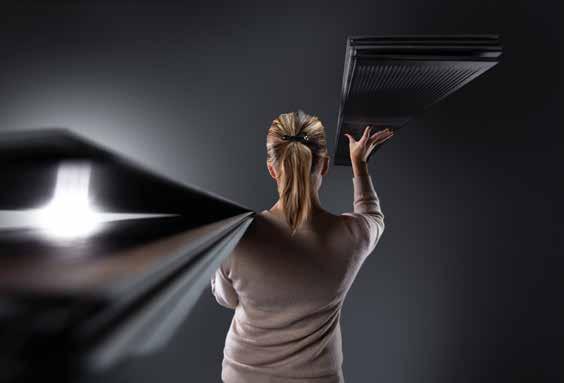
3 minute read
Dossier Ecologie en duurzaamheid
BEGIN BIJ DE BASIS
EEN BETERE WERELD START BIJ HET TOTAAL HERDENKEN VAN JE PRODUCT
Advertisement
Foto – Välinge
We worden al jaren om de oren geslagen met begrippen als duurzaamheid, circulair denken, hergebruik, milieubewustzijn, CO2-uitstoot, enzovoort. Het spreekt bijgevolg vanzelf dat bedrijven hier steeds meer aandacht aan besteden. Maar hoe pakken ze het aan op het gebied van ecologie, recyclage en transport? Dan merken we dat nogal wat van de ondernemingen beginnen bij het begin: ze leggen de eigen productie onder het vergrootglas en gaan na hoe er proactief kan gewerkt worden.
Tijdens onze zoektocht op de markt kwamen we uit bij een schoolvoorbeeld van dit ‘optimaal ecologisch denken van bij de bron’: Välinge Innovation. Dit in 1993 gestichte Zweedse bedrijf staat al heel lang bekend als een pionier als het gaat om technologische revoluties voor de vloerenmarkt en kan daarvoor rekenen op een bijzonder geavanceerd R&D-centrum.
Het herdenken van het eigen product is heel erg duidelijk bij de Liteback-technologie die het op de markt brengt, een technologie die door steeds meer licentiehouders gebruikt wordt. Onder Liteback wordt het eigen product van zoveel mogelijk kanten bekeken, zodat het nog voor het de fabriek verlaat zo duurzaam mogelijk geproduceerd én vervoerd wordt.
Verlaagd gewicht
Een eerste ingreep merken we bij iets wat zo voor de hand ligt dat velen het vergeten: het gewicht van het afgeleverde product. In het geval van Liteback gebruikt men daarom zogenaamde ‘core technology’ voor thermoplastische vloeren, zoals LVT, SPC en WPC. Daarbij gaat men grondstoffen zo efficiënt mogelijk gebruiken en worden vloeren tegelijkertijd lichter gemaakt. Het voordeel voor het milieu spreekt voor zich, net als het voordeel voor de plaatser, wiens rug minder belast wordt.
Volgens de producent wordt het gewicht van het eindproduct met tot 20% verminderd door het verwijderen van materiaal uit de kern. In concrete cijfers: men stelt dat tot 3,5 kg uit één enkel pakket van een typisch 5 mm LVT-product kan worden weggehaald. Een en ander betekent bijgevolg dat alle handelingen met het product gemakkelijker en efficiënter worden, vanaf de levering uit de productieeenheid tot het moment van aankoop en tijdens de installatie door de eindgebruiker.
Hergebruik materiaal tijdens productie
Er is uiteraard meer dan enkel gewichtsvermindering. Zo stelt men dat het tijdens het proces gebruikte materiaal kan worden hergebruikt bij de productie van nieuwe vloerproducten, waardoor ook het materiaalverbruik tot 20% kan worden teruggebracht. Een efficiënter gebruik van grondstoffen betekent dat het aantal leveringen aan de productie-eenheden kan worden verminderd en dat men bovendien met lichtere producten elke zeecontainer efficiënter laadt. Zo verminder je niet enkel het aantal transporten en de benodigde stockageruimte, maar ook de CO2-voetafdruk.
Maak je de berekening in de praktijk, dan stel je onder meer vast dat de 60 miljoen m² LVT, SPC en WPC-bevloering die in 2017 in Europa werd verkocht met Liteback fors gereduceerd had kunnen worden. Ten eerste zou er door het efficiënter gebruik van de grondstoffen dat jaar maar liefst 117.000 ton grondstoffen zijn bespaard. Vervolgens zouden er om en bij de 4.800 minder trucks nodig geweest zijn om producten te leveren en zouden bovendien 3.400 scheepscontainers nooit verscheept zijn. En om het helemaal aanschouwelijk te maken: met een lager verbruik van ruwe materialen en minder transporten, had de CO2-uitstoot in 2017 bijna 80.000 ton lager gelegen, het equivalent van de jaarlijkse uitstoot van meer dan 56.000 personenwagens.
Groeven frezen
Tot slot moeten we u nog even meer verduidelijken hoe dit alles concreet in zijn werk gaat. Bij Liteback worden er met behulp van een groefmachine groeven gefreesd op de achterkant van de vloerplaat. Het materiaal dat tijdens het proces wordt verwijderd, wordt gerecycleerd in het productieproces, waardoor het materiaalverbruik tot met 20% daalt. De groef-unit kan daarbij stand alone worden gebruikt, maar kan tegelijkertijd worden geïntegreerd in het reguliere productieproces, waardoor extra handling van de panelen overbodig wordt.