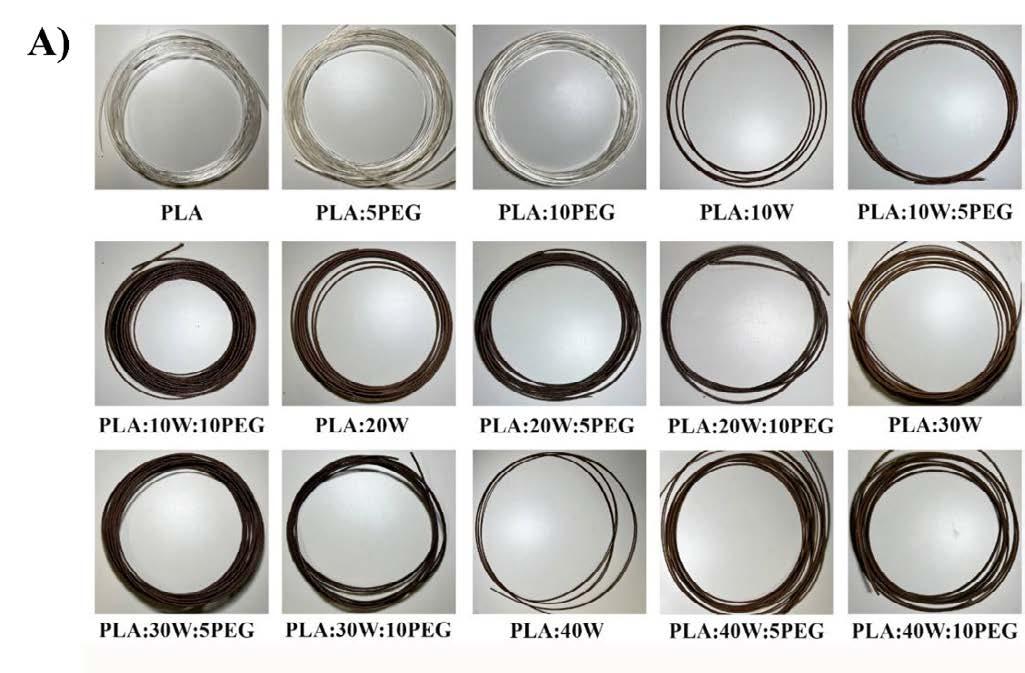
8 minute read
Material Extrusion Additive Manufacturing of Polylactic Acid-Wood Flour Biocomposite and How it
Compares with Injection Moulding
Javid Sharifi, Haniyeh (Ramona) Fayazfar
Advertisement
Department of Mechanical and Manufacturing Engineering, Ontario Tech University, Oshawa, Ontario, L1G 0C5, Canada.
Abstract. This study investigates the development of high solid content wood flour-polymer biocomposites as sustainable feedstock, using industry wood waste as natural filler and Polylactic acid (PLA) as biobased polymer, compatible with fused deposition modeling (FDM) 3D-printing and injection molding (IM). Various formulations were developed, including wood flour concentrations up to 40 wt.% and polyethylene glycol (PEG) as a plasticizer. Mechanical properties were analyzed, revealing that IM samples illustrated superior tensile strength and modulus compared to 3D-printed samples as a result of more porosity in the 3D printed parts. However, the results were comparable for 40 wt% wood and 10 wt% plasticizer for both processes. These findings emphasize the importance of optimizing 3D-printing parameters for highperformance biocomposite applications in industries such as construction and automotive.
Keywords: Fused filament fabrication (FFF); Injection molding (IM), 3D-printing; Wood flour; Polylactic acid
1. Introduction
Additive manufacturing (AM), also called 3D printing, has emerged as a prominent technology for fabrication 3D objects by layering materials, offering various advantages such as design flexibility, cost and waste reduction compared to traditional manufacturing such as injection molding (IM) [1, 2]. Fused deposition modeling (FDM), among various AM techniques, is one of the most affordable and user-friendly AM techniques, which employs extruded filaments through a nozzle with an adequate melt flow index [3].
Polylactic acid (PLA) is a widely used FDM 3D-printing material known for its sustainability and biodegradability, while suffering inherent limitations like low flexibility and brittleness [4]. To address these limitations, researchers have investigated developing PLA composites by adding fillers[5, 6]. Among others, the incorporation of wood flour (WF) to PLA matrix offers advantages like reduced material costs, enhanced compostability, while enhancing the woody aesthetic of the resulting biocomposite [6]. Wood flour, a byproduct of the wood processing industry, is shown to yield high modulus, low abrasion, sustainability, low density, low cost, and excellent biodegradability. Some studies have explored addition of WF to PLA to fabricate wood-plastic composite (WPC) feedstock for FDM [7–9]. For example, Kariz et al. [8] studied the effect of WF content on FDM-printed PLA-WPC, revealing that concentrations above 20 wt.% resulted in nozzle clogging and compromised part quality. Additionally, controversial variations in the mechanical properties of 3D-printed and IM PLA and PLA-based WPCs in literatures highlight the need for further investigation on the effects of manufacturing processes on final properties [10–12].
As such, this study evaluates the influence of manufacturing processes, FDM and IM, on the structural and mechanical properties of PLA-WF biocomposite parts. Composites with up to 40 wt.% wood filler and polyethylene glycol (PEG) as a plasticizer were developed successfully without any nozzle clogging issue, for the first time. Filaments were prepared using a simple desktop single screw extruder, and 3D-printing was performed on a low-cost desktop FDM 3D-printer without nozzle clogging. The findings revealed comparable tensile strength and modulus values for both 3D-printed and injection molded samples at 40 wt.% wood and 10 wt.% PEG concentrations. Such developed green biocomposites using the waste products of industries as natural fillers and biodegradable polymers step towards the sustainability goals to reduce the environment impact and address climate change issues.
2. Materials and Methods
PLA Luminy LX 175 from Total Corbion, PEG 400 from Sigma, and wood flour (0.3-1 mm particle size) were used in this study. Wood flour and PLA were dried at 80 ℃ before processing. Different formulations with PLA, wood (10-40 wt.%), and PEG (5 and 10 wt.%) were mixed using a HAAKE Rheomix 3000 batch mixer at 170 ℃ and 100 rpm. Then, all compounded formulations were ground into smaller granules.
Filaments were extruded with a Filabot EX2 single screw extruder at 155±5 ℃, and type V dog-bone specimens (ASTM D638) were printed using Creality Ender 3 Pro 3D printer, with a 100% infill density and 20 mm/s print speed, at nozzle temperature of 180 ℃ and bed temperature of 70 ℃ with nozzle diameter of 0.6 mm.
In contrast, a HAAKE Mini-Jet Pro injection molding unit was employed to mold tensile test specimens with two heating zones set at 200 ℃ and 70 ℃. At least five replicate specimens were created for each formulation using both injection molding and 3D-printing.
The surface morphology of composite materials was analyzed employing an Oxford Instruments Quanta FEG 250 Environmental Scanning Electron Microscope (SEM) integrated with an energy dispersive X-ray (EDX) system (Abingdon, Oxon, UK) without any sputter coating. The micrographs were provided from cross-sections of broken tensile specimens to investigate the material failure under load.
To explore the viscoelastic behavior of the formulated materials, rheological analysis was conducted using a HAAKE Mars III parallel plate rheometer (Thermo-Fisher Scientific Inc., Waltham, MA, USA) to assess the shear storage (G’) and loss (G”) moduli.
3. Result and Discussion
3.1.Mechanical Properties
Different composite formulations including different amounts of wood fillers and PEG plasticizers were successfully FDM 3D-printed and injection molded to evaluate and compare their mechanical properties (Figure 1). As per Figure 3, there were no significant differencesin the mechanical properties of 3D-printed and injection molded virgin PLA and PLA:PEG5 composites. However, PLA:PEG10 composites displayed a slight decrease in tensile strength and modulus, and an increase in elongation at break due to PEG’s plasticization effect, which caused PLA chains to slip more easily past each other, thus reducing stress [13, 14].
(B)
The addition of WF to PLA led to an increase in elastic modulus for injection-molded specimens but decreased elongation at break with minimal changes in strength. This can be attributed to adding the wood fillers enhancing stiffness while reducing ductility. For 3D-printed specimens, the tensile strength and elongation at break decreased with increasing WF concentration (10 to 40 wt.%), while the changes in modulus were insignificant. The observed differences can be linked to the manufacturing processes itself; injection molding involves high pressure, improving interfacial bonding between composite materials and resulting in enhanced ductility and elongation at break. In contrast, 3D-printing involves layer-by-layer deposition with limited interlayer bonding, leading to a more porous and irregular microstructure.
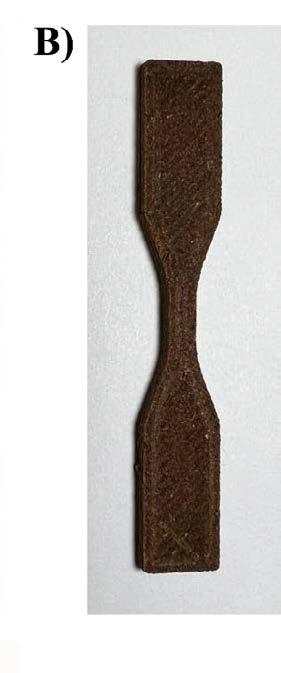
Figure 2 represents the cross-sectional SEM micrographs for both 3D-printed and injection molded PLA:40WF:5PEG samples. The images reveal voids and fiber pull-outs in both manufacturing methods. However, the 3D-printed WPCs exhibit a higher number of voids as the wood content increases, which negatively impacts the mechanical properties of the WPC composites. Additionally, the rasters of the print (indicated by white arrows) can be observed in the 3D-printed sample.
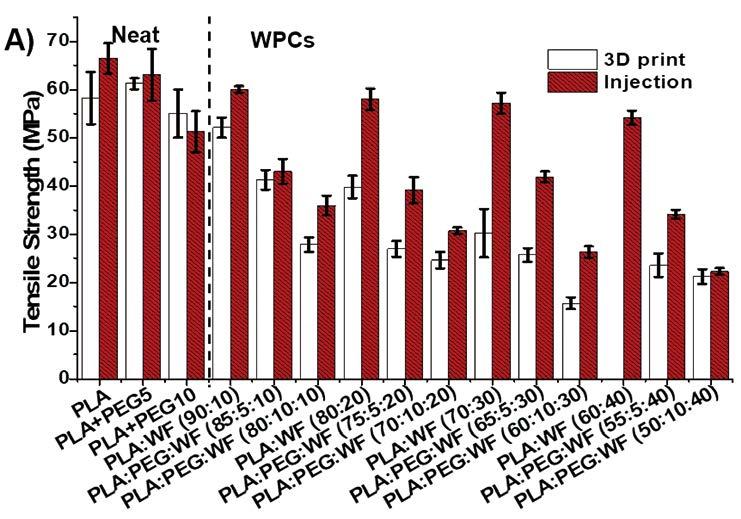
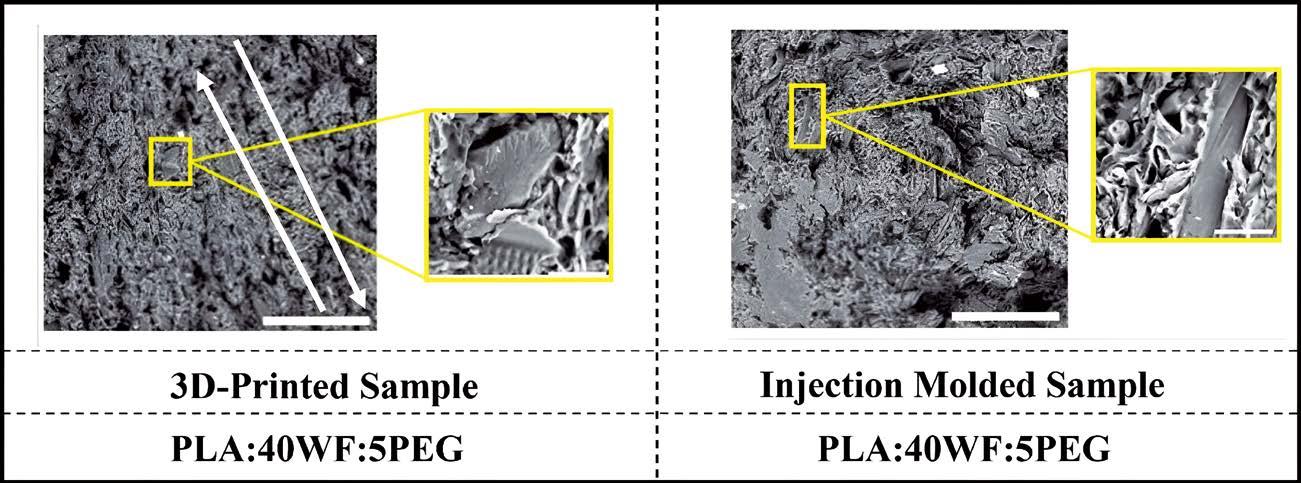
Overall, the addition of plasticizer to WPCs decreased tensile strength and modulus for both 3D-printed and injection molded specimens, with varying effects on elongation at break. Fabrication methods significantly influence the tensile properties of WPCs, with injection molded samples outperforming 3D-printed specimens, except for cases with 40 wt.% wood and 10 wt.% PEG, wherein the 3D-printing and injection molding demonstrated comparable results. To further enhance mechanical properties of 3D printed parts, optimizing 3D-printing parameters such as raster angle, nozzle temperature, flow rate, and printing speed is crucial, as this can improve stress transfer and fusion between print lines, which is under study.
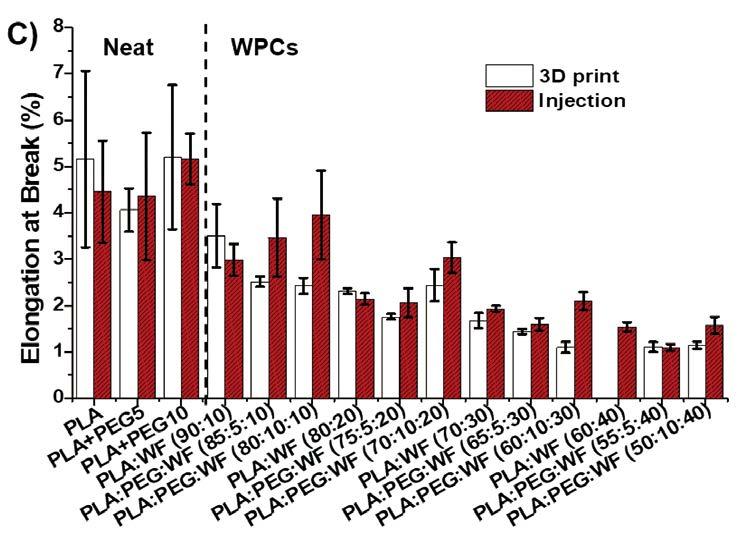
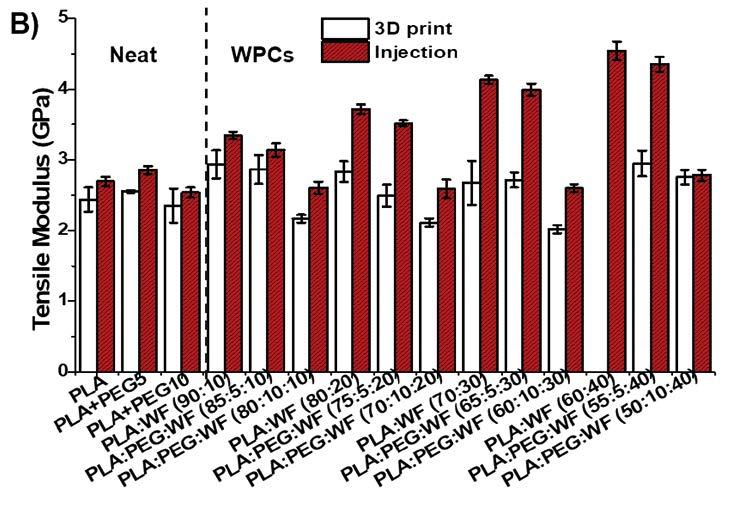
3.2. Rheology analysis
The rheological behavior of different feedstock materials showed that (Figure 4), the storage modulus decreased as PEG content increased for all angular frequencies, with the most significant reduction observed at 10 wt.% PEG. At low and intermediate frequencies, PLA, and PLA+PEG exhibited liquid-like behavior, as the loss modulus (G”) surpassed the storage modulus (G’); however, at higher frequencies, a crossover point emerged where G’>G”, indicating solid-like behavior. The incorporation of wood increased the moduli values, as the composites became more resistant to deformation, but the trend concerning G’ and G” crossover points remained consistent. The sole exception is the PLA:PEG:WF (50:10:40) formulation, where the storage modulus exceeds the loss modulus, suggesting that WF particles are agglomerating and separating from polymer resin due to minimal plasticized PLA inclusion and a decrease in its molecular weight.
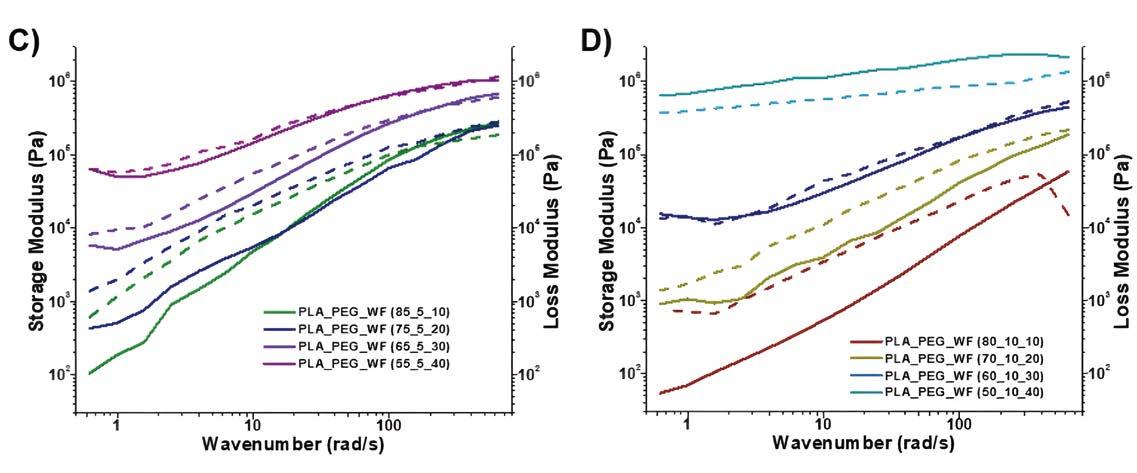
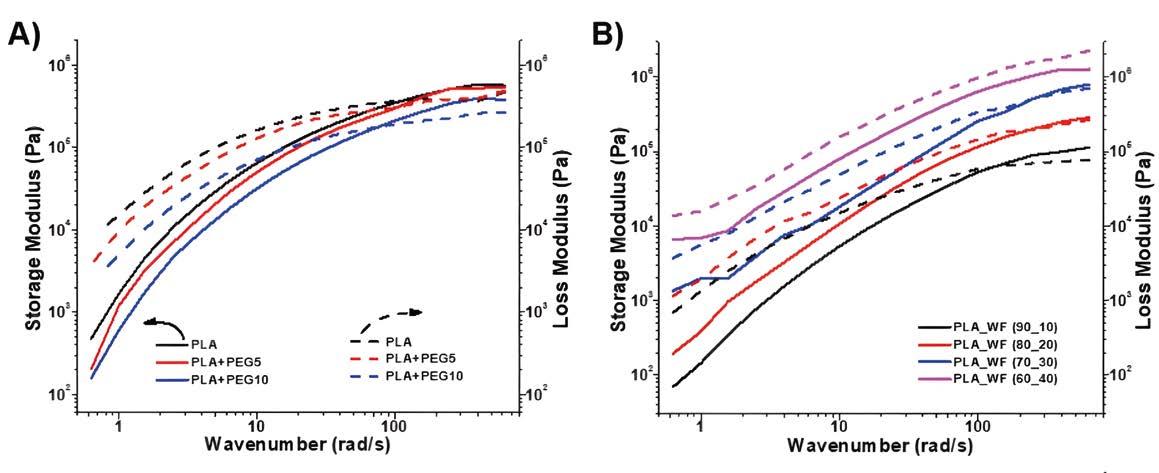
4. Conclusion
This study examined the influence of different manufacturing processes on the mechanical, rheological, and microstructural properties of virgin PLA and high-solid-content PLA-based wood composites. Composites with up to 40 wt.% wood filler and PEG as a plasticizer were developed successfully without any nozzle clogging issue, for the first time. The incorporation of 10 wt.% PEG plasticizer resulted in a slight reduction in tensile strength and modulus for both 3D-printed and injection-molded specimens, while elongation at break increased. Injection-molded samples displayed greater tensile strength and modulus in comparison to 3D-printed ones. However, the results were comparable with 40 wt% wood and 10 wt% PEG for both manufacturing processes. The findings underscore the significance of 3D-printing parameters optimization (e.g., nozzle and bed temperature, infill density, print speed, orientation) using a methodical and systematic design of experiment to produce highquality 3D printed biocomposites without porosity and defects, suitable for demanding applications such as construction, automotive, and sustainable packaging. Additionally, it is worth developing feedstock formulations with more suitable physico-mechanical properties by optimizing wood distribution in polymer matrix and utilizing more efficient compatibilization agents alongside plasticization.
References
1. Fayazfar H, Sharifi J, Keshavarz MK, Ansari M (2023) An overview of surface roughness enhancement of additively manufactured metal parts: a path towards removing the post-print bottleneck for complex geometries. Int J Adv Manuf Technol 2023 1253 125:1061–1113.
2. Tamez MBA, Taha I (2021) A review of additive manufacturing technologies and markets for thermosetting resins and their potential for carbon fiber integration. Addit Manuf 37:101748.
3. Penumakala PK, Santo J, Thomas A (2020) A critical review on the fused deposition modeling of thermoplastic polymer composites. Compos Part B Eng 201:108336.
4. Yang TC, Yeh CH (2020) Morphology and Mechanical Properties of 3D Printed Wood Fiber/ Polylactic Acid Composite Parts Using Fused Deposition Modeling (FDM): The Effects of Printing Speed. Polym 2020, Vol 12, Page 1334 12:1334.
5. Aida HJ, Nadlene R, Mastura MT, et al (2021) Natural fibre filament for Fused Deposition Modelling (FDM): a review. https://doi.org/101080/1939703820211962426 14:1988–2008.
6. Yu W, Li M, Lei W, et al (2022) Effects of Wood Flour (WF) Pretreatment and the Addition of a Toughening Agent on the Properties of FDM 3D-Printed WF/Poly(lactic acid) Biocomposites. Mol 2022, Vol 27, Page 2985 27:2985.
7. Tao Y, Wang H, Li Z, et al (2017) Development and Application of Wood Flour-Filled Polylactic Acid Composite Filament for 3D Printing. Mater 2017, Vol 10, Page 339 10:339.
8. Kariz M, Sernek M, Obućina M, Kuzman MK (2018) Effect of wood content in FDM filament on properties of 3D printed parts. Mater Today Commun 14:135–140.
9. Narlıoğlu, N., Salan, T., and Alma MH (2021) Properties of 3D-printed wood sawdust-reinforced PLA composites. BioResources 16:5467–5480
10. Ecker JV, Haider A, Burzic I, et al (2019) Mechanical properties and water absorption behaviour of PLA and PLA/wood composites prepared by 3D printing and injection moulding. Rapid Prototyp J 25:672–678.
11. Selva Priya M, Naresh K, Jayaganthan R, Velmurugan R (2019) A comparative study between inhouse 3D printed and injection molded ABS and PLA polymers for low-frequency applications. Mater Res Express 6:085345.
12. Komal UK, Kasaudhan BK, Singh I (2021) Comparative Performance Analysis of Polylactic Acid Parts Fabricated by 3D Printing and Injection Molding. J Mater Eng Perform 30:6522–6528.
13. Sukthavorn K, Nootsuwan N, Veranitisagul C, Laobuthee A (2022) Development of luminescence composite materials from poly(lactic acid) and europium-doped magnesium aluminate for textile applications and 3D printing process. Polym Compos 43:6637–6646.
14. Rogovina SZ, Aleksanyan K V., Loginova AA, et al (2018) Influence of PEG on Mechanical Properties and Biodegradability of Composites Based on PLA and Starch. Starch - Stärke 70:1700268.
Dr. Ramona (Haniyeh) Fayazfar, PhD, P.Eng., is an Assistant Professor at the Department of Mechanical and Manufacturing Engineering at Ontario Tech University. Dr. Fayazfar received her Master’s and PhD degrees at Sharif University of Technology. Prior to joining Ontario Tech, she was a postdoctoral fellow in MultiScale Additive Manufacturing research group at the University of Waterloo. She has more than 20 years of experience in developing novel multifunctional composite materials, advanced manufacturing, sustainable energy, and 3D printing. She has been actively involved in several industrially sponsored projects for aerospace and automotive applications with Burloak Technologies (Samuel, Son & Co.), Lockheed Martin, Toyota Motor Corporation, Rio Tinto Company, NRC, etc. Her current research concentrates on addressing current challenges of AM with a focus on development and optimization of novel AM-specific categories of materials for low-cost point-of-need additive manufacturing of recyclable and sustainable products. Also, her research works aim to address critical challenges facing the industrial adoption of AM for example in aerospace and tooling manufacturing and biomedical devices. To this end, new engineering advanced materials compatible with AM have been designed, developed, and characterized in her group to expand the range of possible products and enhance performance outcomes for end-use applications.