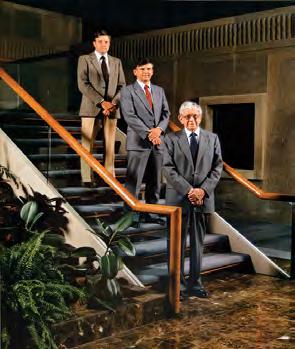
4 minute read
IN THE SPOTLIGHT
On to the Future
As Traylor Bros., Inc. celebrates 75 years, its co-CEOs are already looking ahead BY DALLAS CARTER
Traylor Bros., Inc. was
founded by brothers William and Ferris Traylor in 1946 as a Midwestern marine and bridge contractor. Now in its third generation of leadership and celebrating 75 years of family-owned success, the company is part of a larger brand.
In 2007, Mike and Chris Traylor succeeded their father Thomas (who died on May 9, 2013) and grandfather William as co-CEOs of Traylor Bros. and became equal part-owners with their oldest and youngest brothers Tom and Dan. Under their leadership, they have expanded to the parent company Traylor Construction Group, Inc., which includes Traylor Bros; Ballard Marine Construction, LLC; Traylor Industrial, LLC; and more.
Locally, Traylor Bros. had a hand in projects such as parts of the Lloyd Expressway and Interstate 69, but it quickly expanded, completing infrastructure builds such as the Singapore Mass Rapid Transit North-South line and more than $3 billion of improvements through 2017 in New Orleans after Hurricane Katrina devastated the area. Currently, the brothers are overseeing tunneling and station contracts for new subway lines in the Los Angeles Metro system.
This jump to completing billion-dollar projects didn’t happen overnight but is a delicate balance of the Traylors’ familial traditions and the company’s six core values. Core behaviors, people, innovation, community, safety, communication, and ethics have been unyielding drivers of Traylor Bros. since the beginning.
“I’m proud that Traylor has such a long legacy,” adds Mike. “We’re aware that many family-owned companies fail as generations turn. When I look back, I can see that our grandfather and father were careful about cultivating their sons and the business to be successfully passed to the next generation.”
The 75th anniversary will be celebrated at the annual managers meeting in Evansville in September with attendees traveling to the River City from offices in Colorado, California, Virginia, and more. The brothers also plan to host a celebration at the Evansville home office to include members of the community.
Despite the major milestone for Traylor Bros., Mike and Chris already have their sights set on the future — a future which they say will always include Evansville. Currently, about 385 out of Traylor Construction Group’s 860 employees are based in Evansville.
“Our family’s nature is to keep our heads down and focus on the future,” says Chris. “We’re looking to our hundredth anniversary now by making sure the next 25 years go well.” z
TRAYLOR.COM
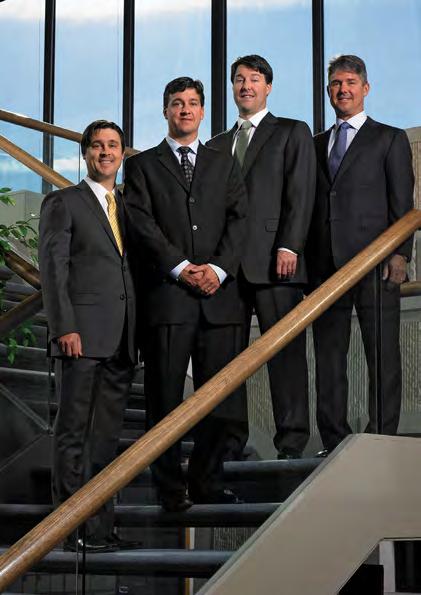
Brothers Tom, Mike, Chris, and Dan Traylor took ownership of Traylor Bros., Inc. from their father Thomas in 2007. The infrastructure construction company was founded by their grandfather William and has completed projects locally, such as the Shawneetown Bridge in southern Illinois, and across the globe.
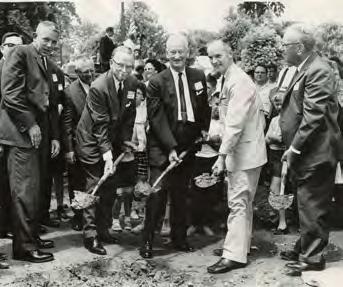
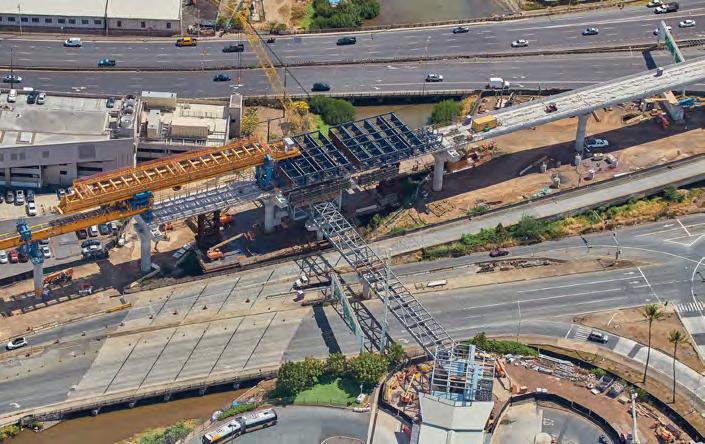


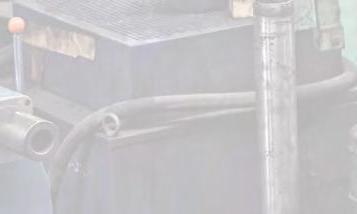

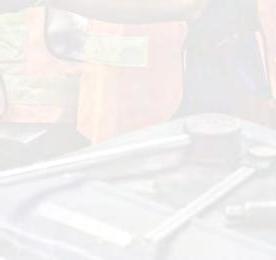
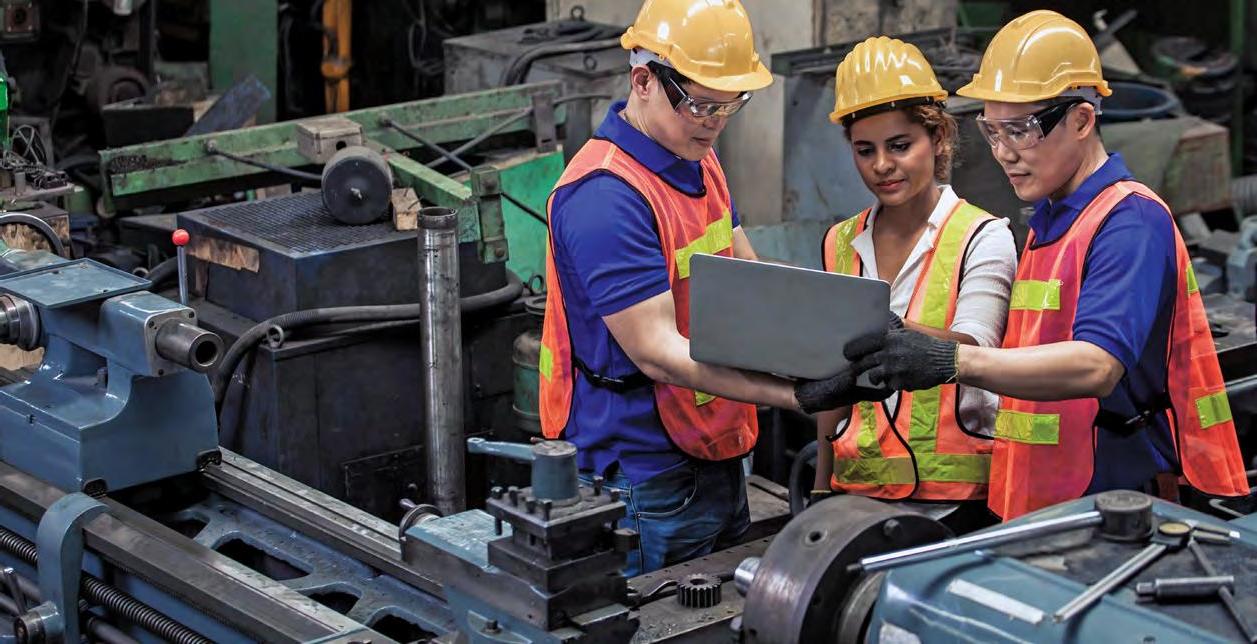
3 EASY STEPS TO SAVINGS
SAVE ENERGY AND MONEY for your business with HVAC control rebates
Your HVAC system could be working smarter with smart thermostats and Advanced Rooftop Controls (ARCs). An ARC system uses digital sensors to monitor indoor and outdoor temperatures, as well as CO2 levels, so that your rooftop unit works intuitively to create the desired atmosphere inside your facility. ARCs, along with smart thermostats, help to maintain occupant comfort, lower maintenance costs, enhance indoor air quality, reduce noise, and ensure that your system is working at peak effi ciency. Upgrade your HVAC controls and improve your bottom line with rebates on:
To learn more, visit us at CenterPointEnergy.com/SmartSavings or call 866-240-8476.
Download application
Determine eligibility, then download and complete the rebate application. Applications for rebates in excess of $20,000 per facility per year must be approved by CenterPoint Energy prior to purchasing or installing equipment.
Select measures
Download, complete and attach the Measure Selection Form(s) associated with the rebates you are applying for.
Retain invoices and log sheets
Provide a copy of all product and service invoices. You may also need to provide the necessary log sheet for services like tune-ups.