
3 minute read
Rogan Printing
Kadva Sheri Rogan printing is a 300 year old art of printing patterns on cloth using rogan paste.
Situated in the old city of Ahmedabad, Kadva Sheri was a Muslim community of Rogan printers. This community has been practicing this craft since the past 300 years and so their surnames are ‘Rangrez’.
Advertisement
They were originally from Rajasthan and seeing the business opportunity in Ahmedabad, they shifted to Ahmedabad about 100 years ago. Before this community shifted to Kadva Sheri, it was a community of Kadva Patels, hence the name.
This craft was practiced on the porches of the houses in the Sheri. Both men and women were involved in the process. Some of the printers, also had workshops elsewhere.
Since the process was mechanised, the value of hand-printed cloth decreased. This caused the community to move to other professions, mainly screen printing, 30 years ago.
Hanifbhai
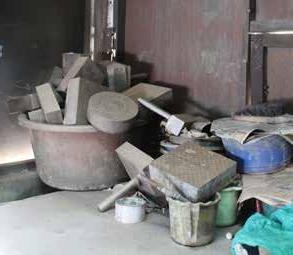
Hanif Rangrez’s family is the only family in the community who still practice this craft.
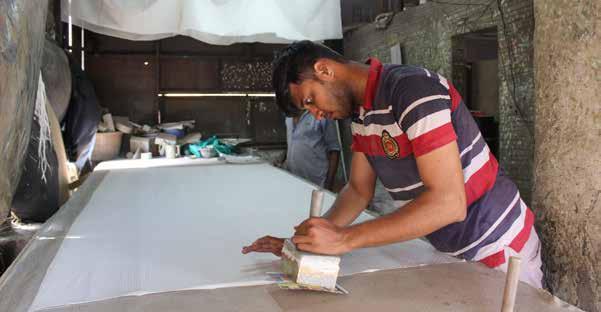
He does Rogan printing along with 1 karigar (helper) and because it is not enough to sustain the family, he does tie and dye and shibori on handmade paper and cloth. The only customers are designers and design students.
Workplace of Hanifbhai
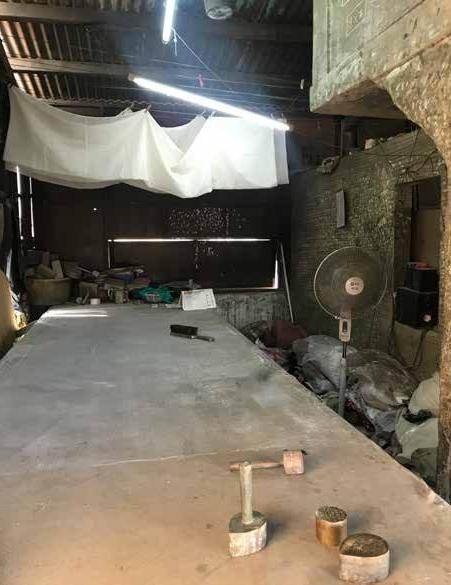

Tools used for printing
Their workshop is on their terrace in Kadva Sheri. The printing is done using a special thick paste made from mixing rogan (varnish), chalk mitti and turpentine. It can be printed on any fabric or paper.
The tool used is a block of wood with a handle which fits into a metal mould with design carved on its base, this tool is called a rogan block.
The paste is filled in the mould and wooden block is put on it. This is placed on the fabric and then the wooden block is pressed to make the design. Once the design is printed on the entire fabric, velvet flock, gold powder or sliver powder is sprinkled on the print and brushed off in a particular manner. It sticks to the paste and the rest of it comes off. The velvet flock comes in different colours and is used for smooth effect on the design.
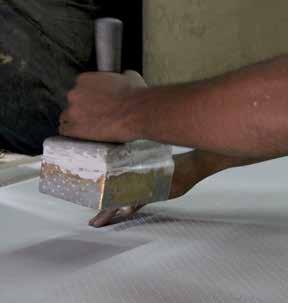
The gold and silver powder give a metallic effect and sometimes, real gold and silver is also used. When the gold and silver powders are used, the fabric needs to be washed after spreading to properly remove the excess powder.
The prints are slightly embossed on the fabric. This takes minimum 24 hrs to dry and if the weather is not sunny, it takes upto 3 days.
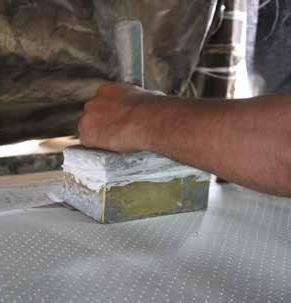
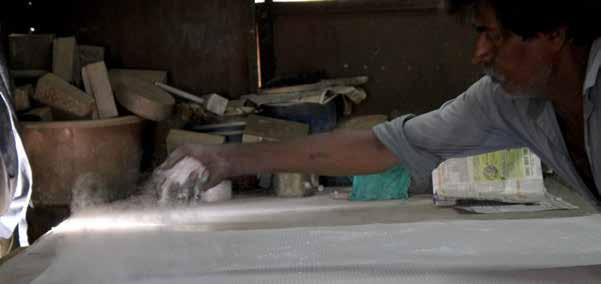

Brushing off the powder Rogan print
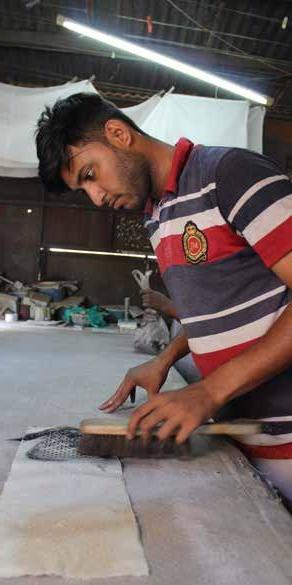
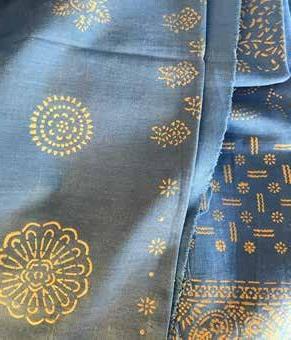
They bring the ingredients from Rajasthan and Mumbai. The tools used for the printing are from Rajasthan and the same tools are used since the practice started as they are not manufactured anymore in todays time.
What used to be community of Rogan printers is now just a family. This art is not passed on to the newer generations, due to the mechanisation of the process, leading to a decrease in the value of hand-printed cloth.
Haniqbhai’s family is a part of the living heritage of Ahmedabad.
Sprinkling gold powder Rogan print



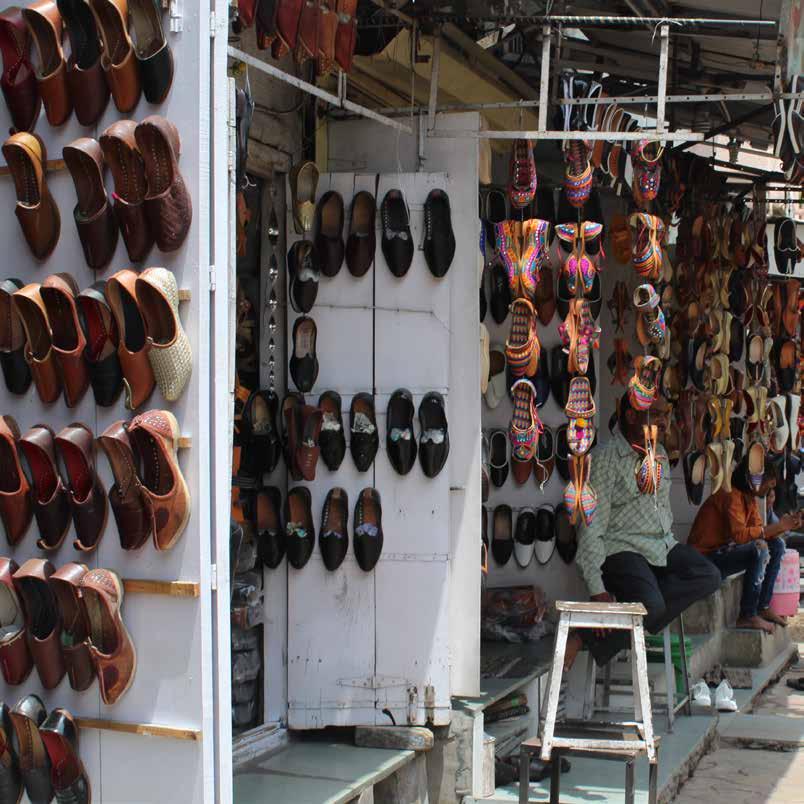