
6 minute read
Special Providers of abrasive materials
THE AMAZING POWER OF MINUSCULE OF ABRASIVE GRAINS
FROM CRUSHED SEASHELLS TO CRUMBS FROM CAST-IRON CABORUNDUM
Advertisement
How difficult is it to sandpaper a parquet or wooden floor? Difficult! Each sort of wood is different and each sanding machine has different specifications. The various sanding sessions, the sanding order, the grain size, the type of sanding machine depending on the sanding session, these are all elements of a parquet floor fitter’s training. Apart from that training, floor fitters can contact most agents for demonstrations, workshops, and product presentations. That also applies to abrasives, another product group which is developing rapidly.
A piece of history The first record of sandpaper dates back to 13th century China where crushed seashells, seeds, and sand were stuck to parchment using natural rubber. On 14 June 1834, Isaac Fisher from Springfield obtained four patents on sandpaper. His sandpaper could only be used dry and the dust caused lead poisoning amongst the labourers who had to use it. The Minnesota Mining and Manufacturing Company, now known as 3M, discovered sandpaper early in the 1920s which could also be used wet. In the past, natural materials such as pumice and shark skin were used to roughen up the base. The term in Dutch for sandpapering (‘afhaaien’), which is still used a lot by older painters, is derived from this. The difference between abrasives lies in various elements: - the underlayer used: paper, synthetics, textile (the latter is often called emery cloth); - the sort of adhesive used (especially whether or not this is waterproof; waterproof adhesive and underlayer can be used for wet sandpapering, otherwise the sandpaper is suitable only for dry sanding); - the grain size of the abrasive: usually designated with a number, where a higher number indicates finer sandpaper: 24 or 40 is rough, 600 is fine; degrees of fineness are available up to 12,000 for use in the metal industry. The number comes from the sieves of the material. Theoretically, the diameter of the grain is as follows. Each square inch divided by the P size in the square is the grain diameter.
And so, with grain P80 the grain diameter is 25.4mm x 25.4mm/80 x 80 = 0.1008mm diameter; - the material of the abrasive: from sharp sand or glass powder (the
English word for these abrasives is still sandpaper) to the much harder korund or the even harder carborundum; - the shape of the base: ordinary sandpaper skins, or cut as required for the sandpapering sole of an electric sanding machine, or in the shape of belts for the belt sander; - the thickness of the abrasive powder on the underlayer: In particular for machine sanding, the grains should not be too close to each other because then the space in between soon fills up with sanding dust and the paper soon wears out and is of no use. What’s new today? For parquet and wooden floors, and certainly for the application of certain specific finishes such as ‘distressed’, the market offers scores of new and innovative brushes and other fairly hard motion tools. There, too, we see constant development. Grinding no longer means just sandpapering. As far as pure sandpapering is concerned, we see that the various materials of which the grains can consist determine the scope of the abrasive. Certainly in the world of parquet in the field of abrasives there has been an increase in quality in the direction of zirconium and ceramics.
Some specialists
Blanchon
In the parquet industry there has been an improvement in the quality of abrasives towards zirconium and ceramics. Glass is not used in the parquet industry and diamond even less so due to the cost price. The four most important materials are corindon, carborondum, zirconium, and ceramics. Each of these materials has specific assets and drawbacks. The key is to choose the right material for the right application. At Blanchon, too, they operate on the basis of three sanding sessions (with separate grain) and (usually) a polish with the single-disc machine. And so, Blanchon offers a range of different abrasives and bearers such as endless abrasive belts, rollers, and discs. A major trend which they have noticed here is the increase in the use of multi-disc sanding machines. These machines are extremely efficient, but due to their relatively low weight they are not used for some heavy tasks (e.g. removing old coats of lacquer).
Devo®

Over the last 40 years, the range of Devo® sandpapering materials has become a regular fixture amongst parquet traders due to innovation and high quality. There has generally been little renewal in terms of basic raw materials. Most ‘new’ materials which enter the parquet sector have existed for a long time, but are now also found on the parquet market due to a growing demand for high-performance materials. In the past, parquet traders used hardly anything except aluminium oxide and silicon grains. Nowadays, they also use zirconium and ceramic materials due to the greater sandpapering grain hardness. The composition of the materials has undergone some change as a result of technical developments. For instance, in 2017, Devo innovated with the Devo® Fiberpad™. This is a completely new sort of sanding disc which offers scores of benefits for floor fitters.

Pallmann
Aluminium oxide abrasives have been virtually obsolete in woodfloor sanding and technological progress has moved on from zirconia alumina to ceramics and finally to diamonds as the current cutting materials for sanding wood flooring. Diamonds are becoming more and more important for the sanding of wooden floors, because it is possible to remove extremely hard coating systems, such as UV-hardened lacquers or DD lacquers. Pallmann abrasives are optimally adapted to Pallmann sanding machines and the intended use. So Pallmann recommends ceramic abrasives for coarse sanding, zirconia alumina for subsequent sanding and silicon carbide for fine sanding. With the new abrasives, it is possible to replace almost all the work of a belt sander with the Pallmann Spider triple disc sanding machine. In addition, the brushing technique for the Pallmann Spider offers the possibility to structure existing floors as well as to renovate already structured surfaces without having to sand the structure.
The DevoNatural range of professional parquet floor products meets the highest standards when it comes to treating parquet floors.
It is all about quality without compromise, developing products using the best raw materials and cutting-edge technologies.

DevoNatural is available in original colours and contemporary finishes, which are fully in harmony with the latest trends in interior design.
You want to play on your parquet floor ?
PROFESSIONAL PARQUET PRODUCTS
Makes it possible !
Discover the DevoNatural product range :
www.devonatural.be/en/
Machines and abrasives from LÄGLER Everything from one source!
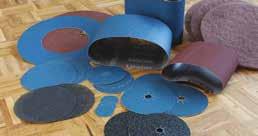

You are still not using a LÄGLER ® abrasives? Then you are missing out on the following advantages: superior quality, efficiency and profitability when sanding. Since our abrasives are characterized by: • high aggressiveness • long lifetime • long-lasting sanding performance Only these abrasives are optimally matched with all our machines and their diverse application possibilities. Get the most out of your machines with the LÄGLER ® - Abrasives!