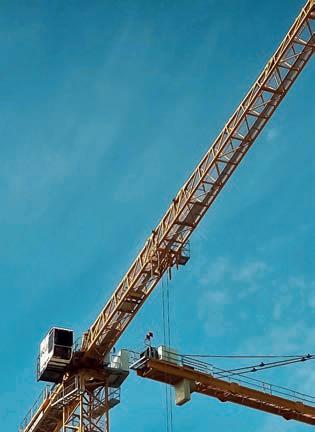
19 minute read
CONSTRUCTION FIXINGS
news and information dedicated to construction fixing products
HEAVY-DUTY ANCHORS FEATURE Competency in anchor applications
Advertisement
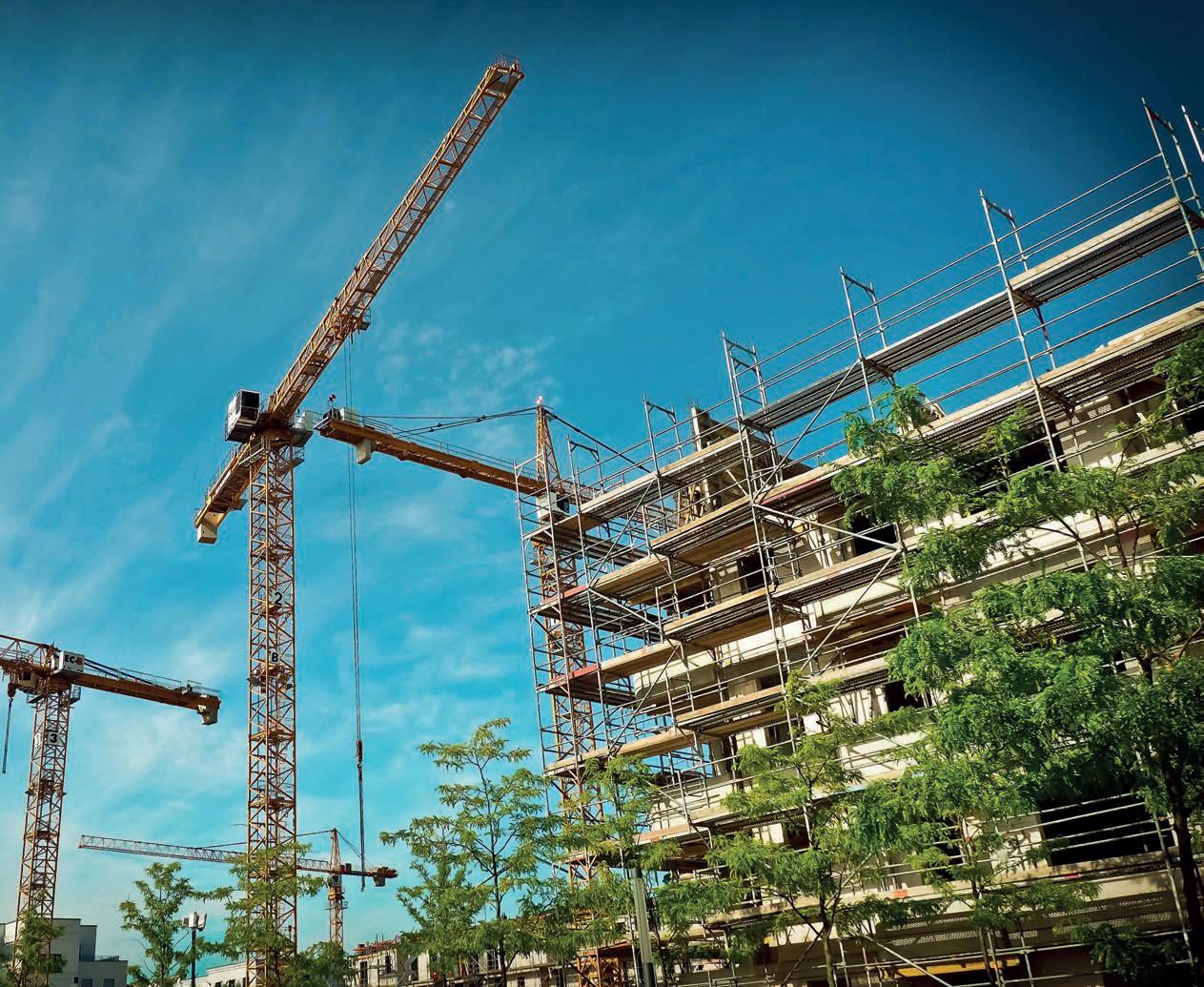
By John Muir, technical manager, Construction Fixings Association
On a construction project, the monetary value of the anchor package is very small in relation to the project value, but should an anchor failure occur, especially with safety critical anchors, large costs could be incurred.
T
hese costs would be in terms of remedial and remediation works and loss of reputation, or worse, human injury or death. This being the case, it is essential that the incidence of anchor failures is reduced or eliminated. The major causes of anchor failures are incorrect selection and design of the anchor, incorrect installation, as well as the incorrect change of anchor specification.
Consequentially, the key functions that impact such failure incidences are specifiers – who design and select the appropriate anchor and provides a full specification; installers – who install the anchor to the correct procedures and manufacturers’ instructions; and contractors/supervisors – who manage and supervise the total application, including changes of specification. Increasing and maintaining the competence of all these roles and functions is an area that needs to be addressed within the anchor industry. In broader terms this has become a focus for the construction industry as a whole.
Construction industry perspective
Safety for the occupants and users of buildings is paramount, with the competence of all those who provide services in the construction or maintenance of a building key to achieving this. A new code of practice, BSI Flex 86701 has been produced to minimise building safety risks and improve protection to building users and occupiers, through supporting the development competency frameworks to achieve a level of competence across the industry.
The code sets out core criteria for competence and aims to facilitate the development of competency frameworks based on specific sectors and across all roles and functions involved. Key to such a framework is the definition of competence. The code defines these elements as Skills, Knowledge, Experience and Behaviours (SKEB).
Each sector, such as a trade or discipline, should develop a framework to meet the specific needs of their sector and the range of roles and functions within that sector, who ultimately impacts safety. In essence, the code relates to all roles involved, such as designers, contractors, managers statutory and end users.
Anchor industry perspective
Prior to the development of BSI Flex 8670, the code of practice BS8539 ‘Code of practice for the selection and installation of post installed anchors in concrete and masonry’2 was developed to define best practice in the area of selection and installation of anchors.
The main purpose of the code was to provide a clear system approach to the whole process, where no formal approach previously existed. The lack of such a clear holistic process has previously led to anchor failure issues.
Within the code, the roles and responsibilities for all functions are defined and competence (for the installer) is also stated as having Skills, Knowledge and Experience, which is aligned to the BS Flex 8670 definition. BS8539 also covers the roles directly involved in the areas of anchor failures.
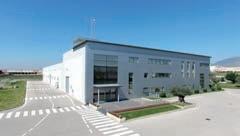


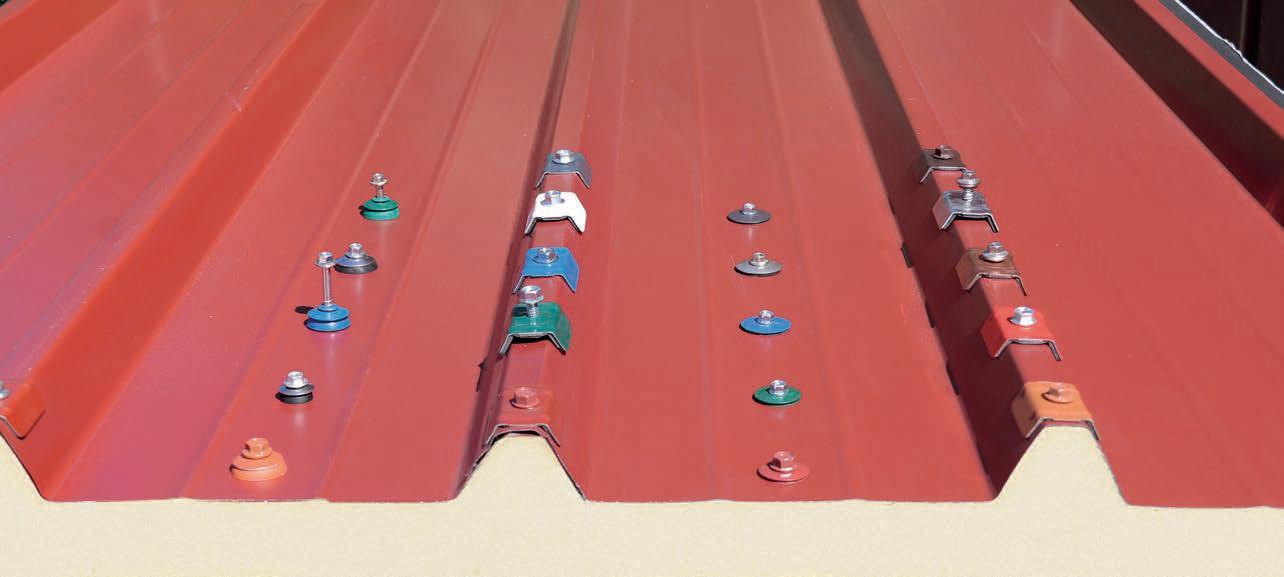
Specifier – the full process the specifier should complete is described in detail in terms of all the elements of design and selection, which need to be covered to ensure a safe choice of anchor. In addition, the design of anchors is now part of Eurocode 2 structural code (BS EN 1992-4)3. This change will hopefully increase the focus on the design of anchors as a key structural issue. Installer – all aspects of anchor installation, including specific issues that may occur during the execution, are described in detail with reference to the different anchor types and key installation factors for each. Contractor/supervisor – the role of the supervisor is vital to ensure good practice at the point of installation, and these key activities are described in the code. Also important to the contractor is changing specification, which is perfectly acceptable, if carried out correctly, to ensure a truly equivalent alternative anchor. The code provides a clear process for all of these functions.
In essence, the means and methods required for a safe anchor installation, and mitigation of potential issues arising, are already available to the industry. What needs to still be addressed, as identified in BS Flex 8670, is a framework to achieve competence in all roles and functions within the anchor sector.
Delivering competence
The goal of creating comprehensive competency frameworks by sector and function will come in due course, but will take time. Within the anchor sector, we need to take an honest look at the current situation. At present, the knowledge and skills elements of competency are being addressed principally through training. This is available through many mediums and varies greatly in quality, accuracy and delivery, and only covers limited roles, particularly installation. Any training delivered should be certified and required to be consistent, accurate in content and delivered by a competent trainer.
In addition to training, systems of certification and accreditation are important in covering all aspect of competence. Currently the only such accreditation is the NVQ in ‘Installation and testing of Anchors’4 , which is a more comprehensive qualification of competence, but again covers installation.
To look at the key roles in an anchor application, as described above, stakeholders need to consider a number of things. This includes providing training and development plans for engineers who carry out the design and selection of anchors in-line with EN 1992-4 and BS8539. Contractors should also provide systems to ensure employment of competent installers and provide training to their managers and site supervisors on all aspects of anchor applications in-line with BS8539. Installers must also be able to prove skills and knowledge through certified training or a suitable qualification such as an NVQ. These actions should be considered as minimum requirements as first steps to complete competence for all roles and functions in the anchor sector.
To achieve the objective of industry competence, the key stakeholders, manufacturers and trade bodies must commit to achieving this and work to developing a unified approach.
www.the-cfa.co.uk
References
1. BSI Flex 8670: v3.0 2021-04 ‘Built environment – Core criteria for building safety in competence frameworks – Code of practice’ 2. BS 8539:2012+A1:2021 ‘Code of Practice for the selection and installation of post-installed anchors in concrete and masonry’ 3. BS EN 1992-4:2018 ‘Eurode 2- Design of concrete structures’ 4. Level 3 NVQ Diploma in Testing, Inspecting and thorough Examination Occupations (Construction) – Installing Construction Anchors and Site Testing of Construction fixings

HEAVY-DUTY ANCHORS FEATURE
Safety critical applications and anchors
Anchors are often used in safety critical applications, but what is a safety critical application and how important is using ETA certified anchors? Here, Rob Lee, anchor specialist and regional sales manager at Walraven, discusses the importance of ETAs and the role of the BS8539:2012 code of practice when it comes to selecting anchors.
T
he European Technical Approval guidelines define safety critical applications as being: “Applications in which the failure of an anchor could result in collapse or partial collapse of a structure, cause risk to human life, or lead to a significant economic loss.” Over the past decade or so there has been a number of major fixing failures, resulting in the collapse of installations causing serious injury or even death. The most common reasons these occur are incorrect anchor selection, incorrect installation of anchors or anchor specification changes. To help ensure this doesn’t happen, it is useful to have an understanding of the relevant guidelines such as BS8539:2012 and what ETAs are.
BS8539:2012 is a code of practice for the selection and installation of post-installed anchors in concrete and masonry. It covers every aspect of the correct use of fixings drilled into concrete and masonry for safety critical applications. If you are a specifier, distributor, contractor, installer or tester, your roles and responsibilities in the use of construction fixings are set out in this British Standard. If your decisions or actions result in the failure of an installation, the British Standard Code of Practice BS8539:2012 states that you could be held accountable in the event of a fixing failure. To help ensure this does not happen, the code recommends the use of anchors with a European Technical Assessment (ETA).
An ETA is a recognised framework worldwide for testing anchors, assessing and interpreting test results and publishing them in a standardised format. An ETA will set out what applications the anchor is suitable for, it’s application limits, performance characteristics and how it should be installed. To gain an ETA, a product must have been rigorously tested to strict EU derived standards known as EADs (European Assessment Documents), formerly ETAGs.
There are plenty of benefits of using ETA certified anchors. This includes guaranteeing the anchor will not fail, provided the anchor has been selected and installed as outlined within the ETA. This means that the liabilities of the specifiers and installers are safeguarded and the installation will comply with BS8539. Anchor selection is also made easier with ETAs. Designed according to the relevant design method, along with software to guide the selection process, specifiers can be confident that the most suitable anchor has been chosen. This ensures economic design of anchors with an appropriate safety margin.
Detailed installation instructions are also provided in the ETA giving the contractor peace of mind that installation can be carried out correctly. Correct installation is paramount to avoid anchor failure in the future. Finally, performance values of approved anchors can be relied upon. ETA certified anchors also have CE Marking, which means that the anchor delivered to the job site will have exactly the same performance values as those tested in the approval process.
Can anchors without an ETA be trusted?
There are many anchors on the market without an ETA. These products may have some performance data published by their manufacturer, supplier or distributor but can we trust this? The reality is that determining anchor performance is a complicated matter. ETA testing subjects anchoring products to a huge range of complex tests to ensure the safety and reliability of their performance in a multitude of situations.
Can you be sure that the testing on non-approved anchors has been carried out to the same stringent criteria? Can the product performance data be trusted? The truth is that we cannot be sure and these products will not offer guarantees of performance in the same way an ETA certified anchor will.
To use a non approved anchor is a risk, and you must decide if it is one worth taking. For safety and peace of mind Walraven Ltd always recommends using ETA certified anchors. ETAs were introduced for a reason so why risk using anything else?
Walraven’s mechanical and chemical anchors are ETA certified, designed for optimum performance and manufactured for maximum safety – so users can be sure they offer a reliable and safe fixing. Alongside its product range Walraven offers a technical support service, anchor selection software and onsite support to help every step of the way.
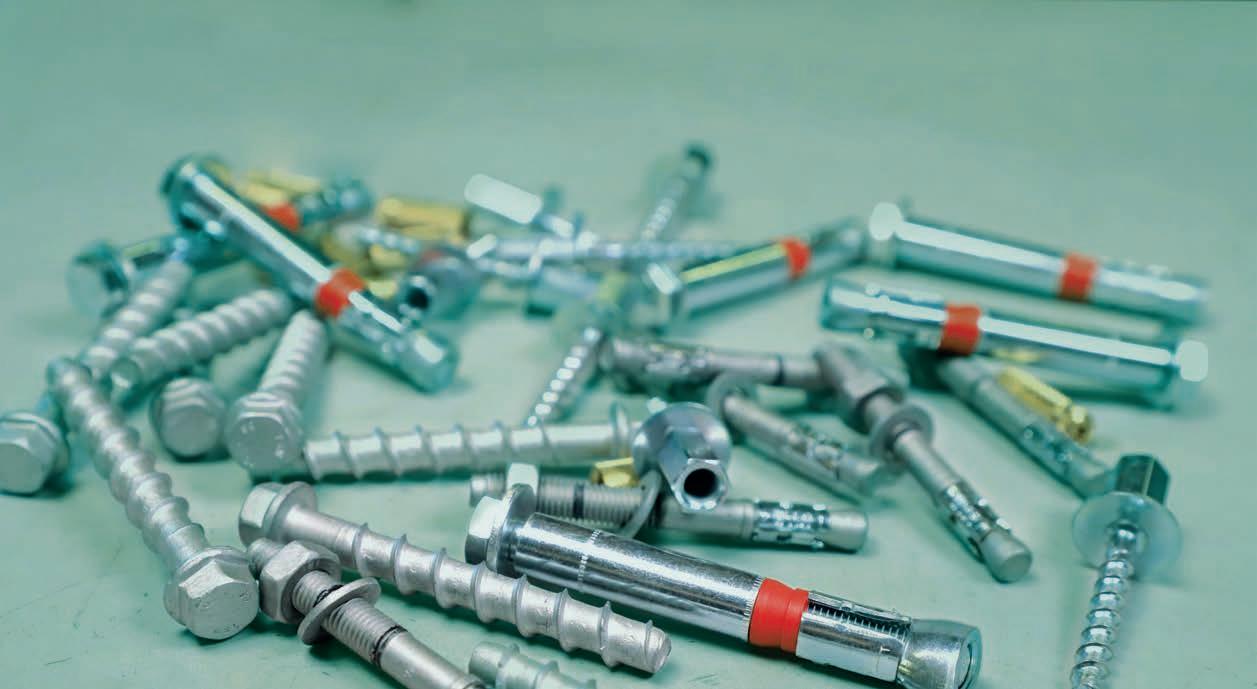
HEAVY-DUTY ANCHORS FEATURE
Removing the guesswork with JCP
JCP, the specialist fixing division of Owlett-Jaton, has seen a continuous increase in the number of requests for product testing, which it says has been driven by main contractors wanting to remove guesswork and ensure safety and compliance. For instance, JCP was recently asked to carry out an on-site pull test on a JCP torque controlled heavy-duty hexagon bolt anchor.
T
he on-site pull test was carried out on a large six storey residential development in Wandsworth, London, UK. A hoist company had been contracted to install multiple hoists, which required certification to demonstrate the chosen fixing’s suitability and capability. The fixing was a JCP torque controlled heavy-duty hexagon bolt anchor.
These anchors are CE approved and ETA (Option 1) certified, substantiating their use in cracked and non-cracked concrete. Plus, they are also approved for use under seismic actions C1 and C2 and offer high tension and shear resistance. They also have resistance to fire exposure of 30 – 120 minutes and come with a fire classification of A1. In addition, a compression ring helps prevent turning and stop torque slippage, whilst a three part expansion sleeve allows for smaller spacings and edge distance with high loads.
Whilst most pull testing is performed during the build phase, JCP is now often becoming more involved at an earlier stage. As a wholesaler, JCP is a supplier to the distributor and merchant trade, but the technical support it provides has led the company to start becoming involved in the specification aspect of projects. Contractors are frequently required to provide proof of testing for fixings. It is an expensive and time-consuming practice, but one that is vital. Whether it is in-line with a building regulation requirement, or for peace of mind, JCP area sales managers are on hand to offer such testing. A European company currently developing a new cutting-edge barrier system has also recently approached JCP to engage the company at the design stage. Working closely with its product development team, JCP has been heavily involved in the anchor calculations following development testing by the developer, ensuring the products specified meet the requirements of the new system. In addition to on-site testing, JCP offers other resources to ensure the correct anchor is chosen and installed effectively. Its Anchor Calculation Program (ACP) is available to download from the JCP website and is designed to simplify specifying connections to floors, ceilings, and walls, and factors in loadings, spacing, and edge distances. To help installers, the website also hosts an installation video for the heavy-duty anchor range that demonstrates clearly how these fixings should be installed correctly.

www.jcpfixings.co.uk
HEAVY-DUTY ANCHORS FEATURE
Increasing performance of mechanical anchors
Bossong has updated its NWS-CE mechanical anchor according to the EAD guideline 330232-00-0601, which it says has increased its performance by about 30% when compared to its previous version.
O
bserving the load data in the new certification Bossong SpA has released a chart, pictured right, showing the admissible tensile load values for the various certified diameters. The company points out that the new version enables the use of a shorter length anchor to fix the same thickness. This means a less expensive anchor can be used, resulting in a lower labour cost because the hole drilled will be shallower.
“Thanks to this new load data the NWS-CE mechanical anchor has achieved performances equal to those of the best Option 7 mechanical anchors on the market,” proudly states Bossong. “The anchor features a number of strengths and is for diameters M8, M10, M12, M16 and M20, which are the most used diameters. Thanks to this the customer can carry out the installation with reduced depth.”
This mehanical anchor is available in galvanised steel, inox A2 and inox A4.
30.0 25.0 20.0 15.0 10.0 5.0 0.0 Admissible tensile loads Admissible tensile loads
6 8 10 12 14 16 20 Diameter Diametro VECCHIOOld version NUOVO New version
HEAVY-DUTY ANCHORS FEATURE
Anchors for the most demanding projects
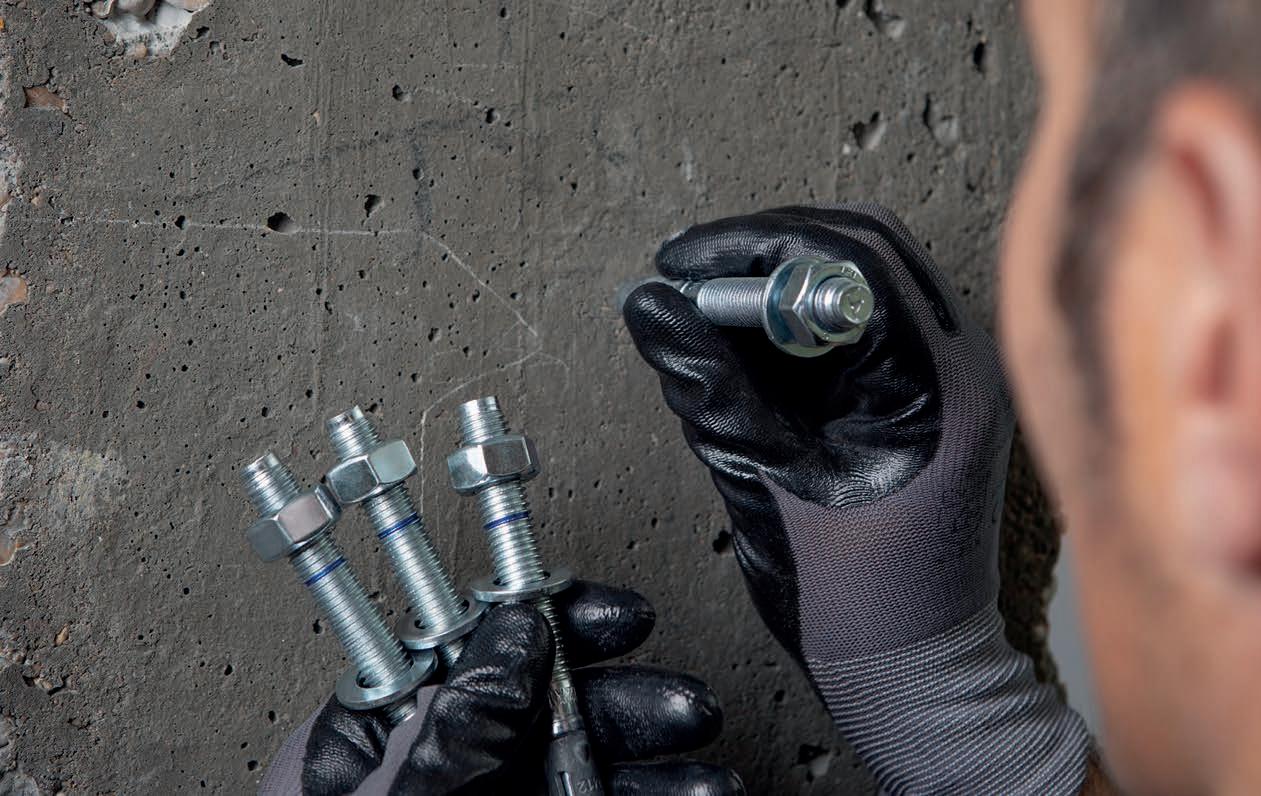
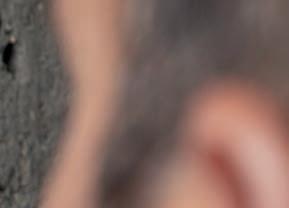
INDEX – A Perfect Fixing says its TH/TF anchors, MR metal anchors, SL metal anchors, and chemical anchors, are ideal for use in the most demanding projects, where the efficacy and performance of the anchor are essential for a perfect fixing.
F
ast and easy to install, the TH/TF approved high performance anchors ensure maximum performance in the nine different head models, making them suitable for installing structural and non-structural elements such as railings, shelves and temporary elements. The anchors have up to three different screwing depths (in the diameter 10 version) in C20/25 non-cracked concrete.
Their use of mechanical interference means they can be utilised in conditions with short distances between the edge of the concrete element or to other anchors, and with hollow core slabs with slim concrete thicknesses for installation. The anchors are also simple to uninstall, leaving the surface of the base material flush after use.
The anchors are available in two different coatings – zinc-plated ≥5μm and Atlantis C3-H, a special coating that provides greater corrosion resistance in category C3 atmospheres. The anchors have maximum recommended loads in C20/25 non-cracked concrete and C20/25 cracked concrete and have two ETAs – (ETA – 20/0046) and (ETA – 20/0494), as well as being approved for fire resistance and seismic approval C1 and C2.
Also available, the INDEX MT range of eight models is approved according to ETA Option 1 and Option 7 in a wide variety of metrics and lengths. The anchor’s clip expands during installation, generating friction with the base material (stone, concrete, cracked and reinforced concrete) to create the fixing.
The main advantages of this type of anchor are that it’s fast to use; once installed they can be put under stress immediately; they’re approved for cracked and non-cracked concrete; as well as also having seismic approval C1 and C2 and approval for fire resistance.
As well as this, the SL metal anchors for heavy loads are available with countersunk and hexagonal head. The anchors come in a wide variety of lengths and metrics and are approved under ETA Option 1, CE and R30-120 fire resistance for use in concrete structures. The plastic component in the body prevents the anchor from breaking on itself while the anchor is being installed, ensuring its correct installation and expansion.
As an alternative, chemical anchors can be used for installing large loads in concrete or brick. Depending on the base material and the installation area (indoor or outdoor), customers can choose from vinylester, polyester or hybrid versions, such as the MO-H version, which is a versatile option developed for more demanding projects. Depending on the model, these chemical anchors are suitable for use in cracked or non-cracked concrete, masonry, and/or connections of post-installed reinforcing bars.
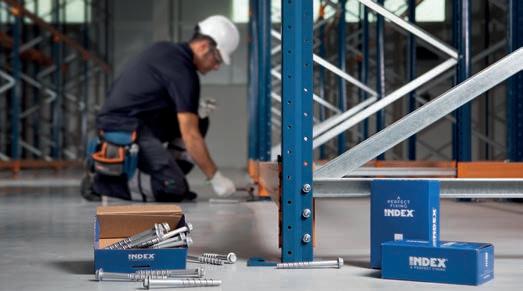
Over 7,000 products and counting
INDEX – A Perfect Fixing has launched its new general catalogue with new products and ranges, including over 7,000 products, as well as news and new type approvals and certifications. Among the most notable new products included in the catalogue is the new range of fixings for ETICS (External Thermal Insulation Composite Systems). This range is made up of fixings and accessories such as the AIS plug (available in polyamide and metal), rosette, rosette for use with screw, metallic plug, washer for metallic plug, and spiral fixing for installation of lightweight elements on the synthetic insulation material.
The ETICS system reduces the emission of pollutant gases, contributing to protecting the environment while reducing the need for heating and/or refrigeration. This offers continuous energy savings throughout the year, facilitating a stable temperature in the home throughout the year.
T-Tec system now with ETA certification
Eurotec’s T-Tec system, consisting of the T-profile timber connector and the self-drilling EST rod dowel, has now been awarded with a European Technical Assessment certification (ETA – 21/0710).
The combination of the two products enables the production of invisible, rigid timber-to-concrete and timber-to-timber connections, thus providing an ideal basis for mainto-secondary beam connections. Whether connections are horizontal or at an incline, the T-Tec system holds the timber in position in a secure and load-bearing manner.
What’s more, due to its double threaded screw and innovative arrow drill, the EST rod dowel can be easily screwed through the timber and aluminium of the T-profile without any need for pre-drilling.
Eurotec explains: “This certification refers to the combination of the T-profile and the EST rod dowel. Accordingly, certification is only permitted for the joint use of the two products. The specified forces and technical data set out in the approval can only be complied with when the products are used together. The values from the product data sheets must be observed in this regard.”
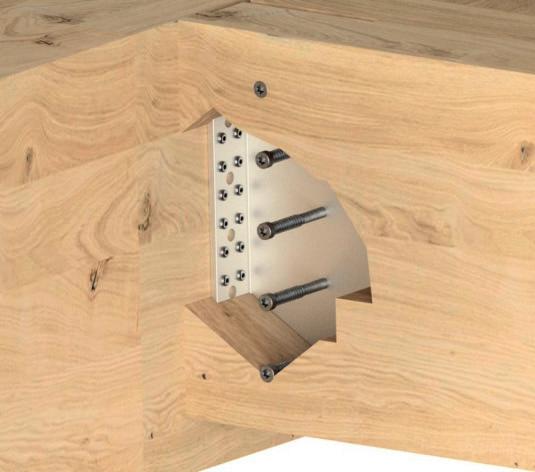

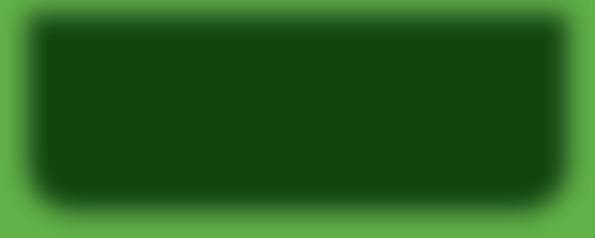
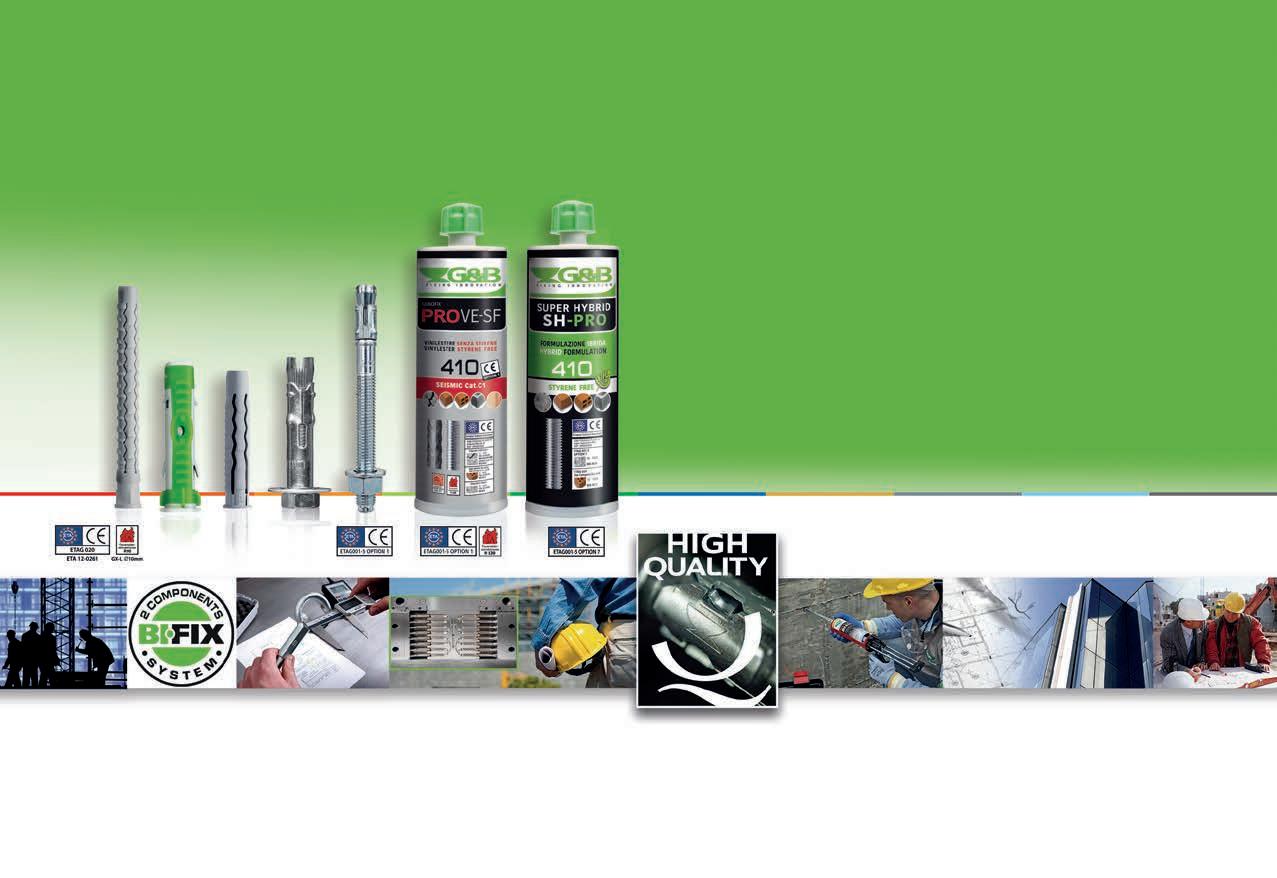
CELO ResiTHERM® with ETA approval
With ResiTHERM® 16, CELO says it has developed a new innovative distance mounting system for ETICS insulated façades, which is the first product of its kind on the market to achieve an European Technical Assessment (ETA – 22/0229).
W
ith the ResiTHERM® 16, heavy loads such as canopies, awnings, French balconies, air conditioning units or satellite dishes can be safely and reliably attached to external insulation – without thermal bridge. CELO Befestigungssysteme GmbH explains the fixing’s thermal separation module ensures effective thermal separation, as well as a high-quality polyamide with high glass-fibre content providing the necessary stability.
The preassembled sealing ring made of high-quality, weather resistant EPDM also provides a tested seal against driving rain; with the usual grain size of the plaster, up to a deflection of 3mm. There is also a simple installation process – the anchor rod with the glass-fibre-reinforced thermal separation module pulls itself, self-cutting through the plaster into the insulation material. At the same time, this ensures a perfect setting process with the chemical mortar compound and, last but not least, cleanly seals the drill hole through the EPDM seal. The result is a clean look with a relatively small diameter of the cover plate.
The ResiTHERM 16 can be used in insulated façades made of concrete, solid and perforated masonry, as well as aerated concrete. It covers insulation thicknesses of up to 300mm in concrete or 250mm in perforated masonry. For smaller insulation thicknesses, the M16 anchor rod is cut to length accordingly. It is used together with the ResiFIX injection system from CELO. The connection thread is an M12 thread, however, an M12/M10 reducing set screw or a common stainless steel screw can also be used.
As well as this, CELO also has another product in this product family – the ResiTHERM® 37, which is an optimal product solution for ETICS insulated perforated bricks and is characterised by superior load values, especially tensile loads in perforated bricks.
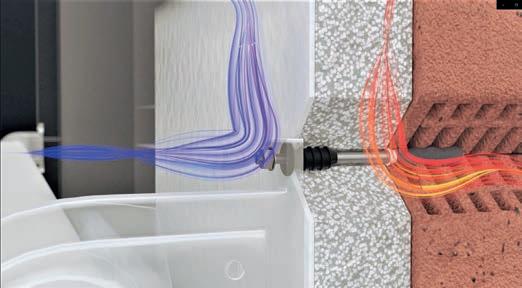
www.celofixings.com
Think Fixing
G&B FISSAGGI, the Italian company
G&B UK warehouse
Quality products with a service to match available for next day delivery direct from our branch in Sheffield (UK mainland only).
Contact our experienced staff to assist you for all you need.
G&B Fissaggi S.r.l. Italia
Corso Savona, 22 10029 Villastellone (TO) tel. +39 011 961 94 33 fax +39 011 961 96 39 info@gebfissaggi.com
G&B Fissaggi UK warehouse
Unit 16 Riverside Court Don Road - Sheffield - S9 2TJ (UK) tel. 0114 242 0074 fax 0114 242 0075 uksales@gebfissaggi.com
G&B Fissaggi Vertretung Deutschland
johnengebfissaggi@gmail.com
G&B Fissaggi Ibérica
gbiberica@gebfissaggi.com
G&B Fissaggi Benelux
export@gebfissaggi.com
G&B Fissaggi France
export@gebfissaggi.com