
5 minute read
How virtual reality and digital twins are transforming
HOW VIRTUAL REALITY AND DIGITAL TWINS ARE TRANSFORMING TUNNELLING
New tunnelling technology company hyperTunnel is revolutionising an industry which has seen little in the way of fundamental change in 130 years. Through technology transfer and digital transformation, this British startup is completely changing the way underground spaces are built, maintained, enlarged, and monitored. As a result, tunnelling projects are set to become more sustainable, less expensive, less time-consuming and commercially less risky – significant advantages when the world’s growing population has increasing need of underground transport and utilities infrastructure.
Advertisement
hyperTunnel’s innovative new approach is made possible by adapting technologies from industries such as Formula 1, mining, oil and gas, chemistry and surveying. This lateral thinking comes directly from the company’s leaders, who possess expertise not only in civil and structural engineering, but also a broad range of other industries. In fact, hyperTunnel co-founders Steve Jordan and Jeremy Hammond first saw the need to modernise tunnelling when jointly exploring a new approach to tidal-range energy. My professional experience encompasses nearly 20 years in top-level motorsport, working with the most advanced race car simulations, building digital twins for vehicle development and race strategy. And the chair of hyperTunnel’s technical board, Peter O’Riordan, led development of London’s Crossrail 2 scheme, the London section of the HS2 project, and the redevelopment and refurbishment of London’s St Pancras Station as part of HS1.
The founders and staff majority-own hyperTunnel. Following a successful convertible loan note (CLN) offering earlier this year, the company is seeking further large-scale investment to develop the business globally.
Swarming hyperBots
hyperTunnel’s most radical departure from convention is perhaps also its most surprising: whereas the age-old approach is to dig a hole and then build the tunnel, hyperTunnel first builds the tunnel, then digs the hole. The tunnel’s structural shell is constructed by sending hyperBots (semi-autonomous robots) into horizontal direction drilled (HDD) bores, where they perform tasks including data-gathering, drilling, spoil removal, and the deployment of composite construction material in an additive manufacturing process using the same principle as 3D printing.
By using swarm construction techniques, hundreds or even thousands of hyperBots can work simultaneously at different locations, with the ability to pass each other to move freely. They work to a construction plan created by Artificial Intelligence which provides all key construction data, such as material strength, chemical volume, and location. This radically new approach results in extremely high productivity.
VR and a digital twin
All this is made possible by first gathering data to create a digital twin of the tunnel. This twin can be viewed in great detail and high-resolution through virtual reality (VR) on computer screens. And by using augmented reality (AR), it could be possible to attend a meeting in a room thousands of miles away from the tunnel to view its interior and see live data about the condition of the structure and surrounding geology. But we’re getting ahead of ourselves, because VR’s greatest value is in the preparation phase, and there’s nothing more important. As I learned in motor racing: ‘Remember the
Five Ps: prior preparation prevents poor performance!’
Preparation entails acquiring a detailed understanding of the ground through which the tunnel will run: what the geology is, how and where this changes, and where there might be fissures, voids or water. Such information is traditionally obtained by dropping vertical boreholes along the planned tunnel path up to 500 metres apart – but because geology can change over such a distance, this method forms an incomplete picture, putting the project at risk of unanticipated difficulties and delays.
With the hyperTunnel method, however, multiple parallel core geology samples are taken along the entire path, by locating HDD test bores at the centre of the tunnel. Additional data is gathered by running a proprietary 3D ground-penetrating radar (GPR) system along the bores. Seismic, tomographic and thermal imagery data can also be meshed together, where necessary, to enhance VR visualization.
This comprehensive, multi-layered information-gathering means it is now possible, for the first time, to form a complete, data-rich picture of the tunnel’s proposed path. This data can be interrogated in the virtual world by ‘visiting’ the tunnel’s digital twin. The VR can also be used for training operatives, eliminating the cost and risk of learning tasks such as spraying concrete linings or injecting exactly the right mix of ground-stabilising chemicals along every centimetre of the tunnel’s path. This is important because tunnelling is a low-margin business which cannot afford mistakes.
The digital twin later serves another important function, as a ‘single truth’ database of construction details which will enhance asset maintenance and management. Through AR and VR, engineers will be able to see not only the tunnel’s construction and surrounding ground, but also the precise location of hidden service facilities such as cables and wires.
Maintaining older tunnels too
It is not only the building of tunnels that hyperTunnel’s methods will improve. The maintenance and refurbishment of tunnels will also become more efficient - valuable, when you think how many old tunnels are in use around the world. Earlier this year, hyperTunnel won a contract to work with Network Rail on non-disruptive tunnel construction and repairs for the maintenance and improvement of railway infrastructure, which includes approximately 650 Victorian-era tunnels across the UK. hyperTunnel’s methods are expected to bring significant cost and delivery-time improvements, as well as greatly reducing inconvenience for passengers.
hyperTunnel expects its IP-protected system to become a core part of how the world’s biggest tunnel builders and maintainers operate. The company currently employs a team of more than 30, mostly engineers, at two sites in Hampshire, England. One of these sites, the hOLE (hyperTunnel Outdoor Learning Environment), is currently conducting scaled concept testing. Work is expected to start on the company’s first completely new tunnel build by the end of 2022.
Patrick Lane-Nott, Director of Engineering, hyperTunnel
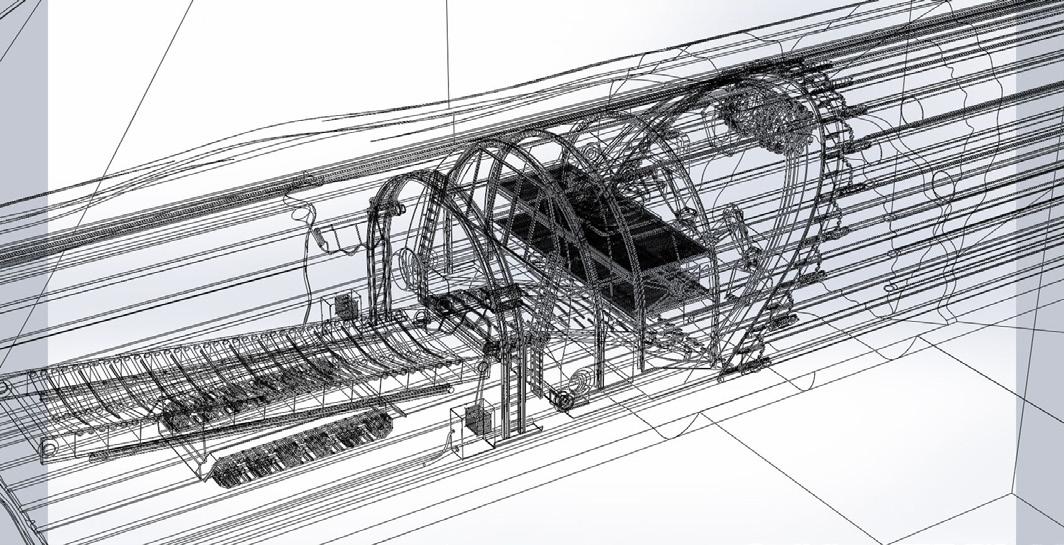
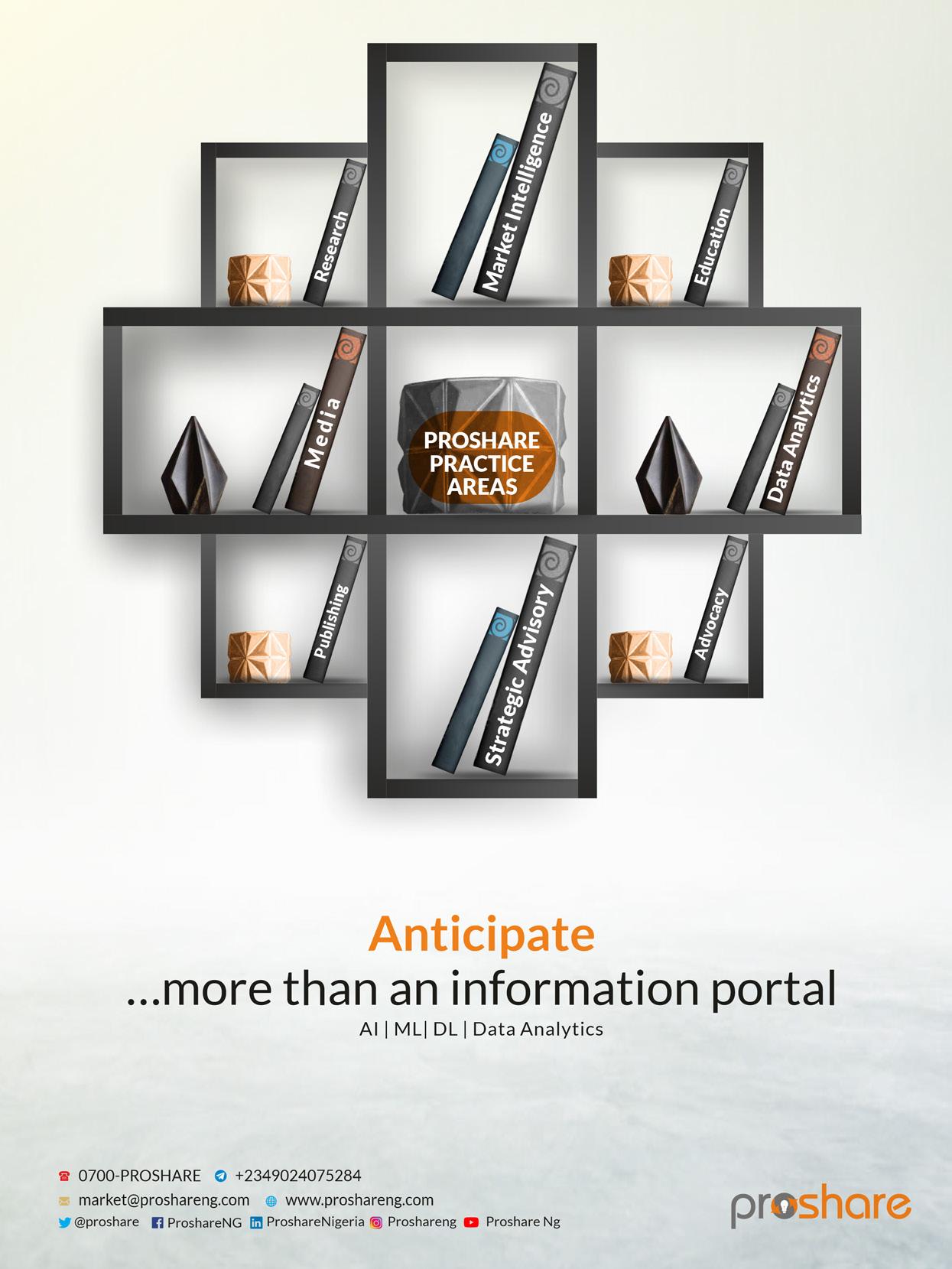