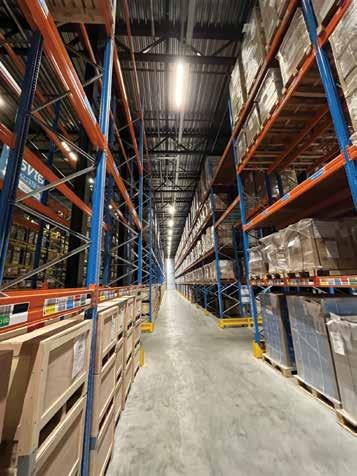
3 minute read
COMMENT
Awards process throws up the interdependence of Irish Businesses
‘From Where I’m Sitting’ Howard Knott – howard@fleet.ie
within the last week or two I have had the privilege of being part of judging panels in two major series of awards. Firstly, those being presented by the Irish Exporters Association and then the series hosted by Fleet Transport Awards. Before then, in late Spring I was part of the panel for the wexford Chamber Awards, one of the earliest such competitions to emerge following the COVID-19 lockdown.
Each of the awards processes operate in a similar fashion with the contenders submitting detailed entries for their chosen categories. From these, shortlists are drawn up, and the companies selected are interviewed by an expert panel. Inevitably, a few companies will make the shortlists on a regular basis and their progression can be easily monitored, but this year, because of the COVID-19 disruption both to the awards and, more importantly, to their own business, every company appeared to be new and there was a strong sense of excitement and respect on the part of the panelists for what was being achieved. Many of the interviewees had to surmount the additional challenge of being quizzed on virtual platforms which, despite the huge improvement in the overall Wi-Fi network, often had its technical challenges leading, in some cases, to the interviews being shorter than anyone would have liked. Driving away from the last interview series I began to think about just how integrated Irish business is and to recall something that I had heard many years ago, that every manufacturing job in Ireland generates another one to service the production and distribution of same being made. It’s clear that manufacturing is built on bringing together a collection of components and assembling them to make something that will fulfil a particular need. That need may well be to be a component in a further manufacture or could be the final thing which will provide a service to its purchaser.
Just how complex this can be is, perhaps, best illustrated by looking at the case of a goods handling equipment manufacturer. The company must first identify the need for the proposed product, who will buy it and at what price, then design it, specify what components are needed to make it, price, and source these, before even thinking about opening production. No single company will have the competences to do all these things so, quite quickly, the services and sub-supplier lists grow. But as the machine leaves the plant that’s far from the end of the matter, there’s a whole supply chain story in getting it to the purchaser and the requirement for a after sales service that will encourage that customer to buy further product from the Irish company. One Irish manufacturer of such equipment spoke about the need for the components and construction of the equipment that is supplied to be as simple as possible so that repair and maintenance can be done in remote locations. Indeed, this remote aftercare was a recurring theme in the interviews as firms learnt how to solve issues online, either using enabling software or simply showing locally technicians how to carry out the service with videos and phones. One aspect of this whole process that previously escaped me was the need for manufacturers to protect their design patents to ensure that their products are not copied, and their market undermined.
While the transport, warehousing, component, packing and other supplies companies had always had a good knowledge and keen awareness of the importance of Supply Chains, it was clear throughout the interviews with manufacturers that, since the 2019 conversations, Supply Chain had moved very far up the management priority list. It always amazed me in previous years how relaxed manufacturers, re-sellers and distributers were about the supply chain for their goods and how prevalent was the notion that ‘our forwarder looks after that’. Since 2019 COVID, Brexit and the Russian invasion of Ukraine have happened and, with these have come serious problems that totally undermine the less alert business. Supply Chain Management is, at least, being seen as crucial to business survival.
For the other panelists and I, carrying out the various awards interviews was a great experience. We really appreciated the commitment of everyone that took part.