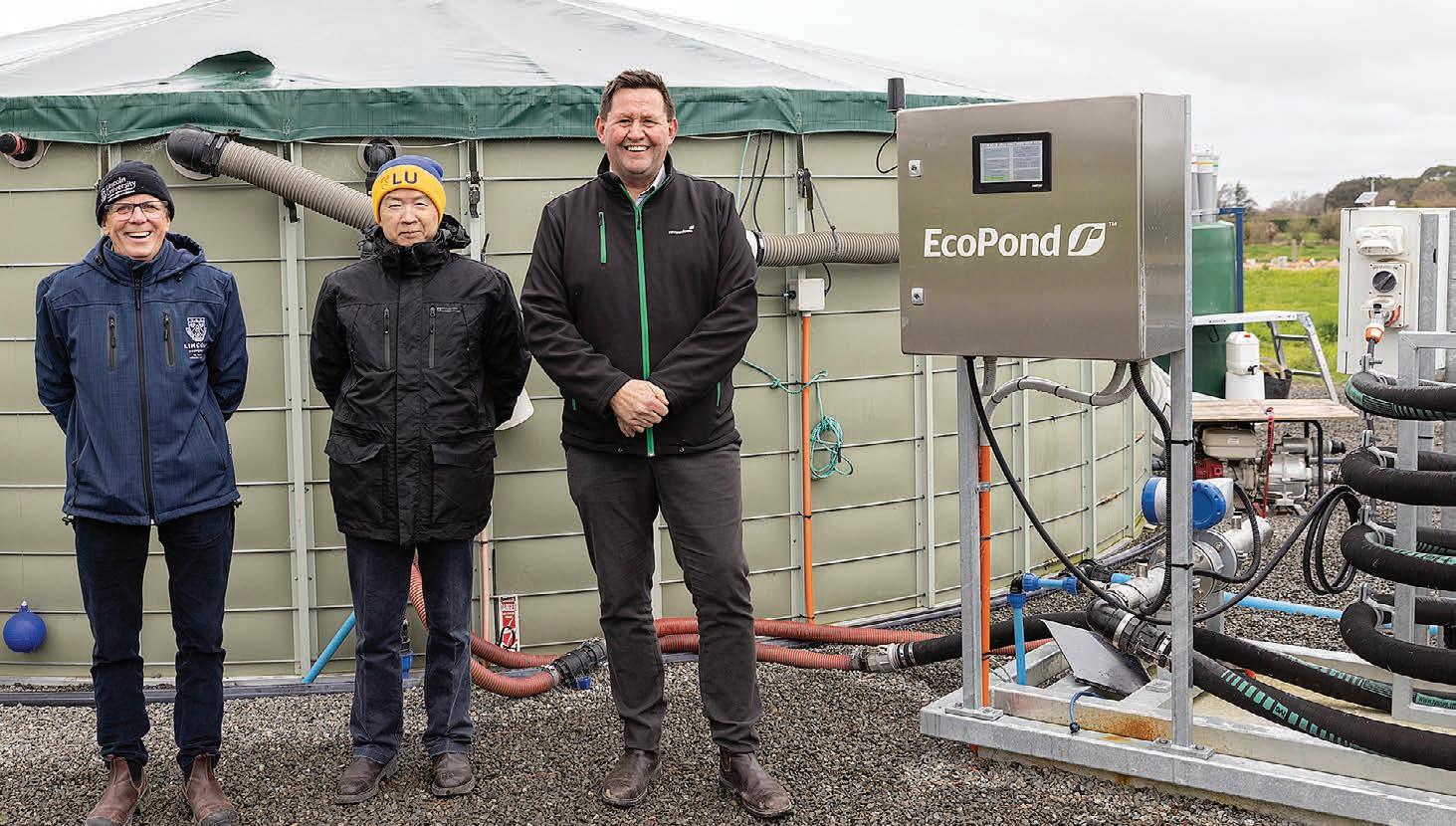
20 minute read
Managing effluent and environmental factors this summer
from Dairy Farmer October 2022
by AgriHQ
Phosphate breakthrough
By Tony Benny
A collaboration to reduce emissions on farms has resulted in technology that will be a game-changer for farmers.
Lincoln University scientists have found a way to reduce the amount of phosphate leached from dairy farm effluent to negligible levels as well as reducing methane emissions by up to 99% and virtually eliminating E coli bacteria.
The breakthrough, which should go a long way to improving water quality in streams and lakes in New Zealand by arresting eutrophication caused by phosphate from farms, involves adding small quantities of iron sulphate to untreated effluent.
“We were absolutely amazed about how effective treating effluent with iron sulphate could be, these were stunning results,” says Professor Keith Cameron, head of soil and environmental research at Lincoln.
The discovery was made when
Cameron and fellow Professor Hong Di were conducting research to ensure there were no unintended consequences from the ClearTech technology they developed earlier in collaboration with Ravensdown to recycle water from farm dairy effluent to wash the yard.
They compared how much phosphate from treated effluent found its way down through the soil profile when spread on pasture to the amount from untreated effluent.
Results from deep lysimeters on Lincoln’s dairy farm have recently been confirmed from simulated tile-drain systems, conducted by PhD student Xueying Che, supervised by the two Lincoln professors. They set up simulated tile-drain experimental plots and found that whereas 3.5kg/ha of phosphate was lost from untreated effluent applied to pasture soil, only 0.24kg/ha was lost from the treated effluent, the same as that from the control where no effluent was applied.
The scientists set up experimental plots and found that whereas 3.5kg/ha of phosphate was lost from untreated effluent, only 0.24kg/ha was lost from the treated effluent.
While 3.5kg/ha of phosphate is insignificant to a farmer, it’s enough to cause major problems in waterways, especially as it can be delivered quickly from pasture to stream via the drainage pipes beneath many paddocks on New Zealand farms – particularly those on heavy clay soils.
“The drainage networks are extensive and some of them have been there for 100 years or more,” says Cameron.
“Normally those drains have a Novaflo pipe, or previously tile drains, and because it’s got a gravel backfill to allow easy drainage, they actually act as a short
Professors studying the new effluent system at Lincoln University dairy farm have made a breakthrough discovery in the war against emissions and phosphate leaching. Professor Keith Cameron, Professor Hong Di and Ravensdown product manager Carl Ahlfeld.
circuit through the soil. The effluent goes on the top and the drain allows the effluent to dribble through, which then contaminates waterways.”
“That 3.5kg is actually quite a high amount,” adds Di.
That phosphorus economically is not worth a lot of money but once it gets into the surface water, a minute amount causes surface water eutrophication.
“We usually say, ‘Economically insignificant but ecologically very significant’.”
“What the iron sulphate does is to help reduce the solubility of the phosphate so that it sticks to the soil and then a plant can use it rather than it leaching out the bottom of a drain. It’s still there but it’s stuck to the soil now for plants to use later,” Cameron says.
Not only does the system stop phosphate, which is contained mostly in cow dung, from leaching from soil, it also is remarkably effective in eliminating both E coli and methane emissions from effluent.
“It reduces the ability of microorganisms called methanogens to produce methane. The sulphate stimulates another group of bacteria, called sulphate-reducing bacteria, and essentially they eat all the carbon for their growth and starve the methanogens of any carbon and then they don’t produce methane.”
The iron in the additive interacts with the “shell” of the E coli bacteria and effectively destroys it, aided by acidic nature of iron sulphate, reducing E coli by 99.9%. Di says this is good news for small towns where councils are concerned that E coli from farm could enter water supplies.
A prototype EcoPond, as the new technology has been branded, has been in action on Lincoln University’s research dairy farm and another has been put on a farm near Te Waihora/Lake Ellesmere, close to the university, to test it under normal farming conditions. EcoPond systems are being installed on other commercial farms as part of the early adoption development work to design and install units that can be easily retrofitted into most effluent systems.
“We’re working on Version 2 plans now, which is a fabricated stainless steel unit, and we’re getting ready for commercialisation midway or late next year,” says Ravensdown product manager Cal Ahlfeld.
“It will be plug and play. Ravensdown are a fertiliser company so we’ll have suppliers and they all have units on the shelf so they can pretty much go out and connect them up and it will be very simple.”
Ahlfeld expects the units to sell for about $45,000, including installation, and annual operating costs for a 400-cow herd milking for 270-280 days will be between $10,000 and $12,000 at current international prices for iron sulphate. Prices are very volatile at present and could easily come down.
“We bring in liquid at the moment but that’s not cost effective so we’re looking at bringing powder in and mixing it ourselves. It’s readily available because it’s used by councils for water purification.”
Ahlfeld says Ravensdown are proactive in working on smarter farming especially environmental impacts and sustainability.
“This technology that we have managed to develop with Lincoln is probably seen as the pinnacle for Ravensdown now. It’s fantastic. It’s come about because 50% of New Zealand dairy farmers use Ravensdown products and are co-operative members so it’s about creating technology for the future success of our customers.” n

The EcoPond equipment takes in untreated effluent from the dairy shed and adds precisely measured amounts of iron sulphate and sends the effluent on to the pond. It will eventually be spread on pasture when the conditions are right.
Solving the poo problem
By Samantha Tennent
Effluent is an issue on all dairy farms but one company has developed a natural product to help farmers deal with the challenges of cow poo.
Knowing his brother was having to spend heaps of money and effort every few years cleaning out the effluent pond on the family farm, Murray McCallum was keen to find a better solution.
“Effluent needs to be addressed almost every day on farms, but it creates so many challenges, particularly the smell and solids in ponds,” McCallum says.
He is now the national sales manager for MicroBio Solutions, who have developed a natural bacterial effluent solution, Effluex.
“We found Effluex helps with all of those effluent challenges.
“It uses a combination of anaerobic and aerobic bacteria that work on the effluent when it’s in the pond, eliminating the smell first then breaking down the crust and continually cleaning the pond.
“And what’s left is a brown, nutrientrich water without the slurry, meaning farmers are pushing out water instead of solids which is easier on gear and reduces the environmental risks on the paddocks.”
They tried the product on the family farm in Maungaturoto, Northland, and were really impressed with the results.
“Our current effluent consent, which allows us to discharge to water, is going to run out soon, so we set out to find the best solution for our farm,” McCallum says.
“The consent is monitored very carefully by the regional council but farms like ours will need to upgrade systems to be able to hold sufficient storage and be able to irrigate and get it back onto the land safely.”
In the three-pond system they currently operate, the first pond captures the solids and sludge from the cow shed, and the water runs off the top into the second pond then onto the third and onto the environment. Most farms will have a two-pond system and irrigation to disperse the effluent.
McCallum and his brother Grant, along with their parents Ron and Pam, converted the farm 29 years ago before there was so much scrutiny on how farmers farmed.
“When I was on the farm 30-odd years ago, it wasn’t anyone’s business how we got the milk into the vat, but nowadays the consumer is driving so much.
“Customers have a lot of choice and data available and it’s really important we’re using the most efficient solutions

Before being treated with Effluex, the effluent pond on the McCallum farm had a crust on the surface and had to be continually cleaned. After being treated with Effluex, the effluent pond on the McCallum farm is now full of nutrient-rich water.
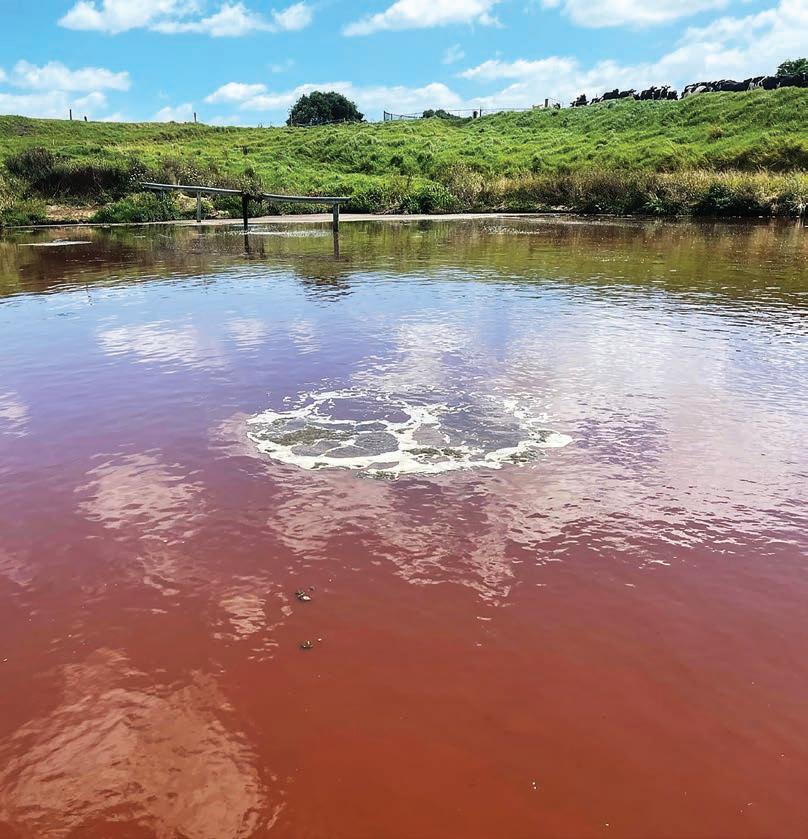
to help solve the challenges we face on farm.
“Effluex is a tool to help solve the effluent dilemma.”
With all the new regulations to store and manage effluent and such a variety of products on the market, it can be challenging to know which system will work the best. And dealing with slurry can be challenging and create problems in both lined and compacted clay ponds.
The McCallum family have been impressed with the results from Effluex, as it eliminates many of those challenges in a simple manner.
MicroBio Solutions has recently formed an exclusive partnership with Farm Source, after they became interested in the effectiveness of the product and conducted their own trials.
“Farm Source wanted to test the bacteria’s safety as part of their process so farmers could use it confidently, and like us they were impressed with the results,” McCallum says.
When farmers sign up to Effluex they receive the product monthly on a subscription basis and it starts with a four-month minimum period.
“We find having the package turn up monthly reminds people to apply it to the pond, rather than buying a big drum of something, using it once then forgetting about it,” McCallum says.
“This way, it’s a good reminder and it’s a simple five-minute job once a month that de-risks the whole operation, and four months gives them enough time to start seeing some results before deciding if they want to continue using it.
“People are keen to give it a go because if it does what we say it does, it saves farmers a lot of money by working with existing effluent systems and solves a lot of problems they have been experiencing.
“And we don’t have many farms drop off because the product really does the talking, it’s really proving to be an easy solution to help manage effluent.”
The team has spent a lot of time determining the correct application rate, which is all based on cow numbers. So all a farmer has to do is select a pack relative to their herd size.
“It took a lot of trial and testing but we wanted to make it really simple for farmers,” McCallum says.
“We didn’t want them to try to measure ponds and work out how many cubic litres they have, we just wanted an easy method and basing it on cow numbers takes the hassle out.” n
Murray McCallum

Microbio national sales manager Murray McCallum – with his son Cameron on the family farm – helped his family find a solution to the continual cleaning of their effluent pond.
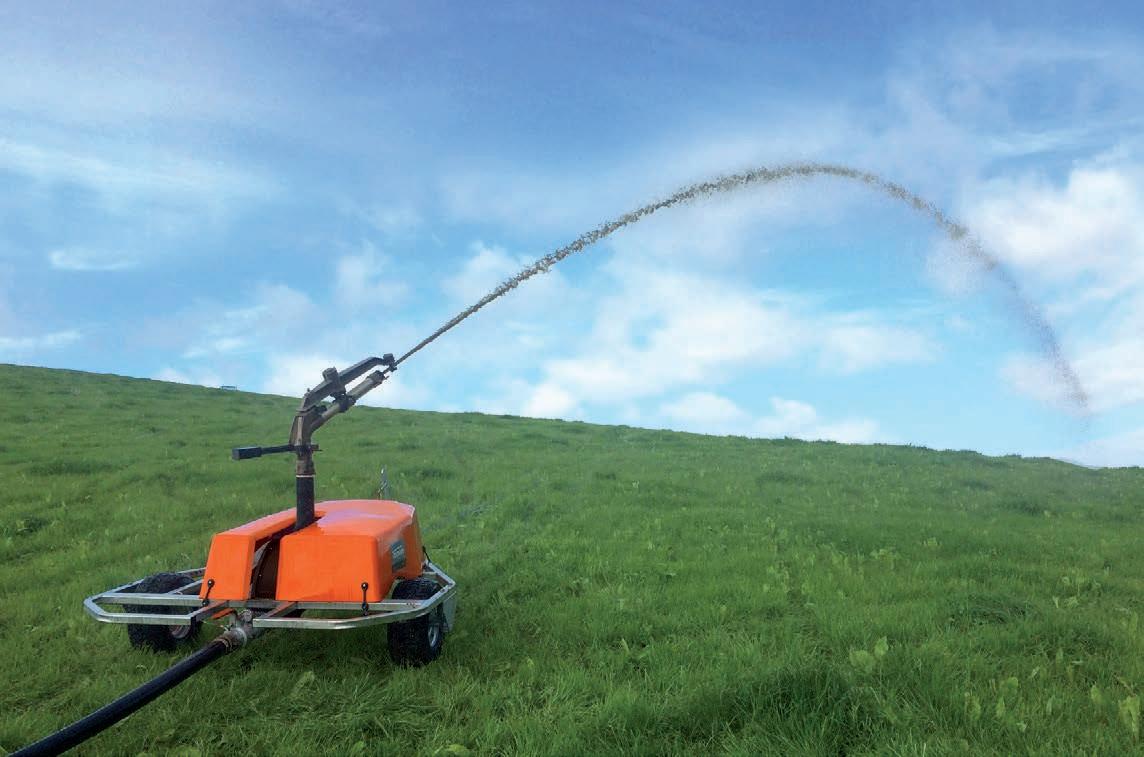
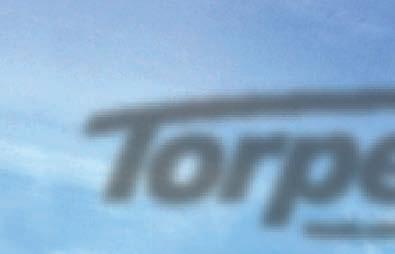

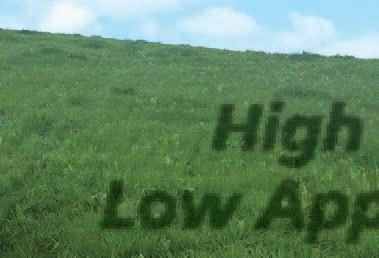
Logan Bowler of Agblution Solutions says there are many areas in and around the shed that water can be saved. Having efficient hosing procedures, hand scraping, water reducing nozzles and green water yard washing, all produce less effluent.
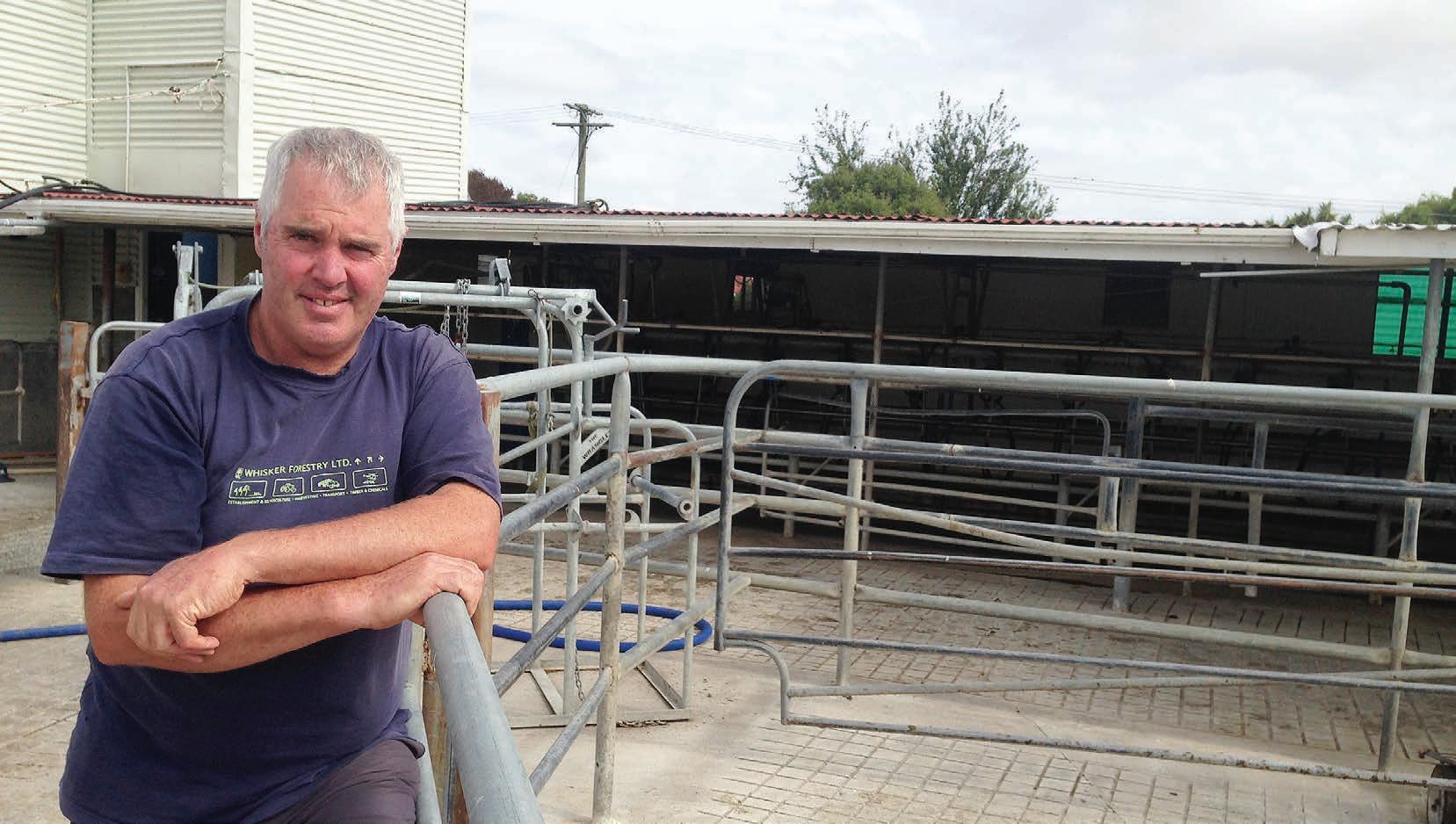
Reducing water use in the dairy shed
By Logan Bowler
I’ve written a few articles in the past regarding measures to reduce effluent storage volumes. Other than finding low-risk soils, reducing water use in and around the dairy shed and having low FDE irrigation application depths are the best mitigations to take to reduce storage requirements.
The two main problems with lowdepth irrigation are that as depths decrease the irrigator must travel faster, therefore completing runs quicker. If we halve application depths, we need to do double the number of runs to apply the same volume of effluent. This all adds up to an increased workload.
The advantage of low water use is that every litre not used in the shed is a litre not needing to be stored in an effluent pond or irrigated to land. Reduced FDE irrigation equals reduced labour and reduced costs.
There are many areas in and around the shed where water can be saved.
Having efficient hosing procedures, hand scraping, water reducing nozzles (hydrofan nozzle), and of course green water yard washing, all produce less effluent.
Rotary sheds in particular can have multiple stationary jets/sprays (D-gate, cows-off jet, skirt washers, wall washer etcetera) squirting water onto the platform to keep equipment clean, and to chase the cows off the platform. The total daily water use through all these jets/sprays in the shed can be huge.
Below is an example showing real data collected from two sheds on adjoining properties under the same ownership. Both sheds’ platforms operate for approximately six hours per day
Among other stationary jets/sprays, each shed had a D-gate spray and a cows-off jet. The D-gate spray at shed 1 (see figure 1) was flowing at 19.2l per minute (6900 litres per day) and, over a 300-day season, using more than 2 million litres of water. If they irrigated via a travelling irrigator with a standard pump rate of five litres per second, they needed to run the irrigator for 115 hours per season just to irrigate the D-gate’s water.
The D-gate spray at shed 2 (see figure 2) was flowing at 4.25 litres per minute giving an annual water use of 459,000 litres, which translates to 25.5 hours of irrigation per year – a 78% reduction in water use and irrigation time. Both D-gates were achieving the same result – keeping the cups damp, preventing a build-up of muck on them.
Likewise, each shed had a cows-off jet. Shed 1’s cows-off jet (see figure 3) was flowing at 18.42 litres per minute (6630 litres per day or 1.99 million litres per year). Shed 2’s cows-off jet (see figure 4) was flowing at 7.8 litres per minute (2808 litres per day or 840,000 litres per year). Both sheds’ cows-off jets worked effectively, but one used nearly 250% more water than the other.
It just so happened that sheds had one efficient jet/spray, and one inefficient jet/ spray each. If one of the sheds had the high water use D-gate and high water use cows-off jet it would have created a huge volume of effluent.
As discussed above, to irrigate the 2.073 million litres per year solely from the D-gate in figure 1 will take over 115 hours for a normal travelling irrigator to spread it to land. If a run 300m long takes five hours, that’s 23 irrigator shifts each year just to deal with the water generated from the D gate sprayer, and another 22 irrigator shifts each year for the water used in the cows-off jet.
Measuring your platform’s water use is easy. Grab a bucket and use the stopwatch on your phone. Measure the volume collected in the bucket and divide this by how many seconds the bucket was under the flow to calculate the flow in litres per second. Now multiply this out for how long the jet/spray is used each day. Complete this for all the jets/sprays and add them all together to get an informed understanding of the volume of water used, and consequently, the volume of FDE created from these nozzles/sprays.
Often when new, the spray nozzles produce a fine mist, but over time the nozzles rust or wear out and what was once a mist is now a torrent. Can you achieve the same result with a fine mist? Can you get away with using the wall and skirt sprays for one round at the start of milking to make the surface damp, and then for one round at the end of milking to help wash the muck off? Will a jet of compressed air instead of a jet of water make the cows back off the platform?
If we think of the end destination of the water, and the cost of labour, pumping, irrigating etcetera of every litre we use in the shed, regardless of whether it’s a rotary or a herringbone, then maybe we will implement much more efficient water use. n
Who am I?
Logan Bowler is the owner of Agblution Solutions, offering common sense, independent advice on effluent systems
Figure 1: D gate, 19.2 litres per minute (1152 litres per hour and over 2 million litres per year)
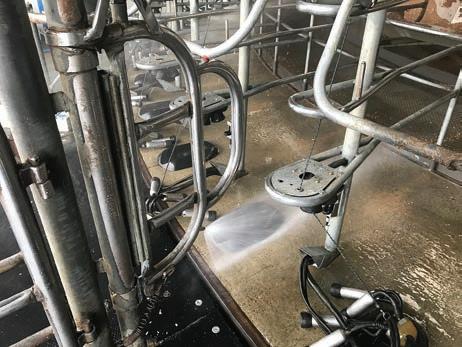
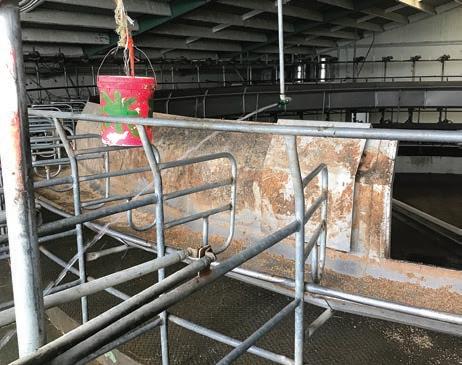
Figure 3: Cows off jet, 18.42 litres per minute (1105 litres per hour, 6630 litres per six-hour day, approx. 1.99 million litres per year) Figure 2: D gate, 4.25 litres per minute (255 litres per hour and 0.459 million litres per year)
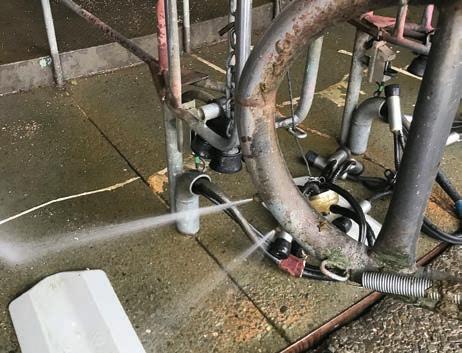

Figure 4: Cows off jet, 7.8 litres per minute (468 litres per hour, 2808 litres per six-hour day, approx. 0.842 million litres per year)
Resistant farmers
By Gerald Piddock
A stubborn minority of Waikato dairy farmers are refusing to make efforts to change their farming practices to become fully compliant around effluent management.
Of the 789 farms inspected by the Waikato Regional Council for the 202122 season, 54, or 7%, were significantly non-compliant.
That percentage is unchanged from the previous season, Waikato Regional Council regional compliance manager Patrick Lynch said.
Many of these farms would have had previous visits from council inspectors, he said.
However, full compliance rates had lifted from 37% to 49%, with 379 farms being fully compliant.
“We’re finding the bad stuff at the same rate. However, at the other end of the spectrum, there are more people improving,” Lynch said.
Those fully compliant farmers know the rules and are following them. But at the bottom end, a minority of farmers are resistant to change, he said.
“It feels like for us, that when we find the bad stuff, these are people who simply don’t want to change.
“They have had all of the warnings and guidance from their own industry – supply companies, DairyNZ, the wider community and us as the regulator and yet there is this realm of around that 7% and we’re having to engage with them one at a time and use our harsher regulatory tools to get them to change.”
Though 7% may seem like a small component of the industry, the scale of the dairy industry in the Waikato means there are as many as 300 dairy farms with inadequate infrastructure, posing a threat to the environment, he said.
“The good farmers are doing the right thing and there are more people trending towards doing the right thing, but the real issue is what appears to be this core of poor performers who are absolutely resistant to change.” n
Is your existing effluent storage okay?
By Nick Calow
At the heart of any welldesigned effluent management system is the effluent pond/storage, and with tightening council rules and regulations we’re frequently getting asked to assess whether existing storage is “okay” to use. As accredited farm dairy effluent designers, we’re always happy to help and advise on your situation, but if you’re wanting to do it yourself here’s some advice.
Council Compliance
For a start you’ll want to look at the basic requirements of being council compliant: • Is your pond more than 45m from the cow shed? This is a must. • Is your pond/storage large enough to hold all your effluent during times when irrigating is not possible?
Online storage calculators can help provide a general guide for effluent storage requirements; however, we recommend having more than the minimum. • Does it leak? Having a leaking effluent pond is a no-no. Not all leaks are going to be obvious, so check around your pond for any mushy areas. If in doubt, best to get it lined – this isn’t just for council compliance, but keep in mind if your pond is at ground-water level, not only will the effluent leak into the water, but groundwater will leak into your pond, filling it up and reducing capacity. So it’s in your best interests to ensure there are no leaks.
Efficiency
Not only do council rules and regulations change, but so do farms. Your cow numbers may have increased, you may have acquired the farm next door, built a new cow shed, no longer have discharge consent ... there are a lot of ways a farm can evolve over time, and this can all have an impact on the viability of your existing effluent storage.
Efficiency plays a big part in the suitability of your existing effluent storage because an inefficient system will cost you over the long term – time, labour, added expenses. Here are some of the things to consider in terms of efficiency: • Is your effluent pond/storage in a suitable location? Ideally it should be central to the farm and in a place that doesn’t cost too much to run power to for pumping/stirring. • Does the effluent flow into the pond via gravity? While this isn’t always possible, it is the best set-up to have. This way you are not reliant on power and don’t have the extra expense of having to use it. • Are you having to get a contractor in to empty the pond? Some farms that have discharge consent can get away with getting a contractor in once a year to empty the pond, However, without discharge consent you may find the need to have a contractor in three or four times a year. In this case it can be more cost effective to increase your storage capacity.
Making Adjustments
If you’re thinking your effluent storage is going to need some adjustments, or a bit of an overhaul, there are lots of costeffective options: • Effluent ponds can be dug out for more capacity – councils do deem this as a new installation, so the pond will require lining after a re-size. • Secondary/emergency storage can be installed for when it is needed – for example a bladder tank or second pond. • Old ponds or sumps can be repurposed if a new pond is needed in a different location. • If an old oxidation pond has been well designed this can often be re-purposed for use as an effluent storage pond.
Every situation is different, so seek advice on the best outcome for your effluent management system. n
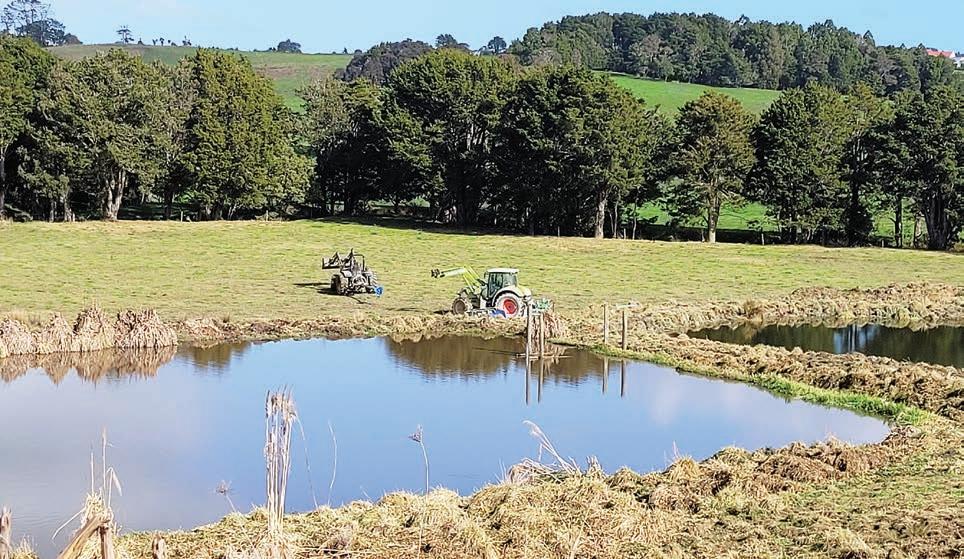
Effluent storage ponds must be large enough to hold effluent during times when irrigating is not possible.