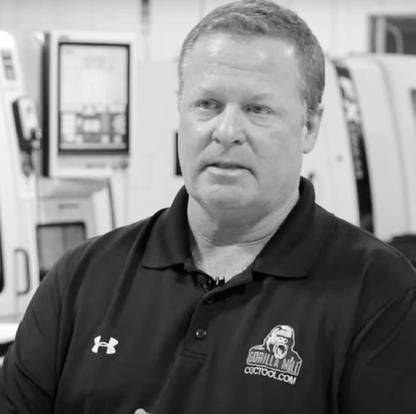
1 minute read
Ultra-Fine Filtration for Many Challenging Applications
CUTTER & TOOL GRINDING
Manufacturers of precision cutting tools have discovered grinders equipped with a Transor system provide them a significant competitive edge in a very competitive market. Transor’s ultrafine filtration addresses the global challenges of producing superior cutting tools faster and cheaper. By reducing the debris on the grinding wheel, Transor’s ultrafine filtration extends its life by a significant period. Other benefits include faster cycle times, improved machine uptime, finer surface finishes, reduced maintenance wth a cleaner, safer working environment.
Advertisement
With automated sludge handling, the filtered carbide/tungsten sludge is ready for reclamation. Another tangible way that a Transor pays for itself.
See why Gorilla Mills trusts Transor for their end mills
Scan the QR Code
See why Revel Serras trusts Transor for their saw sharpening
Scan the QR Code

Edm
With particles at micron level or submicron level filtered out of the dielectric oil, Transor edge filtration technology enables mold processing to achieve faster, more accurate results. With a continuous supply of clean and temperature controlleddielectric after ultrafine filtration, EDM operators have discovered they can stay “in the cut” twice as long combined with finer surface finishes.
While individual results may differ based on machining parameters, Transor users typically experience production efficiency improvements ranging from 25% - 35%. It is easy to see why the payback period on a typical Transor unit is less than two years in most instances.
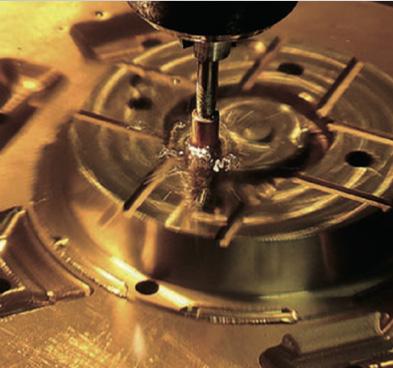
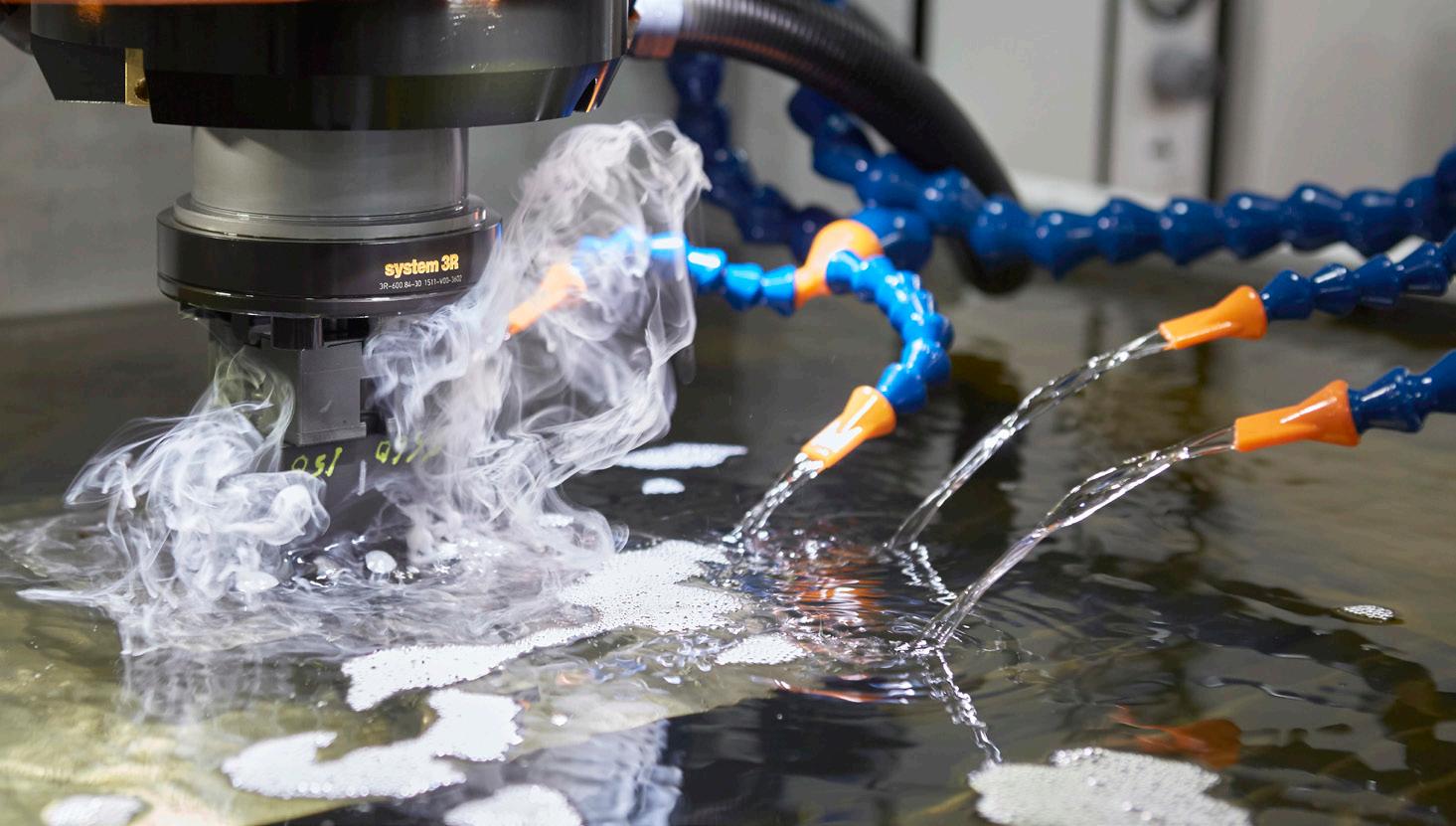
With a Transor system, the cost and trouble of replacing filter elements is minimized along with unnecessary downtime. Also, the service life of dielectric oil is greatly extended.
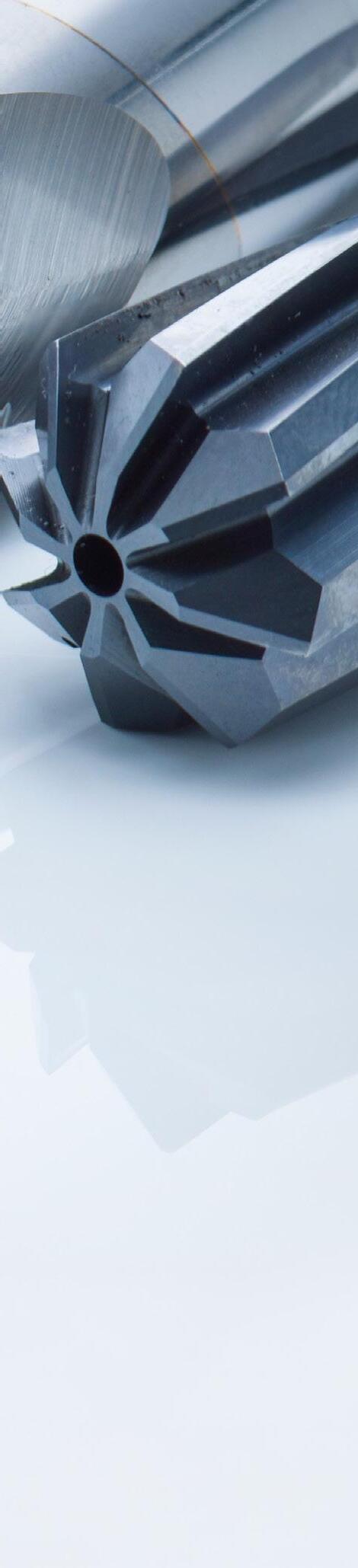