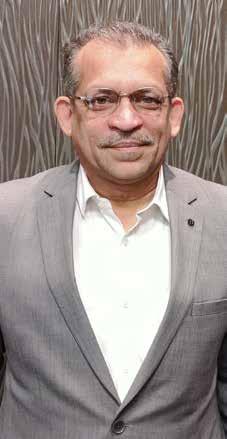
20 minute read
Embracing E-mobility: Q&A with Sajid Mubashir, Scientist G, Dept. of Science and Technology
by ETNews
The development and research on energy storage technologies is the key for widespread electric mobility and adoption of renewable energy. Keeping in mind this target, the Ministry of Science and Technology has led several energy initiatives through Dept. of Science and Technology (DST). ETN spoke to Sajid Mubashir, Scientist G at DST and membersecretary of the new DHI-DST Technology Platform for Electric Mobility (TPEM), to learn more about the efforts underway to make India a leading developer in energy storage technologies.
Advertisement
Q: DST’s energy initiative aims to develop national capacities and capabilities in research-led clean energy and energy-efficiency options and the program research spectrum also include energy storage technologies. Can you share what approach DST is taking to enable India to become
a leading developer in advanced energy storage technologies and what’re the specific initiatives in this regard.
A: The DST is doing a lot of activities, in short, it is developing capabilities in the country in terms of energy security. I would not be able to enumerate all the programs at DST, but I can speak on one important aspect and that’s electric mobility. I have been active for more than two decades in this area of automotive research now so we try to do consortium projects and by 2011 we narrowed down on electric mobility as a major activity to take up so the DST was involved in the formulation of FAME I mission. In fact, that program had 20 percent money reserved for R&D. That means out of the 800 crores, 160 crores were set for R&D and the slogan was use that 20 percent money to get rid of the 80 percent subsidy. So, we tried to do that, but it didn’t work. But now, we are developing a very focused EV R&D program; it’s still in works. Other than this activity there are a whole lot of programs in DST in the energy storage space such as grids, some basic work and more but they are too many to enumerate.
Q: How will DST’s program assist in manufacturing of advanced storage technologies in India? Especially, how can the Indian industry engage in these efforts.
A: If you look at the FAME mission with its three years condensed program and with the ambitious outlay of 10,000 crores, it still talks about everything being made in the country. I think the benchmark is that at least 50 percent of the things should be manufactured in the country, which is a tall order because many of these things are not disaggregated – you cannot take the battery out and have some parts developed in India and some from outside. The manufacturing process doesn’t work like that. If we take the basic component and assemble, to some extent, we can do indigenous effort but beyond that it is difficult. There is a need for major R&D.
Akin to the Himalayas that have protected us from outside influences all our history, in the electric vehicle moment, I think this hot tropical climate is what will save us. No vehicles which developed outside can be brought directly to India and expected to be a success. Just the fact that our tropical climate is much different than the operating conditions the vehicle was originally built for makes everything different. Expensive vehicles are still fine, they can be cooled. But there are many things to be cooled – there’s the battery, power electronics and motor. You would need to do a lot of expensive cooling.
For India, therefore, we may have to redesign things. At least the battery should be made more
temperature resilient and that can be done if only we can do something about the electrodes and electrolytes, which means relevant research.
We have a program where we’re starting this mission where such sellable work with clear intent of a tropical EV battery is the goal. And now performance parameters, energy density, and other things are left to the partners. We’re just keeping one condition: these batteries should operate at 50 degrees temperature without having a cooling system. That’s the kind of goals we’re setting.
Similarly, we have set goals for motors and power electronics.
So, that’s what the mission is about, and the intent is to support component manufacturers in the automotive sector and also in the electoral and electronics sector.
Q: Several Indian research institutes have generated intellectual property in the field of advanced energy storage technologies with the support of the Ministry of Science and Technology and Ministry of Electronics and Information Technology (MeitY), how will this EV R&D mission help in industry-academia connect and the commercialization of these technologies developed by these lab?
A: We have to match with the requirements. Now the big constraint we have is this big accelerated program, the FAME mission itself is three years which is very tough thing to address if you’re talking about new technologies. Therefore, we need to find mechanism to find mature technologies in India, mature means being confident that these will work but many things have to be done to make it operational in field conditions. So, these I will call technologies at level 6. There is this technology readiness level index, it’s a scale of 10, as per that technologies which have reached level 6 in the Indian laboratories would be one set of projects we would like to do. We would like to associate with the industry, create large consortium projects, provide facilities for that. For example, pilot production facilities, test benches and a whole lot of other efforts. For example, for every vehicle segment try to create 10-20 battery packs with new technologies and try it on vehicles and prove it. So, it is towards commercialization of these technologies which are at level 6.
Now, in some areas, we may have a desire for it to happen but may not have developed it in the country. In that case we are open that if agencies outside are willing to come here and work with us and move it from level 6 to level 8 but this alone won’t do the job. This is just harvesting, unless there is something to harvest, we will have to have a program where we would support directed research, here the word ‘directed’ is important, means from level 3 to level 6. We will certainly not go below level 3 as they would mean too much of a research and we cannot do that here. The DST does it anyway (its main program is up to level 3 and level 4). We are hoping there will be harvest of potential technologies and sometimes it is needed to collaborate with China, U.S. and Japan to move all those technologies from level 3 to level 6. The main component is level 6 to higher levels and a supportive, directed research program from level 3 to level 6.
Q: Globally, large part of development work for this technology is also happening in small companies and startups, so will this mission also support startups and existing component manufacturing to participate in this innovation program?
A: We must touch upon the concept of technology transfer here. It is very rare to be able to transfer a complete technology because technologies are so complex. It is not possible to transfer it unless it is a major globally leading facility like the Fraunhofer Society of German no one is able to say that they will develop everything and give it off. And that has been the failing here, we expect our CSIR labs, university professors to develop everything and give it, it is not possible. Things are too sophisticated. There are various talents required, some of the talents must come from the user agency, some from the component industry and some, of course, from the professor. They all must work together. So, in that consortium, there is a good space for startup companies to come in, companies with technology abilities, for example, if something has to be modelled or some prototype has to be developed or a small contract has to be done about a cooling system for instance these projects can be subcontracted to these agencies so these are incubators but we are not incubating the startups. We are incubating the technology part of it though.
This incubation will also include existing SMEs who are good in these areas and the contract given to them will be considered so it’s an incubation program but it’s not relating to the business part and these contracts since they’re given to companies and we’re pursuing them to do a specific work for the mission, some built-in profit would be there for them, let us say 10 percent or 12 percent profit will be assured for them so that’s how we plan to include SMEs and startups.
Sometimes a startup has an exciting technology, in that case, it is not a subcontracting model but they’ll become the centerpiece, therefore, it depends on what is available.
Another important thing is that these projects have partnerships, supporting agencies can also have a lot of partnerships. For example, there could be VC fund and an agency like the World Bank who wants to introduce something, they’re welcome to partner. The idea is the venture part should be taken care of by the partnering agency since DST doesn’t know the business-side much but the technology-side will be taken care by us.
Q: What about the funding mechanism, what kind of funding is envisaged for this program?
A: It’s a mix of activities which require different kind of funding. Something at a pilot level, which is trying to prove the commercial-worthiness
of a technology and the product process can’t be a governmentcontrolled effort. First of all there is a lot of equipment and machinery and all that so if there’s a government property it creates a problem so it is best that those are done by the companies but at the same time there’s also risk involved in it, it could be a pilot which is not going to be so profitable so there is a certain money required from the government to de-risk their effort. I would say certainly it is below 50 percent of the pilot program and everybody put together -- the other agencies can bring that thing because it then makes it free of government-control. If government investment is 50 percent or more then it is practically government property that’s what our rule book says.
So, thing like a pilot plant or test bench we should stick to less than 50 percent of government for this reason. Further this provides companies’ ability to run the management partly maybe and then the government can support such joint ventures. That is one way.
The other way is there are directed research programs that we will take complete ownership of and we will try to fund it as much as we can but there too it depends on what kind of projects. It may not be good if the government funds all of it because then nobody would want to have it. There has to be stake and ownership, there also the government would support more of the directed research, then if there are collaboration abroad then that also is a major government responsibility, test benches could be provided by the government – so these are the broad things.
However, the main things is not the funding mechanism, it how the fund would be administered. There we are making a big difference; we have never tried it so far. What we’re seeing is DST will not manage it directly, we will try to create a hub from among the participants and we’d ask them to manage it. Create a board, take ownership, have formal structure, manage the show, and if there is an audit they need to manage that as well. We want to give that freedom and flexibility, in that sense what we want to say is that there could an energy storage hub – all of energy storage research activity could be administered centrally by some place, some organization, which would issue calls, evaluate proposals, and give out money and it also holds members/ companies who’d contribute money be able to absorb it, to be able to give small subcontracts to smaller companies or startups. All that the hub should do, it’s a new structure that we all want to create, we don’t have much precedence but we hope that we can create one for energy storage which will include also include super capacitators, batteries among other things. Another hub would be for motor and motors and drive research which includes a magnet producing facility. Third would be for power electronics and control and among these the first two look very promising.
Q: We have seen that governmentindustry partnership work well in U.S., Japan and Korea and as you said in India we haven’t seen too many success stories of G-I partnership with applied R&D while there are so what can we learn from past experience and in your view what role can groups like IESA can play to facilitate this initiative further?
A: The organized collaboration of industry and academia is not all that common even in the western countries, most of it happen as individual efforts by individual companies and labs but the culture of collaborative work came from Japan. There must have been a thousand of projects that MeitY funded and the Japanese competitiveness became so strong that the U.S. started to follow the consortium process. They implemented it for 10 years or more. The Koreans have consortium program as well. Now these are implemented as per their culture say Japanese industry there are many small industries, so they all get together, like the Hyundai or the Toyota; they don’t kind of cross supply. In fact, the consortium will also have a bank embedded. We don’t have that culture.
I think in India, we still don’t know what will work, but our expectation from DST is that an agreement is not enough. People tend to forget what was written in the agreement and then it becomes a problem. So, more of a formal structure, a joint venture company we’re exploring to hold all these people together in a program. So, one major project, if there is a large project let’s say a large battery project we’d like to do. There must be 20/30 vehicles packed with these batteries coming out finally. There’ll be component companies, research labs, they all could form a company this is what we’re hoping. We still don’t know how they will all respond but from the government-side we’re hoping they could form a jointventure company, may be a specific R&D company which is not allowed to get into production because that becomes a different issue. That becomes a cartel. We’re only talking about joint development, after that people take their technology and go their way. So, during the phase of development, they should be able to sit in a company structure and may be after five/ten years they can dissolve the company or continues.
As far as the role of IESA, IESA can help us form such a company where you yourself are a partner to manage that program.
ADVERTISE IN ETN GROW YOUR NETWORK Contact: Ashok Thakur - M: +91 9819944543 E: athakur@ces-ltd.com

IESA
India Energy Storage Alliance
YOUR GATEWAY TO INDIA'S ENERGY STORAGE, EV AND MICROGRIDS MARKET
Join IESA to gain insights and access to one of the fastest growing energy storage, microgrid and EV markets.
Cell Manufacturing in India: challenges and opportunities
Is India doing enough to encourage domestic manufacturing of advanced battery technologies? Through conversations with many Indian industries who are active or planning to play an active role in this space, it was found that there are many widespread apprehensions. This article intends to list and present viewpoints, keeping in mind the growth of the cell manufacturing industry in other parts of the world.
The world is undergoing a massive transformation in one of the most key aspects governing our lives - Energy. The generation, availability, and use of energy supports all dimensions of our existence. Food production, processing and delivery, infrastructure development, clothing industry, transportation, healthcare and any other activity crucial for our sustenance depends on energy. Over time we have become used to depending on fossil fuels for providing us this key ingredient which supports our society. It is this core enabler which is undergoing transition.
India has shown its commitment to this transition by scaling up deployment and long-term ambitions in renewable energy. It’s important to understand that using renewable energy sources not only reduces our carbon footprint, but it is also minimizes our dependence on imported sources of energy, which are a huge drain on our foreign reserves. A chief enabler for making all this happen is energy storage or batteries.
Seeing the imminent demand, it is no surprise that globally the battery industry is swiftly moving towards scaling up their manufacturing capability. A significant portion of research funding is being directed towards development and commercialization of advanced battery technologies through various government sponsored programs.
The question to ask here is whether India is doing enough to stay relevant in this competition and hopefully play a leadership role.
Evolving technology landscape and effect of changing chemistries on existing manufacturing facilities
Li-ion batteries are well adapted for EV applications due to their high energy density. Emerging chemistries are moving towards high nickel and reduced cobalt content due to limitations in cobalt availability and price volatility. Next generation of Li-ion batteries will have solid electrolytes which will permit the use of lithium metal as the anode leading to approximately 25-30 percent improvement in energy density at cell level.
One of the main concerns among industry players is whether new emerging chemistries in this space will cause existing manufacturing facilities to become redundant. Such apprehension is a direct sideeffect of the immense flood of news articles promising new technologies with ‘superb’ performance. This is, however, highly misleading for two main reasons. Firstly, it takes at least 8-10 years for results shown in lab-prototypes to translate to commercial prototypes, in the best case. It takes another 3-5 years at least to increase scale of manufacturing to reach reasonable costs. Secondly, the manufacturing process of Li-ion cells is largely invariant across chemistries.
This means that the evolving landscape of new materials does not necessarily pose any threat of obsolescence to the existing cell manufacturing facilities, as the facilities can be tweaked to
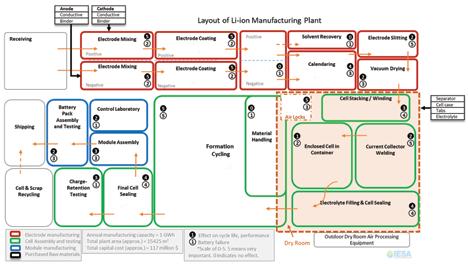
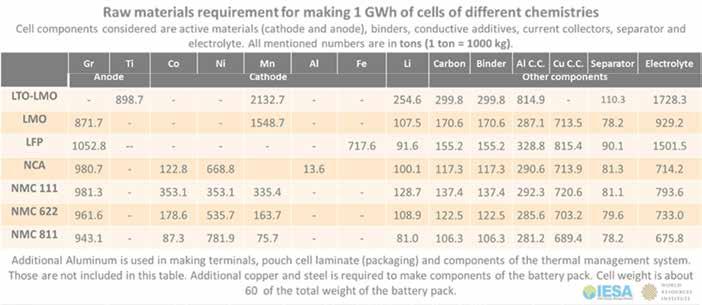
adapt to new chemistries. These findings have been confirmed via detailed interactions with many cell manufacturing companies globally. The intermittent chemistries between lithium ion and solid state are developed with intention of using the existing manufacturing lines with minimal tweaks. Hence, the transactional stage between two technologies will be smooth for the battery industry as a whole.
Ensuring robust supply chain of raw materials for giga factories and indigenization of manufacturing of cell components: do we have the raw materials?
Li-ion battery production in giga factories is supported by a large and complex supply chain of the essential raw materials. Global and India statistics of production of key raw materials are presented in this study. For the ores for which there are existing reserves in India (Mn,

Ni, Cu and Al), an attempt should be made to produce high value battery components which can be used by local and international cell manufacturing companies. These key components are MnSO4, NiSO4, copper foil current collector and aluminum foil current collector. If such high value components are produced in India, the global manufacturing industry can be targeted, which would largely boost exports.
In case of graphite, existing reserves should be evaluated for large flake graphite content which is directly used as anode material. Synthetic graphite produced from coke is finding increased use as an alternative anode material. Even if reserves are inadequate, facilities for processing ore and producing a high value product for Li-ion batteries can be set up locally. Use of silicon as an additive has increased in anode materials. Local production of silicon can also benefit cell manufacturing.
For other raw materials (Co, Li) for which there are no existing reserves in India, adequate arrangements for procuring ores or concentrates from other countries should be made. Localized processing of lithium concentrates is beneficial to the battery industry from a reliability and purity perspective. Purity of lithium raw material such as Li2CO3 and LiOH is crucial for achieving long cycle life. It must be understood that having reserves is only one component of the value chain. After mining of ores, there are several other steps such as concentration of ore, refining, purification and synthesis of active anode and cathode materials, which can all be domestically done even in the absence of reserves.
Can India play a leading role in development of next generation technologies? Recommendations for strengthening feedback mechanism between industry and R&D community.
Keeping an eye on electric vehicle and renewable energy penetration in near future, batteries will get significant attention among researchers, manufacturers and application developers. Many of the Indian researchers are actively working on advanced battery technologies. There are however, some major gaps in facilities, which need to be addressed immediately to foster an active collaborative engagement between industry and academia.
• Commercial prototyping centres within universities (pilot plant for cell fabrication)
Selected institutes should be equipped with facilities for commercial prototyping and testing to demonstrate performance of new developed materials in commercial size cells (TRL = 5). These types of demonstrations are key to attracting the interest of the industry, which can then take the technology further.
• Technology incubators and field testing centers
Field testing centers should be established where real application testing of commercial prototypes (TRL= 5-6) can be evaluated. Such centers can serve as a good meeting point for technology developers and potential manufacturing

partners. Technology incubators are a good medium for grooming PhD and postdoctoral researchers in the commercialization process of technologies. The translation of technological inventions in institutions (TRL = 2-4) to commercial prototyping (TRL = 5-6) is one of the main objectives of technology incubators.
• Skill development programs and knowledge sharing on energy storage and EV
Institutions or private companies should conduct capacity building training programs and provide current market trend on different technologies and different policies/ guidelines.
Batteries will generate lot of waste and India is not equipped to handle this. How should the environmental impact be addressed?
This should be seen as a tremendous opportunity rather than a roadblock. The global recycling industry for Li-ion is in a nascent stage and will be massively scaled up in the next few years. If the Indian industry steps up initiatives in this direction, it could lead the way for the world, while structuring an industry that could be a very large employer. A living example of a robust recycling system is that of lead acid batteries where 96 pwecent of batteries are recycled.
Development of a plan for recycling of Li-ion battery should be put underway alongside establishment of giga factories. Used batteries will be a huge source of several important raw materials (several 100 to 1000 tons per GWh). These could be used for battery applications or in other industries such as steel and alloy making and in chemical industries.
The world is witnessing a complete transformation of how we obtain our required energy and the countries which are leading this transformation are bound to benefit from it. Being a tropical country, India has an immense potential for renewable energy generation. It is up to us to realize this and begin to work in the direction of developing the necessary advanced storage technologies, which would allow us to benefit from this resource. So how long before India finally takes the plunge?