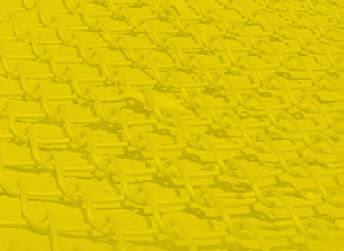
7 minute read
Sandy Neil
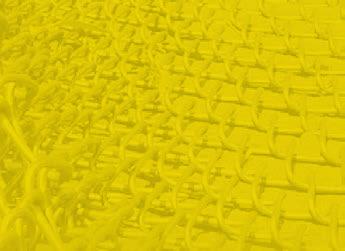

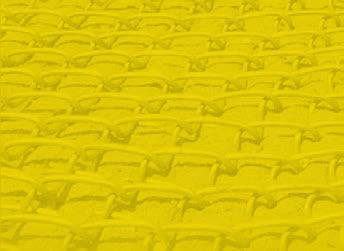

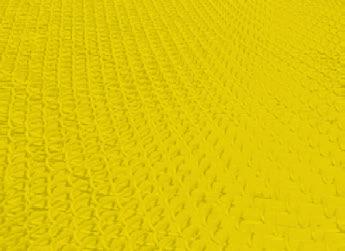
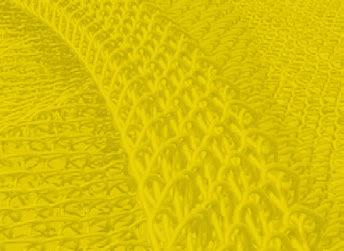

A new approach
Chile-based company EcoSea says its nets are good for farmers, fi sh and the ocean


RECYCLABLE copper submersible nets, pioneered by a Chilean company to rear fi sh “where it was not thought possible” in deep, high seas, will soon be available in the UK following successful tests.
EcoSea’’s UR30 copper-alloy cage system minimises the use of nylon mesh, which the company describes as “the main source of pollution in the seas”. It is 100% recyclable and can be operated continuously for a decade. Copper alloy is also stronger than nylon, so it helps against predators such as sea lions and seals.
“Over the past 12 years, EcoSea has deployed more than 70 of these systems around the world, growing more than 10 million fi sh,” the company says. “In addition, three farming centres in Chile were recycled after a decade of useful life, resulting in a total of 420 tonnes of recycled and resalable material.”
At the heart of the new technology is the element copper, which has antifouling, antimicrobial, and anti-corrosion properties. Copper curbs biofouling, such as adhesion of algae, sea moss, sea anemones, barnacles, and molluscs. When these materials accumulate, they can block the fl ow of water and reduce the oxygen level in the net pen, while increasing pathogens and parasites. Preventing their accumulation helps reduce fi sh mortality, and improves growth and feed conversion.
By halting the growth of organic layers in the cages, the copper alloy meshes “minimise the risky hours of diving and use of boats for cleaning, maintenance and replacement of traditional nylon nets, generating significant reductions in operating costs”, EcoSea says. Nylon netting typically must be cleaned by divers on a monthly basis, but with copper-alloy netting, the frequency of cleaning can be signifi cantly reduced. Even when cleaning is performed, removal is easy, as attachment is weaker.
The copper-alloy cages use a high-density polyethylene fl otation system, which is also fully recyclable.
“The recycling process stopped the use of 160 tonnes of nylon, the waste of 8,000 tons of fouling, which would have been deposited in landfi lls or on the seabed, and 184 tons of chemicals such as anti-fouling paint,” the company says. “It is estimated that the release of 10,300 tonnes of CO2 into the environment has been avoided so far.”
However, some environmentalists see copper as a toxic chemical – is this a potential problem?
“Environmentalists would not be wrong about the impact that copper coating/paints have on the environment, which is traditionally used on nylon or similar nets,” says EcoSea’s CEO Nicolás lon or similar nets,” says EcoSea’s CEO Nicolás Castillo. “In our case, we do not utilise any coat or paint that fl akes off over time and ends up in the bottom of the sea. Our technology utilises a copper-alloy mesh that does not fl ake off, and studies executed by independent labs have proven this does not affect the surrounding environment.”
EcoSea says the copper alloy nets also show less volumetric deformation in high-energy, deeper water: “Under severe current and wave conditions, traditional fi sh cages experience substantial volume reduction due to deformation, generating overcrowding conditions, increasing the fi sh stress and mortality rate. Our technology maintains structural integrity and cage volume under adverse weather conditions.”
The drawbacks of copper alloy are cost and weight. As for cost, the longer product life, reduced cleaning work, better fi sh health and end-of-life recycle value of copper tends to offset the initial cost, according to the company. The increased weight of copper means that fl otation must be increased accordingly. However, in some situations, weight is a good thing as it keeps the net from losing its shape or tangling, especially in rough seas, the company says.
Castillo says: “Our submersible technology allows fi sh farming in open ocean waters, where traditional cage technology doesn’t. By submerging the cages offshore, it is possible to avoid rough ocean conditions on the surface such as high waves and water temperature changes.”
The antifouling characteristics of EcoSea’s cages material reduces the proliferation of pathogens and parasites within the fouling layer, while the ability to submerge provides an additional defence against sea lice, since they
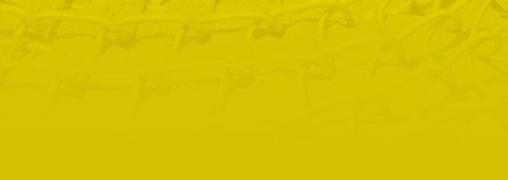
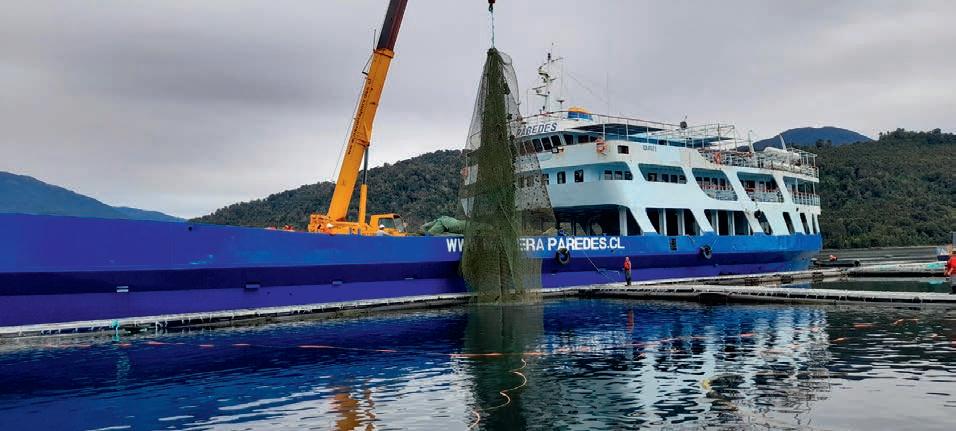

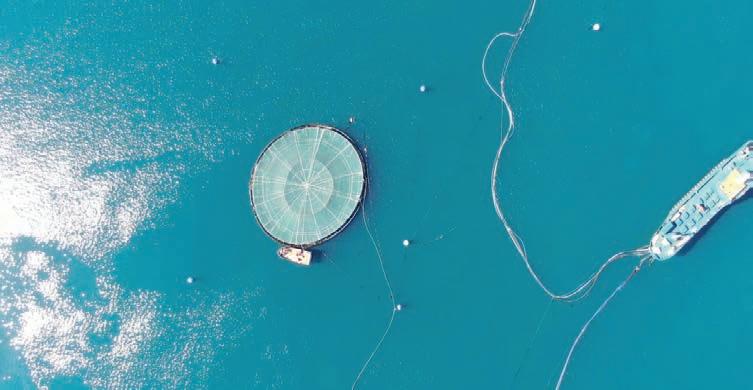
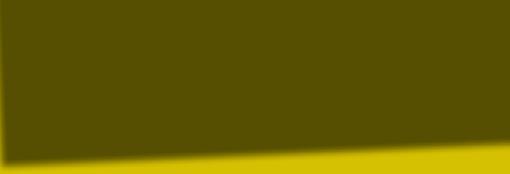
Opposite from top: EcoSea’s submersible 40m cage; Collec� ng the nets Top: The 40m submersible cage Above: The copper cage Above right: Net recycling are largely present in the photic layer (the fi rst six metres).
Castillo adds: “EcoSea’s technology applies to any fi sh species production. Regarding the depth, the pen can be placed as deep as necessary depending on the ocean conditions of that particular site (for each installation a full site assessment is needed, including bathymetric, oceanographic, and oxygen content information). Specifi cally for salmon, it is possible to supply air while the cages are submerged, or surface the cages and let the fi sh to replenish air in the swim bladder. It is basically an operational decision from the fi sh farmer.”
The prototype test was completed at Invermar’s Traiguén 2 farming centre, located in Achao, Chile. It involved a 40-metre-diameter submersible cage, more than 12 metres deep, with a capacity of 18,400m3. In September 2019 it was stocked with 50,000 smolts of Atlantic salmon.
“The main benefi ts were low fi sh stress (no predator attacks or escapes); high growth rates; and an 18% drop in production costs,” EcoSea says.
“When comparing the performance of the EcoSea submersible cages versus the traditional nylon cages, it was demonstrated that the salmon versus the traditional nylon cages, it was demonstrated that the salmon grow at a better rate, because although in both cases, similar-sized fi sh grow at a better rate, because although in both cases, similar-sized fi sh were obtained, the prototype was stocked two months later and with were obtained, the prototype was stocked two months later and with 47.5% smaller salmon; it also had a 2% lower mortality rate and it is estimated that it avoided the emission of 27 tonnes of CO2.”
“The production cycle with the submersible cage raft showed rapid growth development, low bacterial and parasite loads (Caligus), and zero losses due to sea lion attacks. From the operational point of view, the technology is very friendly, safe and effi cient, with very low fouling adhesion, thus validating a robust and reliable aquaculture system,” says Omar Cheuquepil, Head of Production at Invermar, which is also part of the project.
Castillo concludes: “This product is commercially available, currently operating in Chile and Japan. Now we are working to deploy in China, Australia, New Zealand and the UK, as well.
“Since the beginning in 2007, we have been focused on changing aquaculture for the better, reducing its environmental impact and maximising animal wellbeing, both goals inside and outside of our cages. It is for this reason that over more than 10 years we have proven our technology in different locations in the world, under all kinds of conditions and with different fi sh species.
“Through that process, we have also proven the improvement of the fi sh farming process and its reduction of the carbon footprint. In addition to that, we have successfully proven the recyclability of our cages, which after 10-plus years of continuous operation (time in which no debris or nylon netting waste is produced) are repurposed to produce new cages.” FF
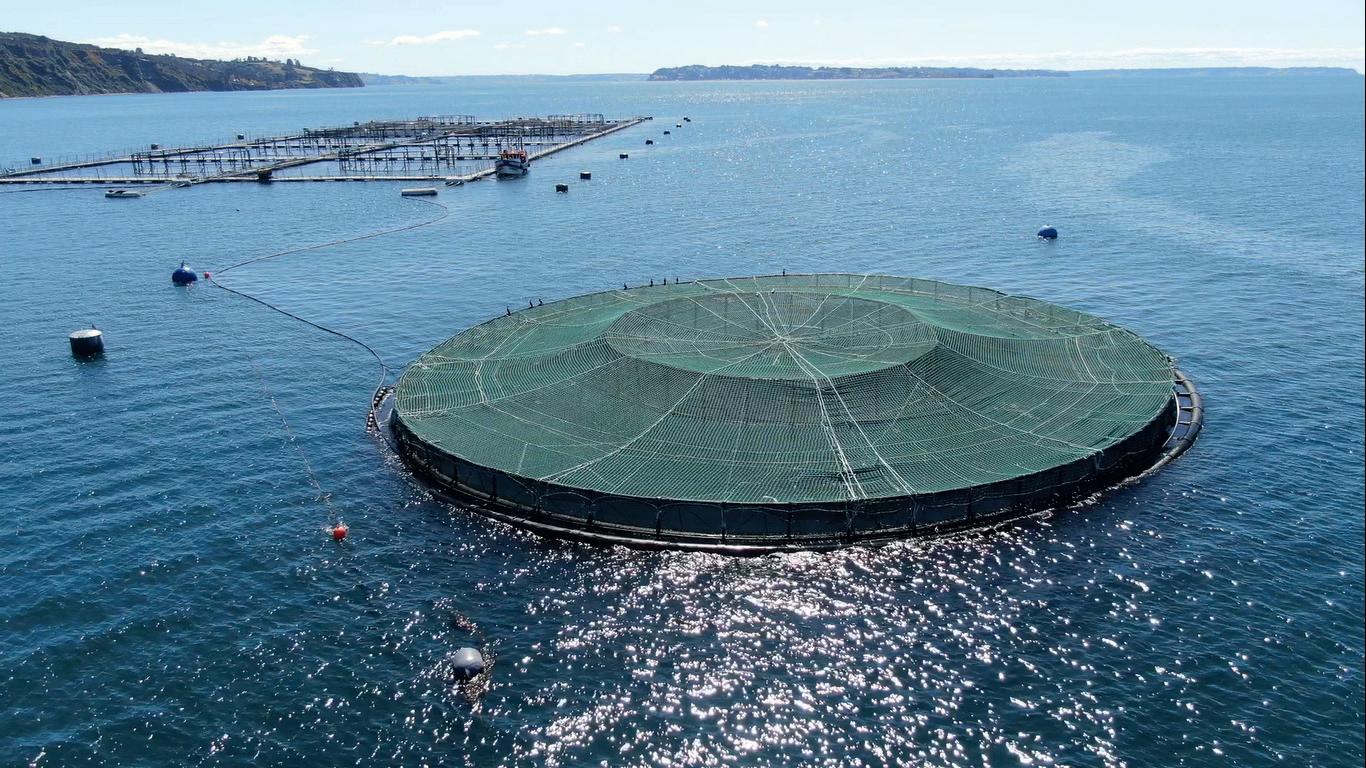
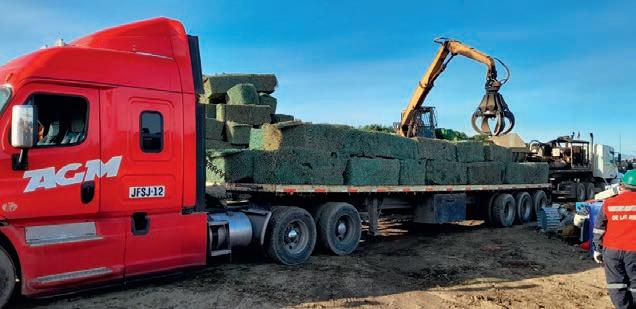
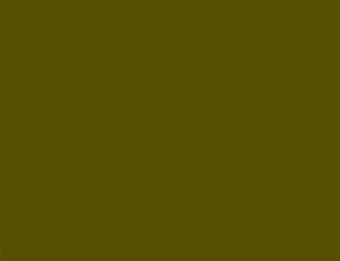

