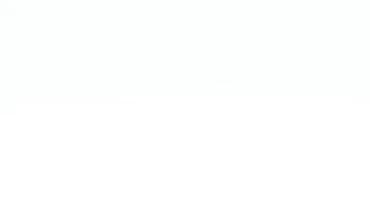
5 minute read
From RAS to pens at sea
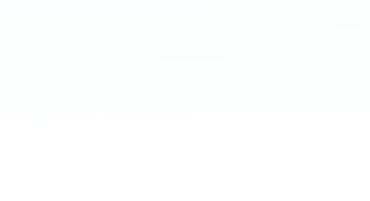
Land
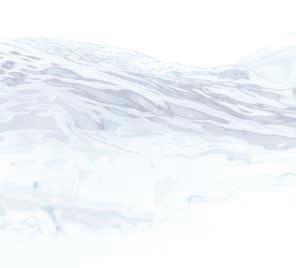
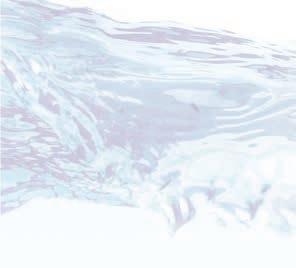
and sea
Fish health in a pen or a landbased farm is dependent on good water treatment
Earlier this year, aquaculture technology specialist AKVA started work on its biggest ever contract – a massive land-based salmon farm Ningbo, near Shanghai.
AKVA is building the recircula� ng aquaculture system (RAS) for Nordic Aqua Partners, which will be running the facility. It is planned to produce 8,000 tonnes of salmon in 2026 and the fi rst phase alone will have a 4,000 tonne capacity.
Ningbo is not the only large RAS project currently under way. For example, in April it was announced that Sande Se� efi sk had signed a deal with water treatment specialists Sterner AS, for the RAS for a large smolt and post-smolt plant in Gloppen, south-west Norway.
Meanwhile, Israel’s AquaMaof Aquaculture Technologies is helping to build a massive landbased farm for Proximar Seafood near Mount Fuji, Japan.
While some land-based farms use a fl ow through system, these larger projects all use some form of RAS.
Jacob Bregnballe, Sales Director, Land Based Salmon Projects with AKVA Group, explains: “Flow through works well only in certain loca� ons. In some sites in Iceland, for example, there is rela� vely warm, clean water which can be used for fl ow through, and also some parts of Norway.
“I know the headaches you get with fl ow through – it’s a pain if the water is not perfect. Few places have clean water all year round and a storm can mean you get weeds and mud.”
“We go for clean water technology because salmon live in clean rivers.”
The classic RAS setup includes a mechanical fi lter, a biofi lter which removes ammonia and a degassing process, removing CO2 which is also excreted and is harmful to the fi sh, before the water is returned to the tanks. It’s a constant process and down� me while fi sh are in the tanks would be hazardous.
Bregnballe says that AKVA prefers to use biofi lters using fi xed-bed technology, in contrast to a moving-bed setup, in which the biofi lters move in the water. The fi xed-bed approach is preferred because this way the biofi lter can remove micro-par� cles in the water as well as its main func� on, nitrifi ca� on (conver� ng ammonia excreted by the fi sh into nitrites, which are not harmful).
He adds: “Micro-par� cles are a hazard to the fi sh because they can get into the gill fi laments.”
AKVA also uses an ozone process to safely disinfect the water and this
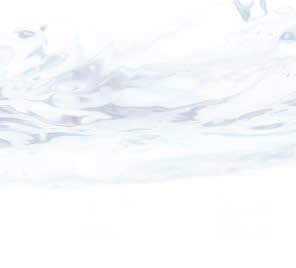
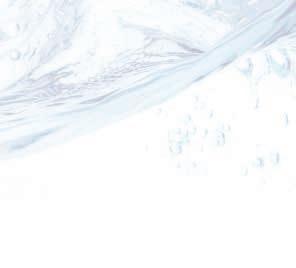
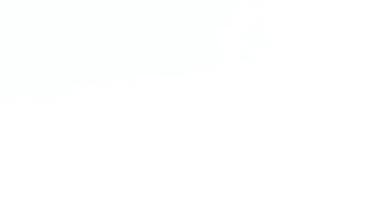
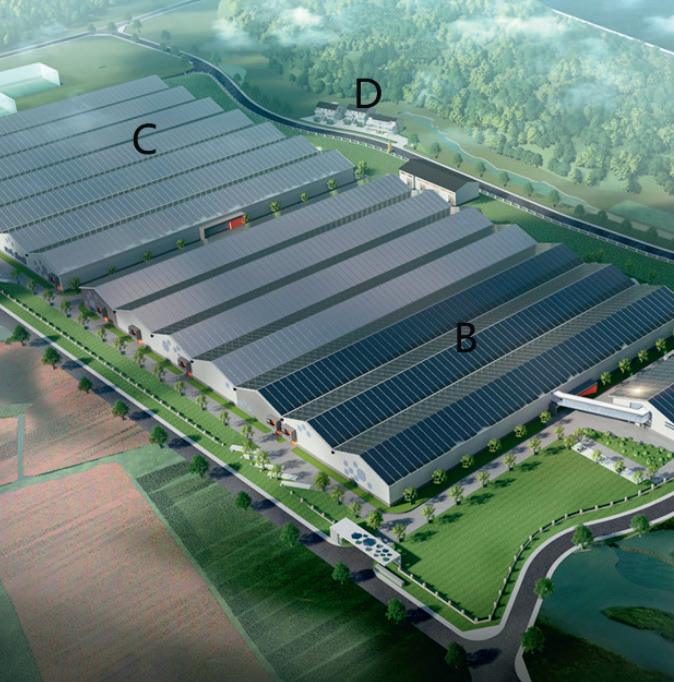
Above: The land-based salmon farm Ningbo Below: Cameron Kerr with compressor

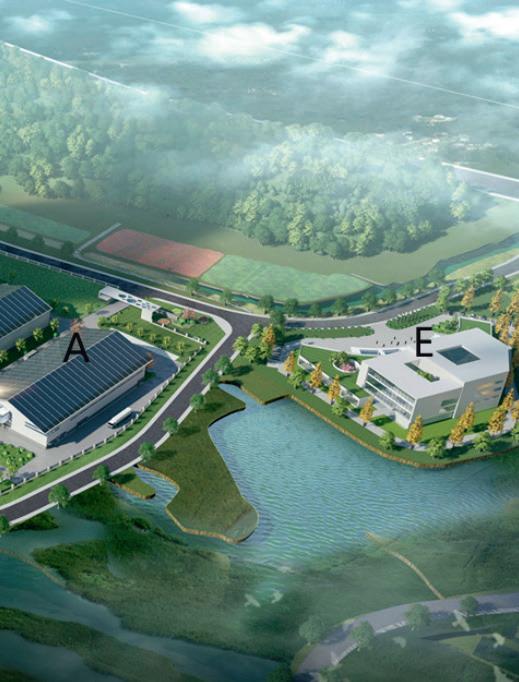
also helps to coagulate any remaining micro-par� cles into large clumps.
AKVA is not the only company with RAS experience – others that come to mind include Alvestad Marin, Evoqua and Kruger Kaldnes, to name just a few. The next few years will provide lessons as what works well and what does not.
Meanwhile, although a pen at sea does not require recircula� on technology in the same way as a land-based farm, even seawater needs treatment from � me to � me. When dissolved oxygen levels drop this can be very dangerous for the fi sh.
In order to counter this, operators can either directly oxygenate the water or use aera� on, pumping up oxygen-rich water from the depths into the pen. The la� er also has the advantage that it creates water pressure, keeping out harmful algal blooms, jellyfi sh and sea lice larvae. Farmers also use bubble curtains to keep jellyfi sh out of the pens.
Operators of fi sh farms, whether onshore or off shore, depend on a reliable, quality supply of low pressure air and compressed air for a
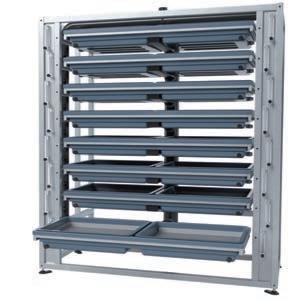
variety of equipment, systems and processes.
As Adrian Feiler, Business Development Manager - Aquaculture for KAESER Kompressoren explains, “A range of reliable KAESER air products are specifi cally designed and built to provide maximum durability in Aquaculture environments and ensure maximum process reliability. They are built to last in tough condi� ons and protected against water, and designed to be easy for the customers to use”.
And the condi� ons out at sea really are tough. As Feiler puts it: “If you want to break something, give it to an aquaculturalist!”
Reliability is key and that requires on the spot maintenance – which is where Kerr Compressor Engineers, the sole Sco� sh Authorised Distributor of KAESER HPC air products and an established and experienced supplier to the Sco� sh aquaculture community, comes in.
Cameron Kerr, Director, Kerr Compressors, says: “Aquaculture was a rela� vely new industry for us just 10 years ago, however, through the increasing use of technology by the industry, much of which relies on the use of compressed air and low-pressure air, it has become our largest single sector in the past few years.”
Reliability is key and that requires on the spot maintenance – which is where Kerr Compressors, a distributor for KAESER, comes in.
Cameron Kerr, Director , Kerr Compressors, says: “Aquaculture was a rela� vely new industry for us, but it has become our largest single sector in the past few years.”
He adds: “Maintenance is the key driver. Even having two, three or four hours set aside for planned maintenance can be diffi cult for the customer, so a breakdown would be an even bigger problem.”
Compressors can be diesel-powered or electric, but the former tend to suit aquaculture, as diesel generators are more robust and take up less space. Nonetheless, KAESER has a range of electric-powered e-compressors – which have a smaller carbon footprint and are quieter – and has sold around 50 to aquaculture clients in Chile recently. FF
NEW CompHatch® 2020
Market leading hatchery has been improved!
Hatching tray and EasyHatch substrate are molded together in one unit Less components for easier service and cleaning Replaced water tubes with channels to improve water distribution The water pipes have been replaced with built-in water channel
CompHatch 2020 is AutoTend Ready!
Compact trays are designed for integration with AutoTend, automatic egg and fry tending robot. WATCH THE VIDEO!
See AutoTend in action at
alvestad.com/en/produkter/autotend/
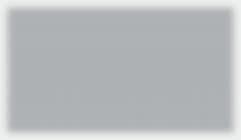
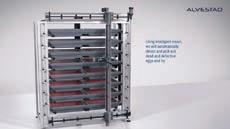