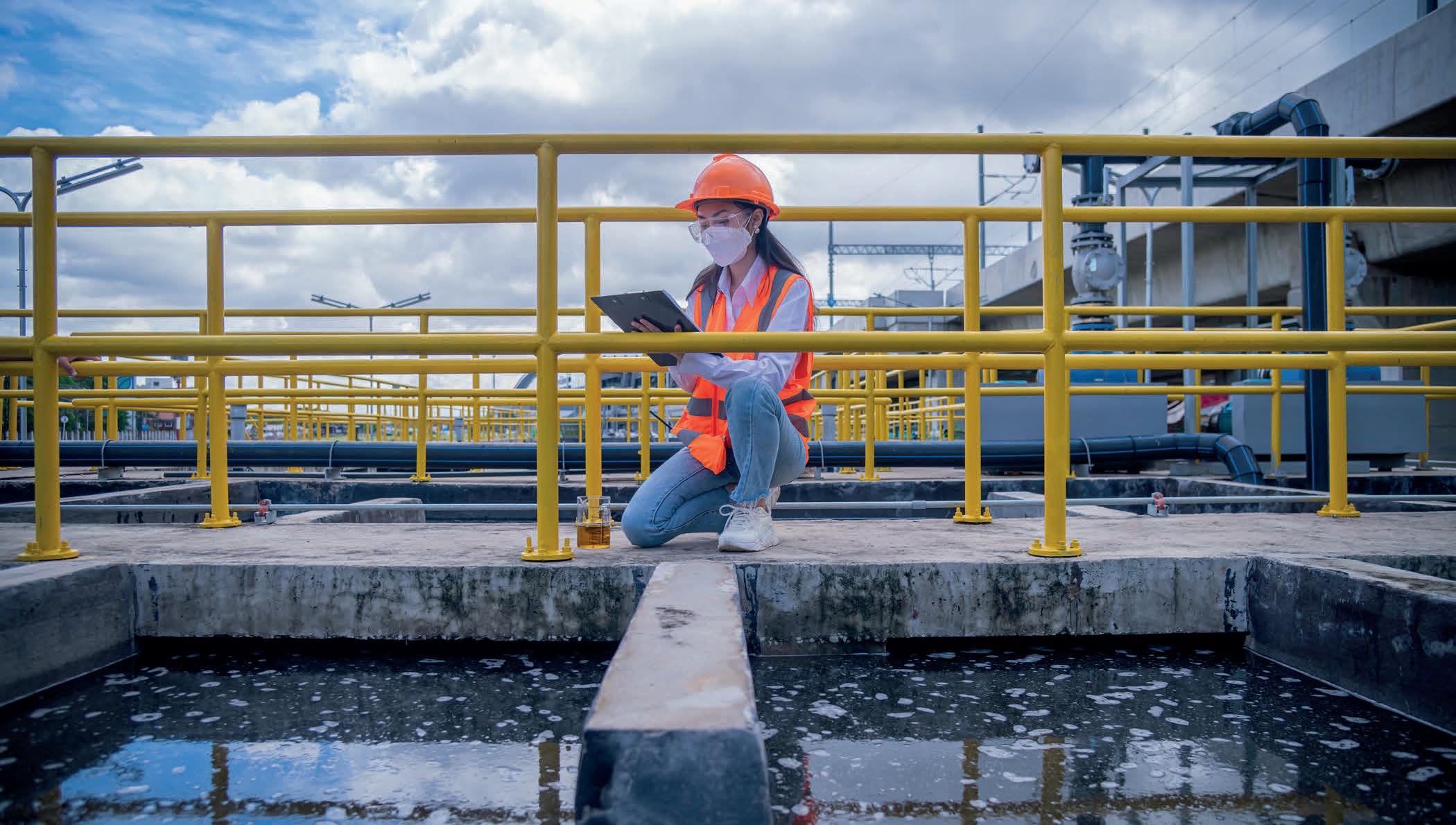
3 minute read
The benefits of using connected safety devices in water, wastewater facilities
By Julian Jarvis
Every industry has gone, or is going through, a digital transformation, and the water and wastewater industry is no exception. Connected technologies have proven valuable for improving operational efficiency and making regulatory compliance more accessible in many industries.
How we keep our workers safe in the water industry is also evolving. While the safety of workers and facilities is the primary concern, connected devices can provide additional benefits from data collected, such as improving productivity, highlighting trends, and lowering the likelihood of future incidents. From data insights, the water and wastewater industry can avoid unplanned downtime, increase efficiency, and mitigate unnecessary costs.
WHAT IS A DIGITAL WORKSITE?
A digital worksite leverages data from connected Internet of Things (IoT) devices throughout an organization. These insights can help water and wastewater organizations understand where productivity losses or bottlenecks are occurring across their operations. From here, proactive decisions based on real-time information can focus on measures to improve productivity, safety, and profitability.
This can save time during maintenance procedures, help get assets back online faster, and add potentially millions in revenue that otherwise would have been lost.
For example, equipping each worker with a connected safety monitoring device, like the G7 from Blackline Safety, provides valuable data to keep personnel safe throughout the entire facility or out in the field. These wearable devices not only alert users and monitoring personnel to the presence of harmful gases, but also indicate the location of individuals that need assistance.
But there are additional benefits beyond the immediate safety concerns. The integrated location tracking capabilities of a connected gas detector means that if a worker is exposed to hazardous air, supervisors are alerted in real time of their precise location and the gas levels encountered in the area. This results in a quicker response time and a more prepared response.
Connected gas detectors also record non-alert level exposures. This data can be used to proactively identify possible leaks so that repairs can be done before a serious incident occurs.
There are additional safety needs for lone workers in the field as well as workers in large facilities, such as multi-floor pump stations where tasks put workers beyond sight and sound. Connected devices provide a lifeline for these work- ers to call for help by pulling an SOS latch, or automatic fall and no motion detection, and missed check-in alarms.

Data analysis can uncover patterns from incidents and highlight areas of safety concerns so that proactive measures can be taken. For example, a high frequency of fall detection alarms in one area of a treatment plant may indicate a water leak is making the area slippery.
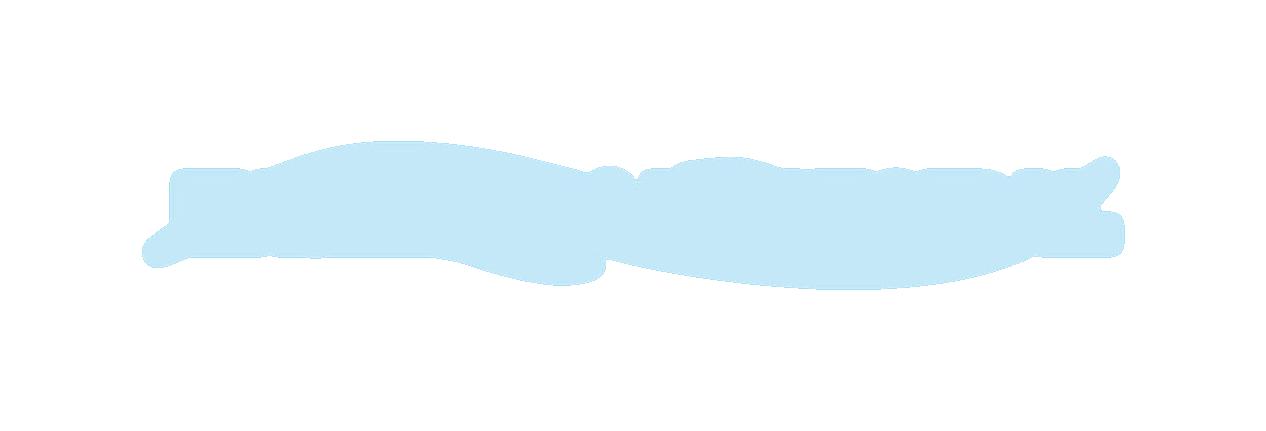
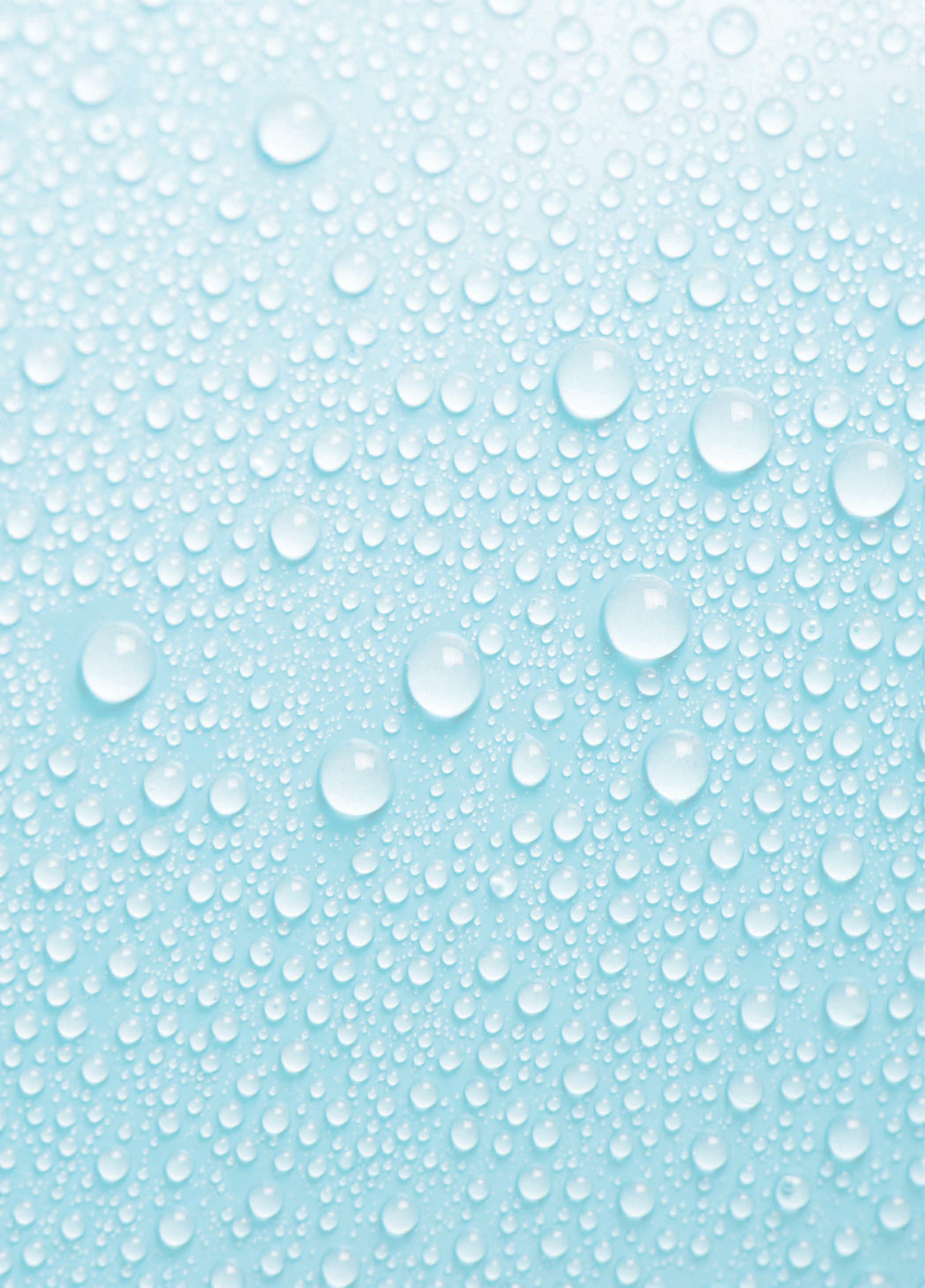
If it only happens in the winter, it could be due to a seasonal icy patch that requires a higher traction surface or deicing.
Hazards And Risks Of Confined Space Entries
To ensure safe working conditions, confined spaces require both pre-entry and continuous gas monitoring. Blackline’s wearable G7 Multi-Gas Pump detector’s pre-entry mode can be used to sample the air quality of a confined space before access. It can then be put into diffusion mode, to continuously monitor the space while workers complete the job.

The detector can also uncover trends from the data for future confined space work that may indicate unexpected sources of toxic or combustible gases that require additional maintenance.
Deploying area monitors throughout a treatment plant allows safety operators to measure changing atmospheric conditions, even when workers wearing personal gas detectors are not present. Setting up a fence line perimeter ensures the safety of the facility and surrounding areas.
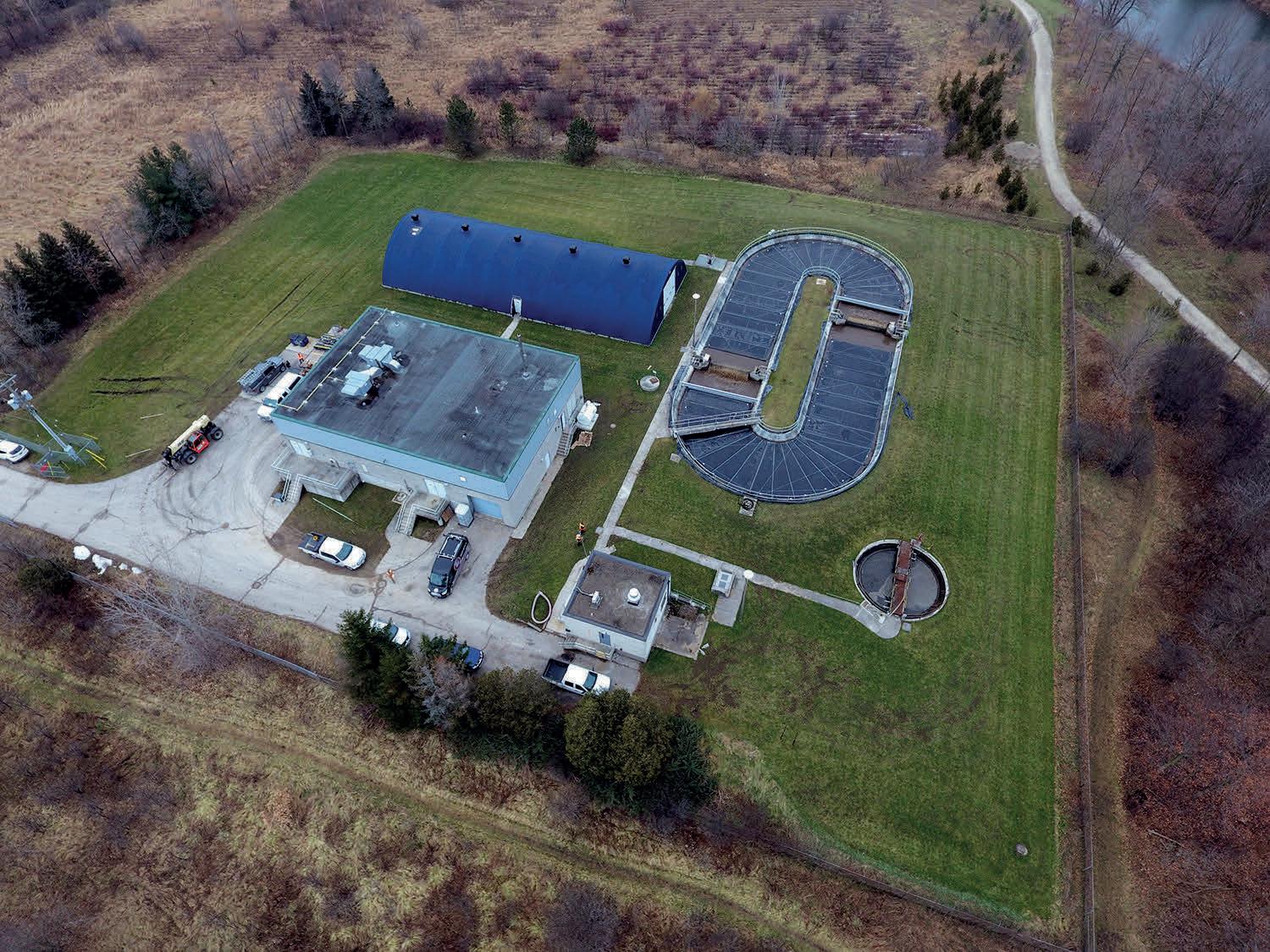
Open path and fixed monitors are limited by location with the need for installation and a direct power source, whereas portable area monitors with a 100+ day battery life have the flexibility to be moved quickly anywhere on site.
If conditions change, a potential hazard is identified, or plant operators want to sample another location, area monitors can be easily moved as often as needed. This flexibility can also benefit wastewater facilities with odour complaints from the public. Operators can quickly relocate devices in response to air quality concerns with quantitative, real-time data, and then share that information with government agencies as needed via an online dashboard.
Conclusion
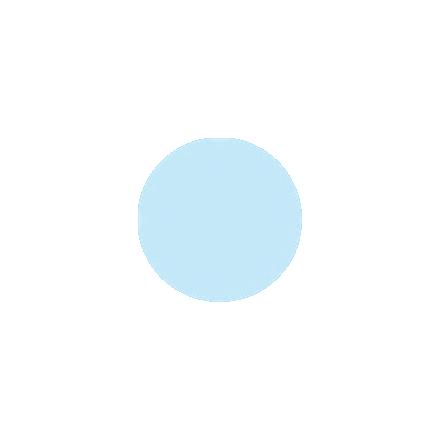
Connected safety devices accomplish the crucial task of helping to ensure the safety of workers, facilities, and the surrounding areas. But, the data collected can also present additional benefits, such as low-level exposures indicating a leak, facility maintenance issues, and trends to aid confined space work, all with real-time visibility. Ultimately, these insights allow engineering and operations teams to reduce unnecessary costs, improve efficiency, and prevent future safety incidents.
Julian Jarvis is with Blackline Safety whose Canadian office is in Calgary. For more information, email: mirvine@blacklinesafety.com