
3 minute read
Grain Handling, Drying & Storage

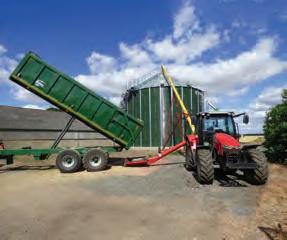
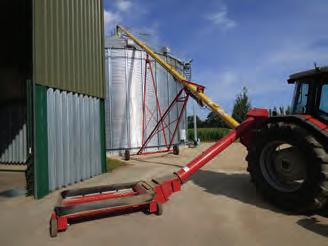


a reputation for manufacturing robust products that would stand the rigors of time served working away in a grain store. Steven sadly passed away in 2014, which was a blow to the business, but the determination of other family members and the dedicated team of brilliant engineers have kept his legacy of producing quality products going.
As well as manufacturing new fans, the team often assist farms with existing Typhoon fans installed over the last 55 years by rebalancing impellers, reconditioning fan cases and repairing and replacing motors.
The primary market for the products is mainland UK, championed by a network of loyal dealers and installers, but buyers from Australia and New Zealand and a few countries in between have discovered Pellcroft and taken shipments of grain tunnels, fans and stirrers, including two new stores in Tasmania which are nearing completion ready for their rst harvest in the next couple of months. FG
Silo stirring and homogenisation helps standardise malting barley product
Norfolk farming business Stratton Streles Estates, based at Colby Hall Farm near Aylsham installed two Sukup stirring drying silos for harvest 2022 which were supplied through Sukup specialist dealer, Allfarm Installations of Wickham Market, Su olk.
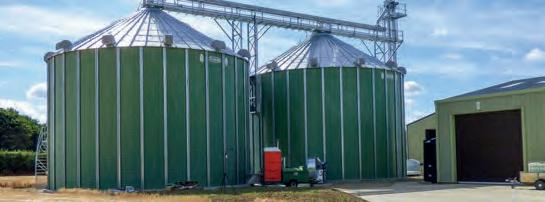
The project consists of two Sukup 4808 drying silos with a total capacity of approximately 2,000t.
The silos are tted with fully perforated drying oors, drying fans and the renowned Sukup silo stirring system which not only increases air ow for drying, it also completely mixes and homogenises all the grain stored within the silos.
Stratton Streles Estates managing director Je van Poortvliet comments: “The Sukup silos are an ideal system for drying and storage of winter and spring barley grown for the malting barley market. With our variable land types and climate conditions they provide the perfect solution to standardise the end product.”

The silos are lled via a tip-and-go intake bunker and 150t/hr Skandia I-Line handling equipment. The silos are then emptied through 100t/h vertical unload systems that discharge grain directly into lorry trailers, so there is no need for a telehandler.
The silos require a much smaller footprint area than an equivalent capacity building and Mr van Poortvliet adds: “With yard space at a premium, they provided the ideal t to centralise the storage where the weighbridge and solar panels are. The construction team are also worth a special mention for their speed and e ciency in the construction of the silos.” FG
Successful grain storage maximises ROI
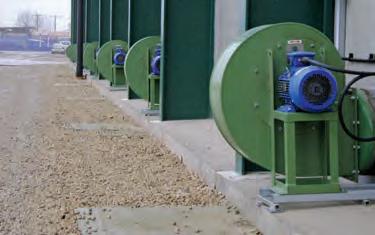
With commodity and energy prices both high, it has never been more important to get the right balance between fan operating times and e ective cooling rates, says Evans & Pearce managing director, Rob White.
Don’t leave fans on continuously all autumn and winter, and don’t wait only for the cool, dry days. The key is the temperature di erential between crop and ambient air; every time the ambient air is 4–6°C cooler than the crop, operate the fans.
Humidity is largely irrelevant in a low volume system; by low volume we mean air ows of up to 6 cubic feet per minute (cfm) per stored tonne. This volume of air is not usually enough to introduce moisture back into the crop.
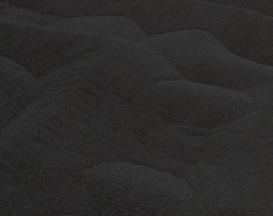
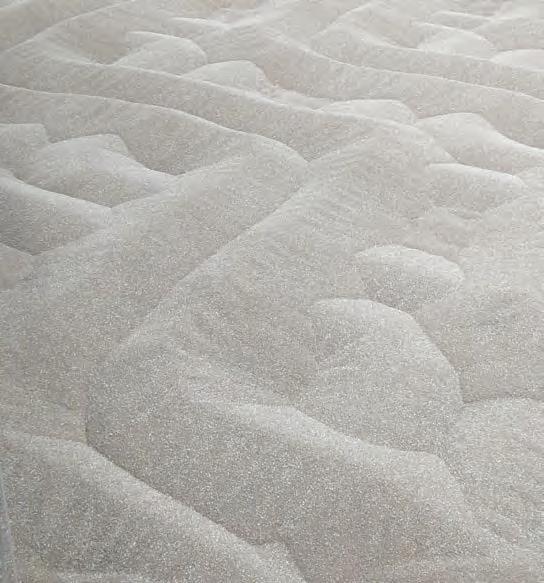
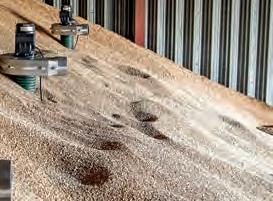
Do not be tempted to change the direction of air ow through the crop – sucking the heat to the pedestal is generally the preferred option. A good quality pedestal fan will do either, so choose a direction and stick to it.
If you do not have a fan for every pedestal, fan rotation is important to ensure all parts of the heap are ventilated. This should be done every 3–4 days. If you use top caps on the pedestals that do not have a fan they should be checked. If condensation is present on the underside of the cap it means that a fan is needed on that pedestal to draw out the warm air that is rising from inside the bulk.
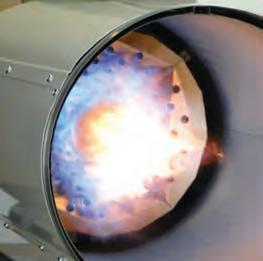
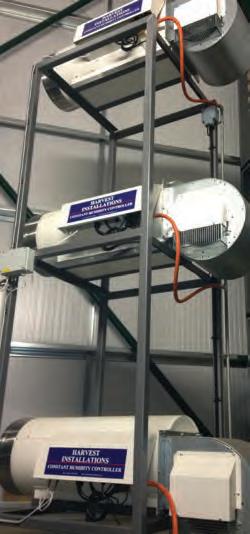
Regularly make sure leaking roof sheets are not allowing a back corner to start spoiling. Is your crop cooling evenly? If not, a screw-in Coolspear might be needed to sort out a problem area. Even with an automated control system crops must be checked – a sometimes tedious but necessary job. Seek advice if you are unsure; crops production costs are too high to let them spoil in the store. FG

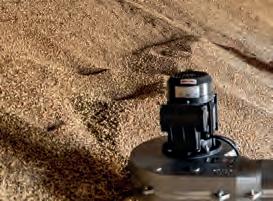

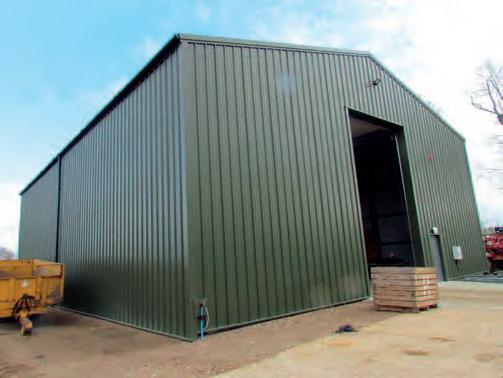
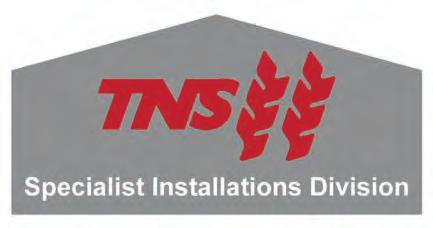

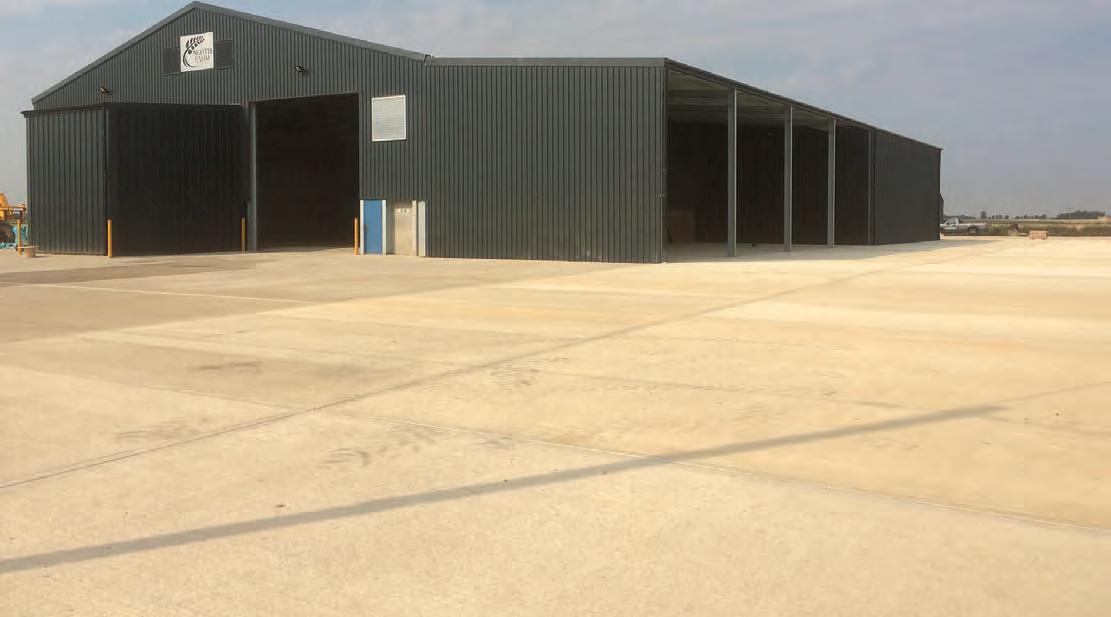
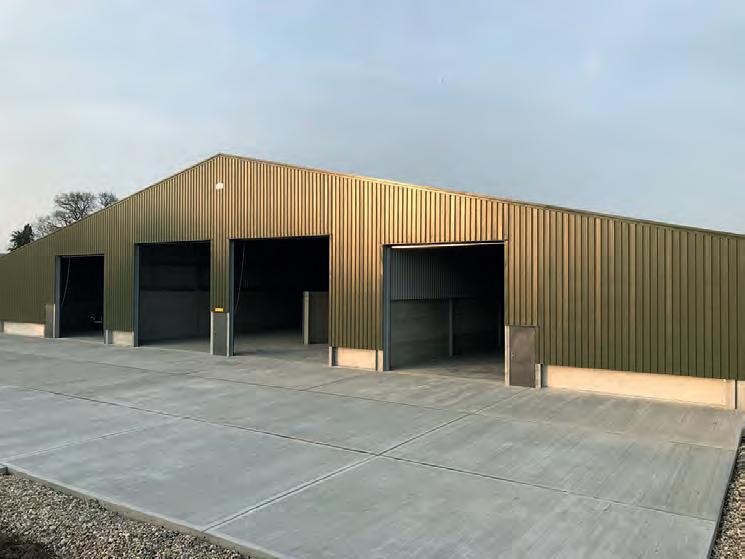
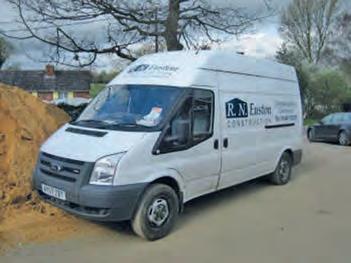
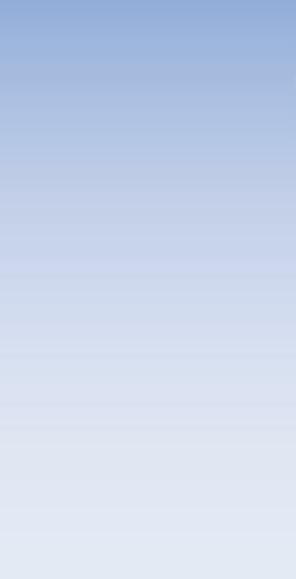
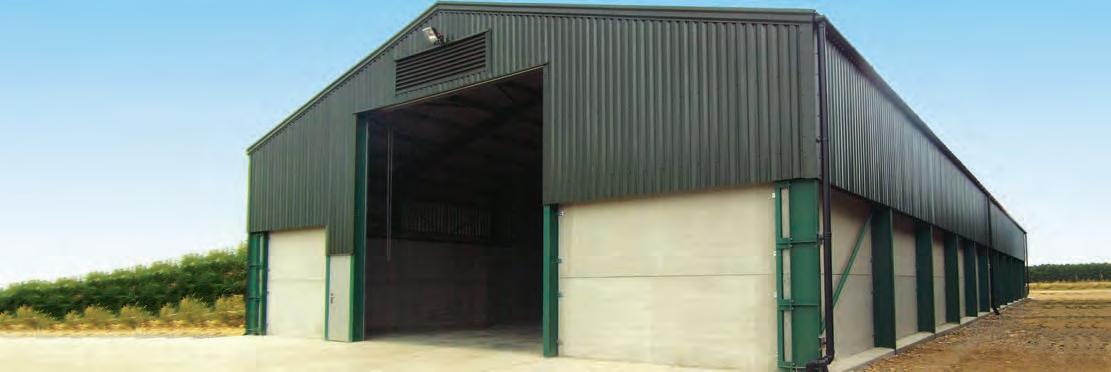
