
8 minute read
Special Curing oil and lacquer with led
IS A LED FINISH FOR WOODEN FLOORS STILL A TRENDY MARKETING TOOL?
TRADITIONAL UV CURING IS STILL THE STANDARD TECHNIQUE FOR NOW
Advertisement
Arjan Maatkamp (DecoRad Systems bv - NL)
DecoRad Systems bv from Veenendaal in the Netherlands offers a full range of portable on-site UV/LED curing equipment plus industrial LED equipment. UV equipment from DecoRad Systems is suitable for all UV lacquers and coatings which are currently available worldwide. General manager Arjan Maatkamp explains: ‘Parquet is one of our three segments. We also focus on the finish of concrete and flexible floors.’
Recently, this company, which is part of an electronics concern, has invested in new corporate premises. All together, the concern numbers sixty employees. Arjan Maatkamp likes to stress the unique selling points of DecoRad Systems: ‘Worldwide, we have a handful of rivals, but we’re the only ones who do our own designing, building, and marketing. We control the entire process. Customers here can be sure of quality, partly through CE, TÜV, and an ISO 9001 quality guarantee.’
‘Customers usually contact us first of all via the web site, where they get a good look at our range of equipment. To give an idea of where the equipment is made and by whom, we’ve made a company video, which we send with all our price quotations. This video has proved to be a nice solution in view of the restrictions on travel.’
Flexible floors as a growth market
We mentioned above that the DecoRad market consists of three segments. The current focus is on flexible floors. ‘This is a very sizeable market, which includes schools, hospitals, elderly care homes, airfields, and such like. Then there are large surfaces of Marmoleum, PVC, and vinyl. Polymering often comes into play there, but there is an attractive alternative. Polymering means putting three coats of wax onto each other and leaving them to dry for a few hours. That’s a process which takes some 10 to 12 hours. Once or twice a year, those coats of wax are stripped using an alkaline agent to soften and remove them. And so, the waste water goes down the drain and you discharge millions of litres of stripped chemicals each year.’
‘The biggest gain with UV coatings is that you never need to do that again. A permanent seal with UV coating is solventless and it dries at once. The result is a really durable solution which also lasts much longer (three to five years, with some frequent dry cleaning and/or with a damp flat mop). In today’s sustainable society, with solar panels, windmills, and electric cars, isn’t it logical that we dispose of an ancient and environmentally unfriendly technique like polymering? After all, we have a fantastic alternative.’
Breaking patterns with UV
‘For those who like figures, did you know that five million square metres of Marmoleum is fitted in the Netherlands and Belgium alone? That means lots of polymer waste is scrubbed off and rinsed through the drains. If you break that pattern, it’s a win-win.’
‘This has given rise to a partnership with Forbo Eurocol, the biggest linoleum floor supplier in the world. Forbo Eurocol 326 UV-CareShield is a mono-component permanent protective layer for high-traffic linoleum floors. Forbo Eurocol 326 UV-CareShield has been developed using DecoRad UV equipment and we’ve become the worldwide distributor for this product due to our expertise in on-site UV. In our view, the shift from polymer to UV on flexible floors would get the most benefit from UV technology. It’s a positive development for everyone and for the environment.’
Everyone seems to be talking about LED curing. The question is, however: What’s the real market share of LED and is it really worth all the fuss? We spoke to a specialist Dutch company, DecoRad Systems bv, and their views are as follows: LED curing could have a decent future, but, in 2021, 95% of curing is still via traditional UV and there’s no sign of much change in the near future.
DecoRad Systems is the ideal source for an interview. The company operates worldwide in marketing mainly portable UV and LED curing apparatus, including for hardwood floors. We spoke to general manager Arjan Maatkamp and asked him first of all to outline the main difference between LED and UV curing.
LED versus traditional UV
‘First of all, you have to understand what it’s about,’ he explains. ‘Basically, UV curing consists of two things. On the one hand, there’s a UV lamp as a transmitter and, on the other hand, you have the chemistry as a receiver. These two elements have to be harmonised minutely to yield full curing plus the required properties in a tenth of a second. The biggest challenge with LED is curing on site. The most common wavelength of LED is close to that of daylight, so an unwanted reaction can occur.’
‘LED curing with pre-finished parquet is another matter because you have more control over the conditions in a factory and can keep variables to a minimum. For instance, in a factory you can keep shining sunlight out by covering the windows. You even have to take account of skylights.’
Shooting as a sniper or shooting hail?
‘UV curing is generally more user-friendly than LED, but especially on site. Traditional UV has a broadband spectrum where, put simply, various wavelengths are transmitted. These reach several receivers (photoinitiators) which are built into the chemistry, whilst with LED there is only one type of transmitter and receiver. If you express it more plastically, you could say that with a UV lamp you shoot with hail (and therefore it’s easier to get a good result), whilst with LED you’re a sniper. The limited possibilities mean there is only one chance of curing and getting the right properties.’
When people talk about LED, one of the positive features which they invariably stress is that it saves a lot of energy. According to Arjan Maatkamp, however, that is not the whole story when it comes to curing lacquers on wooden floorboards.
‘If we compare various things with a machine which is 40cm wide, a traditional UV machine has a voltage of 3000 watts, whilst for LED this is barely 700 watts. That sounds good, but various things mean that the choice of chemistry is very limited and it’s not possible to achieve high production speeds. With the deployment of heavier LED modules (water-cooled), the range of chemistry is greater and higher production speeds can be achieved, but then we come back to the voltage, which is the same as that of traditional UV. Where’s the energy benefit in that?’
Photo – DecoRad Systems Problem of the chemistry or of the LED development?
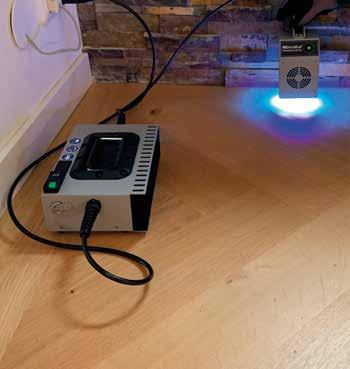
‘The question to ask yourself is whether or not the much more expensive LED systems can be justified financially at present, certainly if they only yield the same result. Yes, LED will have its day in the future, certainly in industry, because you can create the ideal conditions for it there.’
Arjan Maatkamp’s opinion is quite clear. The real evolution of LED is taking place in lighting, but that’s certainly not the same as LED for curing. That is happening due to the difference in demand. And so, for now, we have to accept that what we really need is not yet available and/or affordable. The floor industry won’t give its general approval until LEDs with lower wavelengths and sufficient W/cm² become affordable and available (combi-LED modules). That will make it possible to work with greater coat thicknesses and higher production speeds and there will be a diversity of lacquers, coatings, and oils available for wooden floors.
Arjan Maatkamp concludes: ‘LED is absolutely revolutionary as a replacement for traditional UV in the printing press and labelling industry. In those industries, installations of a few hundred thousand euros are somewhat more easily accepted.’
Two other specialists have their say:
Ciranova
The use of LED technology is relatively new for the wooden flooring industry, so there’s still a lot of unknown territory to explore. The system has lots of positive features and Ciranova – Debal Coatings is continuing to investigate the correct applications, drying techniques and product development. The company has expanded its know-how of LED products and application this year thanks to the takeover of the company Geka coatings from Deinze. Geka Coatings has already several years of experience in LED and UV technology in various sectors. They are using this know-how for research in order to obtain top quality LED drying products for the parquet sector. We are familiar with Light Emitting Diode or LED from daily life. A UV LED generates UV energy in the form of photons. The interaction of these photons with the photo-initiator creates a chain reaction between binding agents (monomers and oligomers) and the fluid is converted into a solid substance. Knowing that short wavelengths are good for surface drying
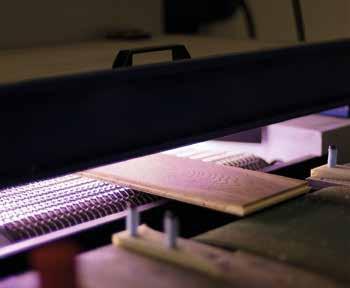
and that longer wavelengths have less energy, but penetrate deeper into the coating, we can say that UV LED performs well for drying in depth and that the classic UV technology (halogen lamps in particular) yields better surface drying. At Ciranova, too, they have great faith that LED will be the technology of the future. Since both the product and drying are still developing rapidly, Ciranova prefers to concentrate on industrial finishes. For more information and samples please contact Ciranova info@ciranova.be or tel +32 (0)51 30 11 40. Chimiver
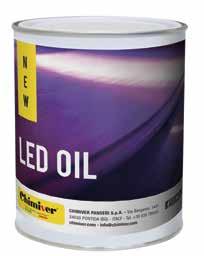
LED systems are the future for the curing process of coatings. Chimiver, always moving with the time, offers you LED OIL, an efficient and performing product which embraces this technology. PRODUCT: - It cures instantly under
LED light and wood can be walked on immediately - Very high chemical and wear resistances - Solvent free, no ozone emissions, no unpleasant odour
- 0% VOC - Natural look and feel - Available transparent and colored - Easy maintenance with Lios range of products LED-CURING UNIT: - Longer service life: LED lights last up to 20000 hours whereas UV lights up to 700/1000 - Energy saving - Low working temperature
Take care of your outdo� living!

Restore your decking and outdoor wood worned by the sun and bad weather using professional and easy to use products:
Lios® Grigioff Grigioff Lios® Sundeck Sundeck Wood Oil Lios® Sundeck Sundeck Soap
Restore old grey wood Renew and protect Clean and nourish
Forbo Eurocol UV-CareShield
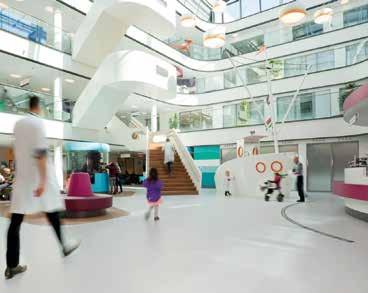