
10 minute read
Customer open day celebrates new building investment
Machinery Customer open day celebrates new building investment
Vegetable and crop handling specialist, Tong Engineering, welcomed customers to two early July open days to celebrate the opening of its new, state-of-the-art manufacturing facilities. David Williams was there.
Tong’s new 90,000ft2 factory is on an industrial estate on the outskirts of Spilsby, Lincs, just a short distance from the shop in the centre of the town where the business started in the 1930s, and which still displays the Tong trading name.
The original product o ering was modest, including simple but popular items such as sack barrows and pig pens.
During the 1950s, an old candle factory was purchased and manufacturing of potato graders commenced, re ecting the crop’s importance in the local area. Adjacent properties were added in the 1960s as demand for the products grew, and Ken Tong built the business to satisfy growing demand for a wider range of vegetable handling equipment.
In 1972, Ken’s son Charles joined the business and by the 1980s the rst Caretaker graders were introduced which remain market leaders today.
Local competitor Peal Engineering was acquired in 2005, and a second factory premises at Wain eet was rented allowing the product range to be expanded to include washers and polishers for potatoes, carrots and other root crops – sold under the Tong Peal trading name.
Charles ran the business until 2015 when he became chairman, and his son Edward, who had gained experience working in several areas of the business and moved up through the ranks, took over as managing director. The company’s branding reverted to Tong.
Demand for the products continued to grow and, in 2020, Tong purchased three hectares of land on a green- eld site for the new factory. Building was completed by early summer 2022.
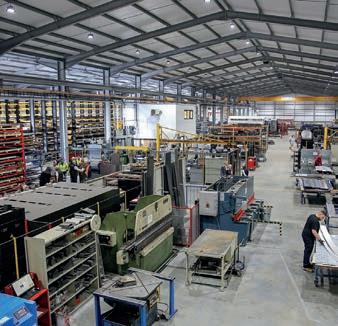
The large fabrication and machining area.
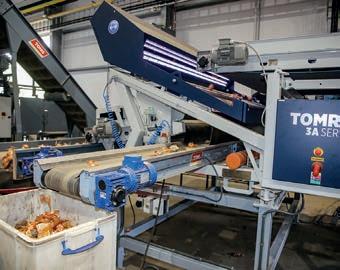
The Tomra Optical Sorter scans the crop and identi es anything that shouldn’t be present. The new Tong factory on the outskirts of Spilsby, Lincs.
achieves product and service sales in excess of £20M, and machines are exported to more than 50 countries. “We are not just root crops,” explained sales director Charlie Rich. “We have a strong reputation in the vegetable handling and processing market too. Tong is regarded as a very good employer in the area which means that people tend to stay for longer, and the company bene ts from their extensive experience.”
In-house manufacture and design
Almost every aspect of the machine design process is carried out inhouse, including electronic control panels which are also assembled on-site. More than 30 hoppers of various sizes are made annually. Metal grading screens have been manufactured by the company for more than 50 years, and more than 1,250 are made each year by hand.
Tong has a very strong reputation for conveyor manufacturing too, and 5,000 roller barrels are made each year.
Recent developments including changes to electronic control systems were highlighted. From manual two-way switches to electronic controls, then remote control and control through the internet by app. As remote control has become more widespread, safety systems to prevent accidental machine activation have also been developed. Tong’s engineers highlighted that QR codes which must be scanned to prove that an operator is present to check a machine before it is restarted, are a potential solution.
Optical sorting
Tong works with industry leaders in specialist elds to provide the very best sorting equipment. The open day featured the Tomra Optical Sorter, which uses an array of cameras and infra-red sensors to detect anomalies while automatically sorting the crop. For the demonstration a bin of onions was sorted – containing a large amount of soil and large numbers of stones and other debris. Anything that wasn’t an onion was automatically removed – even if it had a similar size and shape to the crop. “Automation is increasingly important when labour shortages are such an issue,” explained Tomra area sales manager Steven Skipper, “and we supply systems for integrating into the Tong grading lines.”
Top level back-up
Tong wouldn’t have become such a success if it wasn’t for the excellent after-sales service available to its
continued over…
Shropshire farmer
Farmer Michael Bubb is pictured at the event. Michael trades as JM Bubb & Son, and Shropshire Petals, and farms at Newport, Shropshire. Potatoes are produced for contracts with McCain and McDonalds, and for the chip market. Combinable crops are grown as well as fresh owers to make natural confetti.
A Tong Caretaker cleans and sorts the potatoes straight from the eld before they are put into store.
“I like dealing with Tong as the company is British, the products are reliable and the Tong team is always interested in what we are doing and solving our problems,” Michael explained. “Like other businesses, we are a ected by labour shortages so looking to the future; increased use of mechanisation must be part of the solution.
“We already use a Tomra optical sorting system for potatoes and for our ower petal enterprise too. It stands alone but works in conjunction with Tong equipment.”
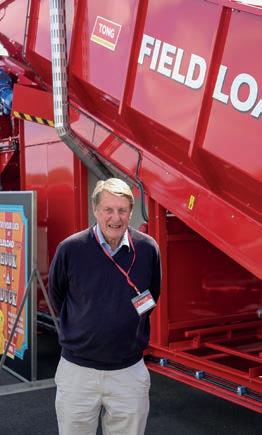
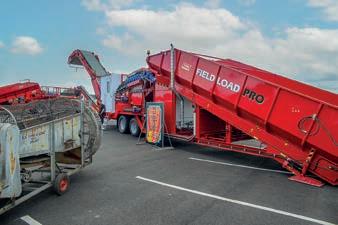
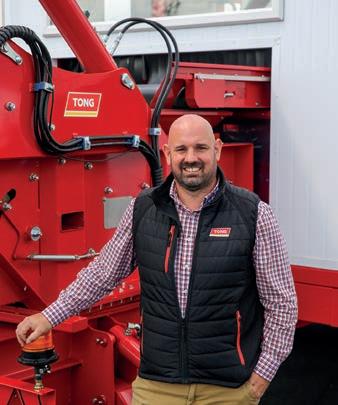
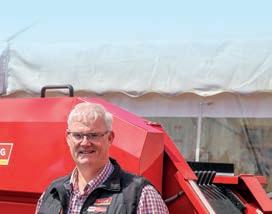
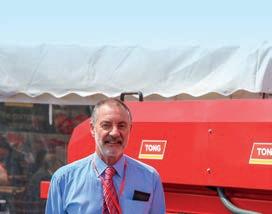
Charlie Rich emphasised that Tong is no longer just for potatoes and other root crops – it designs and manufactures equipment for vegetable and salad crop handling and sorting, too. The Tong FieldLoader will clean, sort and then load the crop straight into bulk trailers in the eld. An on-board generator allows use anywhere, and work rates up to 120t/hr can be achieved. The standard set-up includes a six-row EasyClean and eight rows of Turbo Coils, but as with most other Tong products – bespoke versions are available. A big advantage is soil removal from the crop before it leaves the eld. Most are produced for UK users, but recent exports include to the USA and Canada.
…from previous page customers, and the factory includes new 9m high parts towers, each of which has 40 trays containing up to 500kg of parts. Total parts value at the site exceeds £2M.
Additional engineers are currently being recruited to further improve the back-up available.
The company is working towards the ISO 9001 quality standard for continuous improvement – which it hopes to have attained by mid-2023.
“Demand for our products continues to grow, and although we o er a wide range of standard products, a lot of our business involves integrating our standard machines within bespoke systems to suit our customers’ needs,” concluded Charlie. FG “It’s rare dealing with a company where the fourth generation of the same family is in charge,” explained Burdens Specialist Vegetable Machinery sales and service manager Adrian Harrison, who is pictured (left) with Tong sales manager Nick Woodcock. “I’ve seen the new site evolve, and it’s very impressive.”
Adrian said that the main products supplied by his team include Caretaker Graders, EasyFill box llers and box tippers. “Many of our customers store produce in bulk, so yard-based Caretakers are favoured,” he continued. “But we also come to Tong when we need specialist solutions, including a recent project for a customer which involved a system to blow the outer leaves o cauli owers before they are inspected and chopped.”
Adrian has worked with Tong for more than 30 years and he said that although the factory is only 30 miles from the Burdens depot, the main reason for recommending products to his customers is that they are world class.
“Even when we need bespoke solutions, we are always con dent that what Tong recommends will be successful,” he added. “When we express a view on any of the products then our suggestions are taken on board – they always listen.”

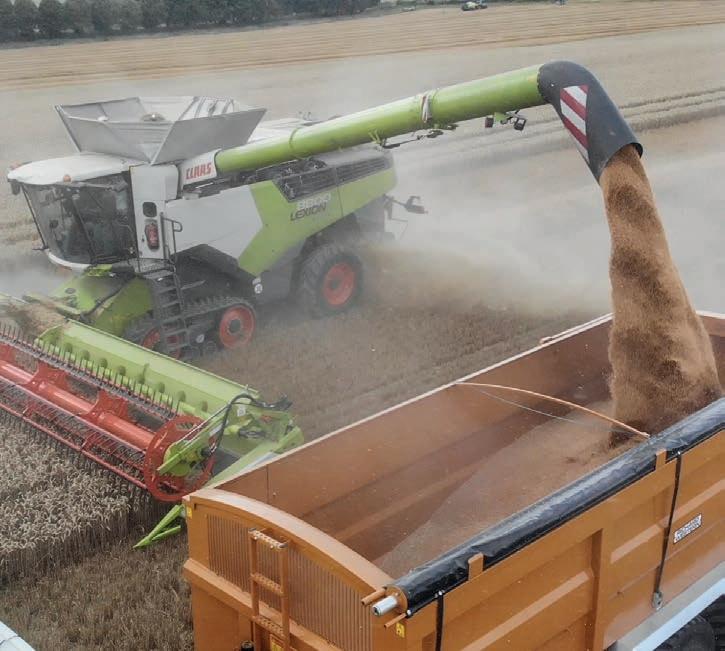
PROVEN IN THE FIELD
CLAAS WESTERN
Please contact your local CLAAS Western branch or call WESTERN Cirencester (Head Of ce) on
Tel: 01285 863190 western.claas-dealer.co.uk
Please contact your local OLIVERS branch or call OLIVERS Luton (Head Of ce) on
Tel: 01582 727111 www.oliveragriculture.co.uk

FARM TRAILERS

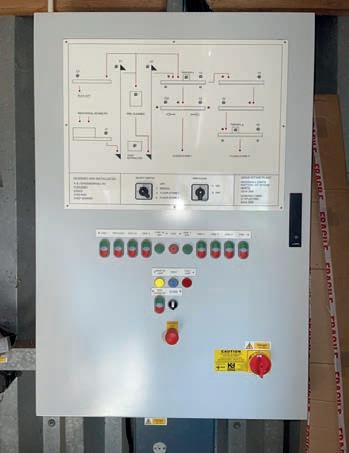
Grain handling business celebrates 40th anniversary milestone
K & J Engineering was established in 1982 when the company John Clarke was working for downsized the grain handling department. John decided to start his own business working in our mills, installing equipment and working alongside companies and suppliers such as BDC Systems, Danagri 3S and Mark Weatherhead.
Today, the company is run by John's daughter and son-in-law, and specialises in all aspects of electrical engineering for the farming industry; including grain handling, oil red burners, and LED potato chitting lights (these range from 6–12ft and can be used hanging or free standing).
K & J Engineering provides all aspects of electrical installations on farms, including grain and oor stores.
Covering most of England and into the Scottish Borders, the company services most makes of old and new oil- red grain driers and also carries spares for most makes, including Allmet, Carrier, Svegma, Farrell, Kentra, Bentall and many more.
Additionally, the company is able to build bespoke designed control panels for installations.
K & J Engineering has been, and continues to be, a member of NICEIC since 1984. FG
Retain nitrogen and reduce emissions with slurry improver

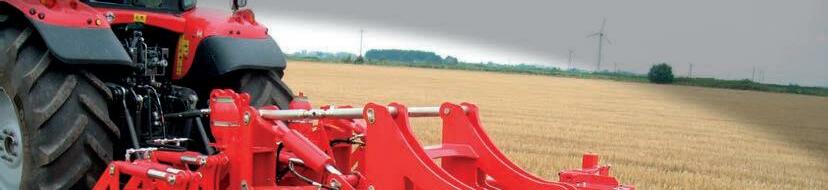
MicroZyme slurry improvers have been launched in the UK by slurry specialist Tramspread. The biological slurry additive reduces solids and ammonia emissions whilst improving nitrogen retention.
Managing director, Terry Baker said: “MicroZyme products will reduce emissions and improve the value of slurry to the crop and soil. The unique bacteria in MicroZyme R (ruminant) and MicroZyme S (swine) break down bre, starch, pectins, fats and protein residues to decrease solids and lower harmful emissions.
“These products will help farmers to meet [Clean Air Strategy] targets and will also make applying slurry more e cient. Slurry treated with MicroZyme requires less agitation and will require less fuel to pump out. It will also make the slurry more homogenous which will improve application accuracy, especially with trailing shoe or dribble bar applicators,” adds Mr Baker.
Degradative enzymes in MicroZyme begin to act on the slurry immediately to decrease solids and reduce crust formation. This will also reduce the buildup of sediment that can lead to some storage, such as lagoons, reducing in capacity and becoming unsustainable. FG
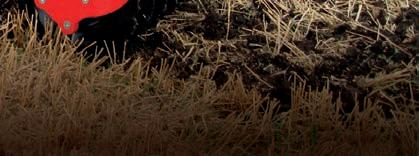

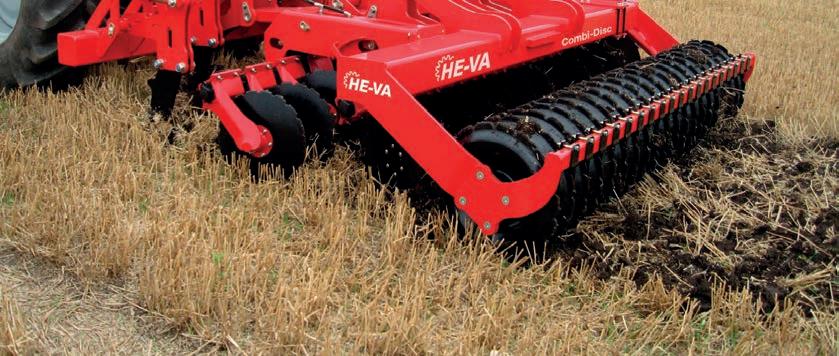
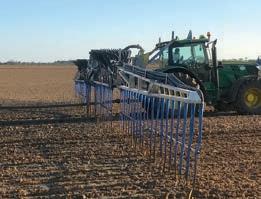
SCAN ME
he-va.co.uk
Scan from your mobile and sign up for a demo
Distributed by
COMBI-DISC
SUBSOIL, CULTIVATE & CONSOLIDATE ALL IN ONE PASS
With working widths of 2.75m-5.25m, the Combi-Disc brings together subsoiling and disc elements in one frame and HE-VA’s clever design allows all the components to be adjusted hydraulically on the move.
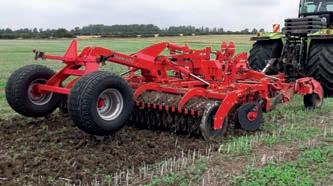
4.5m trailed Combi-Disc
• Subsoiling legs - restructure soils to 16” (40cm) deep. • 510mm discs - cut and mix to 5” (125mm) deep. • Long leg stagger - reduced soil squeeze means lower HP requirement. • Shearbolt or hydraulic auto reset
leg protection.
• 600mm or 700mm single or 600mm twin
V-profilepressroller.
• Mounted and trailed models. • Optional Stealth, low disturbance legs