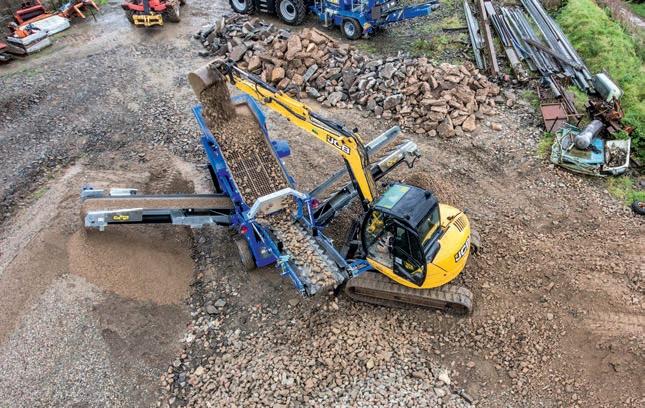
6 minute read
Herbst screener adds to contractor’s crushing operations
Having invested in a tractor-towed crusher and a compact screener, one Devon farmer is turning concrete and rubble into recycled hardcore, Geoff Ashcroft ent to meet him to fi nd out more.
Towed screener boosts contracting business
Looking for an opportunity to supplement income from the family-run 50 hectare Whitehouse Farm, Winkleigh, Devon, James Boundy turned his attention to on-farm crushing and screening services.
“Alongside our forage wagon harvesting business, we have been offering stone picking and burying services, says r oundy.
“It just seemed logical that if we could pick and bury stones for customers, it made sense to look at other ays of dealing ith stone.
“The ability to crush and screen to produce recycled materials seemed a sensible progression.
In early 2018, the business invested in a tractor-powered Herbst Agri
Crusher, to take advantage of ripping up and recycling concrete cow tracks, shed bases and other on-farm stockpiles of un anted aggregates.
“I looked to hire an Agri Crusher to begin with, just to see how it performed, says r oundy.
“But in the end, I bit the bullet and bought one. liked the fl e ibility
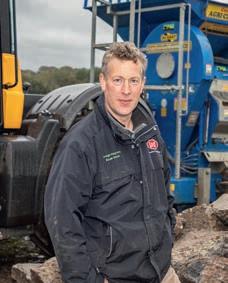
Herbst Compac Screen has a self-contained engine and hydraulic pack, capable of delivering a throughput of up to 150 tonnes per hour.
and convenience of being able to tow the machine from farm-to-farm using a tractor.
“Compared to using a digger with a crushing bucket, which needs specialist transport, this is a
JAMES BOUNDY
convenient solution.
“The Agri Crusher has processed around 12-15,000 tonnes of materials so far, and we have recently added a Bluetooth camera/monitor to watch the jaws of the crusher, to help make the most of productivity, he says.
Towed by a JCB Fastrac 3230 and buoyed by the opportunities to crush materials, the ne t move as to add value to the materials being crushed. The answer he was looking for was also offered in the Herbst stable, in the guise of its ompac creen.
Having been awarded a gold medal in the diversifi cation category in the LAMMA Innovation awards (see pages 94-96), it grabbed Mr Boundy’s attention while visiting the show at the in anuary .
The trailed screen uses its own on-board power supply and hydraulic system, and could be parked on-site and prepared for use in minutes.
In addition to being used as a standalone machine, it has the potential to be placed under the discharge belt of his Herbst Agri Crusher, for direct feeding of crushed materials.
Each of the three conveyor belts are hydraulically folded to reduce the machine s si e for transport. Unfolding them reinstates tension for each belt, and readies the unit for ork. ngaging the vibrating screen bo provides the shaking function to sieve materials being loaded.
Materials
Its upper shaker deck removes over-sized materials, which are dropped onto a conveyor belt that stockpiles larger product at the rear of the machine.
Smaller material cascades down over a lower sieve deck, producing two graded sizes that are unloaded

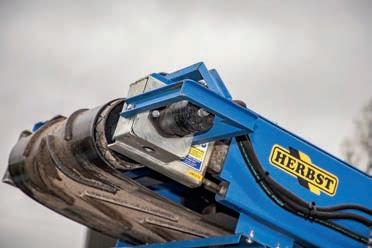
Mr Boundy has made guards to protect the hydraulic motors from accidental damage.
by conveyor belts on either side of the machine.
“It looked a really useful bit of kit, that could handle different materials,” says Mr Boundy.
“I had a local turf company looking for someone to screen 1,000 tonnes of top soil, and it also has the ability to screen compost to meet PAS100 quality standards.”
Towed by tractor, the Compac Screen has already received a few orking modifi cations, to improve on-site set-up and durability. he screen s fi ed front skids meant that it was tricky to set-up unless you were on a level site,” he says.
“So we replaced them with Jost landing legs from a lorry trailer, so we could wind them up or down independently, to get the machine set correctly for optimum output.
“And using bolt-on legs, we can adjust their position through a series of holes, if we need a greater range of adjustment,” he adds.
“We have also replaced the small road wheels with larger diameter items to improve ground clearance when visiting farms, and this is a really useful feature for access.”
To load the screen, Mr Boundy says an t midi e cavator is the ideal solution. deally, you position the e cavator to load the screen from the front, but a short radius e cavator could sit anywhere, as long as it can reach the top deck,” he says. Going for ard, a ide intake bo would be much more practical, and this could then be loaded using a telehandler and bucket.”
Productivity
In terms of productivity, he says the screen is impressive, with a throughput of 100 to 150 tonnes per hour depending on the materials being screened.
“It can soon make a good pile of material under the conveyor belts. So you either move material from under the belts, or hitch a tractor on and pull the screen forward.”
When screening soil, he says best results come from dry material that crumbles and fl o s easily.
“Aggregates are far more easily handled, but wetter materials can cause a build up of fi nes that can eventually block the screen decks,” says Mr Boundy.
“And occasionally, I need to switch off and reach in using a rake or hoe, to scrape the decks clean, to restore the separation quality.
“It is a very simple and robust machine, which works really well, though we have implemented a few changes to make it better for our own applications.”
He says that over-loading the feeder bo can sometimes see material spill down through to the engine bay, having forced its way past a protective rubber fl ap.
“I have added a piece of steel plate to close this area off and stop the overfl o from happening. And ith hinges fi tted, can lo er the plate and still access the sieve deck for cleaning.”
He has also added hinges to a bolted access panel on the right-hand side of the machine, to make it easier to grease the side conveyor belt’s lower rollers, and also to improve access for cleaning. e has added an e tended e haust pipe, to prevent the machine from becoming covered in soot.
“It is a great machine, but we have found that farm life can be more demanding than working with builders, and we have simply made the Compac Screen better suited to our varied workload,” he says.
Typically, he reckons the screen will run for around two days on a tank of diesel, hinting at the Yanmar engine’s economical operation.
“There is no fuel gauge, just a small sight tube, though it only shows the last quarter of fuel tank capacity, so it only warns you when you are about to run out. It would be more convenient if the sight gauge e tended up near the top of the tank.”
Adding a piece of box-section steel has enabled cleaning tools to be carried. Jost landing legs have been added to provide greater adjustment on steeper sites.
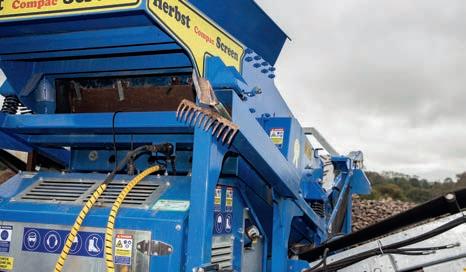
HERBST COMPAC
SCREEN Z
● Power: 27hp Yanmar ● Separation: Three-way split ● n a en ei ht 5,450kg ● List price: From £45,000
he screen’s e ront s i s meant that it was tricky to set-up unless you were on a level site
JAMES BOUNDY
Recycling
For the Boundy family, the purchase of the mobile screen for on-farm recycling has yet to gather momentum.
Mr Boundy says: “While the machine has not yet done a lot of work, it does offer a really useful means of improving the value of crushed materials.
“It is not an obvious choice for farmers, local builders or landscapers, but it should be.
“Compared to the cost of disposing of unwanted materials, we can crush and screen on-site, to provide a really useful recycled material at a much lower cost than they can dispose of, and buy-in quarried aggregates.”