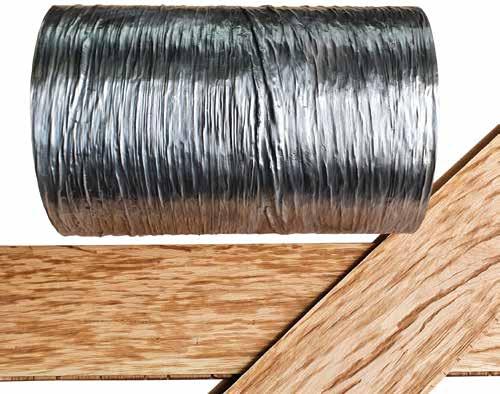
7 minute read
Special Producers of distressing machines / brushes
DISTRESSING IN QUANTITY IS POSSIBLE, BUT ONLY BY MACHINE
IMITATING OLD TECHNIQUES WITH MODERN MACHINES: GREAT!
Advertisement
Photo – Renzo Borgonovo/FNT Trabattoni Stampi
Obviously, it’s not only enthusiasts inspired by grandma who fall for the charms of antique floors. More and more project managers are opting for them because they believe these floors give added value to the interior which they have in mind. As well as those project managers, decision makers such as architects, interior architects, and designers have also discovered that nostalgic charm. Now that antique floors and floors produced from old wood are barely available, all those adherents have no other option but to accept floors which are aged artificially. And, believe me, the techniques used for that purpose most certainly achieve their goal.
Colour distressing Wooden floors can turn darker over the years under scores of influences. The way in which they have been protected and the regular maintenance (mainly with wax), the use of colours and stains, but also influences from damp, oxidation, fluctuations in temperature, dust, and dirt mean that wood turns darker over the years. When old wood is recovered, its former use also shows up. For instance, wood which was once used for old mooring posts turns darker after years of penetration by water. And so, colour distressing is a commonly used technique, often in combination with mechanical techniques (see below). Oak in particular can be treated in several ways so that it is perfectly suitable for taking on various guises. Apart from the classic treatments with lacquer, oil, wax (hard wax), or soap, oak lends itself to various special treatment techniques (e.g. thermal or chemical modification), prior treatment with colour stains, lye, white wash etc.
Mechanical distressing Most forms of colour distressing can be carried out on modern lacquering or oiling lines i.e. on a production line. To find out more about mechanical distressing machines, it is useful to have a brief outline of the distressing techniques themselves. Strictly speaking, with mechanical distressing we have two objectives in mind. We want to create the impression on the one hand that the floorboards have been produced using outdated techniques from 100 years ago (brush ing and scraping), whilst on the other hand that floors have suffered from years of use (scouring, beating, and lashing).
Mechanical operations In view of the growing popularity of ‘distressed floors’, there’s a big need for mass production. It is essential to ensure there is no hint of a repetitive pattern in the applied damage. One solution for this is ‘constant distressing’ (source: Soest). Some machines can distress planks continually at high speed without leaving a repetitive pattern. The required sort of damage and depth are easy to set.
Beating or scourging By scourging and beating, we apply damage to the floor to give the impression either that the floor is worn out with use or the floor boards have been consumed by insects or micro-organisms. By making tiny holes, we imitate woodworm, something which often found in older (damp) houses on floors in pine or pitch pine. The principle is simple; the planks are put inside a drum which is full of bolts, nails, and such like. If we rotate the drum, the loose flying objects in the drum apply random damage to give the floor a distressed look. According to some people, the main drawback with ‘beating’ is that the process is cumbersome and time consuming and may cause unwanted damage to the tongue and groove. The rear side of the plank is also damaged and the corners are rounded off.
Rolling Then there is the rolling method. A metal roller can be equipped with various forms of unevenness which are pressed into the wood. The big drawback here is that there is clearly a repetitive pattern in the damage applied. The same markings appear on the wood each time that the roller rotates. Here, too, the solution lies in continual distressing (at various speeds).
Brushing Brushing highlights the wood grain. The ‘soft’ parts of the wood grain are the most susceptible to wear and tear (through abrasion). This means that over many years of use, even the most perfectly maintained floor will show increasingly prominent wood grain. Brushing is done with a structure brushing machine which (just like the colouring procedures) can be included perfectly well on the production line. These machines are available in various widths and can be fitted with various brushes. Apart from machines with cylinder brushes, there is also the rotor scrub machine (Trivec) which, as it were, scrubs away the soft wood instead of brushing it. The distressed effect is an excellent basis for strong colour highlights which can be stained and/or oiled later.
Scraping, scratching, and ripping Diagonal damage can be applied across the wood surface using a special grinding technique. The effect is comparable to that of sawing, but this technique is easier, faster, and much more consistent. The effect can be established with extra accessories in the machine e.g. continuous diagonal lines or broken diagonal lines. The scarving technique can be combined with one or more brush modules.
Three specialists
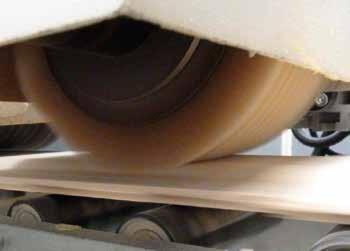
Cardotech CARDOTECH: A DISTINCT RANGE IN EUROPE
Formed in 1886, or five generations Design and manufacture of technical and industrial brushes on the basis of specifications Factory in Sainte Hélène, France, near Le Creusot, Departement 71 ISO 9001 certified, 2015 version Exports 30% of its production to Europe and Asia Supplier to the wood sector since 1998 and a sector leader in Europe Supplier to parquet manufacturers in France, Belgium, Germany, and Poland Brushes for removing fibres, structuring, finishing, and ginning General offer: engineering, production, commissioning, testing, and training

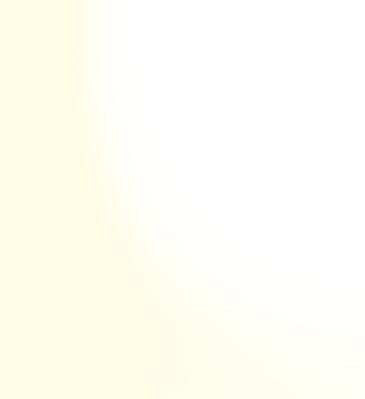
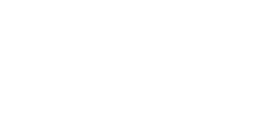
Quality commitment in terms of lifespan, quality, and general cost price Apart from the quality of its recognised products, CARDOTECH offers excellent service (testing, commissioning, training, speedy delivery, and a focus on results).
Trivec Trivec Tumbler machine (new)
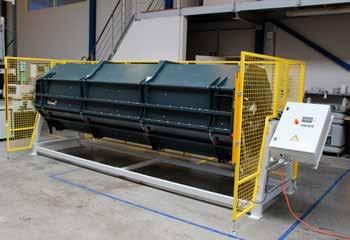
The most attractive distressed floors are made using a tumbler machine. This involves a technique where several planks are put in a large tumbler simultaneously. The tumbler itself is full of specific tumbler equipment designed to cause random and intentional damage to the wood surface. Trivec makes and supplies an industrial Tumbler Machine for this application. This machine can be supplied in various designs of 3, 3.5, and 4 metres. The tumbler is equipped with a touch screen which programmes the rotation speed and cycle time. Together with the right tumbler equipment, this can determine the extent of distressing as required by the user. The entry doors for loading and unloading are big (stretching over the whole width of the machine) and open automatically. Depending on the programme setting and plank size, you can distress between 8 and 16 square metres of planks every two to three minutes. The machine is supplied with a safety gate around it. On the entry side (for loading/unloading) a ‘light curtain’ ensures that the machine switches off automatically whenever someone or something crosses the light curtain. Trivec Surface Finishing programme Trivec supplies the most extensive programme in distressing machines. Apart from the Tumbler machine, they also supply the Trivec Surface scraping machine, the Trivec Edge Cutter for caus ing intentional damage to the bevelled edge, the Cross Cutter with the unique Tapper System for random band saw effects, the Trivec conveyor belt machine with a distressing module, the Disc Cutting machine, and a wide range of brushing machines in working widths of 400 to 1400mm. In fact, the Trivec Reactive Stain Sprayer also belongs to the group of distressing machines. This machine has been developed specially for reactive stains and it is therefore built entirely using non-corrosive materials. This machine is used to apply reac tive stains quickly and very evenly to yield colour effects with a distressed look.
Renzo Borgonovo /FNT Trabattoni Stampi
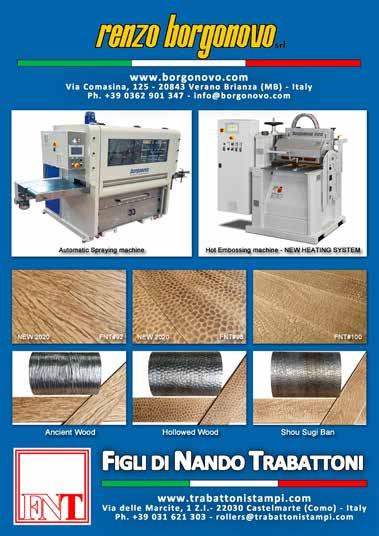

Renzo Borgonovo and FNT produce embossing machines and rollers for the embossing (and distressing) of wooden floor, panels, and more. The machine and roller work using pressure and heat, to replicate the pattern present on the mold onto any kind of wood (solid, plywood, MDF, scrap-boards, reclaimed wood, etc). The machines are safe, fast-pace working, and up to the latest technological standards and can thus be integrated into any working line. These units are capable of hosting rollers with a huge variety of patterns (also customized ones), for the taste of every culture and customer! Our main model, Borgore 500/ITI, has an embossing width of 500 mm., but also wider models, reaching 1,0 and 1,3 meters, are available. Our main buyers are parquet and wall panel makers, and all those who work in the furniture and interior design industry. For more info, feel free to contact us: we will be glad to help you out!