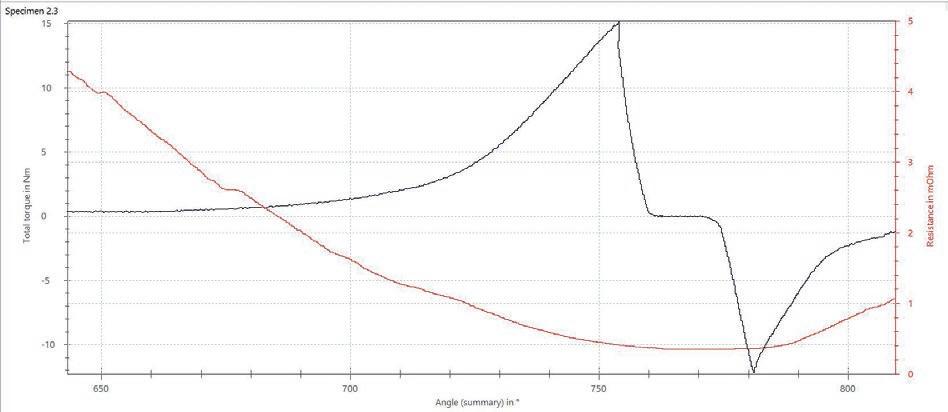
3 minute read
FASTENER TESTING
tests, they can ultimately determine the correct balance between tightening torque and electrical contact resistance for their products and define the optimal tightening specification of the bolted joint on this basis.
Highly sensitive – and ideal for the microohm range
Advertisement
The new module for Kistler’s ANALYSE system uses the Kelvin method to measure electrical resistance. With this method, leads connected to the Unit Under Test (UUT) impress a constant current into the bolted joint. A connected measuring device registers the voltage loss caused by the resistance. Because the measuring module is highly sensitive, the smallest changes in resistance – even down to the microohm range – can be measured as the bolted joint is gradually tightened and loosened.
For accurate results, it is important that only the resistance in the UUT is registered. To meet this requirement, the test set-up from Kistler isolates the bolted joint under test so that current flows exclusively through the UUT, and the instruments only measure the actual resistance of the joint. The choice of measuring points during the test is of overriding importance here. The closer these highly sensitive measuring tips are
The detailed evaluation shows how the electrical contact resistance and tightening torque of the bolted joint behave in relation to one another to the bolted components, the more precise the results will be. As an additional option, a camera can be installed to record the entire test procedure. The corresponding module of the evaluation software then synchronises the video and the recording of the measured values, so any unusual or suspicious values can be checked quickly and easily.
Combined testing of quality characteristics
Exact measurements and detailed visualisations of the results provide manufacturers with a sound basis for decisions on whether the current-carrying parts of the joint meet the requirements for durability, safety, and reliability, as well as enabling them to compare different materials. Providing one solution that combines different measurements –such as friction coefficient, tightening torque, preload or electrical contact resistance – means manufacturers can use Kistler’s ANALYSE system to test components and their behaviour in one single test procedure. Users can now determine optimum conditions and tightening specification for each bolted joint – so the products they bring to market are safer and more reliable. www.kistler.com
Combined competencies at Fastener Fair Global
At this year’s Fastener Fair Global in Hall 1, stand 804, Kistler will be presenting individually combinable applications for quality control in the fastener industry – with customers able to put together a solution that fits their individual needs exactly.
Quality control in the fastener industry is as diverse as fasteners themselves. In order to meet numerous official and industry specific standards, manufacturers must continuously collect reliable data on the properties of their products. Depending on the type of fastener, however, the data required can vary greatly. In addition, it’s frequently not just one quality feature that needs to be checked, but a combination of different properties.
At this year’s Fastener Fair Global, Kistler is presenting the expanded portfolio of its ANALYSE system – the universally applicable test stand for determining friction coefficients can be combined with additional modules for resistance and length measurement, as well as for fracture testing. Thanks to its modular design, fasteners of various sizes can be tested quickly and precisely, thus allowing for reliable statements on product quality on the basis of various measured variables.
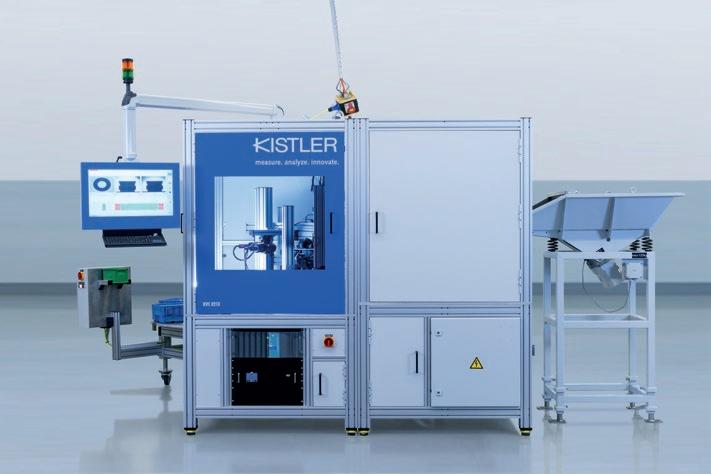
“With the numerous possible applications of the ANALYSE system, we are far surpassing compliance with norms such as ISO 16047. Customers can draw on our combined expertise and will receive an individual configuration entirely in-line with their requirements. Accurate measurement data ensures that they meet all their quality demands,” explains Kay Dierecks, product manager fastening technology at Kistler Group. www.kistler.com
Fastener Fair Global will also mark the first time that Kistler presents an inspection solution for bolts using optical quality control: The KVC 821 test stand, which includes cameras that record bolts, nuts or other fasteners and collect precise data on the dimensions, geometric properties and drive characteristics of the test parts – with the help of the KiVision image processing software. If required, an Eddy current test can also be integrated into the test stand. If the system detects a defect, the part in question will automatically be sorted out.
This quality inspection is not limited to individual parts, Kistler’s optical test stands analyse up to 800 parts per minute, thus maintaining quality requirements even in case of large quantities. The data collected is stored by each test stand in its own database, enabling manufacturers to identify long-term trends in production and analyse them using software solutions by Kistler.
Instron’s Industrial Series and New 6800 Series universal testing systems provide SUPERIOR FRAME STIFFNESS and the DURABILITY needed for testing a broad range of fasteners.
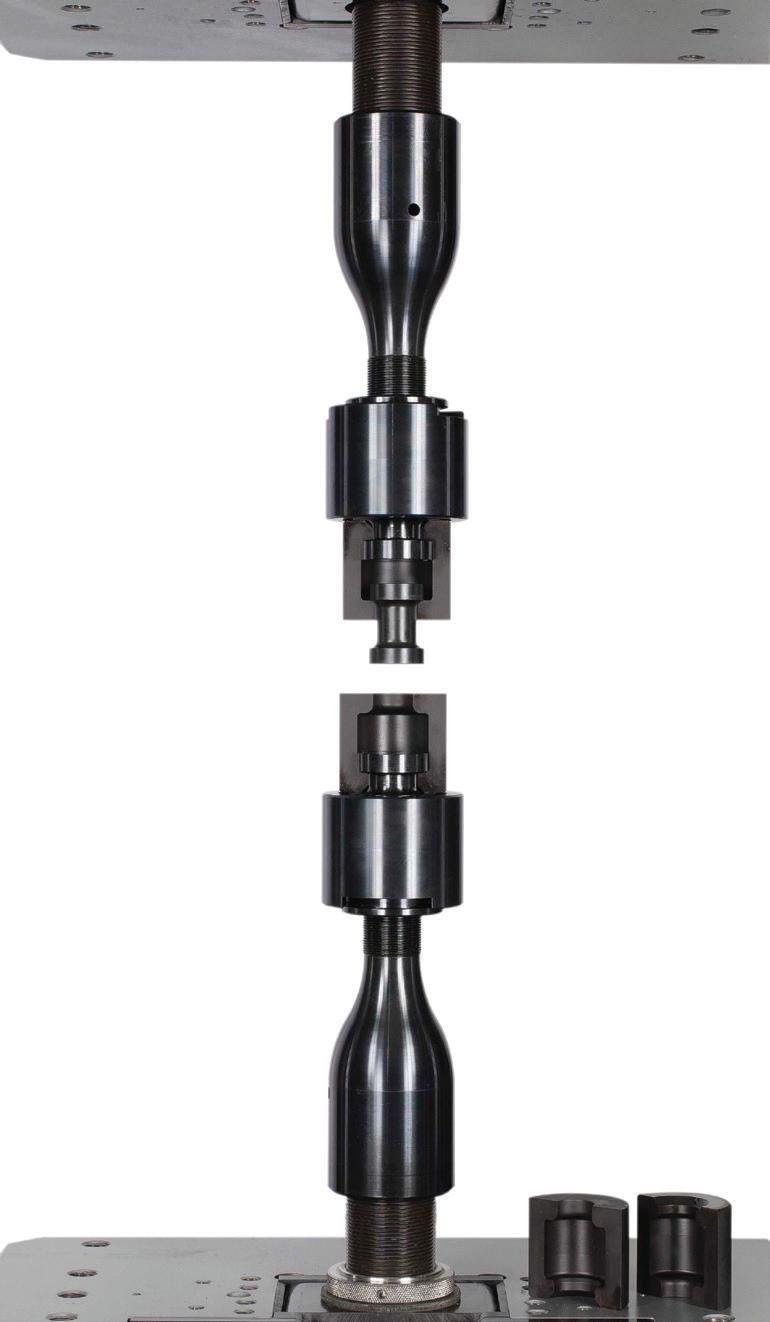
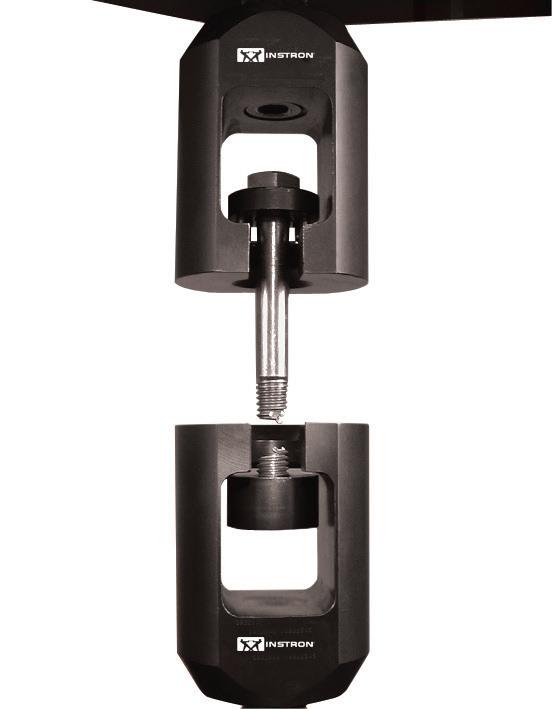
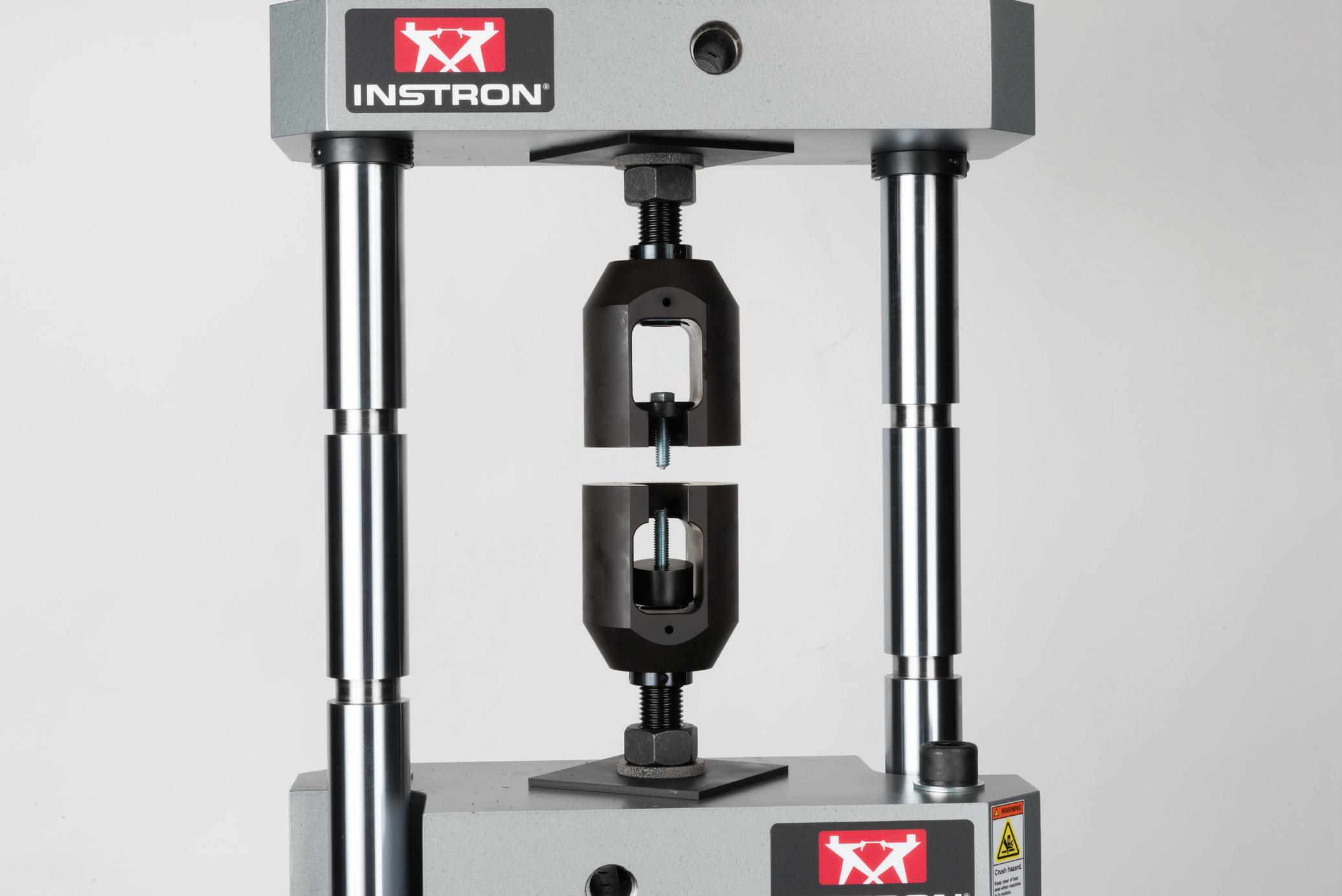
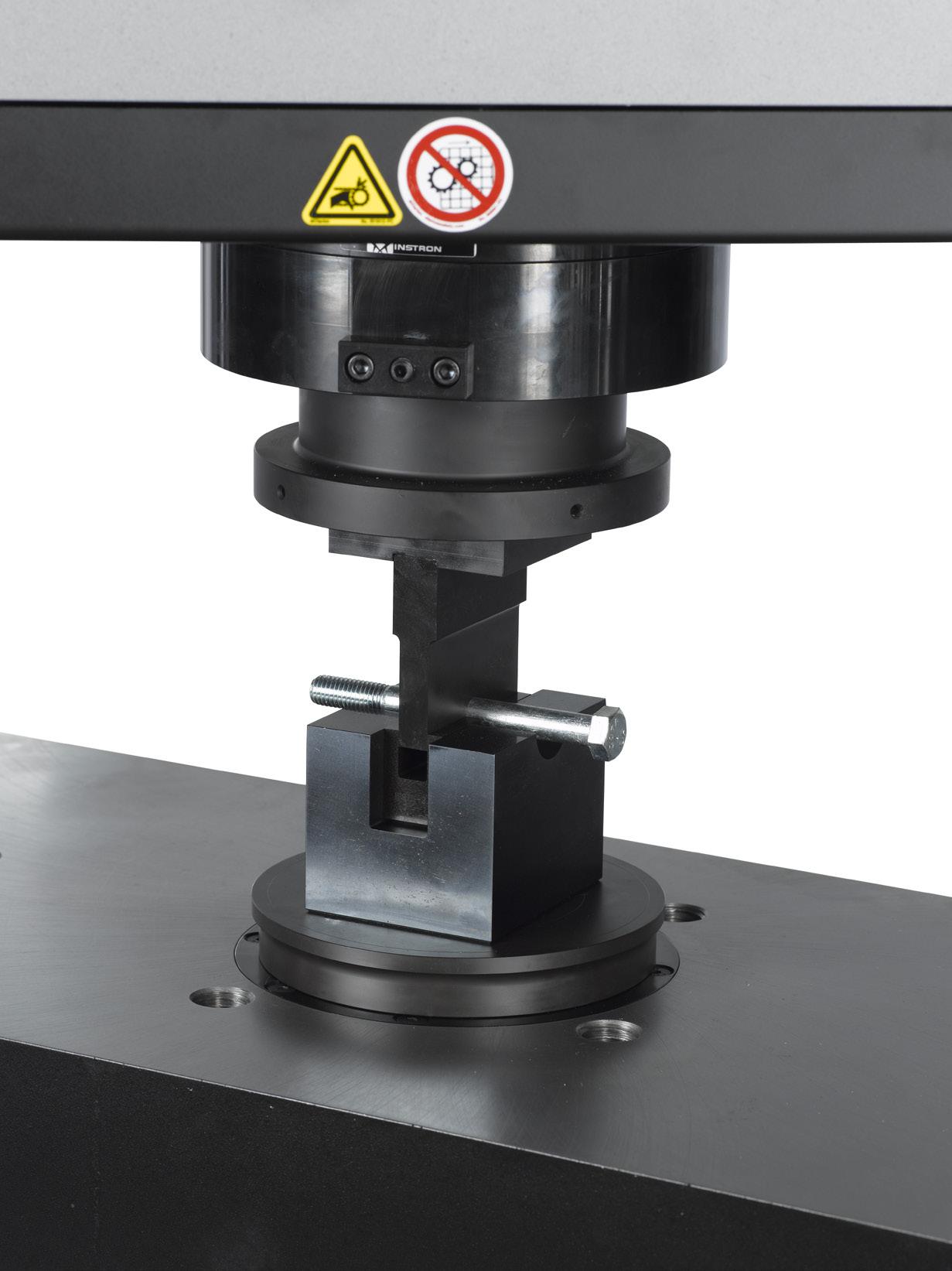
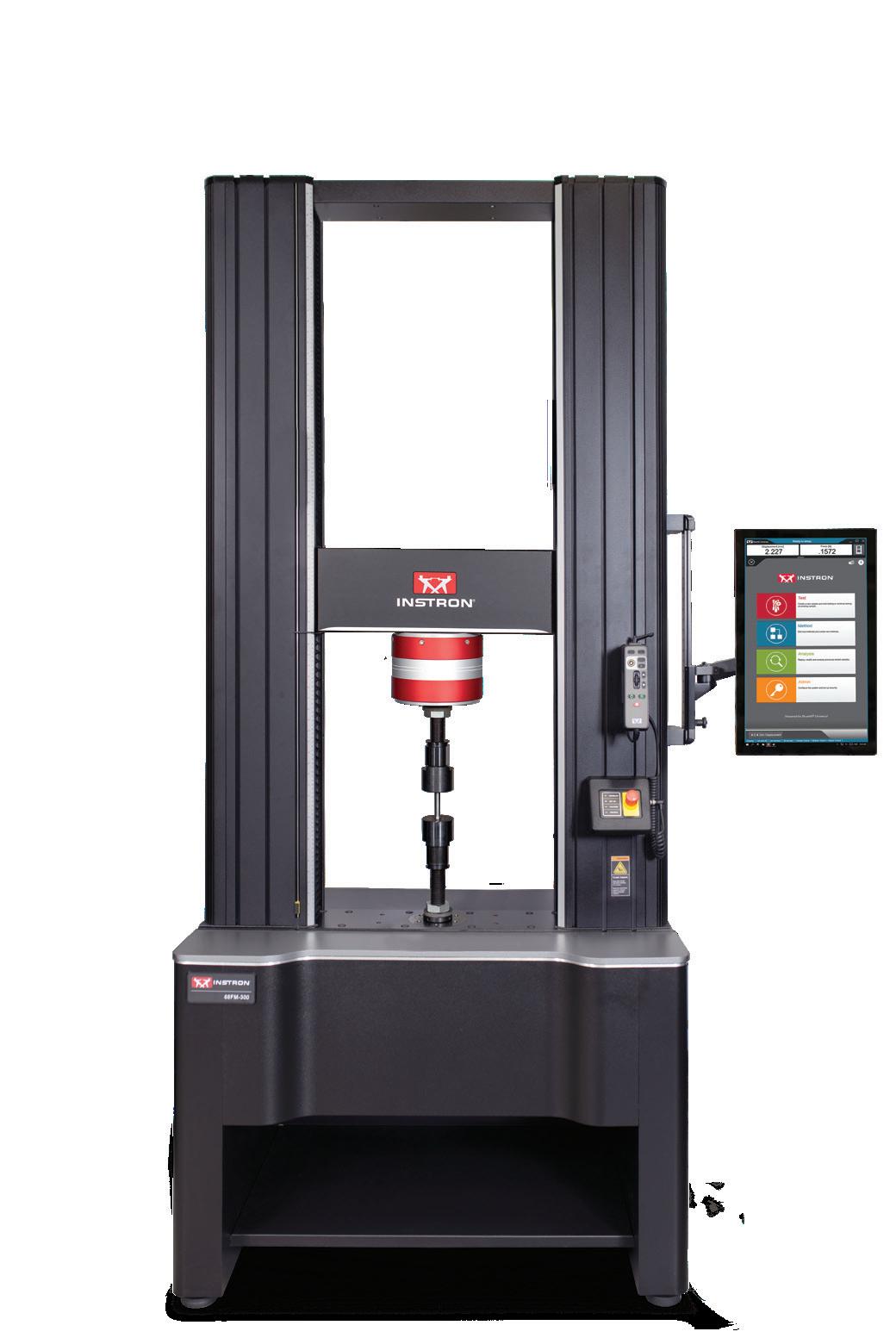
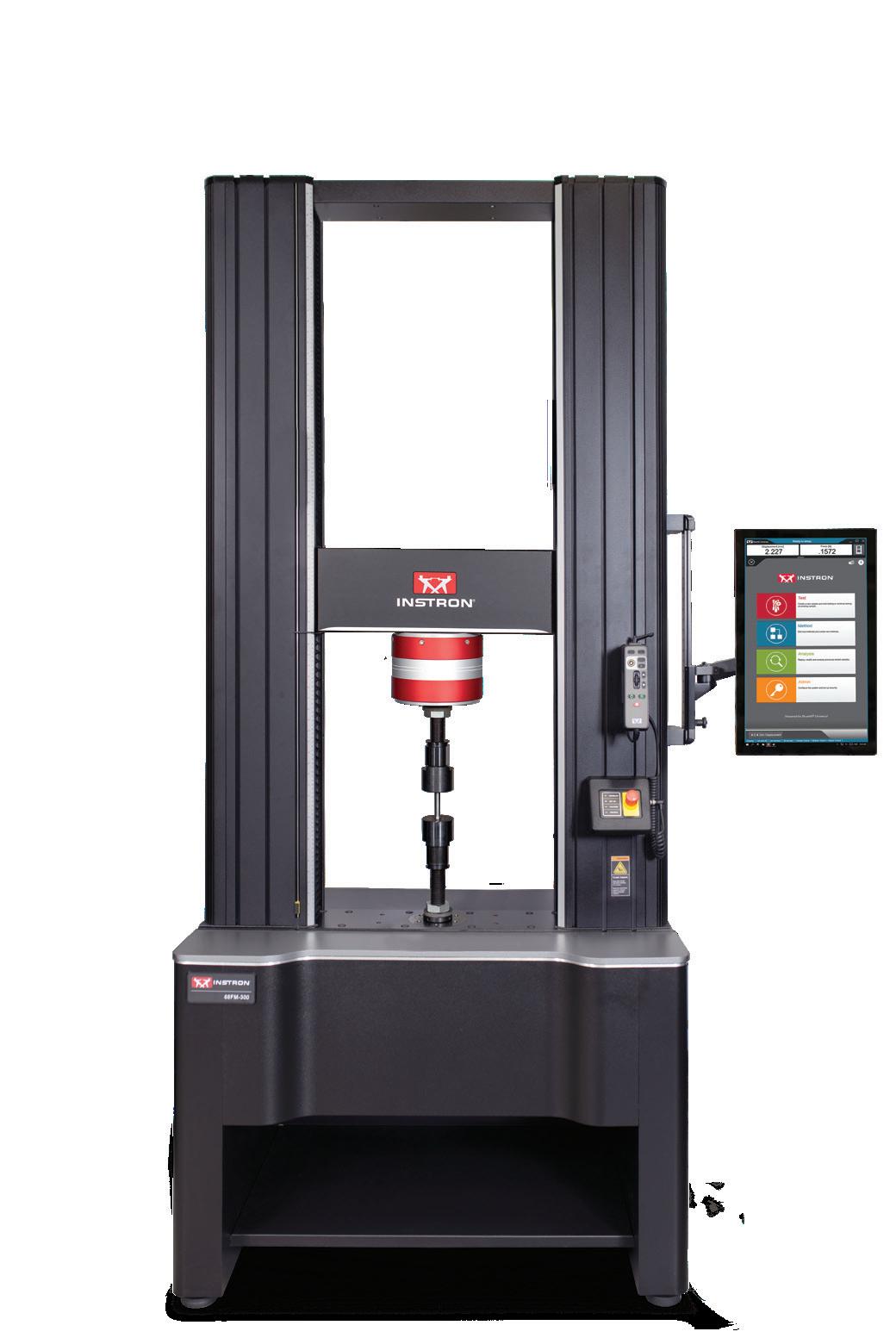
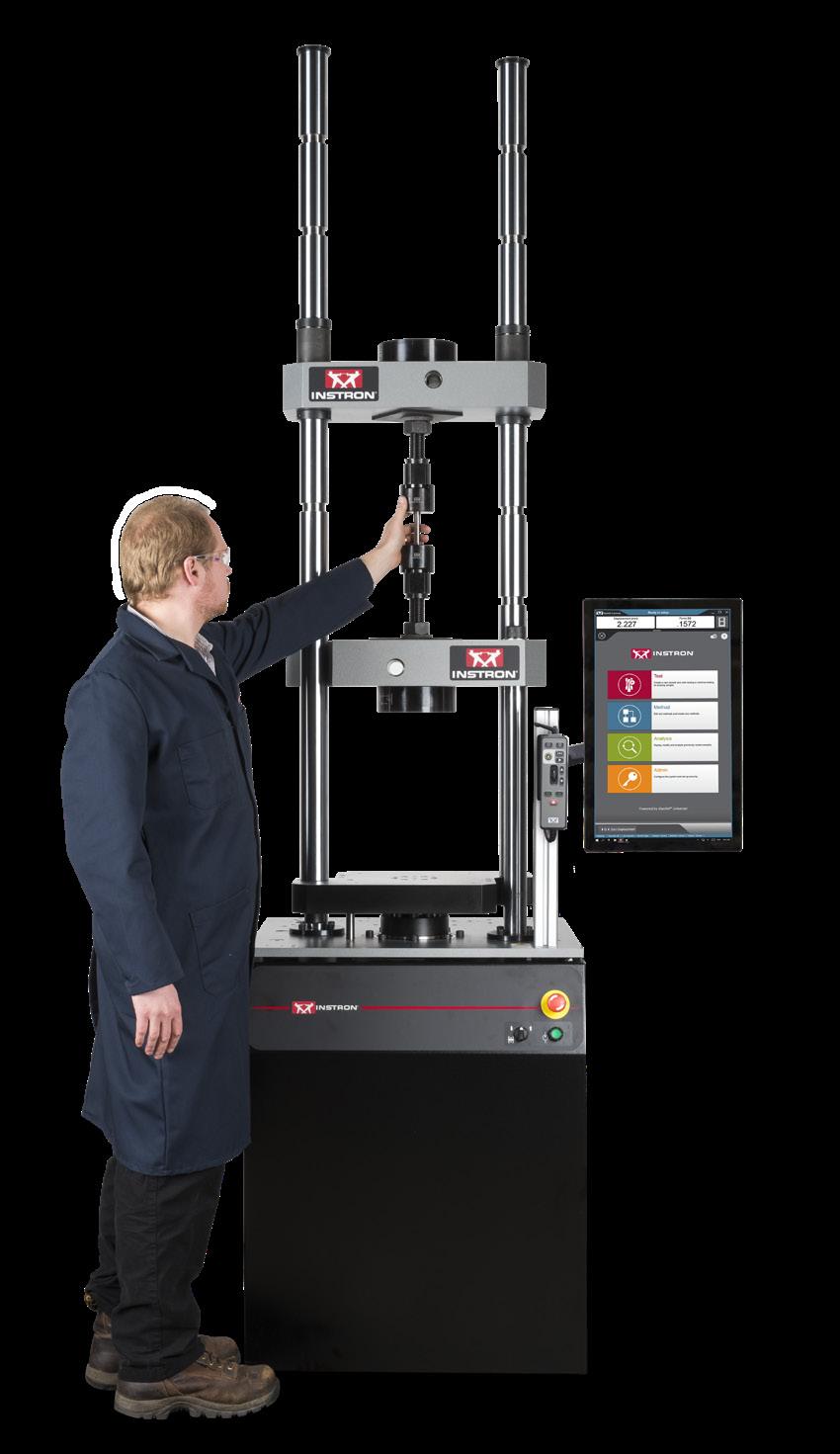
