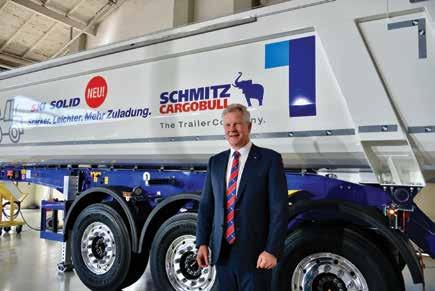
6 minute read
traILEr I
Schmitz Cargobull Tipper Plant Visit at Gotha - More Cargo - Less Bull!
To celebrate twenty-five years of making trailers at its Gotha site, and as a sneak preview of exhibits planned for September’s IAA Transportation in Hannover, Schmitz Cargobull (SCB) hosted a press event to reveal some of its most recent innovations.
Today, the 735 employees at the Gotha plant - which interestingly has been a fabrication workshop in some form since 1883 - only produce Schmitz Cargobull’s tipper models. However, there are over 9,000 variants of tipping trailers available. For the year 2021/22 Schmitz Cargobull Gotha produced 5,360 units, meaning that every 30 minutes a new load carrier was completed. The company has won many awards, including recently winning all three ‘Best Brand Awards’ for its tipping, dry freight and refrigerated trailers.
Over 70 trucks a day deliver the raw materials and components needed to SCB Gotha. The trailers are fabricated using the latest technology, including laser and high-pressure water cutting, to produce trailers to any customer’s specification in one of over 600 colour 10.5 metres. These are mounted on any of the 32 chassis variants from Schmitz Cargobull’s light, heavy and special duty range, with either two, three or four axle configurations. Other options include insulation and an internal plastic liner for the body. While the plastic liner does add a small amount of weight it greatly reduces the potential for damage, a help when tipping certain products. It can also be easily transferred between trailers or bodies.
All trailers are tested on the tipping test rig at Gotha which can replicate the stresses exerted on trailer chassis and components when tipping, including twisting stress on the chassis and the pressures exerted on the rear door during operation. Brakes and safety systems are also tested using SCB’s special brake test rig developed to simulate all manner of braking events. Lead times for build are generally around seven days for standard models, and SCB only builds to order and does not build to stock. Currently, over 90% of trailers are being specified with SCB axles, although the company has for the moment stopped fitting its own brand tyres. The multi-award-winning company which operates other production facilities in Lithuania, Turkey, Spain and the UK, continues to maintain its position as the leading trailer manufacturer in Europe with a 25% market share. Nevertheless, SCB’s Chief Executive Officer Andreas Schmitz did report a loss of €15.1 million for the last financial year. One primary reason for this was that in 2020 demand in the European trailer market crashed to just 200,000 units. In his address Schmitz also referenced the current uncertain trading conditions, alluding to one difficult decision the company has taken - “We will not be servicing the Russian market

anymore, even though this has been a huge dent for us, especially for the Lithuanian plant,” he said, noting that Russia accounted for around 15% to 20% of the European trailer market.
Worryingly Mr. Schmitz added: “Increases in the costs of energy and raw materials, which combined amount to 33.6%, will be passed on to our customers.” Director of Sales at SCB Boris Billich continued by saying: “We see dramatic change from month to month which is seriously interrupting our customers’ plans, and it would seem we will have to live with this for some time. For some products we have seen increases of 35% in 12 months.”
The company is confident that revenues will return in time and SCB is well positioned for the future trading environment. This is viewed as a time to invest in new technology and the company continues to develop new and important innovations. This includes the registering of between 20 to 30 patents
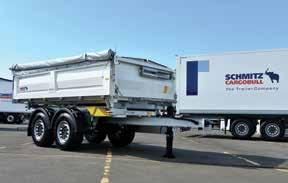
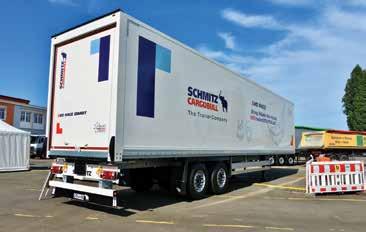
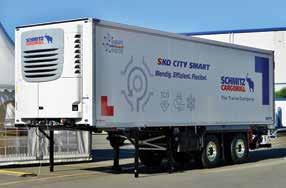
every year. Some of these patents have been realised in the new products displayed at Gotha. This includes a completely new tipping semi-trailer the S.KI Solid. The new tipper features a remote-controlled rear bumper lifting system and comes with a significant weight reduction of 280 kgs.
In addition to the new S.KI tipper, SCB also revealed a new range of multi-temp, multi-compartment ’S.KO City-Trailers designed to meet the increasing demand for urban deliveries. These trailers are different for every customer and SCB can easily meet a vast array of individual requirements for loading, unloading and load restraining. The city trailers are primarily used for temperature-controlled products and here SCB is forging ahead with several innovative solutions.
These innovations include software updates to trailers to reduce fuel consumption and improve monitoring systems to minimise downtime. The updates can now be installed wirelessly using the SCB TrailerConnect telematics programme delivered over the regular
GPS and GSM networks. The company sees a great future in the world of telematics and expects to see demand rise from the current 69,000 units to 250,000 by 2025 and reach 1 million by 2030. TrailerConnect is available in 29 different languages and is a powerful tool for the transport operator. In addition, customers can be allowed access to the system, although only when granted permission which can be restricted to whatever information the operator dictates. Katrina Herde of SCB’s Data Management Centre assures that: “Nobody who is not authorised will get access.” She continued: “TrailerConnect works very simply on a plug and play format and is fully compatible with all other systems that a company may already be using.”
Other innovations shown included the drag-reducing Eco-Flex trailer. The roof section of SCB’s Eco-Flex can be easily adjusted to raise or lower the height of the trailer by 50 centimetres to deliver a tapered sloping rear section. This can create an almost teardrop effect when the opportunity arises, and if the maximum load capacity is needed then the roof section can be returned to its normal full height. SCB is confident that this will deliver a strong 5% saving in drag, although in their field trials some customers reported as much as a 10% saving. Eco-Flex also highlighted some more simple and practical innovations, including a set of rear side skirts which, once opened, reveal a very useful trailer-width pull-out storage bin where all manner of equipment can be safely contained. On the subject of safety and security, SCB has been working to develop and improve security systems for drivers and the loads they carry. While focusing on preventing theft of goods, SCB is also targeting deterring entry by stowaways. The company is keen to highlight that both its physical and electronic security systems are fully compliant with the ‘Transported Asset Protection Association (TAPA) standards.
Equally, SCB’s new fully electric fridge unit will generate interest. The 30 kW battery is powered from the mid-axle of the tri-axle trailer and will last about 4 to 5 hours on a full charge when the trailer is stopped. The unit is PIEK Certified for noise levels. On the subject of certification, it is worth noting that under the transport of perishable goods agreement (ATP), all electrically powered temperature-controlled trailers must now show the designation ‘FRCx’ in addition to the month and year of certification expiry.
Of course, the topic of care for the environment was prevalent throughout the event. SCB, like so many manufac-
turers, takes its responsibilities seriously. Andreas Schmitz was more than pleased to announce that the Spanish production plant is now self-sufficient using only solar power. Schmitz also believes that a move towards larger or different combinations of vehicles is the quickest way to reduce CO2 in road transport, and cites the 25% reduction in CO2 delivered by the Schmitz Eco-Duo trailer combination.
Despite the difficulties of the last two years, it would appear that Schmitz Cargobull will continue to dominate the European trailer market for the foreseeable future.
Text & Photos: Paul White – paul@fleet.ie
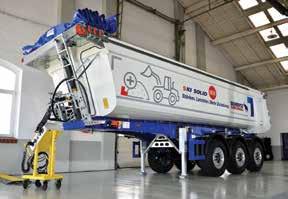
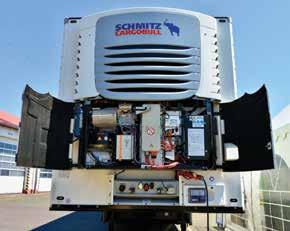