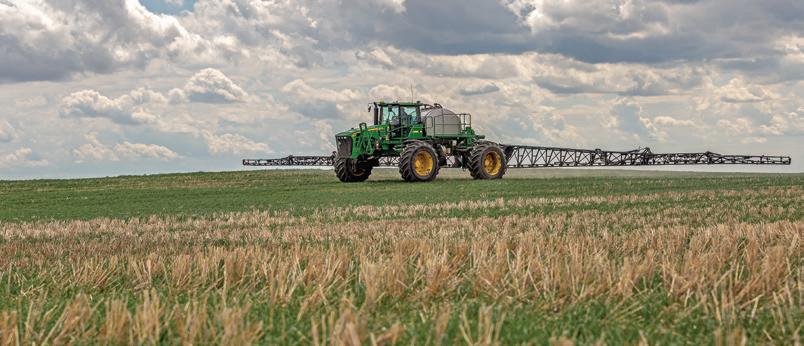
6 minute read
Why Can’t We Solve the Boom Problem?
If I were to rank all the technologies on a sprayer in order of importance, the nozzle would be in first place. It determines the coverage and drift; it ensures that the spray mix is uniformly distributed under the boom. The success or failure of a spray operation often comes down to nozzle choice and how it was operated. Nozzle technology is fairly mature —we know the spray quality we need for success, and all major nozzle manufacturers create products that can deliver what we need.
But the nozzle can’t do it alone, and that’s why on my list, the spray boom is in second place. It is responsible for a host of tasks such as delivering the spray mix at a uniform pressure along its entire length, folding quickly and compactly, as well as preventing the buildup of pesticide residues and, if necessary, allowing for easy decontamination. But its most important task is to be the steady hand of the spray operation, ensuring nozzles maintain a uniform speed along the ground and a uniform height from the target. Not doing those tasks properly can undo much of the nozzle’s good work.
Advertisement
We commonly refer to fore- and aft-movement of the boom as yaw, and up and down movement as sway. And bringing these two parameters within an acceptable range has been a project generations in the making.
Why is boom stability important?
Nozzles create a tapered fan spray for which a certain amount of overlap with adjacent nozzles is necessary. They also create a wide variety of droplet sizes, ranging from about five µm to over 2000 µm. The speed of the droplets, and the distances they travel in a straight line depends on their size. Small droplets slow down significantly almost immediately on their release from the nozzle. Their movement quickly becomes subject to prevailing winds and turbulence, much like that of dust, chaff or down feathers.
For these reasons, nozzles need to operate within a fairly narrow window of distance from their targets. For a typical boom with 20-inch nozzle spacing, boom heights less than about 15 inches have insufficient overlap that creates gaps in coverage, visible as striping. Boom heights over about 25 inches can lead to excessive spray drift because the smaller droplets will, by then, have slowed down enough to be easily displaced by wind. That’s why we see plumes of small droplets behind spray booms. Once they’ve left the spray cloud, they can stay aloft for a long time, and the spray operator has lost all control over their movement.
A rule of thumb is that spray drift potential doubles every time the boom height is doubled. A low boom can make it possible to spray in significantly higher winds than a high boom. With a lower boom, the droplets are still moving fast when they enter the canopy. Their initial energy prevents them from being displaced by wind.
18V 1/2 in. DX13
Brushless Hammer Drill
Cat® is excited to present the first Canadian portable power tool to feature a Graphene battery: the Cat 18V 1/2 in. DX13 Brushless Hammer Drill.
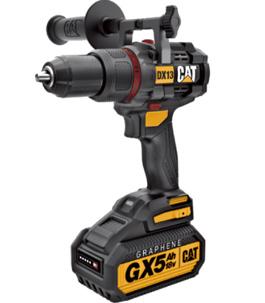
The Graphene battery offers twice the power, charges three times faster, and provides a life cycle up to four times longer than conventional lithium ion batteries.
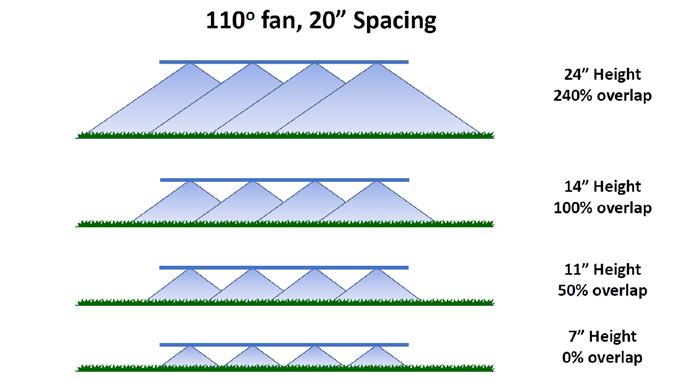
Features like 700in.-lbs of torque, a brushless motor, and a weight of just 4.85 lbs. keeps Cat forefront in the industry and the top choice of professionals.
To keep you working better for longer, the Cat 18V 1/2 in. DX13 Brushless Hammer Drill has a three-year limited warranty and the Cat 18V Graphene Battery features a five-year warranty.
Wind speeds are lower the closer one gets to the ground. The friction of wind with the soil or crop canopy slows it down. A small droplet is less likely to be carried away if it never enters the higher wind of the greater elevations.
But higher boom heights also make the spray less effective in other ways. For example, the ability of an angled spray from a twin nozzle to target a vertical object, or the back of a target, requires the droplets to move in the direction determined by the angle of the nozzle. With too much distance, enough time passes for headwinds or gravity to deflect the path of the droplets. By the time they arrive at the canopy, the original direction is lost and the spray may as well have been created by a vertically oriented nozzle.
The best example for this is fusarium head blight sprays, where angled nozzles are usually recommended. Too high a boom negates their effectiveness.
But that’s not all. High booms can also create problems with deposit uniformity. Wind is not uniform. Its speed rises and falls, creating different amounts of displacement. The higher the boom, the more exposed the spray will be to these fluctuations.
Small water droplets also evaporate quickly. And once the water has evaporated, they are even smaller and more prone to all the displacements we’ve already mentioned. The uptake on the leaf surface may also be lower—dry deposits are not as easily absorbed by a cuticle than a wet deposit.
Boom yaw is another problem area. When booms whip forward and backward, they underdose and overdose, particularly at the boom ends. These problems are less common than sway, but are nonetheless still present.
Where are the stable booms?
Overall, I think it’s safe to say that maintaining the correct boom height is one of the more important jobs on a sprayer. When pull-type sprayers with outrigger wheels were common, setting and keeping that height was easy. It’s more difficult with suspended booms.
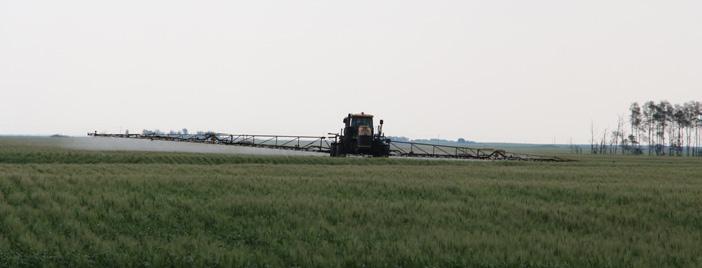
The benefits of low booms are often cited in guidelines to reduce spray drift. But with boom sway of 20 to 30 inches on undulating ground, operators find it difficult to comply with this advice. The risk of the boom making contact with the ground is simply too great. As a result, suspended booms commonly operate at 30 to 35 inches above the target. The cost of this practice, in terms of spray drift or lower deposit uniformity, hasn’t been tabulated. But it may be significant.
It’s time that sprayer manufacturers make boom stability a greater priority. Why do we even have to ask? One of the best developments in the North American sprayer market has been the arrival of European sprayers. These sprayers need to compete in a home market where boom stability is a key performance feature, where significant resources are spent to distinguish a brand from a large number of competing firms. North America has a relatively small domestic manufacturing base—John Deere, Case, RoGator and New Holland making up the majority, with Apache and a few other small manufacturers fighting over the remainder.
In comparison, Europe has about 75 manufacturers, although many are small and regional. Some European countries have had strict performance guidelines about which sprayers can enter their market, and this resulted in engineering efforts to meet those standards. Customers are the winners in this kind of arrangement, with better plumbing systems, and better booms having to be manufactured. Field days are held where 10 to 15 different sprayers march down a standard bumpy track, allowing prospective customers to see the winners and losers first hand.
It’s been refreshing to see the likes of Agrifac, Horsch Leeb and Amazone making their more sophisticated units available in our market in recent years. But even they can do better.
As the role of the sprayer evolves towards more sensing tasks with boom-mounted cameras, and as spot spraying gains momentum, there will be a host of new reasons to have stable booms available. For example, a spot spray of a single nozzle is very sensitive to boom height. At a boom height of 27 inches, a 30-degree fan creates a bandwidth of about 15 inches. When the boom sways down just five inches to 22 inches, the band has narrowed to 12 inches, creating an overdose of 22 per cent. If it sways up five inches to 32 inches, the bandwidth is 17 inches, resulting in a 16 per cent underdose.

These numbers wouldn’t be acceptable in any other industry where inputs are costly and product rates are tightly regulated.
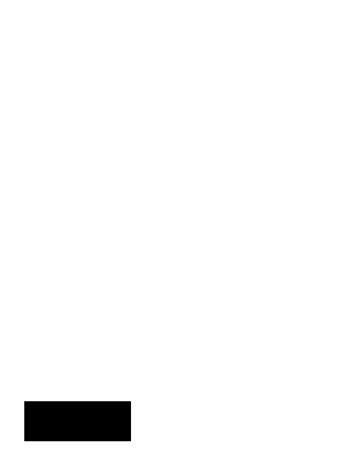
There are signs of change. As John Deere readies itself to introduce its flagship spot sprayer, See & Spray Ultimate, to market, it has developed a boom with a claim that it keeps the tip of the boom “within 10 inches of the target height, 95 per cent of the time.” One might argue with the impressiveness of this claim, but the point is that the company has obviously made a commitment and is prepared to share its specs.
We need to see more of the same design goals so prospective customers can make informed decisions on specifications that matter. Tell us how quickly the boom folds, and why we can trust it to flush clean. Give us a reason to believe a low boom height can be set without fear of striping or boom damage. Allow applicators to take advantage of low, steady boom heights. And may the best boom win.
It’s time to start changing the way we talk about farmers and farming. To recognize that just like anyone else, sometimes we might need a little help dealing with issues like stress, anxiety, and depression. That’s why the Do More Agriculture Foundation is here, ready to provide access to mental health resources like counselling, training and education, tailored specifically to the needs of Canadian farmers and their families.