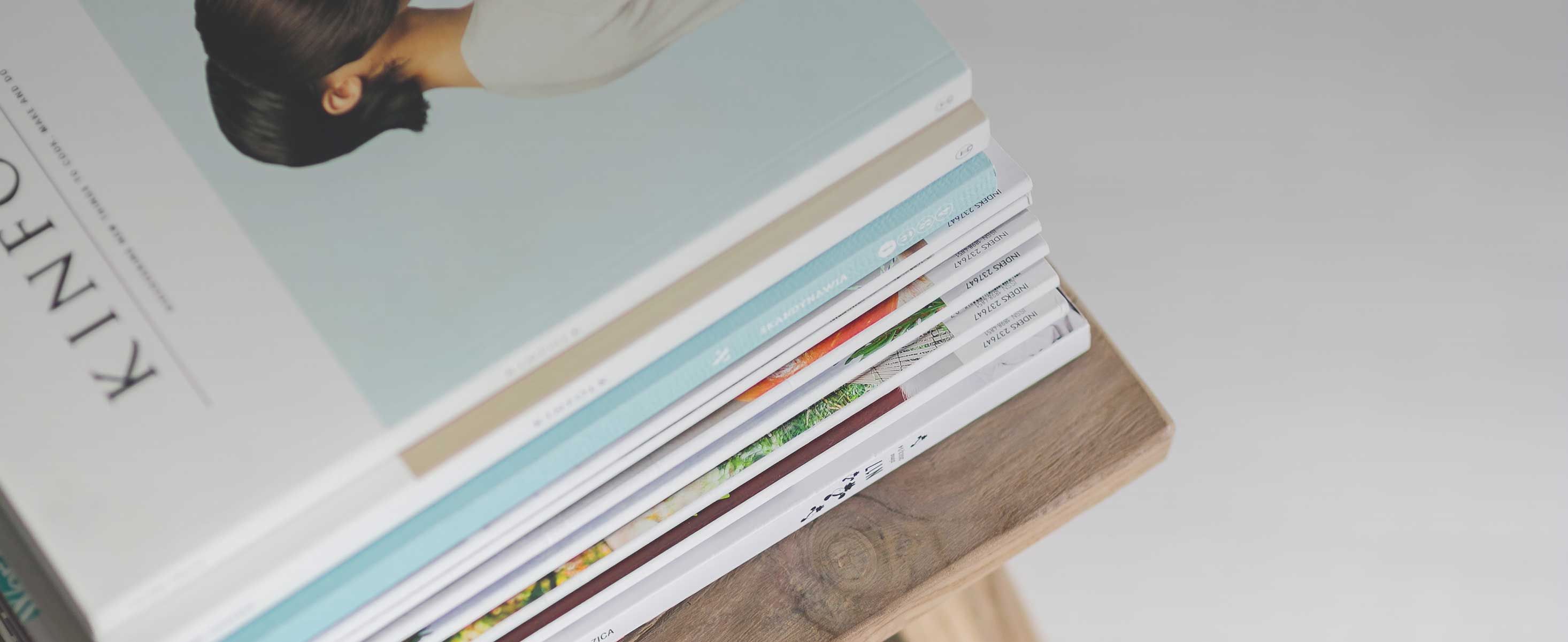
1 minute read
EASY RECYCLING OF HIGH-VALUE BATTERY MATERIALS BY SIMPLY SOAKING IN ALKALINE WATER WITH A LITTLE SHAKING
The demand for batteries has been rising alongside trends of energy transformation and net-zero emission, where major materials contained within batteries, including lithium, nickel, cobalt, and graphite, are becoming increasingly scarce and exorbitant, which is why the recycling of batteries has become an emphasis for the future. US scientists have managed to develop a li-ion battery that is not only eco-friendly and safe throughout production, but can also separate high-value materials simply by soaking it in alkaline water with a little shake and twist.
The technology developed by the Lawrence Berkeley National Laboratory allows simple separation of high-value materials and other components within li-ion batteries just by soaking them in alkaline water, followed by a little shake and twist. These separated components can then be used for new batteries after filtering and air-drying. The research team discovered the potential of quick-release binders when studying lithium-sulfur batteries. Binders are important gelatinous substances within li-ion and alkaline batteries, and are structural materials that are responsible for fixating active materials of batteries at the correct location. The research team combined two polymers, PAA and PEI that are available on the market, and connected the positively charged nitrogen atoms of PEI with the negatively charged oxygen atoms of PAA. Once the aforementioned binder is placed with alkaline water that contains sodium hydroxide, sodium ions would penetrate into the binder and separate the two polymers, which is why electrode parts can then be separated.
Advertisement
This type of binder costs 1/10 of commercial binders. Postdoctoral researcher Chen Fang believes that the particular material can also be applied on batteries of various sizes ranging from small batteries adopted for smartphones to ultra-large li-ion batteries used for energy storage grids. It is also a simpler recycling method. The existing technology requires shredding and grinding of batteries, before heating and combustion, in order to separate metals and other elements within the batteries. Recycling companies are usually driven by high-efficiency recycling, and that recycled materials would remain energy intensive and expensive, not to mention the release of toxic chemical substances that would require subsequent disposals. Gao Liu, head of the Berkeley Lab Energy Storage Center, commented that all resources, including cobalt and nickel mines, will be seeing severe shortages before a complete depletion within the next decade as the market catches up in battery demand, if batteries are being constantly burned or disposed at landfills without any recycling, which is why the recycling of batteries has now become indispensable.
Source: energytrend