
4 minute read
Safety Storage Efficiency
Enhance the Safety, Capacity and Efficiency of Your Storage
Combilift products help customers increase storage without the need to expand the size of their facility.
Understanding the available space and how it is being used is critical to running a more sustainable and profitable business.
Contact Us Today
To find out how Combilift can help you safely and efficiently load containers combilift.com

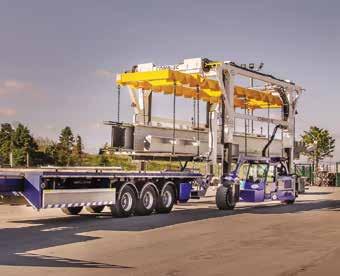
r etur N of face-to face eve N ts
The year also saw the resumption of the IMHX show in Birmingham, the first face-to-face event held under the guidance of the UKMHA, which was formed following the merger of the British Industrial Truck Association (BITA) and the Forklift Truck Association (FLTA).
Supply chain challenges were high on the agenda at LogiMAT 2022 which attracted exhibitors from 39 countries at the Stuttgart showgrounds. The war in Ukraine and the sanctions imposed on Russia caused a shortage in global steel supply which resulted in significant price increases, however, this appears to have stabilised in recent months.
In June, intralogistics specialist Linde Material Handling presented its extensive portfolio of products and solutions at an event for customers and dealers from around the world at its World of Material Handling (WoMH) event in Mannheim, Germany.
a id for u krai N e
In addition to the economic sanctions imposed by governments on Russia in response to its attack on Ukraine, forklift makers rallied in support of relief initiatives. Combilift teamed up with the Ukrainian Red Cross Society, making an initial contribution of €50,000 to aid the supply of relief to the displaced civilians. JCB offered housing to 70 refugees, while KION donated €1 million to the German Red Cross.
Joe O’Brien - contributor@fleet.ie
Ornua Foods is Ireland’s largest dairy products business, exporting to 110 countries worldwide. Headquartered in Dublin, and previously known as the Irish Dairy Board, it has annual sales of over €2.5 billion, 15 global subsidiaries, and a global team of some 3,000 employees. Ornua operates from 10 business units globally, including 16 production facilities. Its brands include Kerrygold, Dubliner, Pilgrims Choice, Adam’s, Horlicks Farms, Forto, and BEO.
Ornua Foods owns and holds large stocks of butter, cheese and milk powders. Before the upgrade, it used over 80 refrigerated storage locations
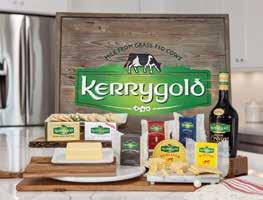
Freshness is key for Ornua’s dairy produce, and the storage and distribution methods are dictated by the original production date of each item. This means that it is essential that the business has full, real-time visibility of all of its product stock and locations.
Oruna required each warehouse to get automatic access to the Movex ERP system so that instructions and reports could be exchanged instantly and in real-time.
It selected In-DEX WMS (Warehouse Management Software) provided by Irish IT business Principal Logistics Technologies.
Since the cold stores came online, real-time stock information has become available for the entire company, reducing data input and improving product traceability throughout the supply chain.
“As far as we are concerned, they did an excellent job in a very short timescale,” explained Kevin Woods, business analyst, Irish Dairy Board/Ornua. “The warehouses using In-DEX were very easily and smoothly integrated into our Movex ERP system. After the first short period of testing and familiarisation there have simply been no software issues.” across Europe. Sales orders and stock movements were fully controlled from head office, with direct instructions being sent, at any time, to the various sites holding stock on its behalf. There would be about 7,000 pallet movements per day.
Any transaction queries or discrepancies are flagged straight away, with no extra data input by the stores.

The In-DEX WMS also provides an error-reducing feature. It is no longer possible to despatch the wrong pallet because orders feed directly through to the pick list.

Warehouse and logistics partner feedback also confirmed that average truck turnaround times were reduced because the relevant loading data is usually on the In-DEX WMS system in the warehouse before a truck has even arrived.
Paper based records and lists have been eliminated across the supply chain. Payments are faster or automated, with discrepancies flagged immediately. Errors have been reduced and truck turnaround times are faster.
Eoin Hennessy is Managing Director of one of Oruna’s facilities, Orchard Warehousing & Cold Storage in Cork. He describes the significance of the change: “No paper, no emails, the whole operation is streamlined. Errors are almost eliminated compared to the tedious chore of transcribing information from masses of documents, which in fact was a bit of a nightmare at peak periods. We hold up to 6,000 pallets at any time, with maybe 200 or so moving in or out daily. So the automated links between the Irish Dairy Board [Oruna] and our In-DEX system, which in turn is integrated with our Sage Line 50 ERP, have significantly reduced the clerical working hours needed.”
Text: Johanna Parsons - contributor@fleet.ie cancelled, was the buzz word of 2020, ‘21 and even at the beginning of ‘22. yet test camp intralogistics attracted an attendance of almost 1,000 participants in the middle of a lockdown, how did you manage that? how was the response to your trade show?
While the corona pandemic forced many organisers to cancel trade fairs and congresses in the past two years, the International Forklift & Interlogistics Awards (IFOY) Test Camp Intralogistics continued to develop and evolve. For the 2023 programme the event is going to be all about testing, trying out, driving and experiencing live when it opens its doors at Messe Dortmund from 29-30 March 29. Up to 100 selected innovations and new products from ten countries will be available for self-testing on 10,000 square meters of hall space.
“Don’t call it a trade fair,” stated Anita Würmser, Managing Director of Test Camp Intralogistics, and Jury Chairwoman of the IFOY Awards and the Logistics Hall of Fame, in an interview with Handling Network.
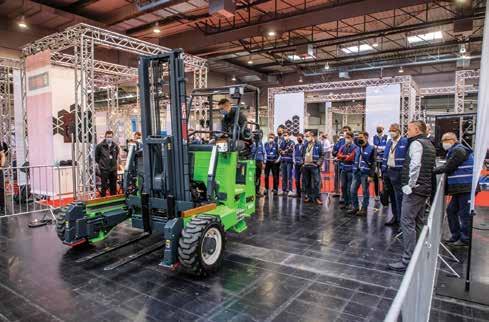
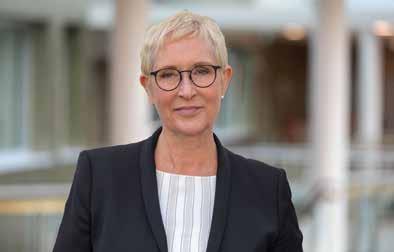
I have been asked that countless times. We just did it. In a nutshell, it was 200% work, 100% courage, 0% planning security. The authorities were tough but helpful, the regulatory requirements gigantic, not to mention the risk. In the end, the momentum was the courage of everyone involved. Guests, exhibitors, testers, team, judges - they all came to test and feel the innovations and keep the business going. And everyone followed the rules accurately. It was a bit scary, though, when we were in the middle of the lockdown in 2021 with 650 people all alone in the hotel and on the exhibition grounds.