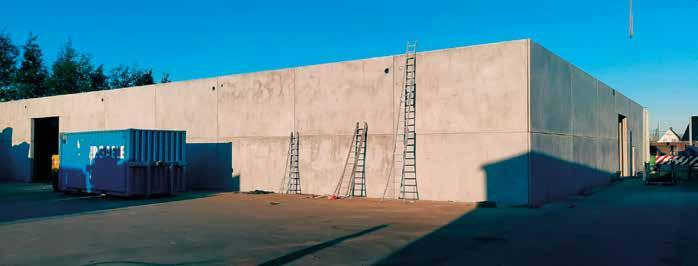
6 minute read
Visite d'entreprise Remmery (B
LE SPÉCIALISTE DES PARQUETS EN CHÊNE MASSIFS ET CONTRECOLLÉS EST ACTIF DANS LE SECTEUR DU BOIS DEPUIS PLUS DE 60 ANS
À Pittem, dans les environs de Bruges (B), la Parqueterie Remmery constitue une valeur sûre depuis déjà des décennies. Créée dans les années ‘50, Remmery est toujours restée une entreprise familiale. Aujourd'hui, elle se concentre principalement sur la production de parquets en chêne massifs et contrecollés.
Advertisement
Au début, les planchers en bois ne constituaient pas son premier centre d’intérêt. Lorsque le grand-père Albert Remmery a démarré son entreprise, il se concentrait principalement sur le sciage et dirigeait un négoce de bois. Ce n'est que dans les années ‘90, lorsque son fils Johan a commencé à produire des planchers, que l'entreprise a commencé à s’intéresser aux parquets. Une activité à laquelle les directeurs actuels que sont Stijn et Thijs, les fils de Johan, continuent de se dévouer pleinement. Une production entièrement en gestion propre
Ces dernières décennies, de nombreuses entreprises ont délégué au moins une partie de leur production à des tiers. Cela n’a toutefois jamais été le cas de la Parqueterie Remmery. Depuis le début, l’entreprise se charge de toute la production en interne. C'est ainsi qu'aujourd'hui toute la production s’effectue à Pittem.
60% à destination de l'étranger
Au cours de notre visite, nous avons rapidement constaté que l’entreprise lorgne bien au-delà de notre marché domestique. Avec les années, la Parqueterie Remmery s'est forgé une solide réputation en dehors de la Belgique et même de l'Europe, si bien qu'aujourd'hui, en 2021, plus de 60% de la production est destinée à l'étranger.
"Nous nous adressons principalement à des entreprises qui revendent nos produits. Il s’agit plus spécifiquement des grossistes et des négociants en matériaux de construction, ainsi que du marché du contract", explique Stijn Remmery. "La demande pour nos produits émane du monde entier, même des États-Unis et d'Australie. Pour servir ces clients, nous organisons nous-mêmes le transport par conteneurs. Nous disposons à cet effet sur notre site de notre propre quai de chargement." "Le poseur de parquet nous connaît assurément car, après tout, c'est lui-même qui pose nos revêtements de sols. Cela dit, d'autres groupes professionnels viennent également frapper à notre porte, en particulier des architectes qui viennent régulièrement nous voir lorsqu'ils veulent examiner les possibilités d’installer des revêtements de sol dans l'un de leurs projets. Nous nous mettons ensuite à table avec l'architecte et déterminons en concertation quel produit répondra le mieux aux besoins de ses clients."
"Nous produisons tout sur notre propre site à Pittem, d’une superficie de plus de 11.000 m²", explique Thijs Remmery, frère et codirecteur. "Tout commence par l'achat de bois de chêne fraîchement scié, que nous importons de France. Pour ce faire, nous faisons souvent appel à des scieries avec lesquelles mon grand-père a travaillé depuis ses premières années. Évidemment, nous nous rendons nous-mêmes régulièrement en France. C'est le seul moyen de pouvoir contrôler la qualité et garantir la continuité de l'approvisionnement."
À son arrivée à Pittem, le bois est traité dans les règles de l’art. Cela signifie notamment qu'il est séparé en fonction de sa destination finale.
"Le bois destiné à la production de parquets massifs est entreposé en extérieur sur la cour. Il y reste pendant 6 à 12 mois, afin d’être séché
par le vent", explique Stijn. "Le reste du bois, qui sera utilisé pour les parquets multicouches, est débité en lamelles de parement lorsqu'il est encore frais. Une fois scié, il est ensuite directement empilé par lots sur des lattes puis, à son tour, entreposé à l’extérieur. En raison de la faible épaisseur, le temps de séchage au vent est nettement plus court que pour le bois massif, et après quelques semaines seulement, les lamelles peuvent être introduites dans un de nos trois séchoirs, pour y être séchées artificiellement jusqu’à un taux d’humidité de 8 à 10%."
" Si nous avons choisi de débiter le bois fraîchement coupé, ce n’est pas pour rien. Vu que les lamelles sont débitées à partir de bois fraîchement coupé, il y a beaucoup moins de tension pendant le processus de séchage et nous évitons la formation de marques de séchage. Ce qui constitue indéniablement un énorme avantage par rapport aux entreprises qui ne disposent pas de leurs propres installations de séchage."
Le souci de l'environnement: une priorité
Au cours de notre conversation, il est apparu clairement que l’entreprise prend la problématique de l’environnement très au sérieux. Le séchage est par exemple neutre en CO2 et les séchoirs sont chauffés par une chaudière à biomasse de 1,1 MW.
Thijs: "Après le séchage, nous transformons le bois massif en planchers après une courte période de stabilisation. Les couches de parement doivent ici d'abord être calibrées à une épaisseur de 4 ou 6 mm sur des machines lourdes spécialisées. Elles sont ensuite collées sur un panneau en multiplex de bouleau hydrofuge, que nous importons nous-mêmes en direct de Russie. Lors de la transformation, nous rebouchons les nœuds et nous ponçons les planches, avant de les profiler au moyen de fraises diamantées à profil conique spécialement conçues à cet effet. Cela garantit une pose et un ajustement rapides. Si le client le souhaite, les lames de sol profilées peuvent être parachevées dans l'une de nos innombrables et uniques couleurs."
Nouveaux bâtiments et seconde presse à coller
Depuis que les petits-fils ont rejoint l'entreprise, Remmery a investi de façon colossale, tant dans les bâtiments de l'entreprise que dans les machines utilisées. Dans les prochains mois, les clients pourront constater que l'entreprise n'est pas restée inactive l’an dernier, que du contraire!
"Un exemple: juste avant le Nouvel An, nous avons construit un nouvel entrepôt, d'une superficie de pas moins de 1.500 m². Ce bâtiment sera utilisé pour l'encollage et la finition des parquets", explique Stijn. "Nous avons aussi acheté récemment une seconde presse à coller, qui sera livrée en mars. Cette presse à coller nous permettra d'augmenter notre capacité de production d'au moins 75 à 80%."
Installation pour la production de bois thermotraité
"Nous sommes également en train d'installer une ligne de production pour bois thermotraité. À cet effet, nous utiliserons du bois indigène, surtout du peuplier et du frêne, mais aussi du chêne de France. Après avoir subi ce traitement thermique, sans utilisation d’aucun additif chimique, le bois convient parfaitement pour être ensuite transformé en bardage de façade ou bois de terrasse. Autre point intéressant: le bois acquiert une couleur brun foncé chaude, jusqu'à cœur. Le ponçage ne pose par conséquent aucun problème, le bois conserve cette couleur."
"Ce qui est intéressant avec cette nouvelle ligne, c'est qu'elle offre un double avantage", conclut Thijs. "Elle nous permettra non seulement de proposer de nouveaux produits et de nous introduire sur de nouveaux marchés, mais aussi, en même temps, de fournir un service encore plus complet aux clients existants. Nous pensons ici, par exemple, aux architectes et aux applications de bardages de façade.”
"Nous prévoyons que cette installation sera pleinement opérationnelle d'ici avril de cette année. Nous communiquerons à nouveau sur celle-ci ultérieurement. Je voudrais également mentionner que nous allons également développer et proposer une nouvelle ligne de couleurs en 2021. Grâce à notre large gamme de produits, nous espérons ainsi séduire de nombreux clients existants et potentiels, tant au niveau international que local."
Plus d’infos via www.remmery.eu


