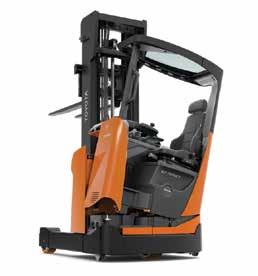
8 minute read
LAUNCH PAD
Toyota Material Handling Europe has launched the first three models in the new BT Reflex family of reach trucks. The latest models – the high-performance R-series, the E-series (which features Toyota’s iconic and unique tilting cab) and the flexible O-series for inside and outside use - set new standards in safety, efficiency and ergonomics.
The trucks, which are offered with load capacities of between 1.4 and 2.5 tonnes and lift heights of up to 13 metres, feature a host of innovations - including an updated ergonomic operator compartment that optimises safety, performance levels and operator comfort.
Within the operator’s cabin the steering unit with palm support has been refined for enhanced touch sensitivity and feel. Also, a new main control console, positioned to the right-hand side of the driver, helps to make the new BT Reflex models highly intuitive to control - which results in improved throughput speeds and safer working.
Another notable addition within the operator’s area is a new large colour touchscreen display which provides a clear view of critical information and direct access to the truck’s programmable features and functions. Like the main controls, the touchscreen has been designed with ease of operation in mind and its instinctive and interactive functionality guarantees a high level of efficiency.
Of course, driver comfort has not been forgotten and all the new models have the option of a high-quality air suspension seat.
With environmental issues a key design consideration, every model is lithium-ion ready and comes with a choice of three intelligent energy solutions to suit every customer’s application requirements. These solutions are based on Toyota’s own modular lithium-ion battery system and deliver a high degree of operational flexibility. With good charging discipline, even the smallest option will provide the consistent power levels required to allow the trucks to work around the clock – even within the most demanding environments.
All reach trucks from Toyota are connected smart trucks. Factory-fitted with integrated telematics, they are easy to connect with Toyota’s I_Site fleet management tool. I_Site allows users to measure truck safety and performance and achieve considerable savings in their fleet’s overall running costs.
For the new machines the driver interface has also been improved, with the availability of I_Site features such as Smart Access - which allows only authorised operators to start a truck. In addition a Pre-Operational Check tool makes sure that an automated check is carried out by the driver before the beginning of every shift or day.
Toyota has been at the forefront of class-leading reach truck design for over 25 years, during which time the company has brought such innovative features as the iconic tilting cab, transitional lift control and 360° steering to the market.
The latest additions to the BT Reflex range continue the company’s proud history of reach truck innovation, as José María Gener, Vice President Sales & Marketing, Toyota Material Handling Europe, explains: “Providing businesses with high-quality, cost-effective and safe ways to power material handling equipment is of foremost importance, while keeping the environmental impact to a minimum. With these new products, we are reaching new levels in terms of safety, ergonomics and energy efficiency and we will continue to focus on bringing customers sustainable and efficient material handling solutions in the future.”
new reach truck models from toyota optimise safety and performance levels
Safety Storage Efficiency Safety Storage Efficiency
Whether you handle lawn & garden supplies, building supplies, palletized goods, engineered floor, wall and roof structural Manage your warehouse logistics more safely and more productively using less space with components, Combilift has the solution Aisle Master. with guaranteed improved storage capacity, safer product handling and increased productivity. • Safer product handling • Optimised production space • Improved storage capacity • Increased productivity & output • combilift.comEnhanced profits
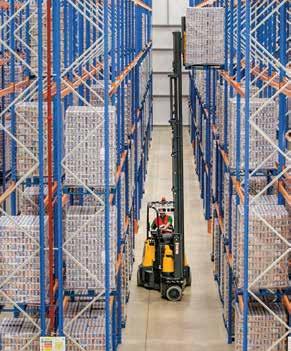
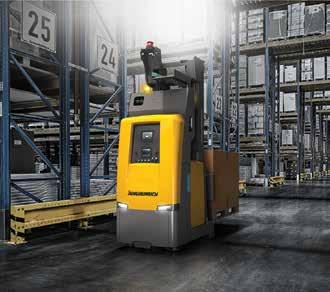
Jungheinrich presented its newest automated guided vehicle (AGV) at its recent virtual trade press INNOVATIONS & HIGHLIGHTS 2021 conference. The new EKS 215a can independently store loads weighing 700 kilograms at a height of up to six metres and is therefore the ideal solution for the automation of high lift deployment.
the eKs 215a - innovative automated high lift solution from Jungheinrich
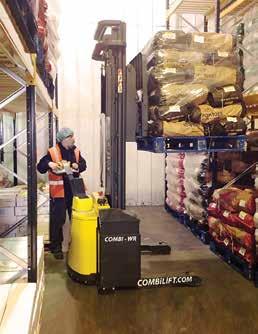
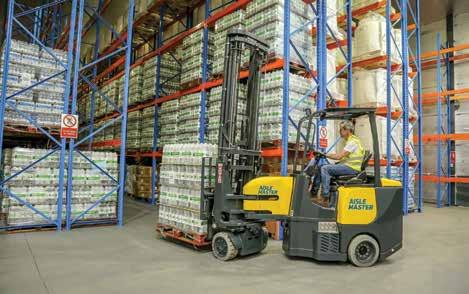
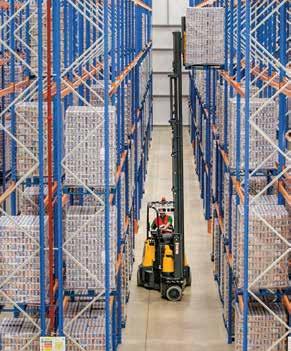
The truck is based on a completely new and especially compact AGV chassis and Jungheinrich has also succeeded in reducing the virtual footprint of the EKS 215a significantly thanks to its new protective field concept. This enables the integration of the truck into existing warehouse layouts. Manual processes can be automated with the new EKS 215a that are currently mainly still carried out with counterbalance and reach trucks. A completely new human-machine interface ensures the particularly intuitive operation of the truck.
“The new EKS 215a is Jungheinrich’s response to numerous customer requests relating to space requirements and possible uses. The truck is more compact, powerful and user-friendly than all before it,” explained Manuela Schmidbauer, product manager responsible for the new EKS 215a at Jungheinrich. “With a residual load capacity that is 40 percent higher than the previous truck, it is the ideal AGV for automating in-house transport and the storage of pallets in wide aisles.”
A special innovation in the new EKS 215a is its new AGV chassis with its extra compact dimensions. Security scanners are installed below the truck floor to prevent them from being damaged and to save space. At 131 millimetres in length and 85 millimetres in width, Jungheinrich has managed to reduce the physical floor space in the EKS 215a. Nine mast types enable individual solutions for each application and the self-supporting forks increase the versatility when it comes to handling.
The new EKS 215a uses 24-volt technology rather than 48-volt. This results in an energy cost saving of up to 30 percent. Charging processes are automated. A new human-machine interface with touch display offers additional options for interaction between the operator and AGV. The status of the new EKS 215a can be seen immediately at a single glance. In the event of faults, the truck offers a problem description in plain text and additional specific recommendations for action which also enables errors that could previously only be solved by a service technician to be eliminated easily. The human-machine interface may also be used to define or start manual driving orders, which was previously only possible centrally via the control station.
“Jungheinrich offers its customers an extensive and customised solution with its long-standing expertise in automated intralogistics,” added Ms. Schmidbauer. Despite all the new features and although the AGV was developed specifically on the basis of customer requirements, the new EKS 215a is made up of over 90 percent proven Jungheinrich standard components.
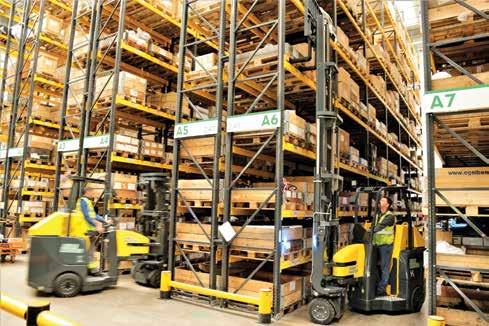
Anyone exploring the subject of returning the best possible results from a warehouse will soon discover how the right choice of forklift, combined with the ideal warehouse layout, are essential factors.
With advice from Aisle-Master, these topics are explored and explained further:-
Why? Simply because the perfect combination of both forklift and layout means maximising warehouse capacity, reducing damage to goods, faster transfer of items from storage to onward transport and – most of all – a workforce who have the right tools and set-up to work at their best.
As part of its broad customer service levels, Aisle-Master, through its sister brand Combilift, provides a warehouse design package that can enable up to 50% extra warehouse capacity through a specialist layout.
How important are forklifts to warehouse efficiency?
Using articulated forklifts in a warehouse increases storage and reduces aisle depth while enhancing efficiency. In particular, electric forklifts are particularly popular in warehouses as they help reduce emissions and lower the company’s carbon footprint.
An electric forklift can be utilised across 2-shifts operation by having a spare battery that is easily interchangeable, thus reducing downtime.
How wide are warehouse aisles for forklift use?
This varies on the brand of forklift and depth of load. But a standard counterbalance requires a 4m to 5m aisle, decreasing to a 3m to 3.5m aisle for a reach stalker. But an articulated forklift, for example an Aisle Master very narrow aisle forklift, reduces this to just 1.6m.
How wide should a drive pattern be for driving a forklift in a warehouse? This will depend on the depth of the load but with an articulated forklift the intersecting aisle would be 2.7m.
What is the best way to control forklift damage in a warehouse?
Using safe, ergonomically-designed forklifts will help reduce product damage. In addition, safety barriers could be added to enhance safety even further.
Is a forklift manual?
Most warehouse forklifts are electric as they are operating indoors with a simple forward and reverse motion – therefore no gears are required.
forklifts and the warehouse – essential, cost-saving Advice
How much does a forklift weigh?
This with depend on the brand of forklift and application the forklift would be working in, but typically if 4 tonnes are needed to be lifted, a 5 tonne forklift is required.
Creating Results from a warehouse – Proven method unlocks up to 50% increase
Would increased warehouse storage capacity mean better bottom line results for your business? Many businesses in Ireland, the UK and worldwide have been using a tried and tested method to drive savings in their warehouse operation by pairing:
1 A FREE FACILITY PLANNING
SERVICE:
Provided by the warehousing equipment specialist Combilift, a free review includes racking layout proposals and storage density calculations to create the best possible performance from any warehouse.
2 THE AISLE MASTER VERY
NARROW AISLES ARTICULATED
FORKLIFT:
An ability to work in aisles as narrow as 1.6m and 15m tall means a single multi-purpose truck and faster ‘truck to rack’ operations.