DESIGN-BUILD RESTORATION AND MODERNIZATION OF SCOTT BARRACKS
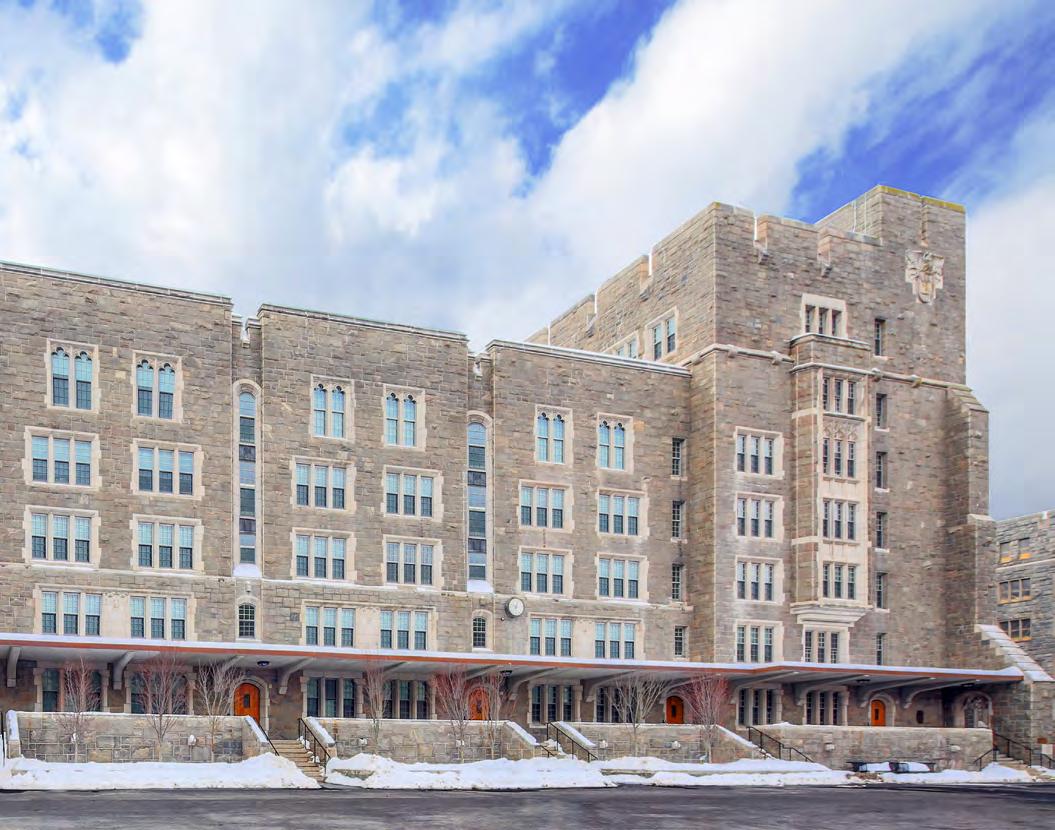
ARCHITECTS
ENGINEERS
INTERIOR DESIGNERS
PLANNERS
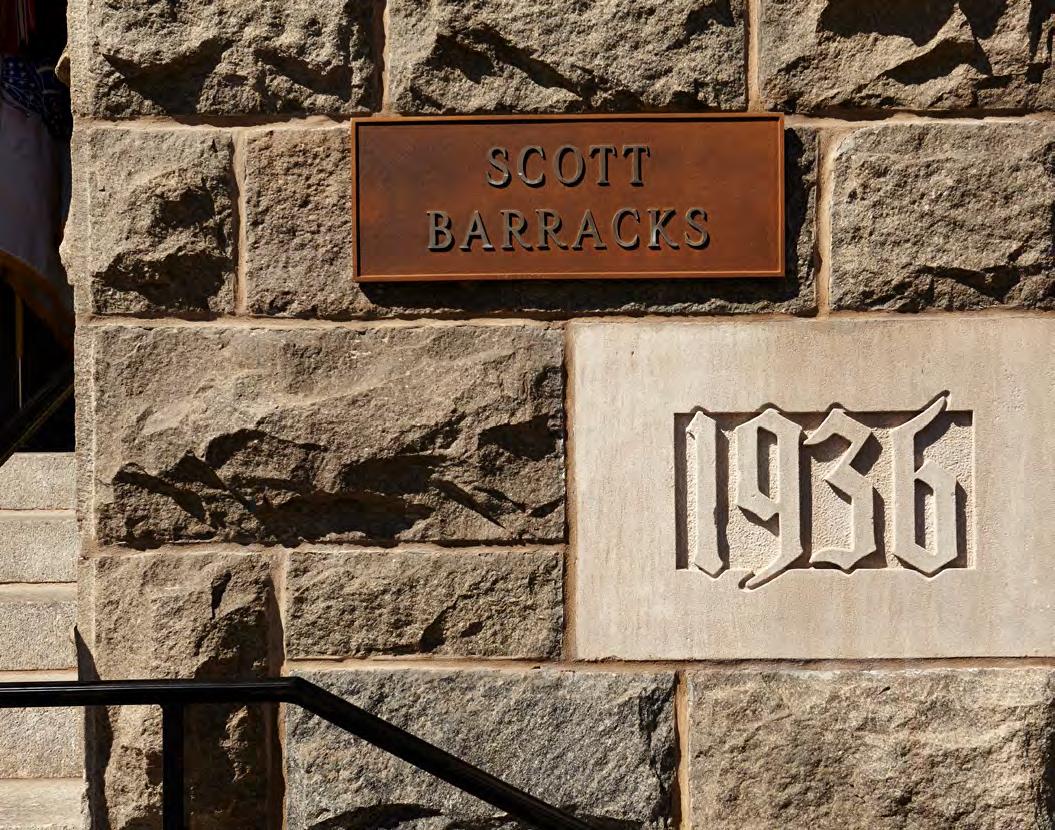
ARCHITECTS
ENGINEERS
INTERIOR DESIGNERS
PLANNERS
As part of a designbuild team, EwingCole developed the renovation and modernization to the Paul Philippe Cret designed Scott Barracks.
Opened in 1938, Scott Barracks is currently home to 477 United States Military Academy cadets and had not seen a major renovation since 1988. This 147,755 sf modernization, completed in 2014, was designed in accordance with the National Historic Preservation Act given that the campus is designated a National Historic Landmark District.
Renovation to Scott Barracks involved bringing the barracks up to current coders, the complete replacement and upgrade of the mechanical, electrical, plumbing, telecommunications, heating,
ventilation and air conditioning, fire detection and sprinkler, and insulation systems. Exterior upgrades include masonry repairs and a new roof which has been retrofit for air conditioning. The interior modernization includes the replacement of all floors, wall finishes, and windows, new furniture, and bathroom renovations to accommodate female cadets.
The new design is on track to obtain US Green Building Council LEED certification and is designed to achieve Net Zero in 2017.
This meant that each team member did not allow formal and legal requirements to hamper their actions. Problems were solved without worrying about who they belonged to.
In order to keep the owner engaged throughout the project, the Design-Build Team utilized several strategies including:
• Partnering & Planning Workshops as part of the notice to proceed to define engagement process and methodologies.
• Owner ’s Request for Information Forms in lieu of Design-Build Team forms.
• Weekly Meetings with the Owner’s Project Manager.
• “Over the Shoulder Reviews” of Milestone Submissions
• Submission Orientation Briefings Prior to Owner Submission Reviews.
• Collocating RFP Professionals, Owner’s Project Manager, and Design-Build Team Staff
Client/Owner
U.S. Military Academy
Design-Builder
FSA + JKC Joint Venture One, LLC
Design-Build RFP A/E
Atkins Global General Contractor
J. Kokolakis Contracting, Inc.
Architect/Engineer
EwingCole
Specialty Contractors
• AECOM Technical Services, Inc. (ATFP & Structural Engineering)
• QPK Design (Building Envelope)
• Pennoni Associates, Inc. (Civil Engineering)
• Weston Solutions (Civil Engineering Support)
• Argus Architecture & Preservation, PC (Historic Preservation)
• MJ Engineering & Land Surveying, PC (Surveyor)
• Building Science Corporation (Hygrothermal Modeling and Analysis)
The Scott Barracks teaming philosophy was for every team member to act in the interest of the project and the USMA cadets first.
As the first renovation in the Cadet Barracks Upgrade Program, this project had to be completed in 11 months so that swing space was available for the remaining nine barracks renovations. The number of working days it took to deliver the 95% construction package.
In order to minimize the impact to the West Point cadets, the Department of the Army and USMA established an aggressive period of performance for this $54.5M project, contractually requiring the Design-Build Team to complete design and construction, suitable for cadet occupancy, in 387 days.
For greater efficiency, the Design-Build Team made a risk management decision to take the owner’s bridging document BIM files and not redraw the work. Instead, any inconsistencies were corrected within the file.
Construction documents were issued in a multi-package/fast track fashion in order to give the builder sufficient time to meet the schedule.
Implementation of a six day work week, second shift and overtime to maintain the aggressive schedule and staggered trades in order to maximize productivity.
Work flows were established to take advantage of the vertical nature of the building and to avoid congestion, downtime or inefficiencies, while allowing for the integration of successor trades.
Monies saved from this endeavor were reinvested in the construction of a completely new duct bank, with spares, connecting the two wings of the facility.
“The project was completed on time and on budget due to the fact that each party involved shared the same teamwork philosophy. Without this, the project would have never been such a great success.”
– Daniel Middleton, Project Manager, United States Military AcademyHistoric preservation goals, concepts, and standards for the renovation were established as part of the RFP and carried forward through the documentation and construction of the project. The design included repair of the historic exterior of the building as well as substantial alterations to interior historic components.
• Replacement windows replicate the design of the original windows, while meeting stringent UFC ATFP requirements.
• Historic wood exterior doors were restored to seamlessly include modern access control devices.
• Damaged existing historic asphalt pavers on the terraces were removed and replaced as well as the cleaning of those that remained.
• Historic concrete site steps at the west end of the building were repaired.
Several state-of-the-art HVAC design considerations and strategies were used to provide an energy efficient building that meets the Energy Code (2007 ASHRAE 90.1) requirements and achieves LEED Certification. These included:
• Night setback temperature setting to reduce energy consumption and the utilization of occupancy sensors.
• Variable volume pumping for the hot water systems to reduce the water flow rate
• Total energy recovery wheels, transferring both sensible and latent heat, precondition the outside air and reduce energy consumption.
A new chilled water supply and return piping was valved and capped in the mechanical room for connection to the forthcoming campus chilled water system.
A whole-building energy simulation was done on the Scott Barracks Renovation and Modernization project using Carrier HAP v4.61.
The energy model showed a LEED energy cost improvement of 16.2% over a baseline building design.
Utilizing the UFC 3-400-01 metric the total energy consumption savings is 38.5%.
Investigation via selective brick removal established the elevation of the weeping point of the parapet membrane and implications to the perimeter flashing replacement. The removal of the sealant above the parapet counter flashing exhibited trapped moisture in the wall. Moisture meter testing down the brick face of the parapet wall indicated increasing moisture levels moving down the wall (the highest reading being just above the sealed flashing). Based on this finding the existing weep location was corrected.
Hygrothermal Modeling and Analysis: The Design-Build Team utilized Hygrothermal Modeling and Analysis augmented by material testing of the existing envelope. The findings of these results informed the basis of design for the most energy efficient building envelope possible.
ATFP Modeling & Design: A two step-process was utilized to deliver the ATFP Window Framing Betterment. There were 34 different window types and a total of 364 windows affected by this requirement. The first step utilized High-Fidelity, Physics-Based (HFPB) finite element simulations using the commercially available LSDYNA software. The second step utilized a bundle of protective software sponsored by the United States Army Corps of Engineers including CONWEP, SBEDS, and HAZL.
While designing a glazing system to meet the AT/FP criteria is straight-forward, anchoring such windows is very challenging due to the existing un-reinforced façade elements and the offset of the window from the interior stud wall system.
The bridging documents proposed six-inch deep structural steel tubes to support the windows. Assuming a 10 ft. long element, the lightest tube would weigh around 65 lb. Our approach was to use more efficient systems to resolve the blast loads imposed by the window systems. Hence, cold-formed, six-inch deep, 16-gauge metal studs were selected, each weighing approximately 20 lbs.
Betterments included:
• Occupied one month earlier than contractually required.
• Alternative electrical distribution design.
• ATFP window framing – cold formed six-inch deep, 16-gauge metal studs, saving 70% in material weight alone.
• Interior stainless steel railings. Pickets and posts were to be painted steel.
• Cus tom VCT, three color patterns.
• Accent wall paint.
• Cus tom ceramic tile at cadet bathrooms.
• Door hardware upgrades.
• Full-scale barrack/dormitory mock-up including FF & E.
The Design-Build Team initiated a new location for the padmount service transformer and the main electrical room from the basement level of Division 54 to the basement of Division 51 saving $ 250,000 which USMA then used to add new card readers to the scope of work, illustrating continuous design-build value engineering.
Some best practices applied by the Design-Build Team from the RFP through construction included:
1. Utilization of Third-Party Criteria Professional and Advisor for the preparation of the RFP and during the execution of the contract.
2. Evaluation of proposals and selection process with clear basis of award and scoring.
3. Balanced contract language.
4. Partnering & Planning Workshop as part of the Notice to Proceed.
a. Included establishment of communication, lines of reporting and issue resolution methodology.
5. Promotion of collaboration and shared development of teaming philosophy.
6. Collocation of design and construction team during design.
7. Continuous value engineering.
8. Collocation of owner, contractor, criteria professional, and architect during construction.
9. Knowledge Sharing – active log of lessons learned, identifying 58 separate items which have been documented and shared amongst the entire team.
CADET BARRACKS
COMMUNITY SPACE / CLASSROOM
CIRCULATION
BATHROOMS
TAC OFFICES
BUILDING SERVICES
BUILDING STORAGE
CADET BARRACKS
COMMUNITY SPACE / CLASSROOM
CIRCULATION
BATHROOMS
TAC OFFICES
BUILDING SERVICES
BUILDING STORAGE
CADET BARRACKS
COMMUNITY SPACE / CLASSROOM
CIRCULATION
BATHROOMS
TAC OFFICES
BUILDING SERVICES
BUILDING STORAGE
CADET BARRACKS
COMMUNITY SPACE / CLASSROOM
CIRCULATION
BATHROOMS
TAC OFFICES
BUILDING SERVICES
BUILDING STORAGE
CADET BARRACKS
FURNITURE / MILLWORK
CIRCULATION
BATHROOMS
TAC OFFICES
BUILDING SERVICES
BUILDING STORAGE