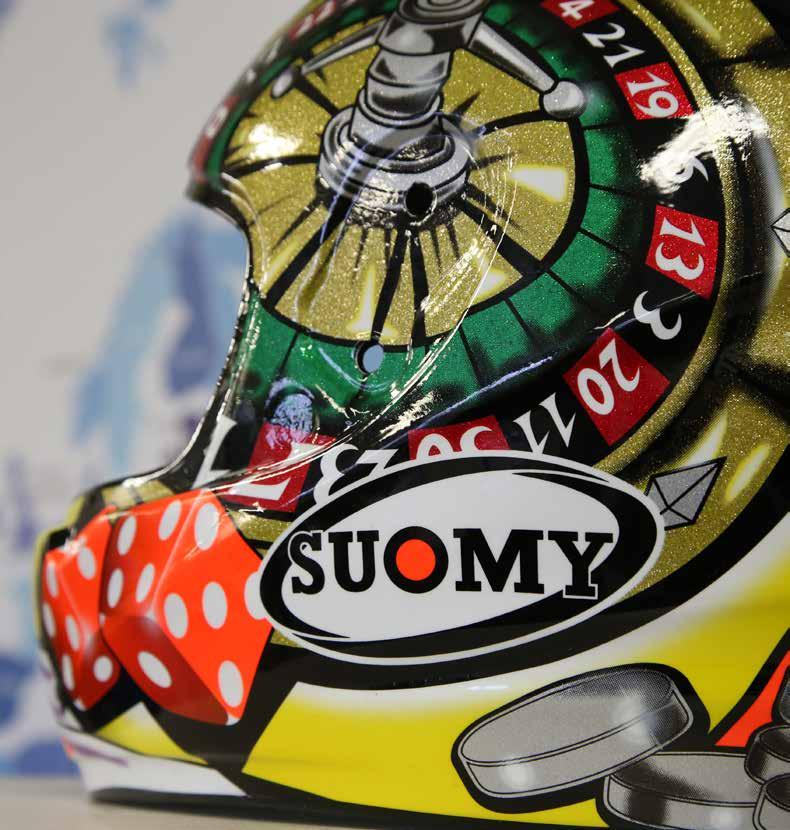
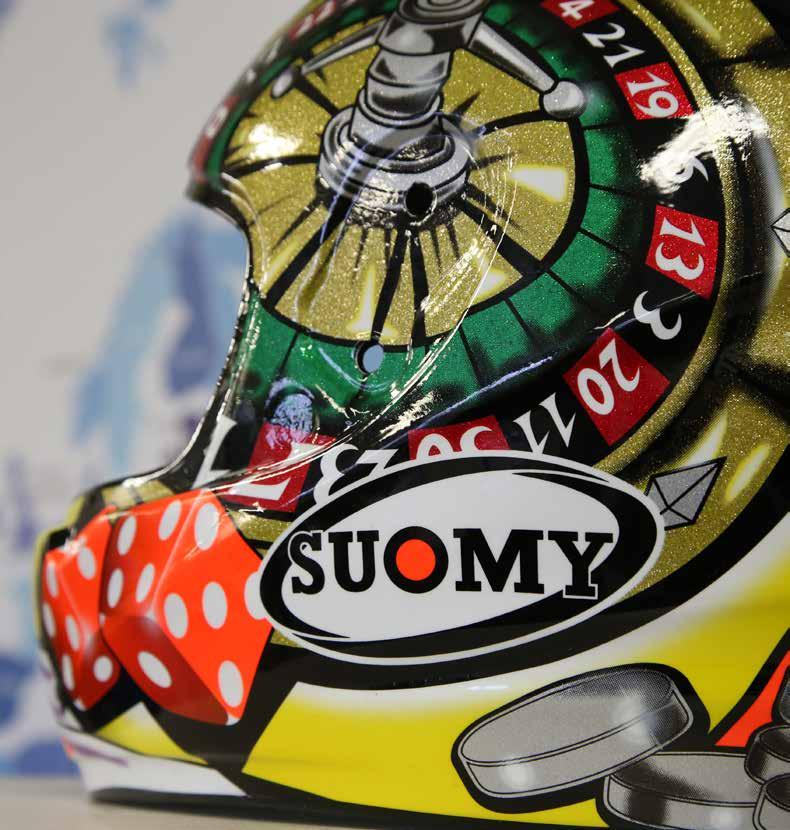
What is a waterslide decal
Decalcomania is a decorative technique based on the realization of a graphic artwork that can be transferred onto 3D surfaces. Decals are an excellent solution for decorating items which are not suitable for the direct printing, due to their shape and features.
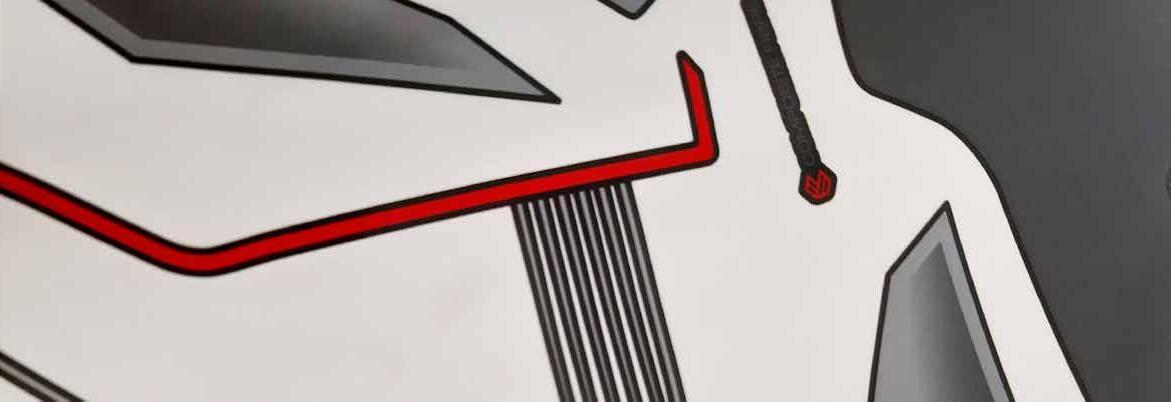
Where to use Waterslide Decals
Waterslide decals must be applied on pre-coated substrates
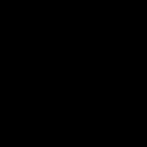
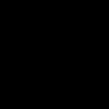
Decals can be used for the decoration of any object made in plastic , metal , wood or carbon fiber .

Why use waterslide decals
To decorate curved surfaces and complex shapes , fitting the needs of any industrial designs and aerodynamical features
To realize elaborated graphic artworks , with several colours, including metallic and fluorescent effects. Any request can be fulfilled in terms of communication, customization and graphics.
To achieve top-quality results . Due to their very low thickness (25-30 μm), decals can perfectly blend with the object and the final over-varnishing allows to obtain high mechanical and weathering resistances. There is no comparison with traditional stickers, that have about 100 μm thickness and tend to unstick over time.
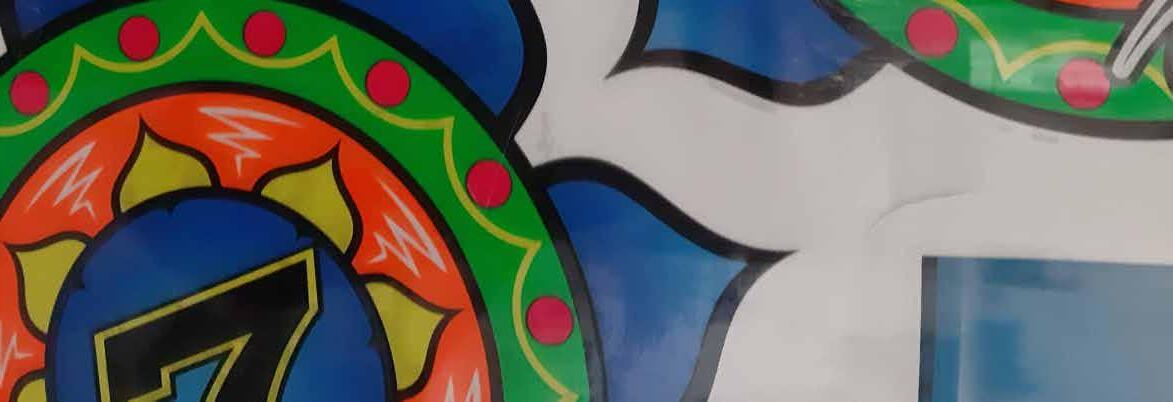
How decals are made
3. Peelable coating
Peelable coating
Collodio is a special wrap that allows to transfer the decals from the paper to the final object. Collodio can be screen printed with high thickness.
Transparent ink
2. Inks
Coloured ink
Texylon 58.000 and Texylon 59.000 series are our market-leader inks for manufacturing water slide decals. It is possible to choose between 58.000 matt and 59.000 glossy finishing. The most common printing sequence is to apply one or more background white layers, followed by colours and a final transparent ink.
White ink
1. Printing sustrate
Printing substrates
Special paper, with a specific water-soluble coating that allows to remove the graphic artwork by means of a simple water immersion.
Printing substrate: Special paper
The special paper for decals is treated with a water-soluble coating on the print side . The water-soluble coating allows to remove the graphic artwork with a simple water immersion.
The special paper is non-absorbent and it helps to maintain a good register among the printing layers.

Inks: White
In the most common graphic artworks, one or more layers of background white are applied first. The white background avoids that the colour of the substrate affects the colour rendering of the decals.
It is possible to choose among two dedicated products:
TEXYLON OPAQUE WHITE SP (code A31258107SP)
Excellent results in the production of waterslide decals due to high opacity and flexibility.
Suitable for semi-automatic printing machines.
TEXYLON WHITE HS (code A31258108)
“High Speed” white, suitable for cylinder machines and high printing speed. Excellent printability without compromising opacity and flexibility. It is the perfect choice for high print runs and industrial productions.
The drying process is fundamental to obtain a perfect result. It must be run in well aired Wicket oven, or at room conditions in a well aired environment.
It takes 3 – 4 hours at 25 – 30°C and 60% RH to reach a complete solvent evaporation.
Inks: Colours
The colour range includes all the products of the Texylon 58.000 and 59.000 series:
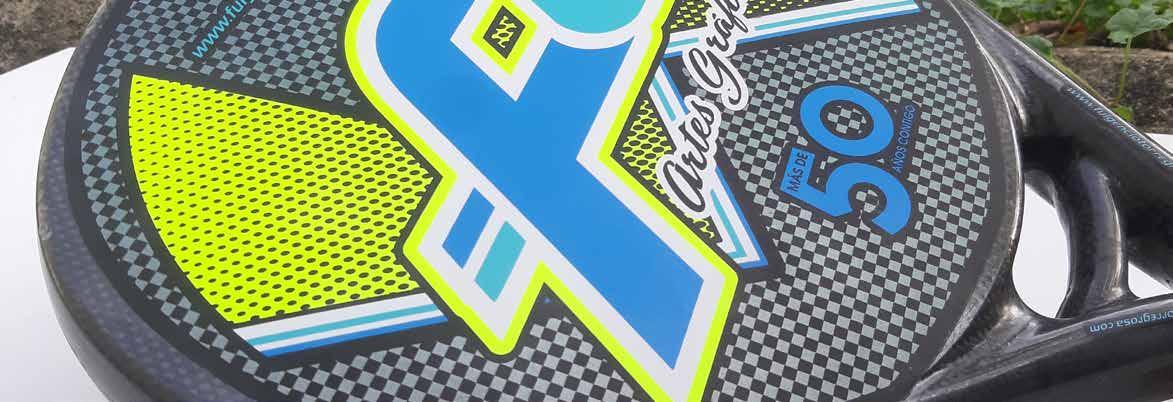
58.000 AMC Matt Bases
59.000 Colormatic Gloss Bases
58.000 Opaque Colours (16 colour shades)
58.000 Process Colours
Metallic and Fluorescent Pigments, (96.000 series)
Mixing bases
Inks: Colours
The printing sequence has to be set according to the graphical needs. It is possible to realize even the most complex graphic artworks.
Metallic and fluorescent pigments of the 96.000 series must be mixed with A31159850 – Bronze Binder in a maximum percentage of 30%. It is suggested to add also A31258911 – Flex Additive 58.911 up to 5%.
With the process colours it is possible to use A31158880 – Thixotropic Gel Toys, which allows to reduce the shade strength without modifying the typical rheological behaviour of the process colours.
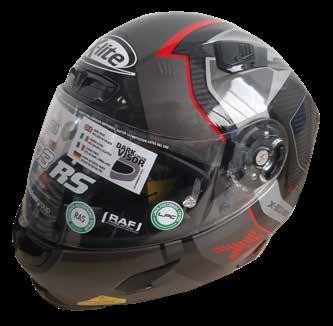
It is possible to mix the 59.000 glossy mixing bases with A31258840 – Texylon
58.840 Cutting Paste to obtain semi-matt finishing and a faster drying.
It is mandatory to wait until the complete drying of a colour before proceeding to the next one.
Inks: Transparent
For the best final result, it is mandatory to print a transparent ink. It has the function to protect the underlying layers and to allow the peeling of the upper coating.
It is possible to choose between two different products:
TEXYLON 59.800 TRANSPARENT BASE (code A31159800)
Standard transparent of the Texylon range. It is flexible, elastic and suitable for all applications.
TEXYLON OVERPRINT SOLAR SHIELD (code A31259045)
Transparent with high light fastness. It is perfect when outdoor resistance is requested.
It is suggested to print the final transparent layer 2-3 mm wider than the layers below. Always check the drying of the transparent before printing the peeling coating.
Thinners
According to the printing needs, it is possible to choose among a wide range of thinners to achieve the optimal printability:
A31890904 FAST THINNER: the perfect choice to print full-field and when quick drying is required
A31890918 SLOW THINNER: the perfect choice to print fine details or when working in warm conditions
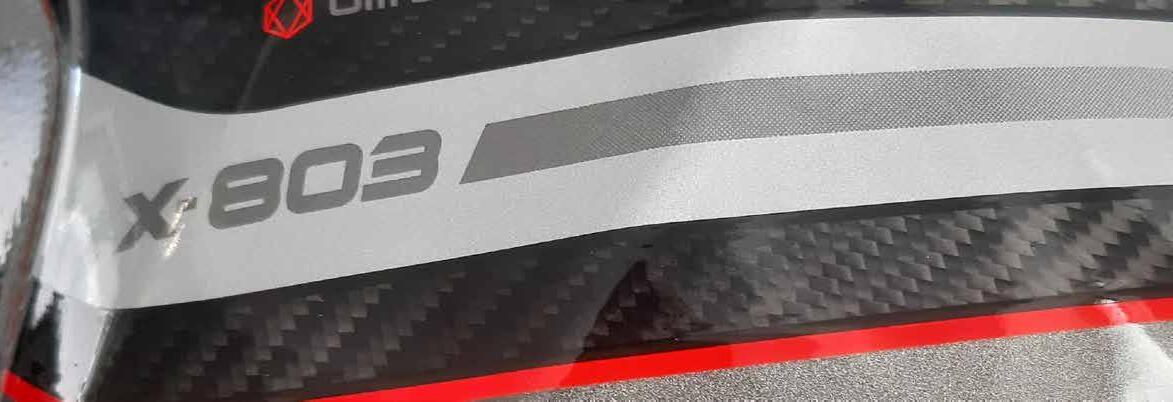
Peelable coating: Collodio
Collodio is the product that allows to easily transfer and apply the decal. Collodio can be screen-printed by covering completely the graphic artwork. It is possible to choose between two different products, depending on technical features and application processes:
PEELABLE COLLODIO C (code A31295867)
To be removed before the final spray painting of the object. It allows to obtain decals with minimal thickness, reaching a perfect integration with the decorated substrates. It is the best choice for fine artworks and high-quality production.
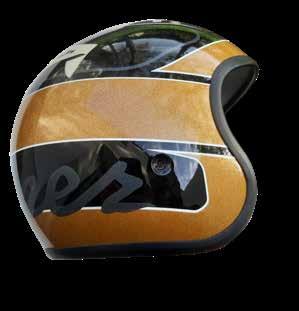
Peelable Collodio C can be screen-printed with 15 -32 threads/cm screen, one or two applications, according to the desired thickness. Collodio must be printed full-field, with an edge of 5-10 mm wider than that of the Texylon transparent.
The drying of Collodio is one of the most crucial steps of the process. Standard drying conditions are 24 hours at 25-30°C and with RH not exceeding the 60%. The full drying of the Collodio is fundamental to reach an optimal peeling.
FIX COLLODIO (code A31195869)
The Fix Collodio is not removed before the final spray painting. The use of Fix Collodio allows to avoid one application step, and it could be the best choice for cost-saving or for some special substrates.
Application of the Waterslide decals
The application of waterslide decals is a very demanding process, requiring manual skills and precision. Decals must be applied on pre-coated substrates.
CUT
the paper around the graphic artwork, leaving 2-3 mm edge
SOAK
the decals with lukewarm water for 1-2 minutes to remove the paper support
STICK
the decals on the item and spread them out with the help of a spatula
REMOVE the peelable coating after drying in the oven for at least 1 hour at 60°C
SPRAY PAINT
the object, with a solvent or UV based varnish, to protect the decal
Storage
PACKAGING
For a good storage of the decals it is suggested to seal them using a polyethylene film.
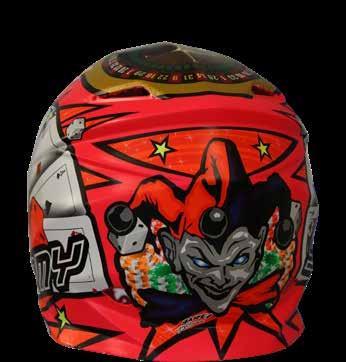
STORAGE TEMPERATURE and RH
Printed decal sheets are very fragile and could decay over time due to the thermo-hygrometric variations.
It is suggested to store the decals at a temperature of 20 – 25°C with a RH% not exceeding 60%.
The decay changes the properties of the decals or some of their components, leading to application failures. Decay processes may affect the paper and the Collodio too.
Decals printed with Texylon products, according to the technical guidelines will maintain a good applicability up to six months after the print itself.
Product range





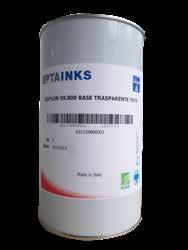
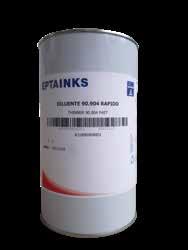
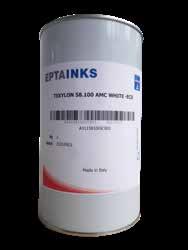
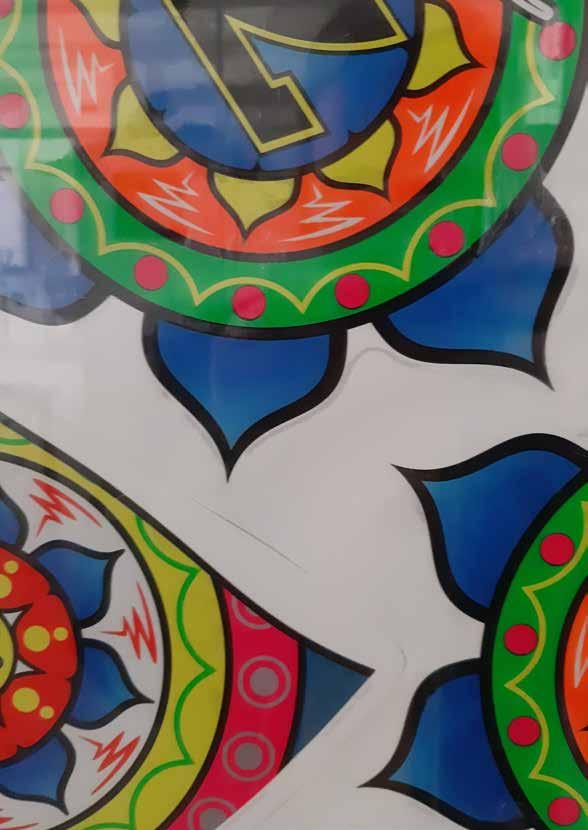


