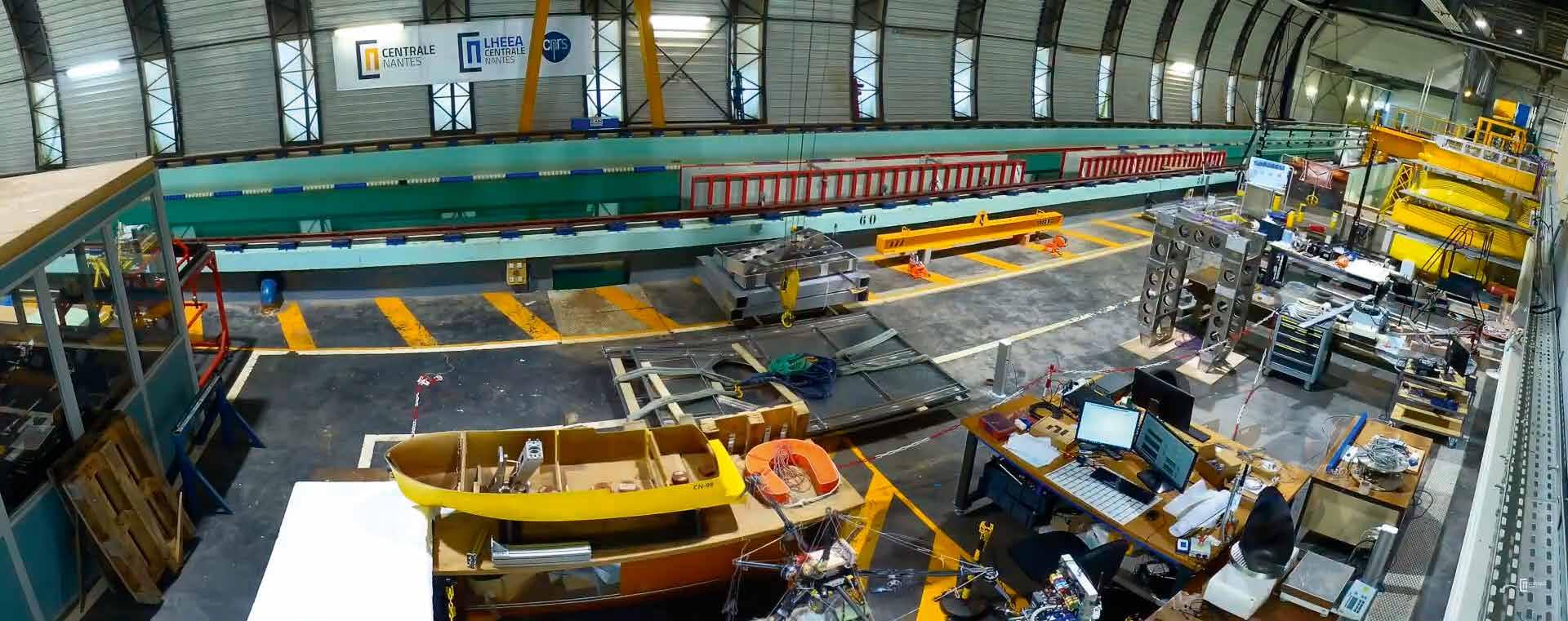
13 minute read
Innovating to make wave energy viable
Developing Innovative Strategies to Extract Ocean Wave Energy, or the LiftWEC project, is exploring the potential of using lift forces generated by ocean waves as a source of power. Principal Researcher, Matt Folley, seeks to finally prove waves can make sense as the next big renewable.
There have been many attempts and trials to convert energy from the natural power of ocean waves. It is an area of enormous potential because waves are relatively predictable and reliable as natural forces. There is a range of technologies established such as heaving buoys, oscillating water columns, overtopping devices, and line absorbers, among many other methods of capturing energy from waves. However, there is an issue with the majority of ocean wave energy converters because, despite their useful functionality, they have not proved to be commercially competitive with offshore wind, or solar power. However functional a device might be, it has to be cost-effective and make economic sense for wide-scale adoption and to attract industry investment.
“Wave energy is probably thirty years behind wind energy,” began Folley. “If you think about where wind energy was thirty years ago, where there were a few prototypes but limited commercial interest; that’s where wave energy is now. People would treat wind energy back then as a marginal technology but of course, that changed, partly because of the demands from climate change, but also because effort has been spent on developing wind turbines resulting in a significant reduction in cost. This is even more apparent when you see the changes with solar panels. The cost of solar panels has plummeted dramatically in the last ten years, making it more attractive to manufacture and install.”
The power of starting afresh
The LiftWEC project was created to discover new ways to approach the challenge of making wave energy commercially viable and to fulfil its potential as a major renewable, alongside wind and solar.
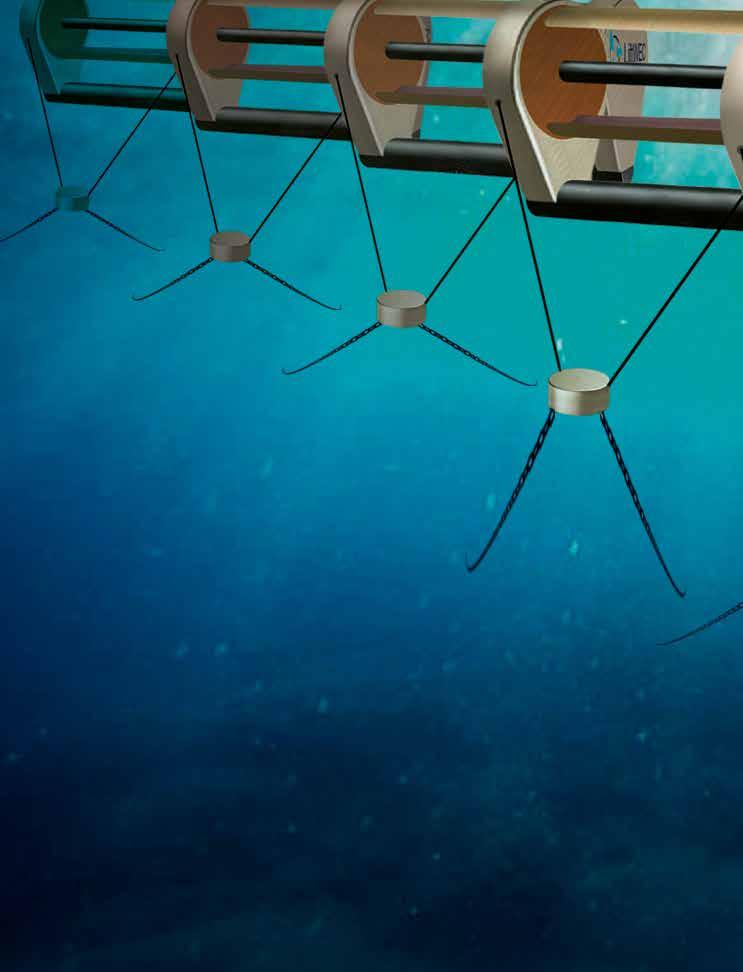
The engineering design began with ‘a blank canvas’ and the coming together of experts and specialists in related fields, to understand the hydrodynamics involved. The wider goals stretch beyond making a device that works and the aim is to design and engineer a device that is viable in the renewable industry. This goal means considering the environmental impact, the maintenance requirements, and the costs. For a design to be successful it has to operate in the ‘real world’ with a range of considerations beyond functionality.
“A lot of people are trying to do wave energy today, and it feels to me like there are too many ideas and not enough are filtered out. There can be a tendency for inventors to have one idea and focus on developing it, with a blinkered vision, and this may encourage a bias towards its positives, ignoring its flaws. We wanted to avoid that. Following a structured design process, we initially came up with seventeen different concepts which we narrowed down to four concepts after analysing the ideas in detail, and finally to a single concept to go forward with for detailed engineering.”
Through a process of analysing different ways to extract wave energy in an economically sound way, the research team, derived from a consortium of 10 European universities and companies, has developed a concept for a cyclorotor-based wave energy converter reliant on lift forces from rotating hydrofoils.
These relatively large devices would be positioned underwater, out of sight, and connected to the Grid.
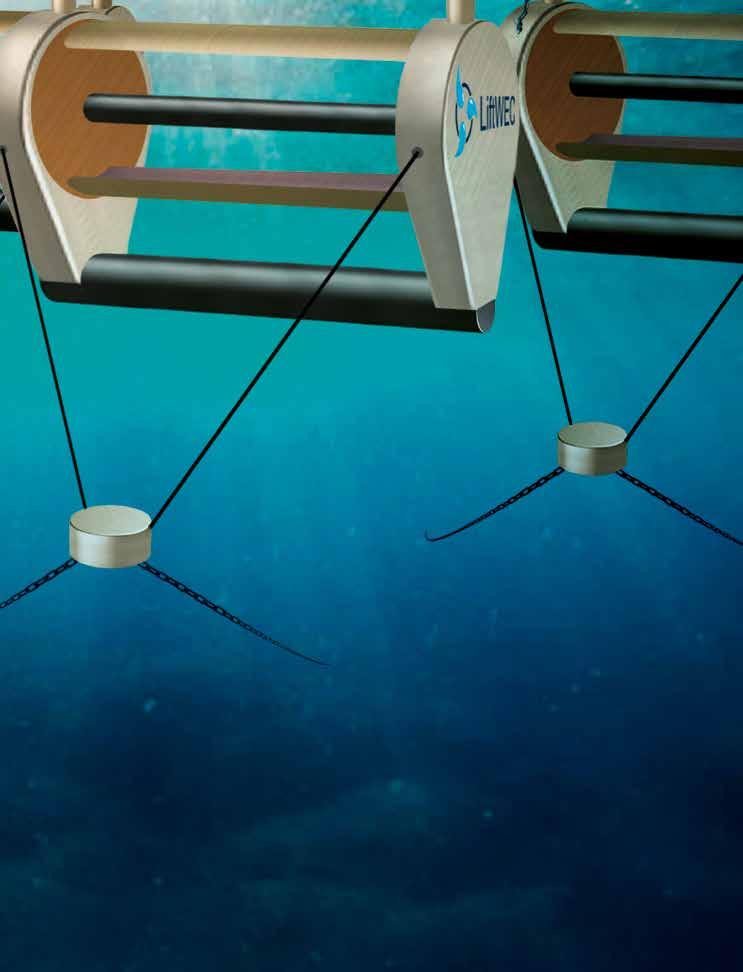
“The major difference to other wave energy converters is that our device couples with the waves through lift forces rather than diffraction or buoyancy forces, and if you look at the history of wave energy, although there have been hundreds of devices invented, the number of devices that have used lift is probably less than half a dozen,” said Folley. “What we tried to do in this research project, is to look in terms of how it can be done most effectively and to reduce the cost to make it competitive with other sources of renewable energy.”
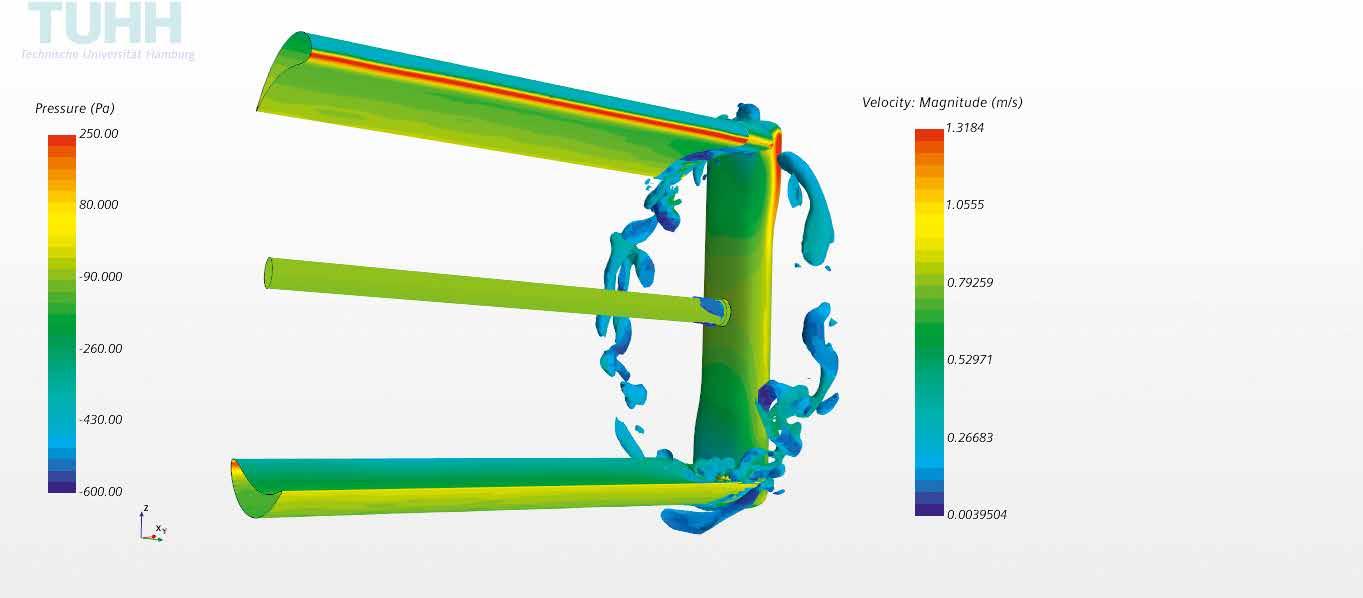
Technology fit for the sea
With a wave energy converter there are core problems to address. One is the device’s survivability and robustness. The advantage with lift-based devices is they have a similar benefit to wind turbine devices, which is they can decouple and stop generating lift in order to survive extreme events, like fierce storms. This sets it apart from many other types of wave energy converters.
“If you look at buoys, oscillating water columns or overtopping devices there is little they can do in extreme conditions, they just have to be built to survive it,” explained Folley. Another issue is the ability to perform essential maintenance for these machines in the sea. It is key to place these devices where there are lots of waves but where there are lots of waves, it makes maintenance very challenging. The biggest issue with maintenance at sea, where people are involved, a game-changing piece of technology development in this field. In the future, with inevitable advances in technology, there is likely to be further progress in providing better solutions to this challenge.
“Our current maintenance policy is to return it to base as that seems most viable. It may be in twenty years’ time that remotely operated vehicles or ROVs, latch is of course risk to life. LiftWEC’s solution would be to tow the devices back to port to be worked on in safety. Using knowledge gleaned from other projects means it is now possible to disconnect such a device in 15 minutes, on to these devices and crawl around to fix them. If ROVs were deployed in the future, it could dramatically change the landscape for offshore wave energy making it significantly cheaper and commercially viable.”
LiftWEC Developing Innovative Strategies to Extract Ocean Wave Energy
Project Objectives
The LiftWEC project aims to develop understanding of how best to extract wave energy using wave-induced lift forces and to design a novel wave energy converter based on this understanding leading to the identification of a viable renewable energy technology.
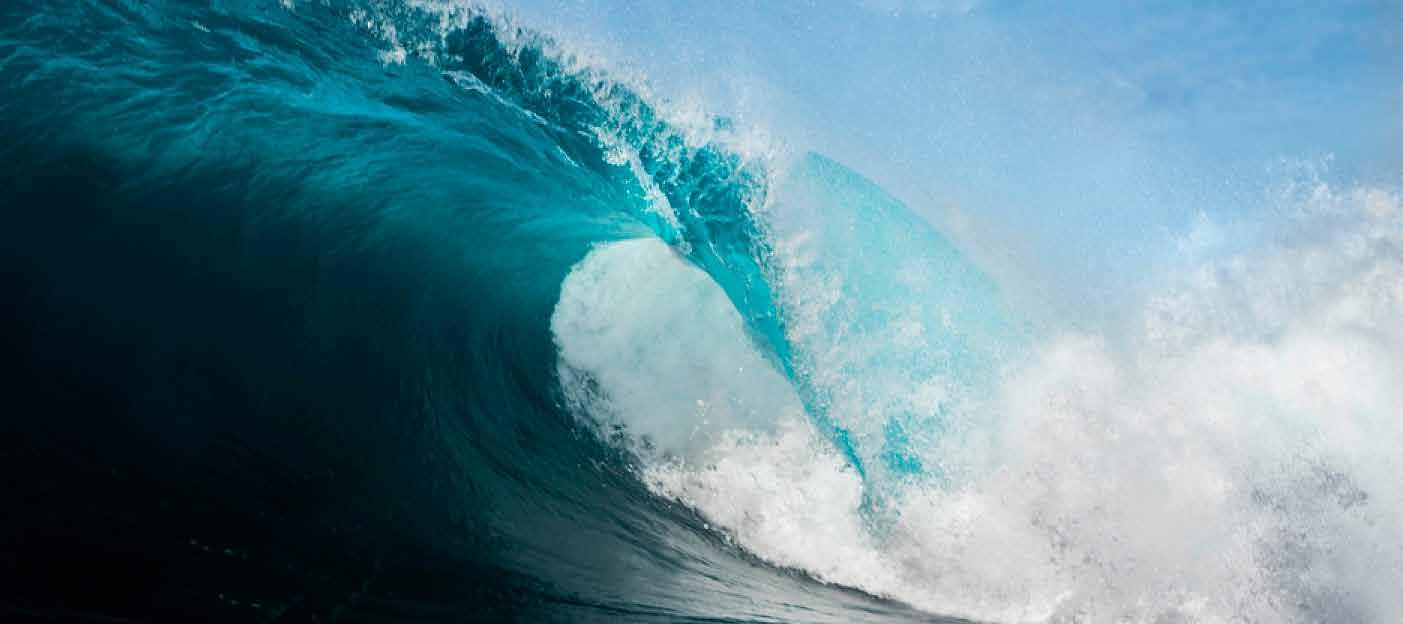
Project Funding
3.4 Million Euros
Project Partners
• Queen’s University Belfast • Technical University of Hamburg • Innosea Ltd • Maynooth University • Aalborg University
• University College Cork • Strathclyde University • Julia F. Chozas Consulting • Wavec/ offshore renewables • Ecole Central Nantes
Contact Details
Project Coordinator, Dr Carwyn Frost
Lecturer & MRG Lab Manager
School of Natural and Built Environment
QUB Research Portal Research Gate
T: +44 (0) 28 9097 4012
E: c.frost@qub.ac.uk
W: https://liftwec.com/ : https://www.youtube.com/ watch?v=CJjVeFMwlDA.
Always seeing the bigger picture
Dr Matt Folley is the principal researcher in the LiftWEC project having worked in the research and development of wave energy converters, from conceptual design to fullscale prototypes, for over 30 years.
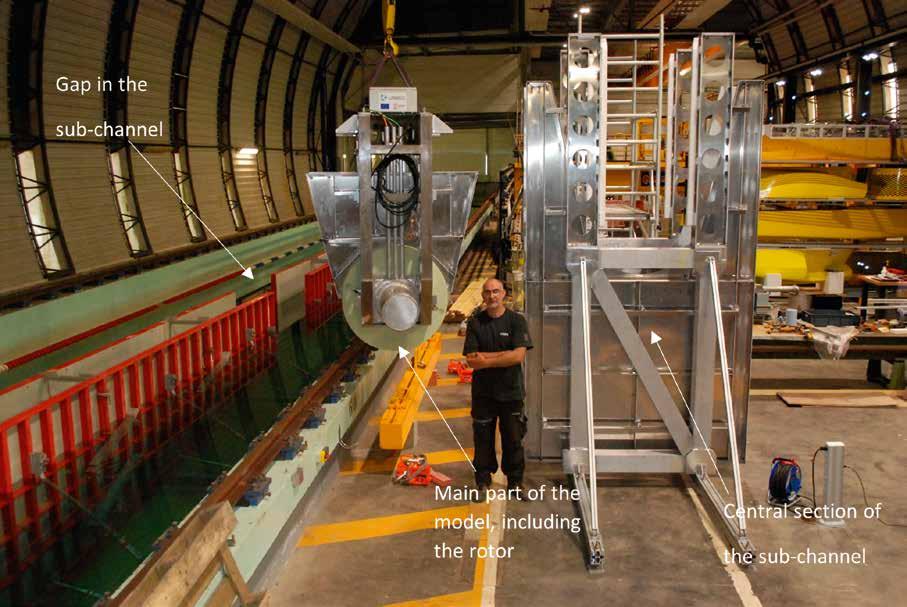
Dr Carwyn Frost is an academic in the offshore renewable energy sector, facilitating lab and field scale testing and measurement campaigns for the development of renewable technologies.
Dr Paul Lamont-Kane is a research fellow at Queen’s University Belfast and is working on developing the fundamental hydrodynamic understanding of the LiftWEC concept.
After the initial design phase, numerical modelling was the crucial next step. There were many different models. There were highresolution models that took days to run and produced all the details of the vortex shedding and the lift generation, a model around potential flow solutions and an engineering design model. By validating those numerical models, the team could generate performance data for different wave scenarios and also for different dimensions of the device, to understand more completely how the device works and which configurations were optimal. However, with the wider perspectives of the project focused on commercial viability, there needed to be a holistic approach with every change.
“If for example, they said increasing the length ten metres would increase power capture by fifteen per cent but then the structural people come in and said it will increase the cost by twenty per cent, then that’s when the development is not going in the right direction. Unfortunately, there is not always sufficient focus on how power capture and costs change with dimensions so that novel concepts cannot be truly optimised. What we are trying to do is avoid that pitfall. It makes it more complicated during development but produces a more economically viable result.
There is a delicate balancing act with the developing technology and dimensions of this machine.
The physical modelling involved testing a small-scale model in a two-dimensional configuration and a larger-scale model in a three-dimensional configuration. A special water tank was used for the simulation of ocean waves in a controlled environment. This way performance could be measured and assessed much faster than if the device was in situ in an ocean environment.
LiftWEC has a profound understanding of why wave energy converters have historically failed to develop into large offshore farms. The project is taking a broader view of all the factors that need to be satisfied for adoption by the sector, as well as choosing a novel solution that bucks the trends that have not previously translated to industry.
The resulting wave energy converter appears robust and effective and a promising new direction as an ocean-based renewable. The testing and engineering of this device may well pave the way to large-scale energy harvesting from our seas. There is more to be done. Further optimisation of the concept has to be worked on in line with the wider aims of the project. Every detail, configuration and environmental parameter must be thoroughly investigated. Ongoing marginal changes, paired with the potential of newly developed materials and technologies, could lead to the first major success story for wave energy harvesting.
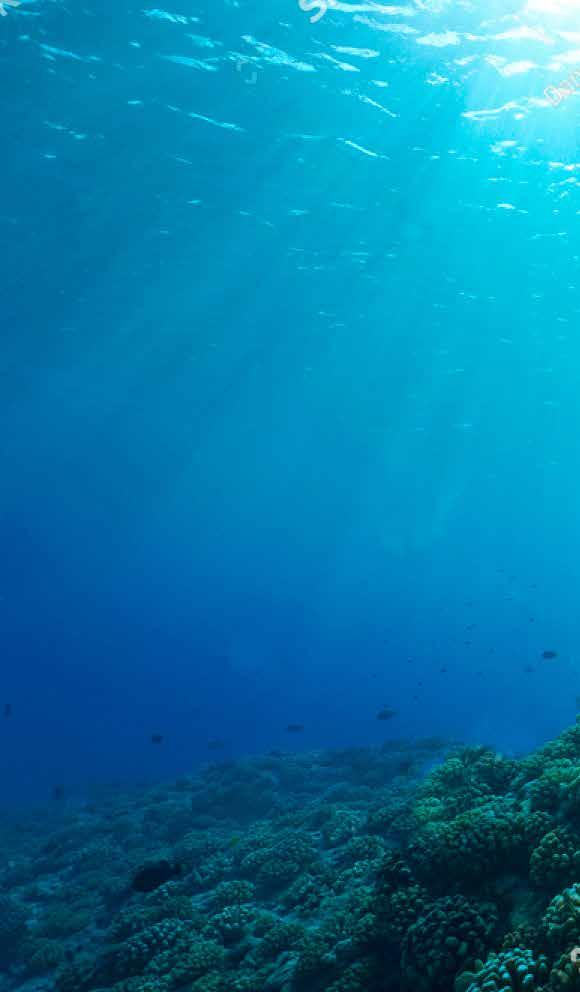
A new avenue for microenergy sources in autonomous sensors?
Professor
The autonomous cars, trucks and other vehicles of the future, which are expected to the market after 2025, will require a large number of sensors, for example in speaker systems, parking aids or temperature/pressure sensors. Sensors will also be required for systems in the infrastructure and environment to enable the vehicle to communicate with surrounding objects. All these sensors and systems require energy sources. The different systems inside a car are typically connected by large amounts of wiring, greatly adding to the overall weight and complexity of the vehicle. “There may be more than 2 kilometres of wiring inside a car,” says Giacomo Clementi, a researcher at the FEMTOST Institute in Besancon, France. After completing his PhD as an early stage researcher (ESR) in the ENHANCE project, an initiative bringing together academic and industrial partners from across Europe, Clementi is now working to develop hybrid energy harvesters which will address these issues and help reduce the environmental impact of the automotive sector. “Our idea in the project is to reduce the wiring cost and the complexity of cars. At the same time, reductions in the weight of the car will also lead to reduced CO2 emissions,” he explains.
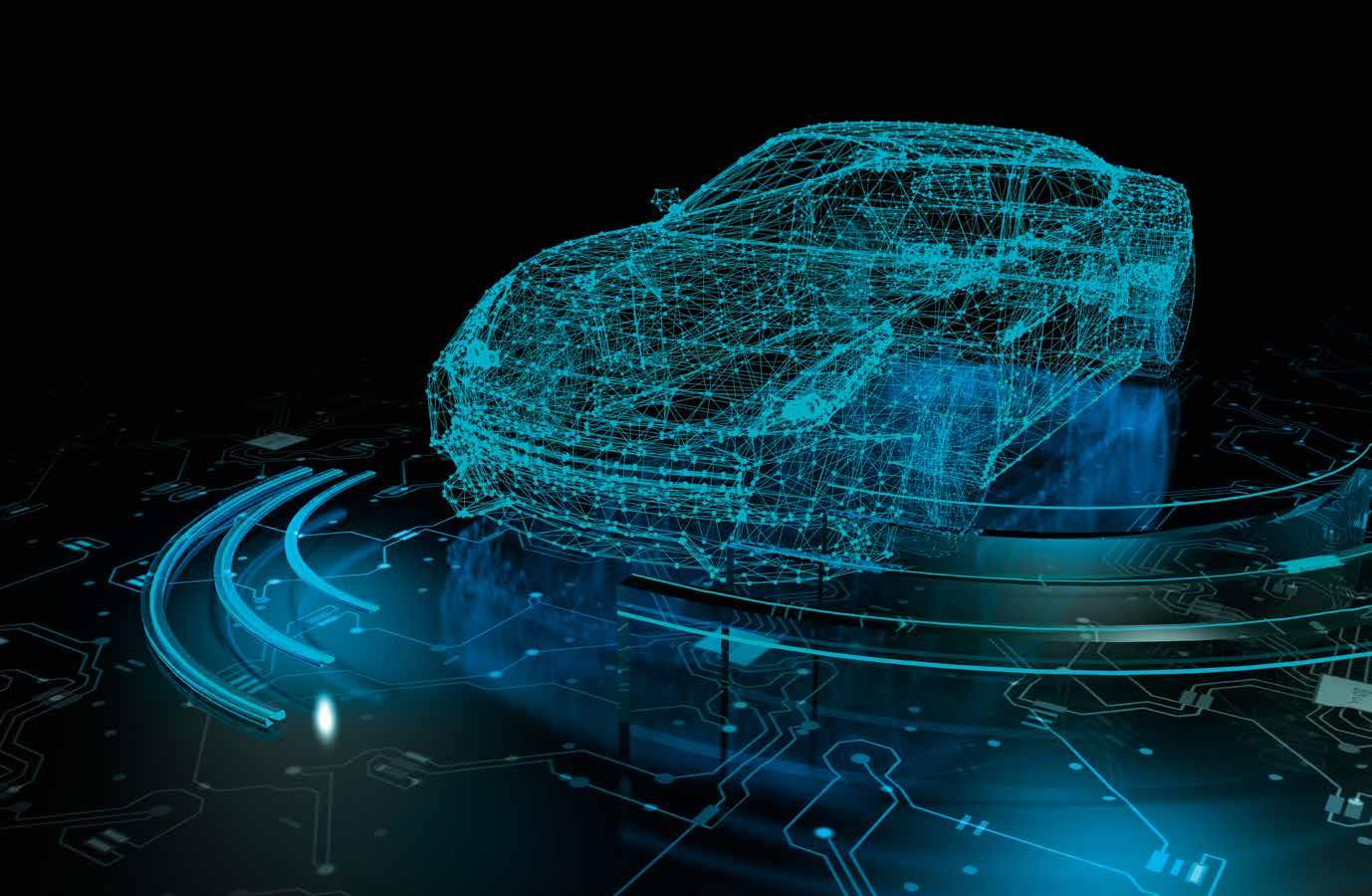
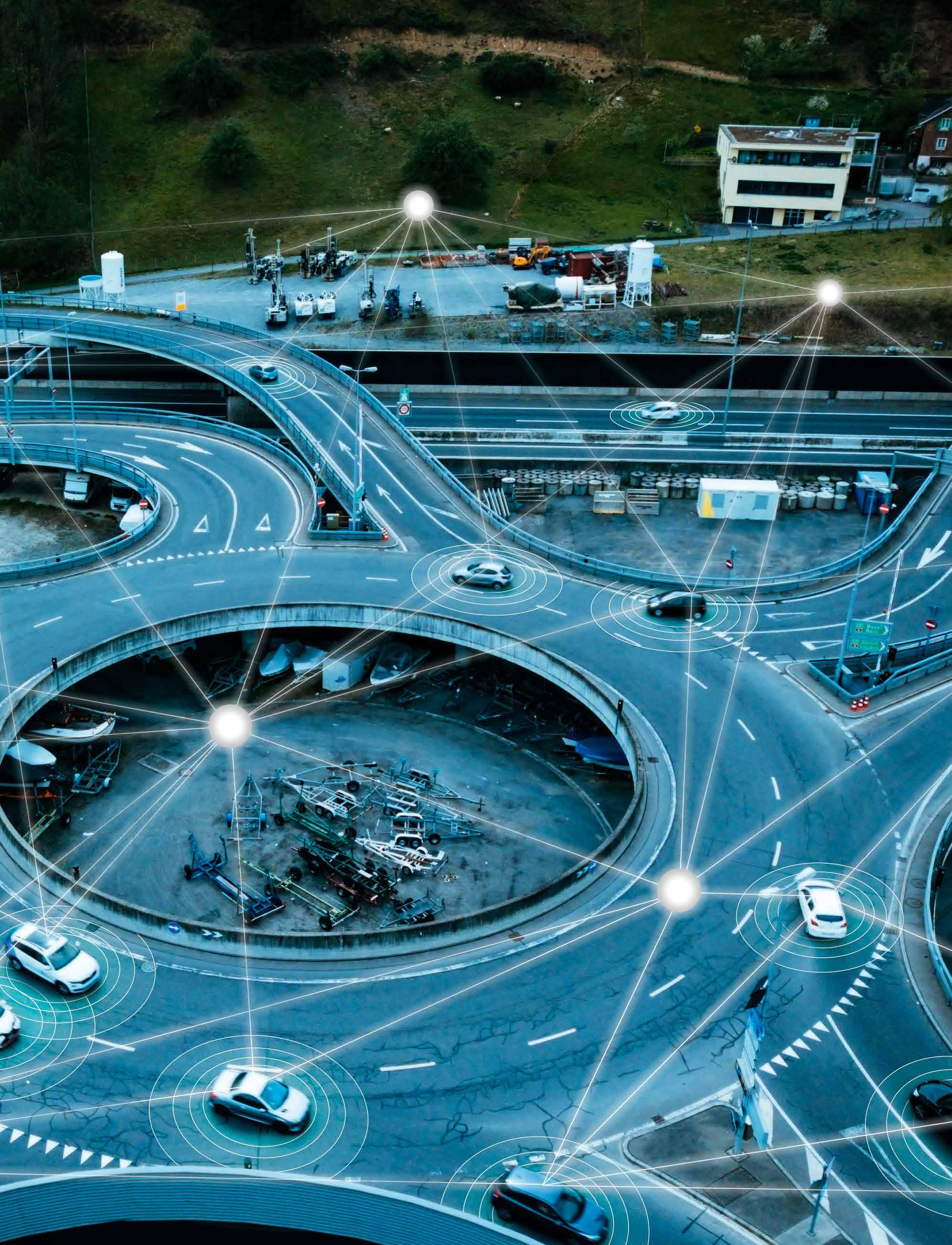
The ENHANCE project itself is an Innovative Training Network (ITN), which provides training to ESRs across a range of disciplines, including chemistry, physics and electronics. This reflects the complexity of the project’s work in developing a complete energy harvesting to Professor Ausrine Bartasyte, and Doctor about
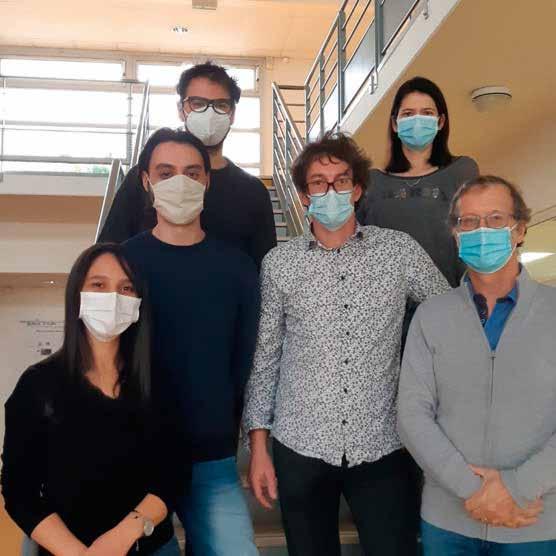
Lead-free Piezoelectric materials
system. “We are taking a multi-disciplinary approach, starting from the material and finishing with the electronics. We’re not focusing on just one part, we’re looking at the complete system,” says Professor Ausrine Bartasyte, Deputy Director of the FEMTO-ST Institute and the coordinator of the project. The ESRs are also receiving training in ‘soft’ skills, such as how to write presentations or apply for research funding, which will help prepare them for their future careers, whether in academia or industry. “We organised schools, workshops and conferences covering topics from chemistry and physics, to electronics to micro and nano-technology, as well as soft skills,” outlines Professor Bartasyte.
Clementi’s primary focus is on vibrational energy harvesting, so converting mechanical energy from the environment into electrical energy, which can then be stored or used to power small wireless sensors inside a vehicle. Piezoelectric materials, which have an internal electric charge, hold great potential in this respect. “When piezoelectric materials are essentially shocked or deformed by mechanical stress, due to their intrinsic atomic structure, they can convert this deformation into an electrical charge. That charge can then be stored in a battery, or used immediately to power a sensor,” outlines Clementi. Researchers are seeking to replace commonly used lead-based piezoelectric ceramics, prohibited under EU regulations since 2016, with environmentally-friendly piezoelectric materials offering competitive performance, in particular a piezoelectric material called lithium niobate (LiNbO3). “I am studying the microfabrication of this material and its application in vibrational energy harvesting,” says Clementi. “This finds applications not only in transportation, but also in areas like smart buildings, factory automation, internet of things (IoT) and structural health monitoring.”
In the frame of ENHANCE project, it was demonstrated that LiNbO3 implemented in vibrational energy harvesters offers competitive performance in terms of scavenged energy and stability at high operational temperatures with respect to the lead-based ceramics. This opens new avenues to the eco-friendly microenergy sources needed for further development of IoTs and communication systems.
The common theme here is the need for a reliable source of energy to power small sensors, with demand set to grow further in the coming years, as more and more physical objects are connected to the IoT. The main expected area of application at this stage however is the automotive sector, with researchers studying vibrations inside cars. “We’ve looked for instance at acceleration levels and the magnitude of the deformation, and how this relates to different ranges of frequency,” says Clementi. A further step in the project involved developing simulations to look at how a device would function in the practical context. “We implemented a very simple structure in the form of very small beams of a few centimetres –then we studied them with finite element analysis,” continues Clementi. “After that we optimised the structure, then we looked towards fabrication and prototype testing.”
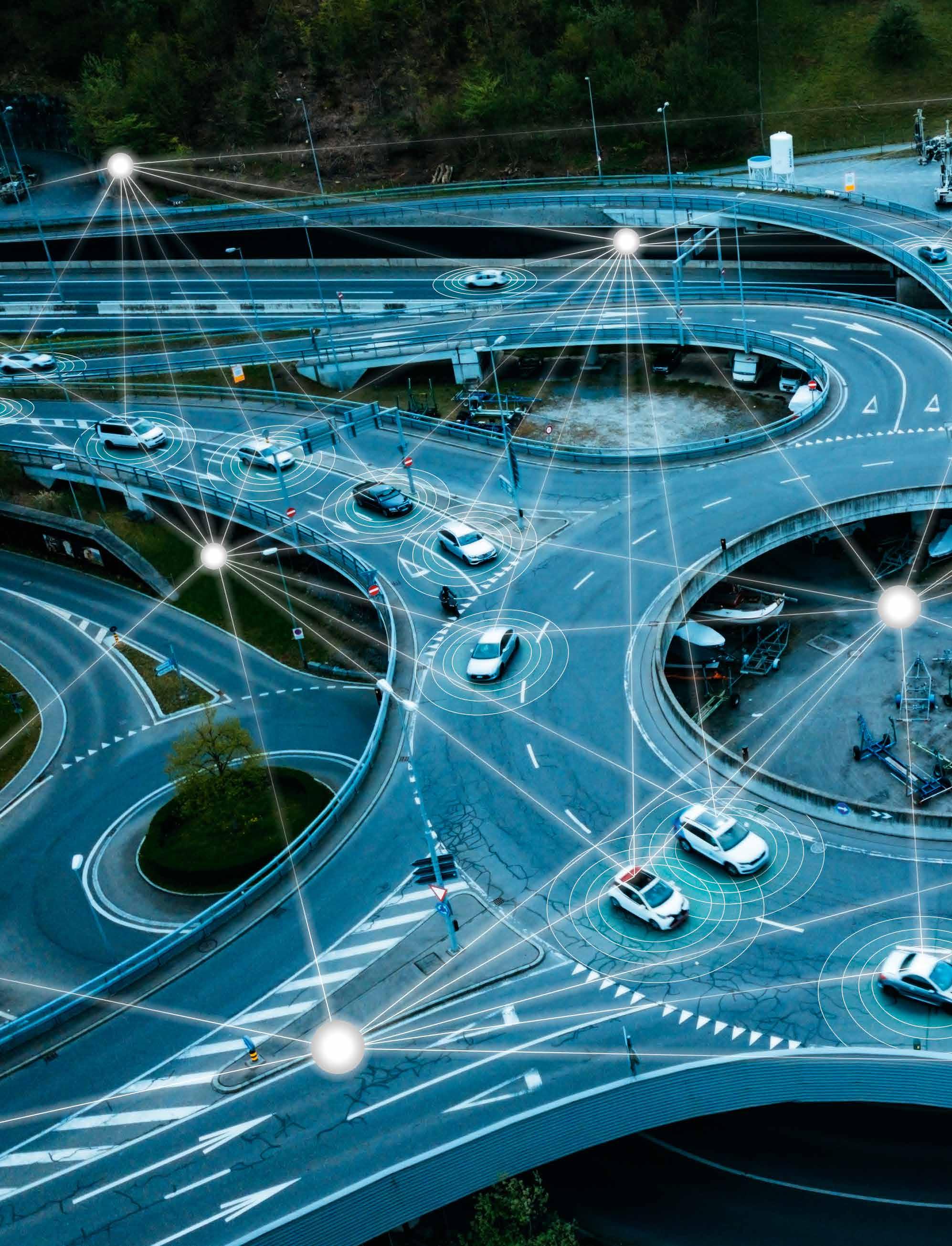
Researchers are using LiNbO3 in the development of the harvesters, seeking to harness its interesting electro-mechanical properties. In particular, Clementi says that LiNbO3 has some very promising performance characteristics in terms of robustness and flexibility. “We are now able to implement such piezoelectric materials on metal foils, which are more reliable,” he explains. This means it is possible to achieve power levels comparable to other materials,
Self-powered sensor
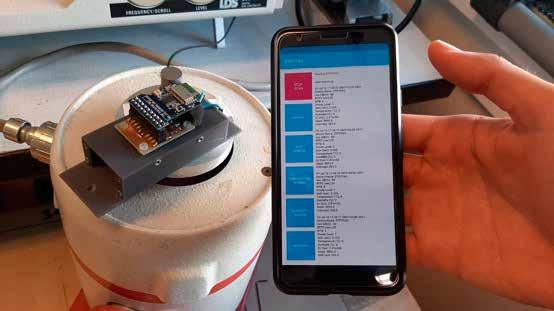
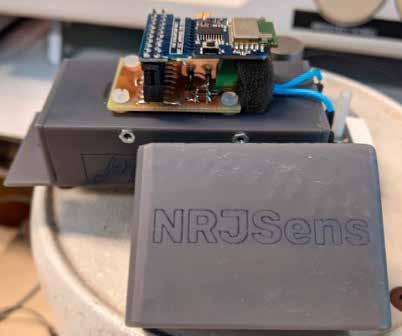
The material is also chemically inert and can go to high temperatures, in terms of both processing and application, which is highly valuable in terms of facing different conditions. The aim here is to design a module that essentially functions as a selfpowered sensor. “The harvester can be used already as a vibration sensor, it can without any of the toxic effects associated with lead-containing materials. “We can theoretically convert 49 percent of the mechanical energy into electrical energy. That is comparable to both lead-free and and lead-containing materials, and in some cases even higher,” continues Clementi. “Moreover, we can lower production costs, because this material comes in the form of very high-quality wafers, which are commercially available.” communicate the acceleration of the car. In other cases you may want to measure temperature or humidity, which can be communicated using Bluetooth,” says Clementi. The early tests on this device in the lab have shown promising results, with the project’s research essentially demonstrating a proof-of-concept, while there is also potential for these harvesters to be applied in areas beyond the automotive sector. “For example they could be used in structural health monitoring, in bridges. Wherever there are vibrations you can use these kinds of devices, so there is a broad range of potential applications,” outlines Clementi.
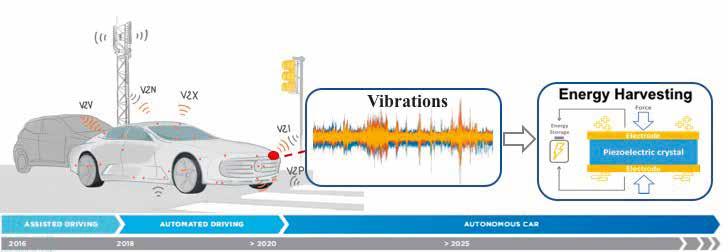
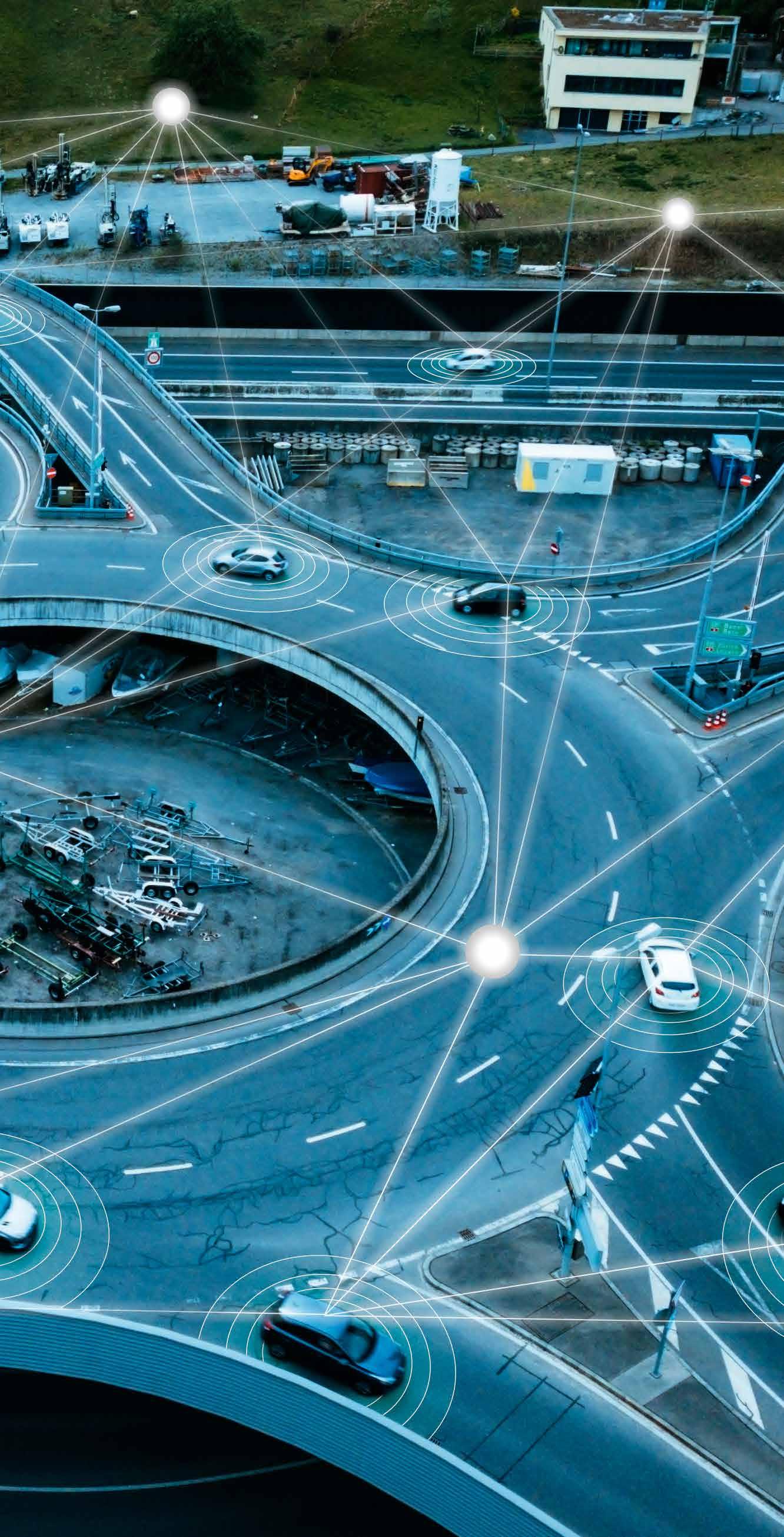
This represents an interesting alternative to existing methods of harvesting microenergy, such as photo-voltaics, which is already widely used. While photo-voltaics is highly efficient in the presence of direct light, it is not really ideal for indoor or enclosed applications and requires regular cleaning, whereas researchers in the project have taken a different approach. “Our approach is about converting every coulomb of energy. This will be achieved thanks to the ultra-low power electronics,” says Samuel Margueron, an Associate Professor at the FEMTO-ST Institute who is also closely involved in the project. These sensors do not require any maintenance, and their nontoxic nature means they can be used in the natural world, with only minimal human intervention. “If you are going to distribute these sensors in nature then you cannot use lead-based materials, because they would cause pollution,” explains Professor Bartasyte. “LiNbO3 is chemically inert and will not lead to any pollution, as it doesn’t contain any toxic elements.”
The wider aim here is to develop reliable and efficient energy harvesters that can be adapted to industrial needs. The industrial partners have played an important role in directing research towards the development of products relevant to commercial needs, and Clementi says a lot of progress has been made in the project. “Now we have a device that is at Technology Readiness Level (TRL) 4, with prototypes ready to be tested on the field,” he says. The next stage of tests are being prepared, while Clementi has established a start-up company to eventually bring these harvesters to the market. “We are in the maturation stage now, and we are in contact with investors. Our market is vibrational energy harvesting, we are trying to sell our device as an alternative to conventional ceramics,” he continues. “Transportation is the obvious market for us at this stage, as we have worked a lot on that, but ultimately we would like to develop a device that endusers can then implement wherever ambient vibrations are present.”
An effective energy harvester could have a significant impact in this respect, helping reduce the weight and complexity of vehicles, and so mitigating their environmental impact. This technology could reduce the weight of a vehicle by up to 50 kg, while it would also be significantly easier to maintain. “In many cars sensors are connected by a complex system of wires, and if you have any problems then it can be quite complicated to repair. If the sensor is completely autonomous and battery-free, then it’s much easier, as it doesn’t require any maintenance,” points out Professor Bartasyte. “By taking out the wires, you simplify the system.”
Enhance
Microenergy sources for autonomous sensors
Project Objectives
The Innovative Training Network (ITN) entitled “Piezoelectric Energy Harvesters for SelfPowered Automotive Sensors: from Advanced Lead-Free Materials to Smart Systems (ENHANCE)” provides thirteen Early Stage Researchers (ESRs) with broad and intensive training within a multidisciplinary research and teaching environment. Key training topics will include development of energy harvesters compatible with MEMS technology and able to power wireless sensor. Applied to automobiles, such technology will allow for 50 kg of weight saving, connection simplification, space reduction, and reduced maintenance costs - all major steps towards creating green vehicles. Other important topics include technology innovation, education and intellectual asset management.
Project Funding
This project has received funding from the European Union’s Horizon 2020 research and innovation programme under the Marie Sklodowska-Curie grant agreement No 722496.
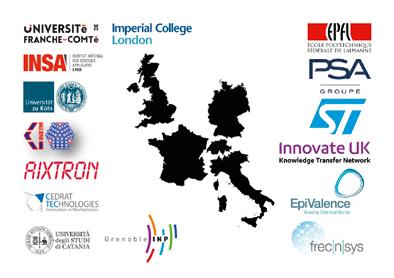
Project Partners https://www.itn-enhance.com/nouvel-accueil
Contact Details
Project Coordinator, Professor Ausrine Bartasyte
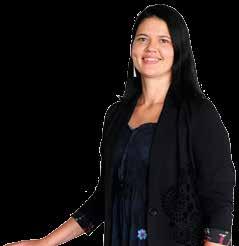
Deputy Director of FEMTO-ST Institute University of Franche-Comté
26 rue de l’Epitaphe
F-25030 BESANCON Cedex
France
T: +33 3 81 40 28 24
E: ausrine.bartasyte@femto-st.fr
W: https://www.itn-enhance.com/enhance
Professor Ausrine Bartasyte
Ausrine Bartasyte is a full professor at University of Bourgogne FrancheComté and a deputy director of the Institute FEMTO-ST (Besançon, France). Her research focus on advanced architectures of alcaline niobates for the next generation acoustic filters & sensors, energy harvesters, actuators and integrated photonic devices.