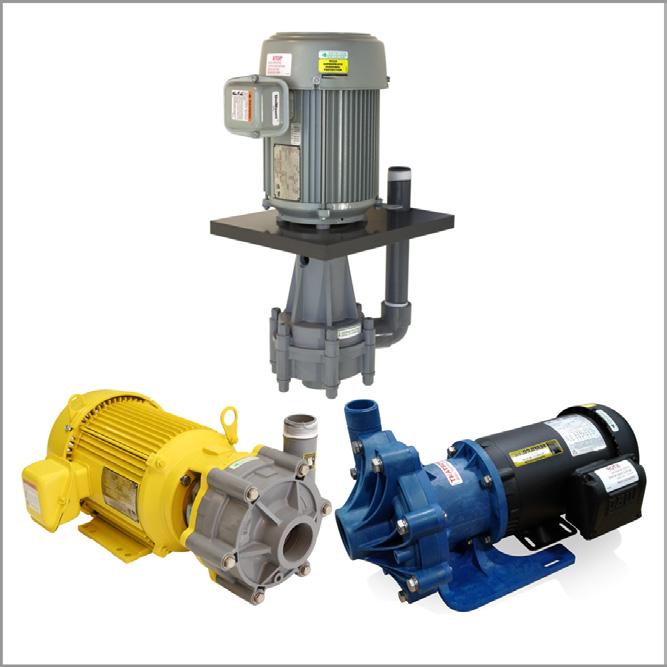
2 minute read
Examining the basics of pump selection
By Chadi Halahel
Pumps are used in virtually every facility across the world and have become a commodity and a critical piece of equipment for almost any means of production. Every sector directly, or indirectly, relies on this equipment to operate. So, it is important to understand how to select the right equipment for each application.
Every application differs and with growing technology, there are dozens, if not hundreds of options to choose from for each application. However, there are some options that are much more efficient than others. Selecting the right pump will lead to energy savings, lower maintenance costs, process improvements, and a significant reduction in risk of system failure.
Some of the more common types of pumps are electrically driven by a motor or by air. Some examples of these are horizontal mechanical seal, magnetically coupled, vertical, air operated double diaphragm and metering pumps. Each one of those pump categories can be broken up into subcategories based on the construction material and internal components. Material selection is a very important part of pump selection, as the incorrect one can heavily impact life expectancy, or even lead to instant failure.
Every pump is selected based on three important factors. Without knowing them, selection will be inaccurate, and the desired results will very likely not be achieved. The required flow rate, total dynamic head, and fluid properties must be known.
Flow rate is how much fluid must flow through the system in a given period of time, typically dictated by gallons per minute (GPM) or litres per minute (LPM).
Total dynamic head is the height that a fluid is to be pumped, and friction losses in the pipe. It is typically calculated in feet of head (FT) or PSI.
Lastly, the fluid properties of the liquid being pumped need to be known. These include chemical properties, heat, concentration and specific gravity. Some processes are not purely liquid-based and contain solid matter, so applicable solid sizes need to be factored in.
Due to the complexity of the equipment and the required application information, pump manufacturers need authorized distributors to be trained by them in selecting, assembling, repairing, and warehousing. This allows distributors to be able to successfully supply end users with the right equipment.
Every application is unique, and each facility has different requirements, so the end user will have many options to consider. Authorized pump distributors have a better understanding of what type of pump is required for the application. They should be able to recommend options for the end user to consider for their application to operate efficiently.
Pumps are used in virtually every facility across the world.
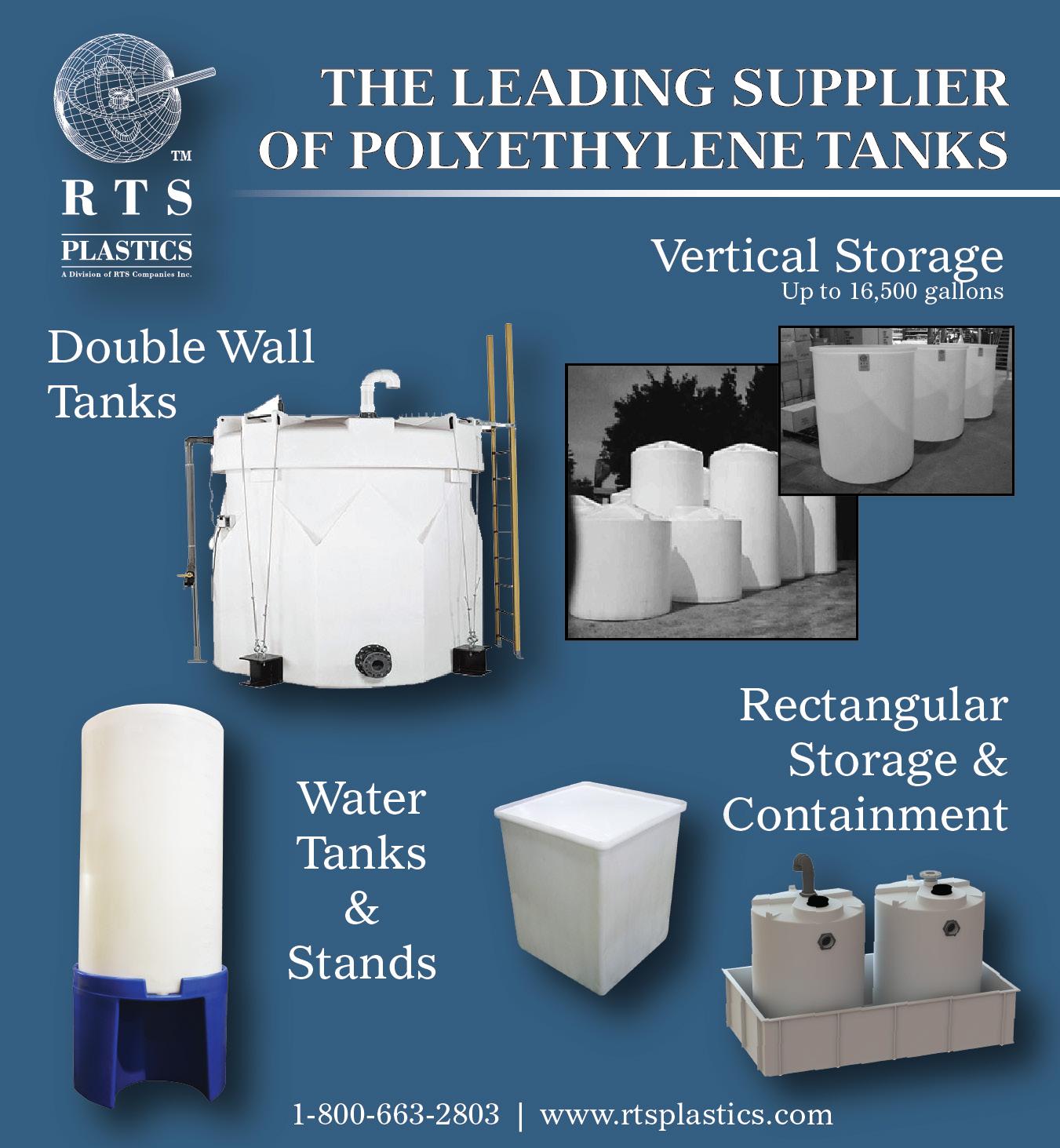