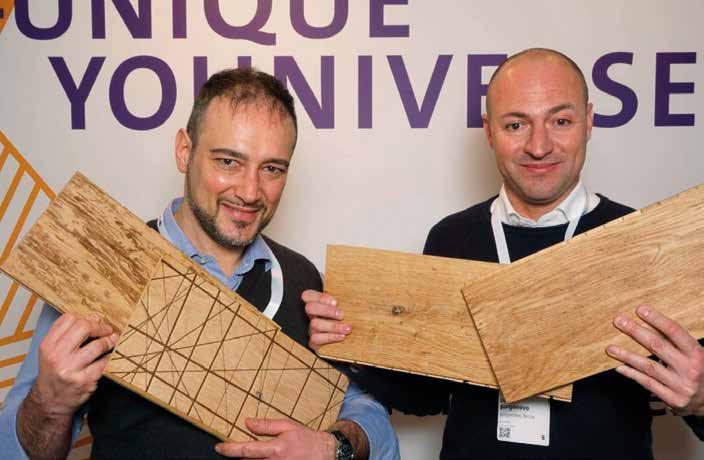
4 minute read
Advertorial Renzo Borgonovo
Mr. Matteo Trabattoni of FNT Srl (left) and Mr. Luca Borgonovo of Renzo Borgonovo (right)
Advertisement
Placed on the northern edge of the Po River Plain, the most developed industrial region of Italy, not far from the major cities of Milano and Como, the companies Renzo Borgonovo and Figli di Nando Trabattoni (FNT) have developed, during their 60 years of partnership, a strong collaboration based on mutual respect and appreciation which has made possible the constant evolution of the hot embossing technology offered and popularized by the two brands.
Founded in the late 50s and early 60s of the last century, FNT and Renzo Borgonovo moved their first steps within the sector of frames and linear profiles finishing, where they enjoyed outstanding results, supplying all over the world mainly cold embossing machines (among other machinery) and embossing moulds to engrave the products with the help of wood pulp. Following the changing of the international markets, the machinery manufactured and the technology exploited started to evolve, and the two companies began to focus more on units able to process wider work-pieces and to operate with the use of a heating source.
This brought to the creation of the first Hot Embossing machines, which made use of methane or propane gas for the heating of the embossing roller, which now needed to engrave directly onto the wood, without any intermediary agent. The first hot embossing machines, developed in the late 60s and still working on a width no bigger than 150 mm, were featuring a heating system made by Bunsen burners, and may look fairly rudimental in the eyes of a current day customer. The burners emitted open flames that directly hit and thus heated the embossing roller, and, despite being very effective, the system had not real control over the roller’s temperature and was probably not so energy efficient and surely not up to the current safety standards.
With the years, the machines grew wider and sturdier, being able to accommodate work-pieces as big as small panels, but the real evolution came with the changing of the burner, passing from an open flame system to a gas limited and controlled heating system. This change was a great step forward for the safety and quality of the machine, since it allowed the control of the embossing roller’s temperature and, starting from these models, the machines got equipped with a HMI software, and thus a Touch Screen. While in later years the machine became bigger and reached even 1300 mm of working width, the unit preferred and most purchased within the parquet and flooring sector remained, throughout the years, a middle size unit, with an embossing capacity of up to 500 mm in width.
This same unit is, for about four years now, available with a heating system run by electrical lamps: this last update, which has quickly become the favorite and most-purchased version of the hot embossing machines, made possible the overcome of many technical and safety issues, since the unit features no gas usage whatsoever. The current version of the model targeting the flooring sector is thus an electrically heated machine, with an embossing roller with a working-width of 500 mm, a touch screen to operate most of the machine’s parameters, a transport system with inverters which automatically synchronize the upper and lower dragging rollers, and a user friendly embossing roller changing device, which make it possible to uninstall a roller mould and install back a different one in about 10 minutes. This latter feature optimizes the versatility of the machine, which is able to engrave different patterns by changing the upper embossing rollers. The manufacturing know-how and the quality of these essential tools have done giant leaps over the years, as well. Starting from basic linear frame drawings, the design has evolved, pushed by newer and more complex demands, and by exploiting more and more technologically advanced instruments, Renzo Borgonovo and FNT are now able to replicate on roller the negative of extremely complex patterns, which, when used to engrave on wood, result in outstandingly accurate natural patterns, modern and geometric drawings, and aged-wood looks.
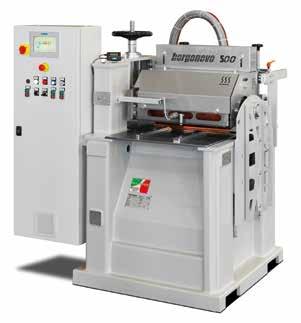
Other than the hundreds of patterns already available, the two companies develop new rollers every year, and provide the service of designing patterns from the scanning of real material, if customers have in their hands something they wish to replicate. The art of ennobling wood profiles, flooring planks, kitchen and wall panels at an industrial level as always passed through machinery: with the technology manufactured by Renzo Borgonovo and FNT the customer will obtain a sturdy and versatile companion, capable of handling successfully the most demanding tasks.
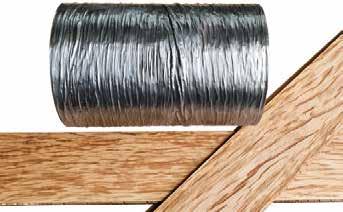
For more information : www.trabattonistampi.com / www.borgonovo.com
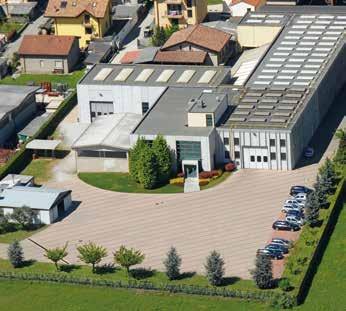
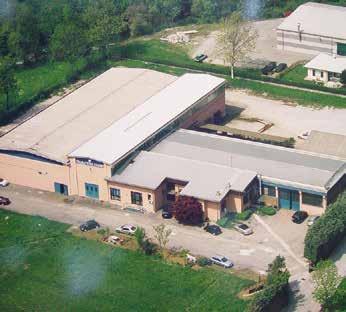