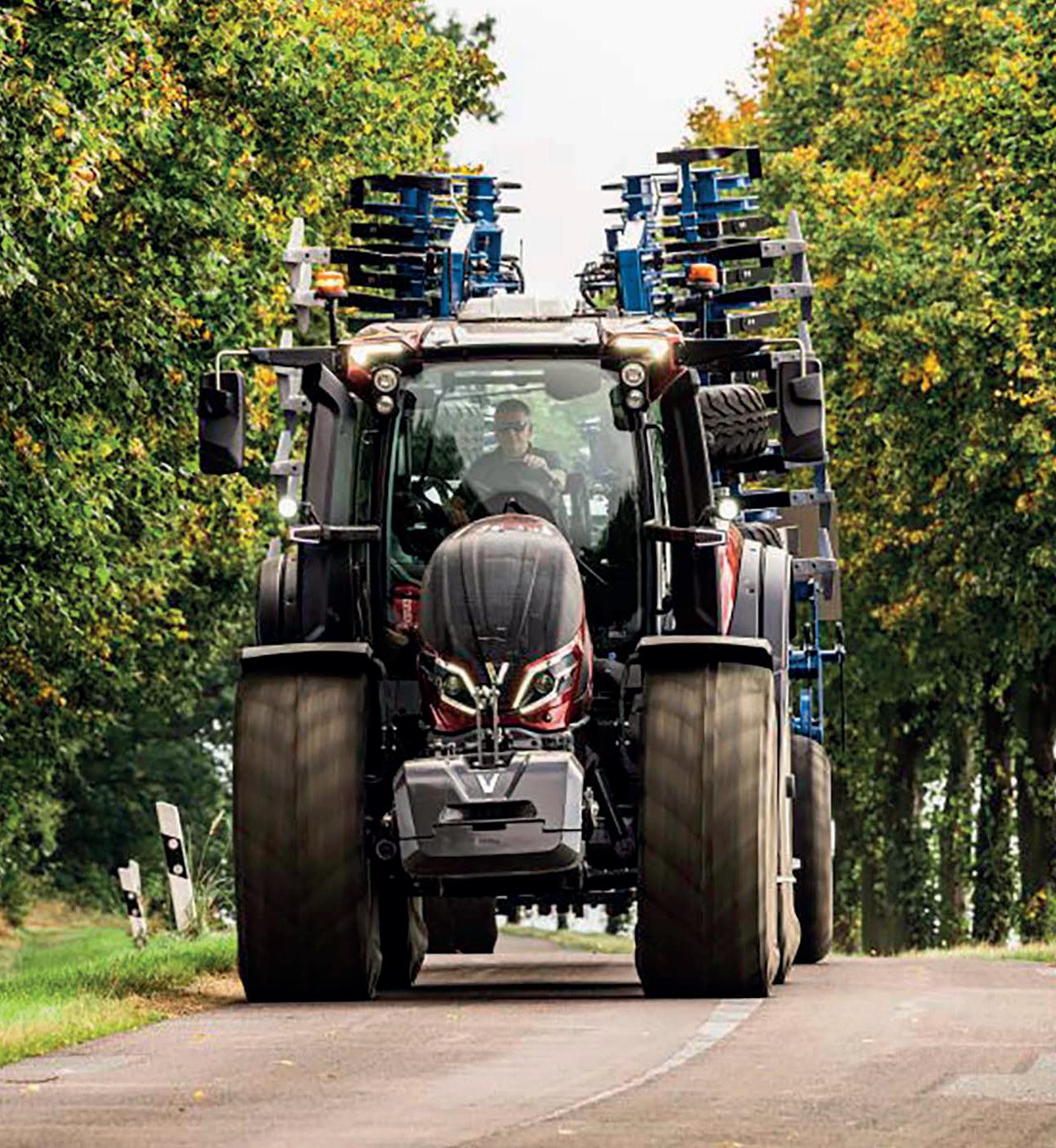
12 minute read
New mid-HP tractors from Valtra
After more than five years in development, Valtra has launched its high performance Q Series tractors equipped with an AGCO-sourced continuously variable transmission. Simon Henley reports.
Valtra launches Q Series
The unveiling of the all-new Q Series completes the Finnish manufacturers fifth generation portfolio, with a line-up that has been developed to slot between the current S Series and T Series models.
Designed and built at Valtra’s X

The Valtra Q Series is designed to fit in between the T and S ranges.
SPECIAL OFFER
SAVE £40 ON RED TRACTOR FRESH PRODUCE & CROPS MEMBERSHIPS
When you transfer or join as a new member with SAI Global between 15/08/22 - 31/12/22
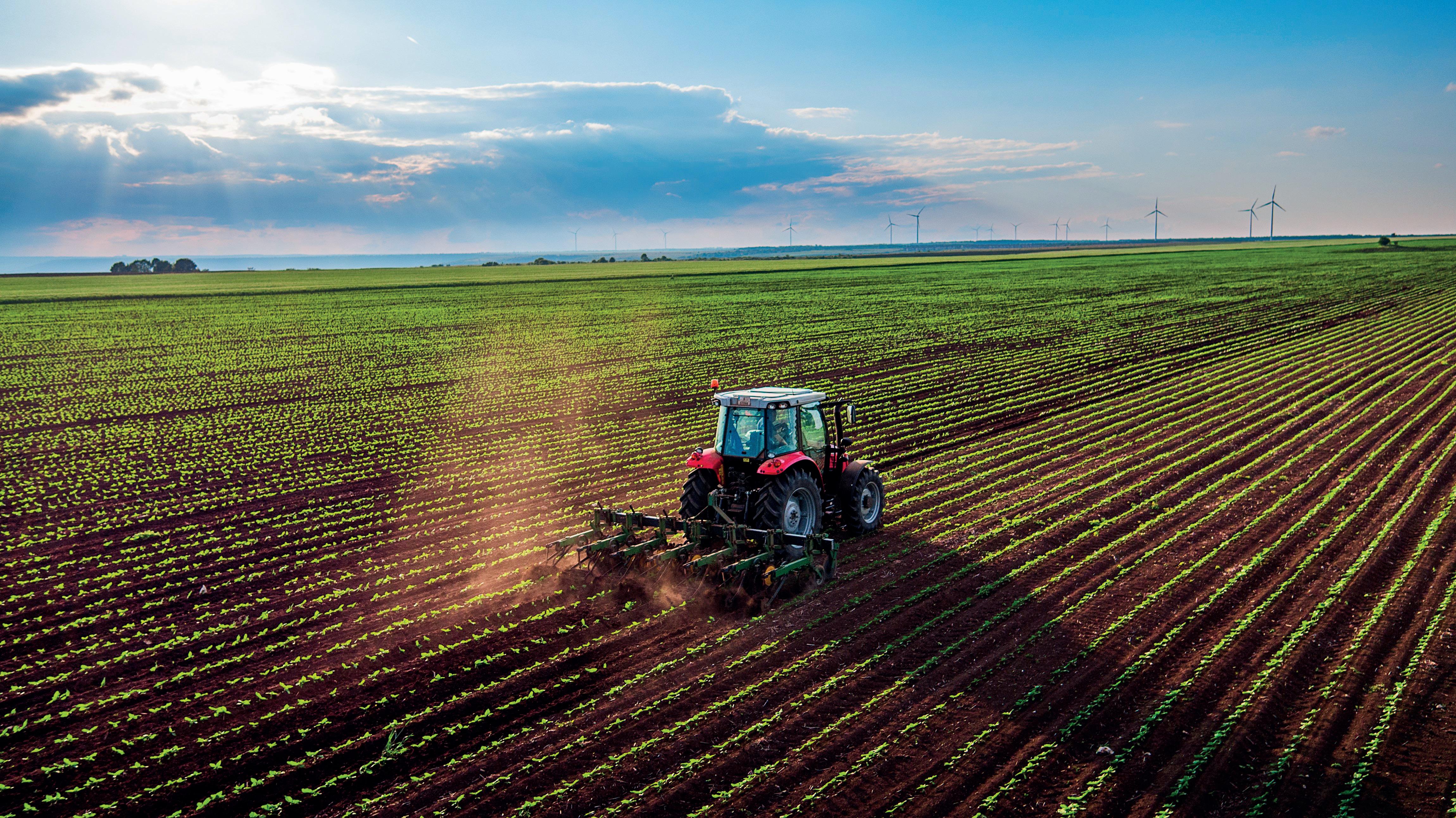
Call: 01908 249950 Email: agrifood@saiglobal.com
T's & C's Apply. Offer cannot be used in conjunction with any other discount.

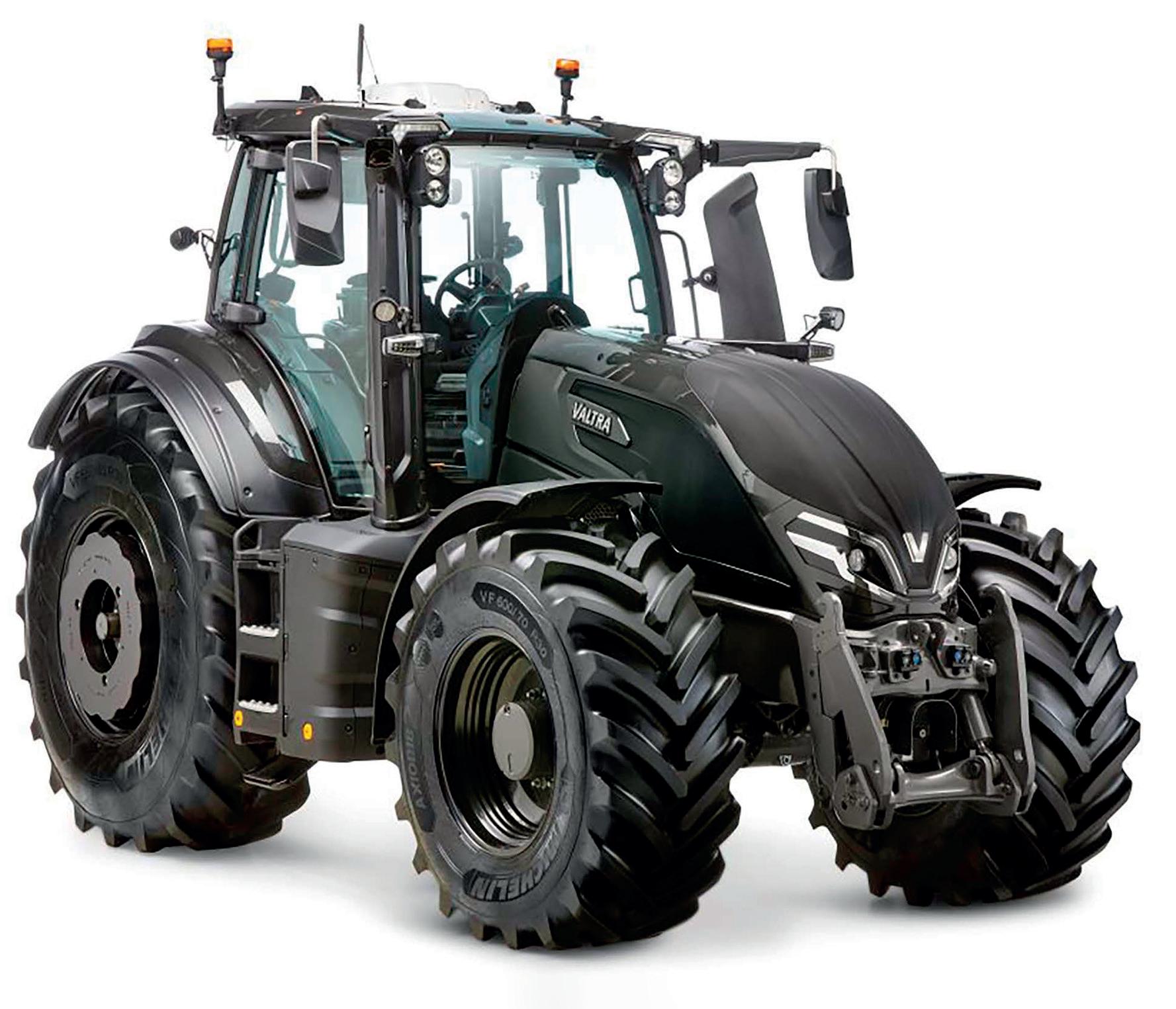
Suolahti factory in Finland, the new range introduces five models with power outputs extending from 230hp up to 305hp.
As the demand for medium-weight powerful tractors with a high specification of equipment and a continuously variable transmission (CVT) continues to grow, the Q Series has been launched as an easy-to-use intelligent tractor range, with a favourably low cost of ownership.
You cannot ignore the fact Valtra is a relative latecomer to this popular sector of the European market, where there is already plenty of competition from other manufacturers. So what does the new Q Series bring to the table?
Stability
Starting with the basics, the new models feature a low working height and a long wheelbase, to reduce the centre of gravity and improve operational stability.
Under the hood, you will find the well-proven AGCO Power 7.4-litre engine, which boasts the largest capacity in this market sector. Maximum power occurs at 1,850rpm, with peak torque arriving from 1,000rpm upwards.
Tipping the scales with an unladen weight of 9.2 tonnes, the range-topping Q305 boasts an impressive 30.1kg/hp. Which is more power per kilo than a John Deere 6250R, which previously topped the charts with a score of 31kg/hp.
Underneath its distinctive sheet metal, the new Q Series shares its powertrain with the Massey Ferguson 8S range.
Like the MF models, the Valtra Q Series has adopted the Fendt-designed AGCO ML270 Vario transmission, instead of using its own built in-house Direct CVT unit.
The reason cited for adopting the AGCO Vario transmission is its ability to reliably handle the high torque loads of up to 1,280Nm produced by the Q Series engine.
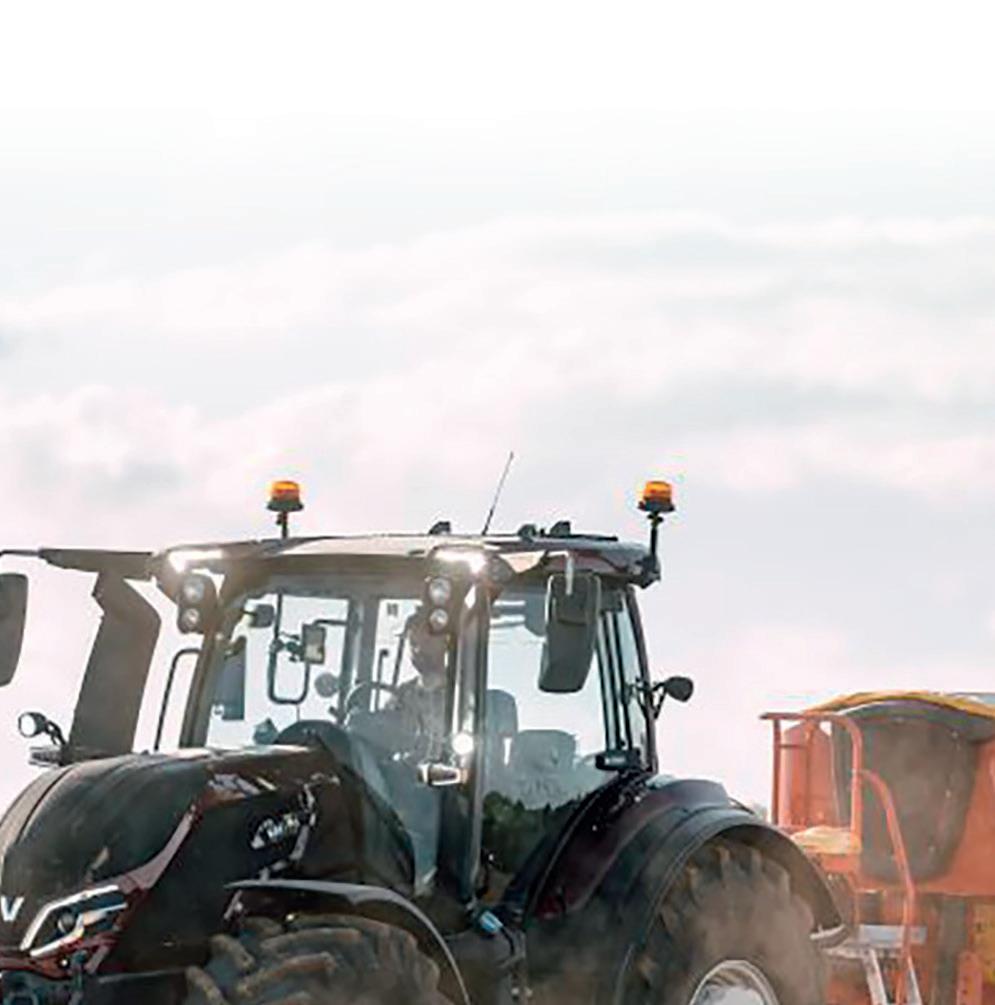
Maximum speed
Unlike Fendt Vario models, which offer a maximum speed of 60kph, AGCO has mandated the Valtra Q Series models will only be available in 40kph or 50kph specification.
The Q Series cab is shared with the Valtra T Series. This well-designed operator station provides identical specification levels with the same updates to the internal layout, including the A-pillar display introduced in the T Series last year.
In terms of tech, the Q Series is available with Valtra Connect Telematics, Auto U-Pilot and the SmartTurn headland system. You can also spec the cab with the TwinTrac reverse-drive set-up.
The base price for the new flagship model is listed at £197,350 (mrp). Production is scheduled to start this autumn, with the first examples arriving in October.
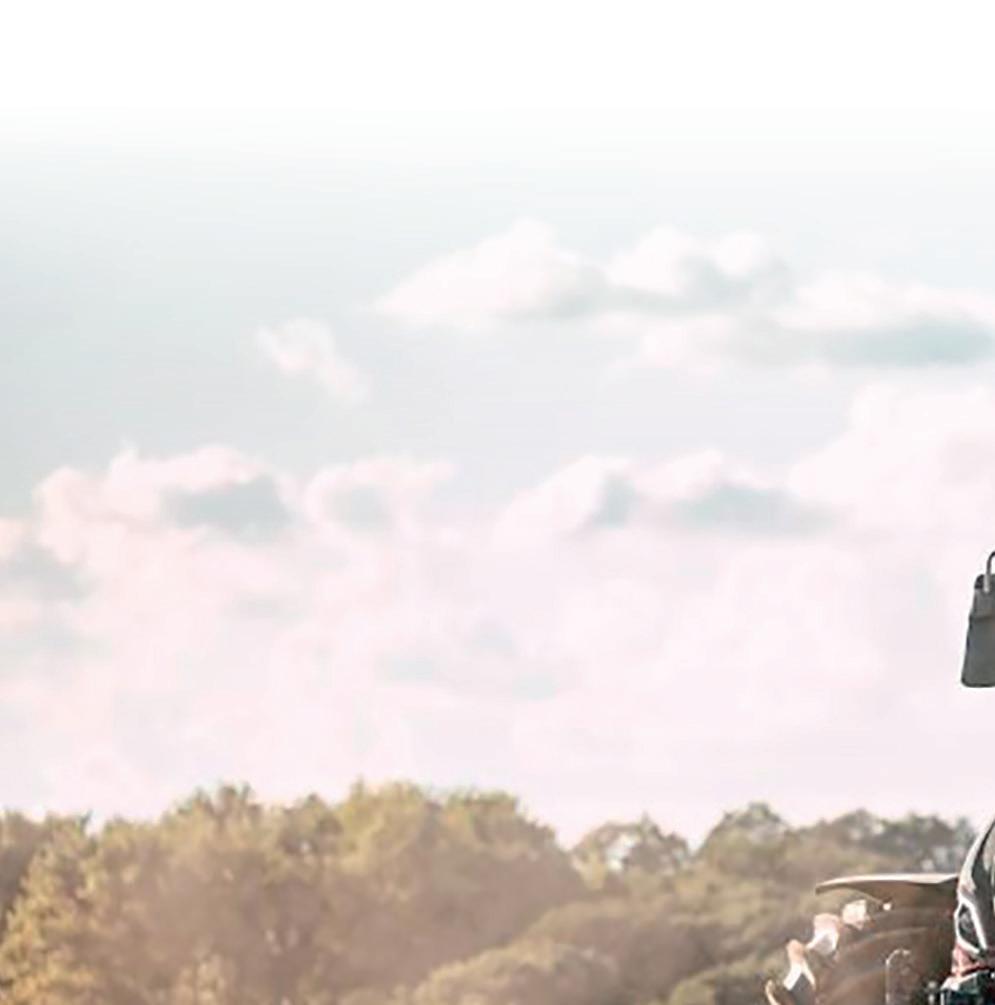
The five-model range offers a maximum power output of 305hp.
Valtra Q Series
Model Horsepower Torque
Q225 230 (250 max) 1,000Nm
Q245 245 (265 max) 1,100Nm
Q265 265 (290 max) 1,200Nm
Q285 285 (305 max) 1,280Nm
Q305 305 (N/A) 1,280Nm
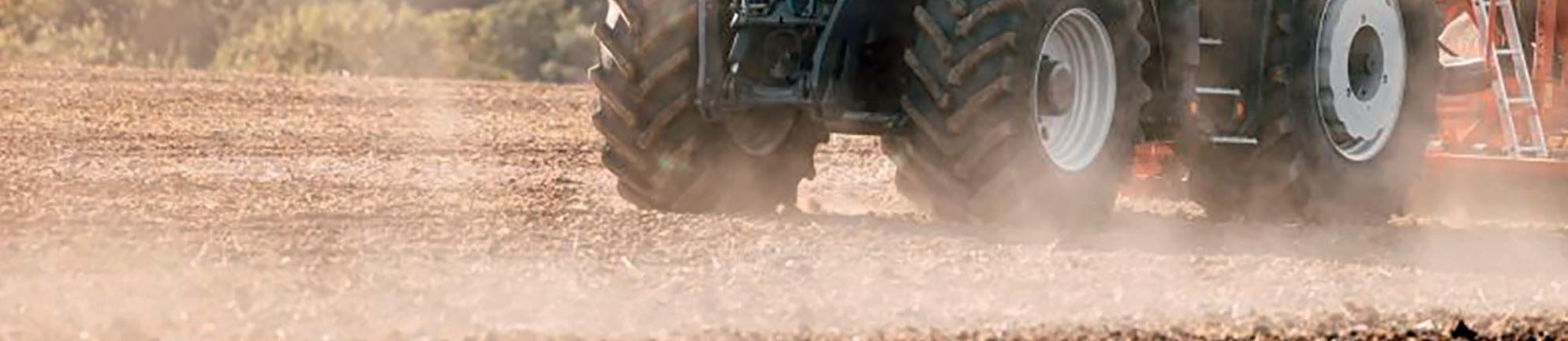
The use of technology to help manage crops is set to gain further importance as we seek to use resources more economically and responsibly. Jane Carley talks to one of the pioneers of implement guidance systems.
Looking into the future
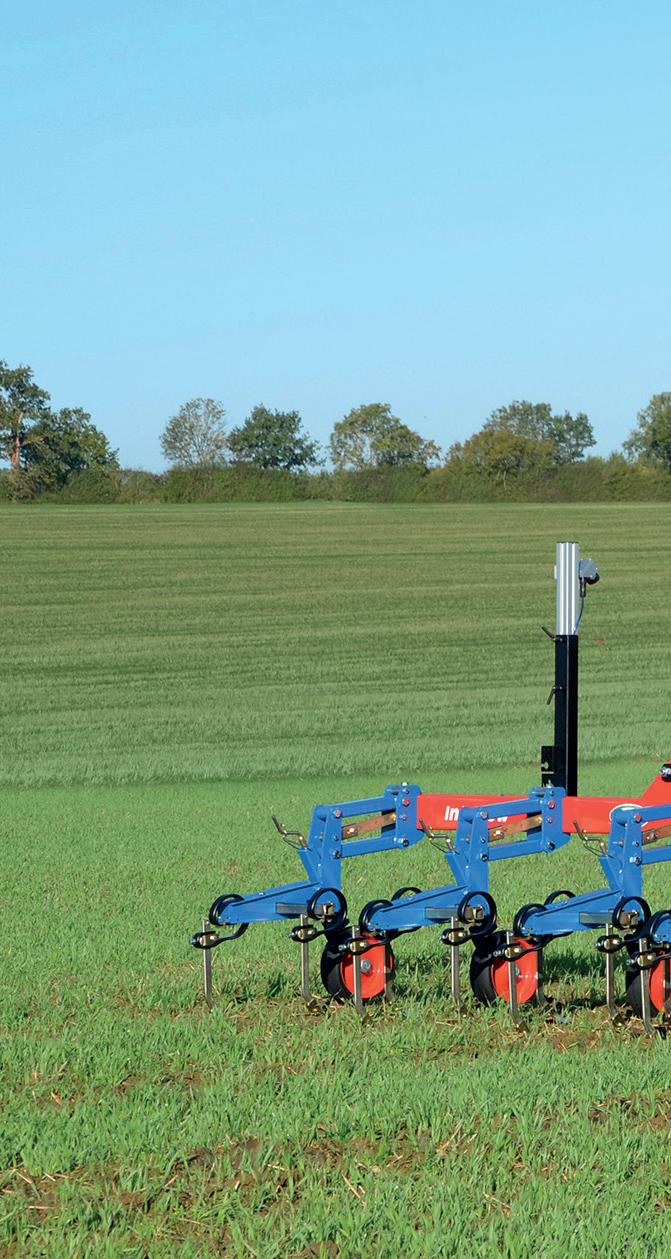
Visual assessment of crops and their weed competitors has always been key to achieving maximum yield potential, but with increased mechanisation, farmers are increasingly reliant on their equipment to provide information on crop status.
Use of autonomous machines will take this further, using cameras linked to artificial intelligence algorithms to identify threats such as weeds and treat them without the intervention of the operator.
It is fitting then that the first forays into vision guidance for machines by camera system pioneers Tillett and Hague were part of an autonomous vehicle project which began at Silsoe Research Institute in 1993.
Nick Tillett, director at the company, says: “We were studying the possibilities for selective spraying in vegetables and by 1996 were using camera guidance on an autonomous vehicle to spray cauliflowers.”
Weeding
However, developments soon turned towards more immediately available tractor-drawn implements and to mechanical weeding rather than chemical application, he says.
“There were fewer barriers to commercial uptake when working with a mechanical weeder, mainly due to the regulatory issues involved with chemical application. We could simply implement the technology on tractor-mounted hoes and manufacturer Garford Farm Machinery was one of the first to adopt it.”
While still working as researchers for Silsoe’s main sponsors, the Biotechnology and Biological Sciences Research Council, Mr Tillett and Tony Hague also gained commercial partners and when SRI closed in 2005 they established a business to continue their work.
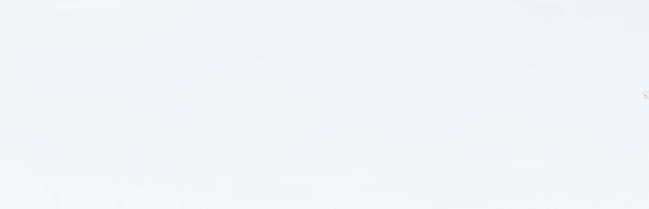
Transplanted crops, such as brassicas and salads have distinct heads, so require in-row weeders to tackle weeds that grow between the plants.
“Mechanical weeding was an established technique for crops such as sugar beet and there was sufficient interest to build a number of commercially available models,” he says.
The market has since expanded significantly. Still based at Wrest Park, Silsoe, Tillett and Hague operates as a hardware manufacturer mainly

Range of applications for vision guidance
JAt its basic level, mechanical weeding presents quite a simple task for camera guidance, says Nick Tillett.
“Cultivating tools are required to work between the crop rows, pulling out or cutting weeds, so the camera identifies the rows and, working in real-time, activates a side shift or steering mechanism to align them.”
However, transplanted crops such as brassicas or salads have distinct heads, so weeds can grow between the plants, potentially outcompeting them and reducing yields. In 2005, the company developed rotary

NICK TILLETT
supplying original equipment manufacturers (OEMs) and in industry-funded research.
Compared to the early designs, modern vision guidance systems have the benefit of increasingly powerful computing platforms.
“Using hardware of roughly the same size and cost, processing of camera data in the cab is now possible, while the camera technology has also improved,” he says.
Cameras
“Systems developed in 1993 used monochrome analogue video cameras moving to colour USB II cameras for the first commercial machines, which then transferred data through Apple’s standard FireWire and now Gigabit ethernet.”
Software has also moved on, although Mr Tillett says it has been possible to build on some of the original 1990s code, layer on layer.
“Equipment is certainly more robust and user friendly, which is important because we were initially working with technology enthusiasts who are more tolerant of the inevitable issues that occur. As products head to the mass market, training of operators and serviceability of equipment become part of the task.”

Training
Tillett and Hague works almost exclusively with OEMs, so its role is ‘training the trainers’ but luckily, the company had begun to develop a library of video tutorials for manufacturers and end users just before the pandemic.
“Some OEMs are specialists, but their dealers will have more general skills so it’s important to present the information in a way that can be easily understood.”
Range of applications for vision guidance
Nick Tillett

mechanisms for in-row weeding, which worked around the crop heads, requiring their individual position to be identified, rather than just the rows.
Garford Farm Machinery has developed a wide range of inter-row and in-row weeders, using Tillett and Hague camera technology.
“We have also worked with Opico on the Hatzenbichler range and with German company Kult Kress, providing vision guidance for all sorts of mechanical weeders, including a reciprocating blade.
Former Silsoe Research scientists Tillett and Hague have developed camera vision systems widely used on inter-row cultivators such as this Hatzenbichler hoe supplied by Opico.
Flexible
“The technology is really quite flexible but there is still considerably more interest for in-row cultivation.”
Vegetable and other high value crops have proved the main market to date, but he suggests mechanical weeders can operate at higher work rates in cereals, potentially getting closer to competing with spraying.
“It’s possible to use wider machines and, as long as the mechanical parts of the implement can cope, go faster – up to 8kph, certainly and rarely to 12kph. Unlike manual guidance, which can only watch one bout with accuracy, vision guidance can use multiple cameras and control systems spanning multiple passes.”
Most machines in use are single bout, but Garford has a number of 18-metre weeders working, he says, and 12m versions are increasingly popular.
“The challenge remains in mechanical design and also in transporting machinery in Europe.”
Away from weed control, the Tillett and Hague system has been trialled with other inputs, including a BASF project on spot drenching with biological controls.
As for spot spraying, Mr Tillett says the same technology can
Continues over the page.
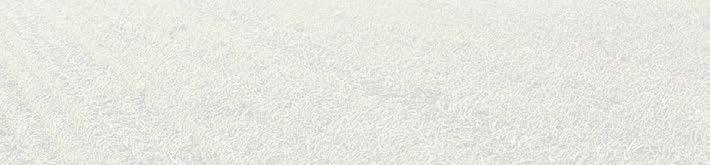
be applied when the market is ready, using data captured by the cameras to switch nozzles on and off.
However, he reports no real commercial interest.
“Even multinational organisations who have acquired technology providers seem to be struggling to get selective spraying off the ground commercially. We have two machines in development, one with Techneat, which is being trialled this summer in high value drilled crops.”
One promising application is for control of large weeds, such as volunteer potatoes in carrots and onions, Mr Tillett says.
“We’ve completed a few tens of hectares of commercial crop. There are similar challenges in terms of work rate to mechanical weeding, plus there is added cost and more sophistication, so greater operator skill is required.”
He adds future drivers in favour of spot spraying will be legislation, concerns about pesticide resistance and lack of labour. Differentiation should be made from patch spraying, he adds, which was the subject of much research at Silsoe.
“In the early days of precision agriculture, Silsoe Research pioneered the use of historical data to map the field and use the data to guide selective spraying. It was governed by the resolution of GPS systems that were available at the time, so as the technology developed the ‘patches’ that could be targeted decreased in size.”
Technology
This approach has been developed further by application equipment manufacturers, large and small, as nozzle control technology evolved. However, historical data can’t be used to target crop threats at plant level, he says.
“True spot spraying targets large individual plants, such as volunteer potatoes. When looking to control black-grass in cereals, for example, it is impossible to target individual plants, so patch spraying is the only technique available. For cereal crops it is certainly more relevant.”
Applying the technology to autonomous machines presents different challenges, he says.
“Work rates are less of an issue for autonomous machines, but implement control becomes more important because a machine can’t automatically recognise a functional problem in the way a human operator can. We have to build in controls that detect when a system isn’t working, stop the operation and request help.”
Tillett and Hague has recently collaborated with French autonomous machine specialist Naio, which has developed Orio, a multi-purpose robot aimed at broadacre crops.
Working over a 1.8-2m track width, the battery-powered straddle robot has a run time of eight to 12 hours and is fitted with central and rear hitches and the option for a pto. Tillett and Hague has provided Orio’s camera guidance for electricallyoperated inter-row hoeing tools and rear tool carrier.
“We were introduced by Kult Kress which produces implements for Naio,” Mr Tillett says.
“Larger frames are generally easier to work on and to place cameras so they can easily see the crop. On smaller rear-mounted implements, for example, the tractor frame can block out the cameras.”
Mr Tillett suggests demand will continue to grow for camera guidance on tractordriven machines as well as autonomous systems.
“Autonomous machine developers still face challenges over safety in Europe due to the size of land areas and public access. Smaller machines are perceived as safer, but still cost as much to develop and are less productive. Several manufacturers are sticking with tractor-driven machines as well as developing autonomous systems and fortunately our technology can work with both.”
Away from crop protection, machine vision may have a role to play in planting and harvesting, tackling the labour shortages which, for many countries, are as big an issue as crop safety and environmental concerns.
Tillett and Hague operates increasingly in Europe and has ridden out the difficulties of Brexit largely due to its high value product and good margins. Appointing an operations manager to look after the commercial side allows the two partners to focus on further research.


In-cab image processing is now possible, thanks to significant developments in technology, says Mr Tillett.
Implements are getting wider – this 18m unit from Garford is for the export market, but 12m hoes are increasingly common.
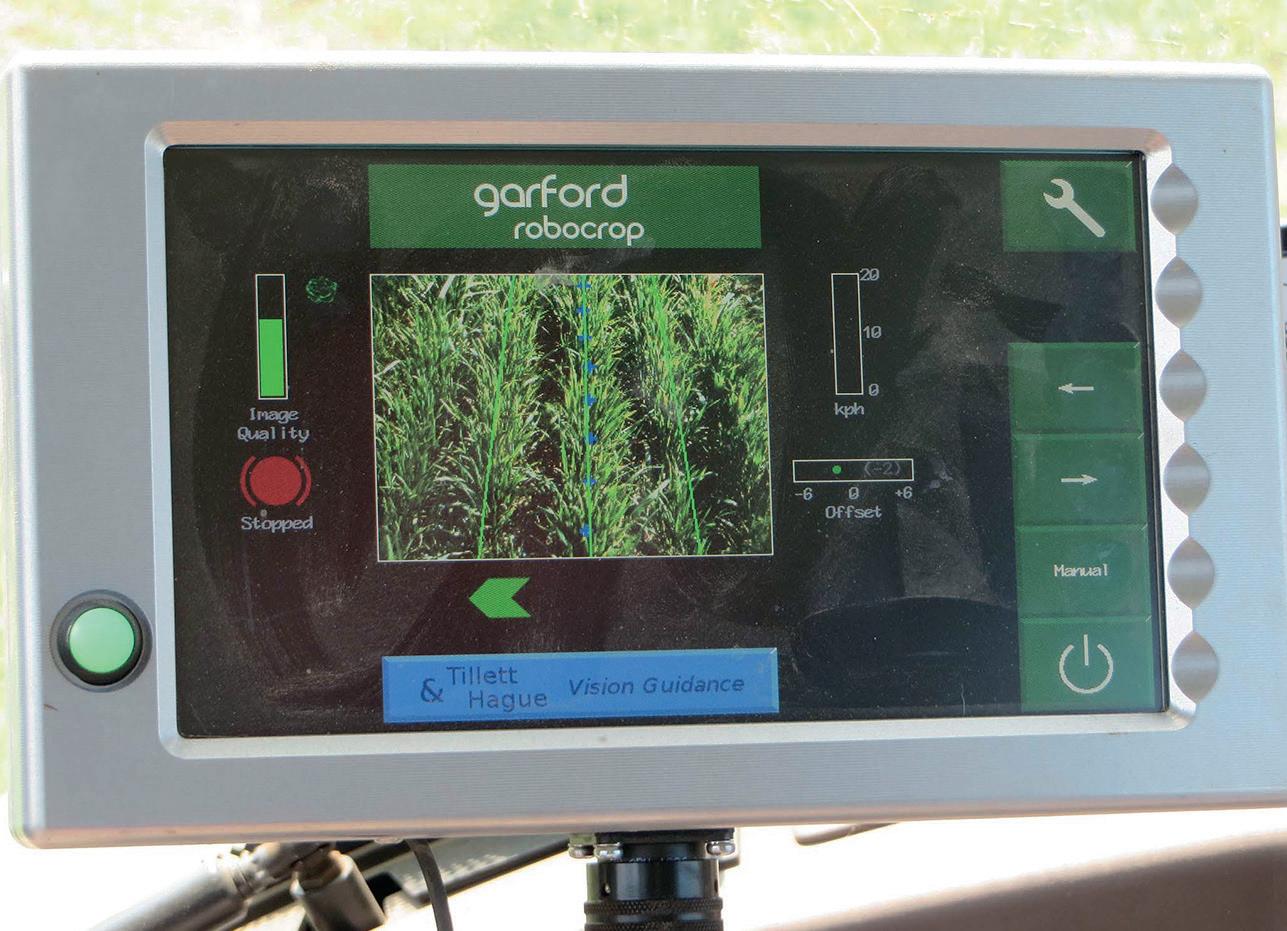
Interest
Looking to the future, Mr Tillett suggests restrictions on active ingredients are driving interest in non-chemical weed control more widely.
“In France, there is already increasing demand as the choice of chemical products becomes limited for important crops such as maize and sunflowers, so we need to be ready to take the opportunity.”