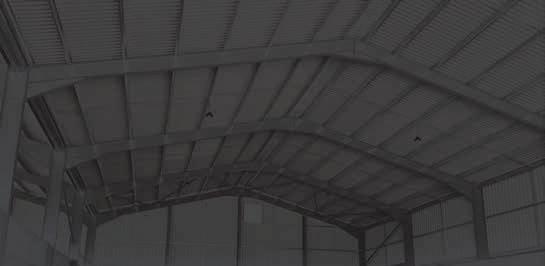
2 minute read
Grain Handling, Drying & Storage
Soil stabilisation – a cost-e ective solution for steel framed buildings
Not giving due consideration to site ground conditions can be “extremely problematic” when undertaking any building project. Johnstruct Ltd managing director Mark Allen o ers some guidance on soil stabilisation solutions.
“Considering the ground/soil conditions and ensuring that the foundations are correctly designed for your steel frame building will make a big di erence to the stability, longevity, and use of the site. Due consideration equally applies to the drainage and underground support conditions for concrete oors and aprons in and around the building,” Mark explained.
Steel frame building company Johnstruct Ltd, has many years’ has recently been successfully using modern sub-base/soil stabilising solutions to address poor ground bearing soil issues.
“Far too often, the ground/site preparation and the associated costs are overlooked or seen as a nonperformance bene t to the overall structure/project. A good percentage of the time, particularly on clay, a mechanical sub-base consisting of the topsoil removal, with an applied geotextile and a 200mm+ mechanical hardcore sub-base, is used to support concrete oors/slabs and
Equally, designed mass concrete pad foundations in clays/chalk are more than su cient. But things get more complicated when poor ground load bearing properties are present, e.g., with gravel, sand and/or a high water table/high shrinkage rates.”
Mark continued: “As with all projects, there’s a balance between initial cost, the likely longer-term use of the building, and risk. Being held to ransom at certain times of the year when using imported materials, e.g. crushed concrete/hardcore, limestone, and chalk, can often result in a cost con ict before your building gets out of the ground.
“Further, the environmental impact, time and cost of importing ‘foreign’ materials/hardcore into any site to form a working sub-base is often subject to quality, performance and material reliability issues. These issues are more apparent in the wetter months when demand is high.”
Modern soil stabilisation methods are often a cost-e ective alternative that should not be discounted by landowners, Mark said. “The main bene t is that it negates the need to remove/relocate as much material/ spoil from a site and importantly, it reduces the need to import large volumes of expensive new material back into the site in the form of hardcore etc.” Large land areas can be addressed extremely cost e ectively and quickly when compared to using traditional imported hardcore, chalk, or limestone, he added.
In its most basic form, soil stabilisation requires the localised removal and reinstatement of the original sub-base/ground material. “The ground material is combined and mixed with a ‘cement’-like additive that changes the soil moisture and structural properties. This results in the reinstated material curing to form an excellent mechanical/structural bearing layer.”
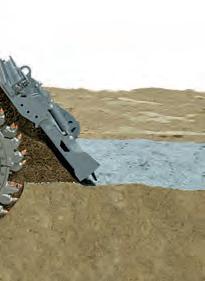

This bearing layer is approximately 300mm thick for a typical steel frame building site area. Sites that have been stabilised normally have a ‘top’ or ‘wearing’ coarse directly applied e.g., concrete oor/apron or tarmac/ road plannings.
Johnstruct Ltd. covers Bedfordshire, Cambridgeshire, Essex, Hertfordshire, and Su olk. It o ers free initial advice on the planning of, and supply and installation of all aspects of steel frame buildings. FG
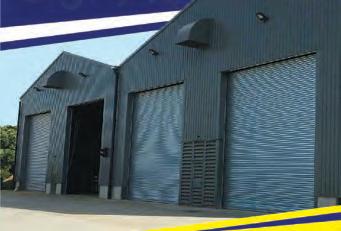
Pre-Stressed Concrete Wall
