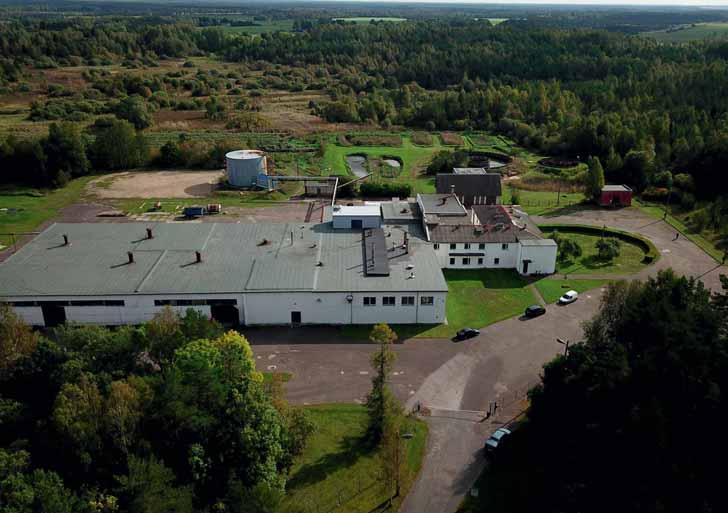
6 minute read
Strong environmental focus resonates with customers
by Eurofish
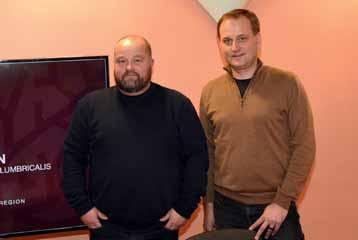
Algae cultivation forms part of the EU vision for a more sustainable and competitive aquaculture sector. The production of algae is also highlighted in the EU’s farm to fork strategy, a blueprint for a healthy and environmentally friendly food system . The reasons for the official interest in algae are manifold. In a broader context, population growth, climate change, resource depletion and environmental factors call for a new approach to food systems.
Advertisement
One of the ways to address these pressures is to use Earth’s seas and oceans more to produce human food. These vast resources only contribute 2 to human food despite covering 70 of the globe. More immediately, the Russian aggression in Ukraine has affected supplies of fertiliser, animal feed ingredients, and energy. Algae, both macroand microalgae, can contribute to mitigating some of these shortages and also offer several other benefits including decarbonisation, the preservation and restoration of biodiversity, protection of ecosystems. Algae can be used as food, fuel, feed, and fertiliser and serve as a raw material for biostimulants, biochemicals, and other materials including packaging.
Seaweed has multiple applications
With their content of micronutrients, bioactive compounds, dietary fibre, and pigments algae have applications in the field of pharmaceuticals, nutraceuticals, cosmetics. They can also remove nutrients (nitrogen and phosphorus) from aquatic ecosystems. Macroalgae (seaweed) when cultivated at sea removes carbon thereby mitigating ocean acidification. Despite the benefits that algae offer, production in Europe is virtually non-existent being still based on harvesting from the wild rather than farming. In Asia, by contrast, algae accounts for about half the production from aquaculture. However, the potential for algae production in the EU is high—the bloc is already major imported of seaweed and demand is forecast to increase in the future in line with increased focus on health and sustainability. In Estonia the company Est-Agar is exploiting the growing demand for algae products. The company produces furcellaran, a gelling agent, from the red seaweed Furcellaria lumbricalis. As a gelling agent and texturiser furcellaran is used in the food industry, but it also has a number of other applications in cosmetics, pharmaceuticals, feed for animals and fish, fertiliser and soil conditioners as well as bioplastic applications.
The company has been through different economic and political times, as it was established in 1966 under the Soviet regime but has functioned uninterrupted from its inception. Today it is privately owned by four seaweed enthusiasts. Co-owners Urmas Pau and Mart Mere, act as the CEO and business development officer respectively. The Soviet Union could not import agar agar, a commonly used gelling agent also derived from seaweed, and needed therefore to produce it domestically. Three factories were established each in
Latvia, the Russian Far East, and Estonia, of which the plant in Estonia is the only one remaining. The factory was built specifically to exploit Furcellaria lumbricalis and is today, according to Mr Mere, the only factory in the world producing furcellaran, a product that can only be extracted from this variety of seaweed. Currently, rather than growing it, the company harvests the seaweed from the wild. For this it is licensed by the government which allows it a quota in the Baltic Sea. The estimated biomass present in Estonian waters is over 200,000 tonnes wet weight mostly between the Estonian islands. The resource is managed by the Estonian Marine Institute and the company’s quota is 2,000 tonnes, it may be possible to increase the quota over time, but the goal is to start farming the seaweed, says Mr Mere.
Commercial farming of seaweed in the Baltic Sea soon to become a reality
Trials have been carried out over the last five years and the technique has now been tested in the sea. In addition, Estonia’s marine spatial planning strategy was recently approved which identifies sites for different farming activities, bringing commercial farming of seaweed by the company a step closer to fruition. The factory is located on the island of Saaremaa, the biggest
Estonian island. The building is the one built nearly 60 years ago and even some of the equipment, custom built in Estonia, dates back to that time. The current owners of the company bought the factory from the previous owners six years ago and have since then invested considerable sums in modernising it, including making it more environmentally friendly. One of the measures was to use switch from oil to LNG as a source of heat, but as prices shot up it was substituted with LPG. The factory can now run on four sources of energy including biogas. The waste water treatment process was also upgraded both to increase efficiency, but also to send a message to the company’s customers, the food industry, cosmetics, and some pharmaceutical companies, that it takes its environmental obligations seriously. This is also reflected in the solar panels that have been installed on the roof of the building and which, in summer, cover about a third of the company’s consumption of electricity.
The image that Est-Agar wants to convey of an environmentally conscious company partly explains why it wants to start farming. It is another reason why the proper management of the wild seaweed biomass is so important. Part of the material the company uses is the biomass that drifts ashore when there is a storm. Some 20 families from the local community are contracted by the company to gather the seaweed from the beach after a storm and dry it. The final product is then sold to the company. This arrangement goes back many years—it is the second or third generation of these families that is carrying out this work today. While initially the work was done manually some families have now invested in tractors and other equipment making it a commercial undertaking. This integration into the community and the support that it can offer local workers is an important aspect of the business for the company. However, the material collected this way is not enough to sustain the company’s operations, but just to supplement the biomass from harvesting. The frequency and intensity of storms vary greatly and the biomass available for collection can be 30 tonnes one year and 300 tonnes the next. But usually whatever volume the families supply, the company buys it all.
Climate footprint is a major consideration in investment decisions
Extracting the furcellaran is done by adding freshwater from a well to the seaweed and then boiling it, a process that demands a lot of heat. Some of the machinery runs on steam which the company generates itself. And, as far as possible, the heat is recycled and used to warm the factory. Another environmental measure is the collection of rainwater to wash the seaweed. Resource efficiency has been baked into the upgrades and the investments that that have been made to reassure buyers that the environmental footprint of the product is as small as possible. The company has now started a process that will assess each operation for its carbon production to get a granular picture of overall emissions so that it can implement measures to reduce them further.
Est-Agar AS
Kärla Village Saare County 93501 Estonia
Tel. +372 454 2205 info@estagar.ee estagar.ee
Owners: Urmas Pau CEO; Mart Mere, BDO; UG Investments
The fact that furcellaran is a plant-based food ingredient is a very useful attribute as this market is rapidly increasing. The cosmetic industry, in particular, is focused on using plant-based materials and when it originates in the sea this is even better. Seaweeds, in general, have several useful components and F. lumbricalis is no exception. For now, Est-Agar is looking at extracting pigments and antioxidants The plan is to use a multi-extraction process that allows different components to be extracted one after the other. While the technique has shown promising results in the laboratory, it needs to be tested at scale. Another idea is to create a product from the material left over from the boiling process. This could be formed into small pots that can be used to grow salads or herbs. The residual furcellaran content would allow the material to act as a membrane that controls the water content of the pot.
The company already exports over four fifths of its production to 10 countries. The product takes two forms—furcellaran flakes and powder but going forward more of the powder will be produced as it is easier to mix with other products. Powder is the future, says Mr Mere.
Product: Furcellaran (a gelling agent and texturiser from the seaweed Furcellaria lumbricalis)
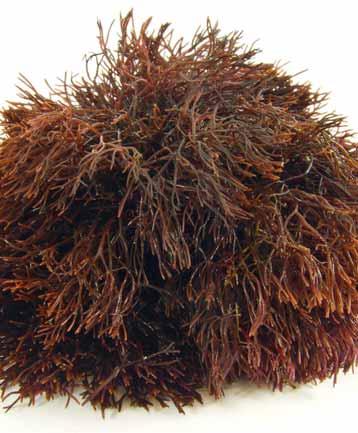
Production: Up to 150 tonnes per year
Applications: Food, cosmetics, and pharmaceutical industries
Volume of raw material: 2,000 tonnes of seaweed harvested from the wild
