cutting machine which controls colour through the utilisation of an engraved anilox roller with metered doctor blade that consistently delivered colour without variation. This secure singlepass manufacturing process eliminates the risk of admixture and is combined with a streamlined BSI approved MIS system to enable fast accurate order administration. This generates clear unambiguous instructions for production processing and dispatch of product with simultaneous invoicing.
You’ve been in the industry a while now and have worked with a range of clients. How has packaging evolved over your time to account for things such as counterfeiting or tampering?
I have seen an improvement, driven by ISO, an independent non-governmental international organisation, where through the implementation of ISO9001/2015 PS9000/2016 accreditation, printing companies such as Reelvision have to demonstrate a robust secure disposal process of all manufacturing waste. Thus preventing the counterfeiter from gaining access to confi dential documentation.
More so, can the cost of implementing these technologies put companies off using them?
Many counterfeiting measures are cost free if implemented at the point of artwork generation. However the printed packaging industry needs to be careful not to confuse brand owners with jargon & terminology, after all this is an industry that quotes such buzz words as grips, chokes and bleeds to stochastic and samba screens! Therefore it’s vital that a good dialogue chain is established between brand owners and converters where a plan can be formulated to implement the right solutions for a multi layered approach to a sound counterfeit strategy.
So, we know about tracking features and things like holographs and invisible printing for protecting packages but what other technologies are available that manufacturers may not know about?
Most organisations will be aware of counterfeiting techniques such as bifl uorescent and colourshift inks, debossed emblems, QR codes, RFID tags and smart labels. But even the most sophisticated anti-counterfeit approach is worthless if you can’t identify a genuine product from a fake or that the genuine pack has not been tampered with.
I feel brand identity protection through the control of material specifi cations and colour consistency is a critical layer of the cake. Packaging converters need to be challenged to reduce the gap between light and dark colour standards and tasked with matching agreed pantone references. It should not be acceptable for colour to drift during production runs or repeat orders as this variation raises a question with the end consumer… is it a fake or has the colour faded because it’s passed its sell by date?
With such a plethora of technologies available, is there a way (either through policy or regulation) for them to be better integrated throughout pharma?
I think dialogue is the key to improving the implementation of counterfeit techniques and this needs to be done prior to MHRA artwork approval. From my experience the food retail sector has this nailed down. I recall as a trainee salesman back in the 90’s, I’d spend hours driving up and down the M1 visiting Baker Street, Blackfriers, Cheshunt, Leeds with a few deviations down the M4 to Bracknell. All these visits would enable me to participate in a group discussion with brand managers, designers, food technicians, food manufacturers and fellow printers. This created the opportunity to view artwork concepts, discuss material grades, check the correct machine drawings have been submitted, voice any concerns and agree a critical path to ensure launches are always achieved on time. Subsequently fi nal artworks were created and approved by all parties. These days all this is achieved via a time saving digital workfl ow but the principle is still the same with opportunities to voice your opinion prior to artwork being formalised.
Has the implementation of the Falsifi ed Medicines Directive (FMD) in the EU improved the overall safety of medicines in the supply chain?
Introducing measures to ensure all medicines are safe to use can only be a good thing and by adding extra features such as 2D matrix codes with tamper evident features only enhances the security of all drugs.
Do you think the UK’s departure from the EU will harm the safety of medicines being imported into the UK?
In short no. Both the EU and the UK have mirrored each other on the safe fl ow of medicines back and forth. The fact that the UK is now outside of that shared policy, we will still see the UK following the same rules and regulations.
Outside of FMD, is there anything regulators can do to ensure that companies are adopting technologies that prevent counterfeiters?
Understanding the impact of counterfeit goods is an incentive to drive companies to protect their brands as surveys would suggest that approximately two thirds of consumers who have unintentionally purchased a counterfeit product have in turn lost their trust in a brand. Within the pharmaceutical world the ‘trust’ element is essential as consumers need to know that the product they’re using is a safe and eff ective treatment.
About the company
Reelvision was founded in 2007 as a company specialising in the manufacture of small to medium order volumes of printed folding cartons. From the start, Reelvision off ered a standard 10-day lead time for clients wanting to buy small batches from an accredited source that came with all the required quality checks. In the past 12 months, Reelvision has been involved with supplying folding cartons for numerous Covid-19 clinical trials and has worked with the NHS as a key supplier for the Oxford/AstraZeneca and Pfi zer vaccines to be delivered around hospitals and vaccination centres.
ADVANCES IN SAFETY
How the pharma industry has continued to advance its eff orts to improve the safety of child-resistant packaging.
Unintentional poisoning continues to be a widespread medical emergency across the globe, with medication being one of the most common causes, putting children at the highest risk of potentially fatal accidents. In the European Union (EU), poisoning is the fi fth leading cause of unintentional death among children and adolescents. Research from the European Child Safety Alliance estimates that 3,000 children under the age of 14 die from acute poisoning every year. More recently, this has sparked increased eff orts into improving parental education in ‘child-proofi ng’ homes, as well as patients and stakeholders calling on pharmaceutical companies to recognise the importance of child-resistant closures (CRCs) in medical packaging. The reduction in the rates of child poisoning since 2010 in the United States (US) is indicative of a global decrease (Figure 1), but accidents can and do still occur, and regulations are continually evolving to optimise the safety of childresistant packaging for drugs.
As the industry is improving its packaging standards and unintentional child poisoning therefore decreases, it continues to be a prominent factor in the development of pharmaceutical packaging. Eff ective CRCs for medical packaging must protect young children from gaining access to harmful substances, without hindering the ability of older patients to access their medication.
GLOBAL GUIDANCE AND REGULATIONS
There are varied mechanisms for incorporating CRCs on medical packaging, which are broadly categorised into: • re-closable bottles, which include push and turn caps or squeeze and turn caps.
Figure 1: Estimated number of emergency room (ER) visits in the United States for accidental medicine poisoning under the age of 6 years. (Source: Safekids Worldwide) • non-re-closable blister packs which include a peel and push method.
Now, in many countries, pharmaceutical and healthcare companies are required by law to produce packaging that is child resistant. The US has been leading the way in child-resistant packaging for years, where protocols were originally established in 1966. In 1970, the Poison Prevention Packaging Act (PPPA) was passed and placed under the jurisdiction of the Food and Drug Administration (FDA). In addition, the International Organisation for Standardisation (ISO) has published an internationally recognised agreed standard test procedure for re-closable child-resistant packaging and in Europe, several regulations have been introduced to complement this ISO standard. For packaging to be classed as child-resistant, it must meet one of the following standards: • ISO 8317:2015 – the
International standard • EN 14375:2018 – the
European standard • US 16 CFR § 1700.20 – US regulation
To qualify as CRC packaging, pharmaceutical companies must now have certifi cation of child resistance for their full packaging solution – including the container and closure – and must recertify if either component is changed. One barrier that drug manufacturers face is the time and cost associated with certifi cation. By partnering with a packaging manufacturer that can provide innovative packaging, as well as the required certifi cation, this process can be streamlined, and companies can ensure child safety for their drugs.
As awareness of unintentional child poisoning increases globally, large pharmaceutical companies are driving recognition and innovation in child-resistant packaging, with more advanced designs every year. One example is GlaxoSmithKline (GSK) which, as one of the world’s largest pharma companies, has made signifi cant contributions to increasing awareness of the importance of child-resistant packaging and has integrated this approach into its drug manufacturing pipeline.
However, there are important considerations when advancing packaging designs, such as the cost and sustainability. For example, failure to comply with exact requirements of child-resistant packaging could result in company fi nes or payouts in the event of child injury, while brand damage is also at risk in the event of unintentional poisoning. In terms of sustainability, increasing
environmental awareness across the global pharmaceutical industry has drawn attention to the need for more sustainable packaging solutions. Aligning child-resistant packaging with additional components that make these solutions sustainable are increasingly important for both customers and company initiatives alike. Moreover, innovative user-friendly childresistant packaging solutions are driving the move to a more patient-centered treatment approach.
SENIOR-FRIENDLY PACKAGING
When developing child-resistant packaging for pharmaceuticals, one of the greatest challenges is designing a closure that both prevents children from gaining access to harmful substances, without limiting the ability of senior patients to take their medication. Increasing population age combined with the growing trend for home care is directing the focus of child-resistant packaging simultaneously onto the accessibility needs of older patients. There has been criticism over the lack of acknowledgement in current protocols for disabled and vulnerable patients, who, if their needs are not met, may leave the closure off their medication and, in turn, increase the risk of child access.
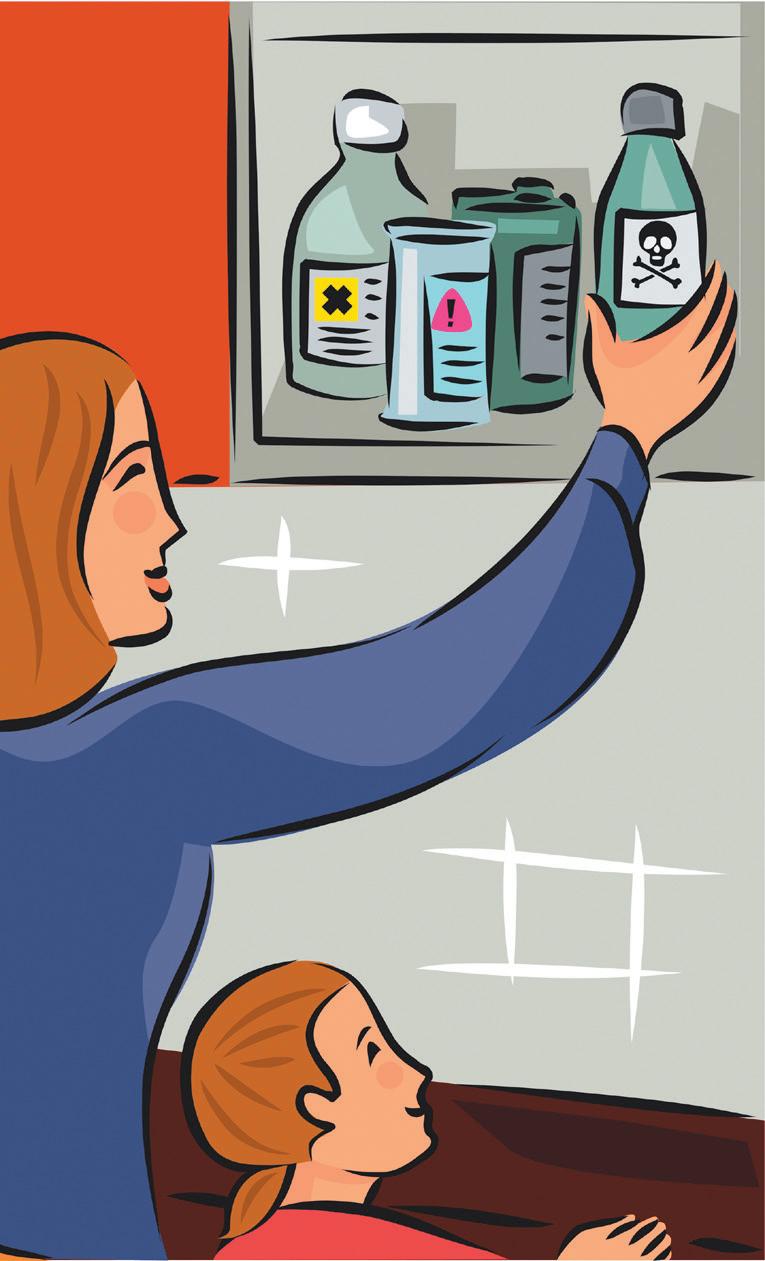
This, therefore, provides an opportunity for pharmaceutical packaging manufacturers and pharmaceutical companies to lead the industry in designing truly child-resistant seniorfriendly (CRSF) packaging for medicines. Strong relationships between drug manufacturers and packaging suppliers, as well as with healthcare providers and patients, will help facilitate this approach, for example by overcoming the currently perceived trade-off between child resistance and seniorfriendly packaging.
THE FUTURE WITH SAFE, COMPLIANT CHILD-RESISTANT PACKAGING
Following the introduction of child-resistant packaging requirements, the incidence of poisoning in children has decreased steadily throughout the last 10 years. As well as enhanced regulation, this decrease is thought to be attributed to increasing awareness campaigns and educational eff orts, through initiatives such as the Centers for Disease Control and Prevention (CDC) PROTECT Initiative and Up and Away Campaign, and Safe Kids Worldwide’s medicine safety programme.
However, unintentional poisonings and fatalities still occur across the globe. The risk to children depends heavily on their environment, and with more adults receiving prescriptions for medication such as sleeping aids, strong painkillers, and antidepressants, childhood exposure to harmful medication increases.
As certain drugs have become more problematic for child safety, such as the increased prescription of opioids, the need for safe, compliant childresistant packaging has received increased attention. There is always room to improve the safety of pharmaceutical packaging that also maintains medication compliance with patients, particularly seniors. Innovation is continuing to take place to ensure child-resistant packaging is truly senior-friendly. As we look towards the future, it is vital that drug manufacturers and pharmaceutical packaging manufacturers collaborate to supply the safest packaging solutions and meet the regulatory requirements to prevent unintentional deaths across the world.
Authors: NAJET MEBARKI
- senior product marketing manager at SGD Pharma.
DR ROLF ABELMAN
- managing direction at IVM Childsafe.